November 2015 Vol. 70 No. 11
Rehabilitation
CIPP In Jail
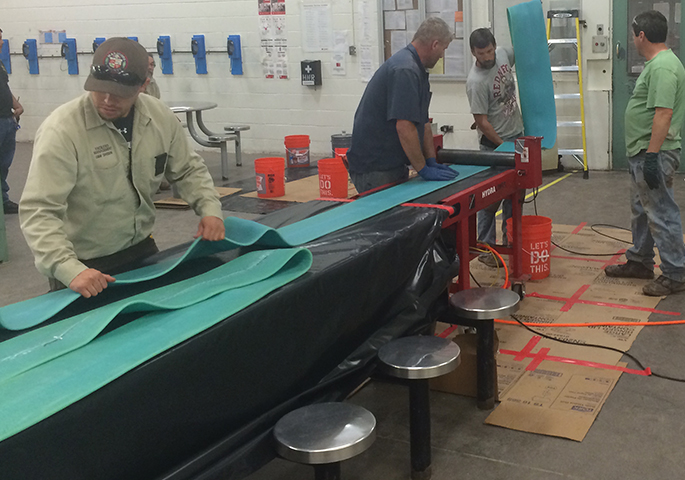
CIPP Keeps Maricopa County Within Budget, Without Disruption
Estrella Women’s Jail in Maricopa County, AZ, can anticipate at least 50 years of improved flow with no more backups from its rehabilitated sewer system. The emergency cured-in-place-pipe (CIPP) upgrade was performed by Irontree Construction Inc. using HammerHead Trenchless Equipment’s HydraLiner line of CIPP equipment and consumables.
Compared to the jail’s only other alternative – traditional demolition – pipe replacement and restoration via the use of CIPP has spared taxpayers considerable expense. Since Estrella is the county’s only female detention facility, digging up the pipe would have required relocation of half its inmates for the duration of the job.
Staying within the county’s budget was critical, since the sewer main had not been part of the original project plan. Irontree Construction, a commercial plumbing contractor based in Mesa, AZ, had actually been lining branches and risers connecting dormitory toilets to the main when problems with the main were discovered.
Irontree Project Manager Court Wood said the original project was for his five-man crew to shoot five to 6-foot-long vertical branches from pipe chase accesses. Things had gone well, shooting eight of the branches on the first day, but the night after their second day a major backup occurred. Irontree determined the problem had to lie beyond the branches and risers.
“We sent a camera in from the outside to have a look,” Wood said. “That’s when we discovered the mains were in extremely bad shape. In many places there was visible channeling and pitting, allowing waste to hang up. In other areas, it looked as though the invert might be completely gone.”
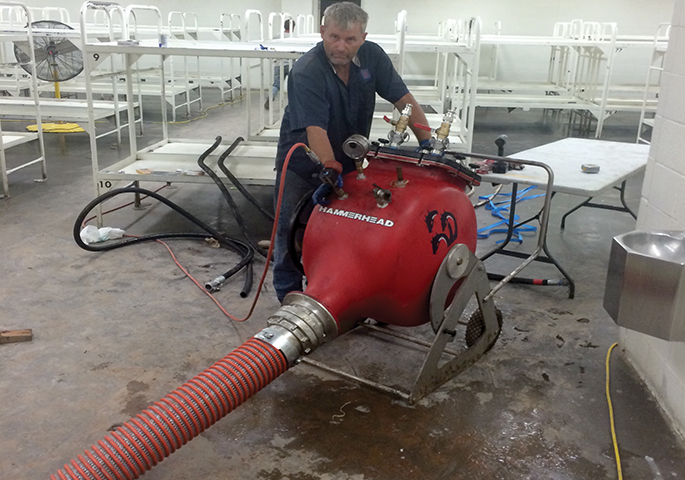
Inside job
A change order expanded the scope of work to include rehabilitation for the main located under the four dormitories with some unusual plumbing job limitations. First, Irontree’s work must be performed at night, when lavatory usage was at its minimum. However, the work must not disturb the detainees, since state law requires that they have eight consecutive hours of uninterrupted rest each night.
Second, facility personnel could not turn water off before 8 p.m. and must turn it on again each morning by 6 a.m. It takes about an hour on each end of the work window to shut water off and turn it back on. Irontree’s actual work window would be between 9 p.m. and 5 a.m. During that time the crew must complete any run it started, including wet out, inversion, curing and reinstatement.
Third, jail routines must continue with as little interruption as possible. Should a detainee need to use the restroom during the night, an officer would escort her to an outside portable toilet.
And finally, project funding restricted overtime pay, limiting the use of detention officers required to work additional shifts to maintain security with non-county personnel and non-routine activity inside the jail. The crew was allowed to work only on the Thursday, Friday and Saturday nights of two consecutive weeks. The project would have to be completed in that calendar period.
The four dormitories of the building lay in a row side-by-side. The main run entered the building at 8 inches in diameter for 65 feet, transitioning to two 55-foot lengths of 6-inch and then a final 100-foot length of 4-inch pipe farther into the building beneath the risers.
General contractor BRYCON Construction of Chandler, AZ, providing overall coordination and supervision, specifically cement work, handled cutting in and consequent restoration. Since machine noise was not permitted at night, BRYCON cut the 5-by-5-foot access holes in the first and third dormitories from the building’s corner during the day on Thursday.
Thursday night began with jet-cleaning and video-recording the two mains. Before the shift ended Friday morning, the crew had also measured and cut the liner material to length. Everything was made ready to begin inversion immediately once they returned Friday night.
Inversion began with wet out. First the crew attached a vacuum pump to the liner to eliminate entrapped air and make wet out easier. They measured and mixed the two-part, styrene-free resin at a four-to-one ratio. They poured it into the liner, working it progressively down its length using the clamping and roller system of a wet-out table. After wet out, the crew wound the liner onto a spool inside the HydraLiner inversion drum, feeding the end through and back over the nozzle. Clamping the liner in place sealed the drum.
Pressurizing the drum forced the liner to spool out through the nozzle, turning itself inside out as it progressed, its epoxy resin side bonding and sealing with the existing pipe to create a continuous, joint-less rehabilitated line.
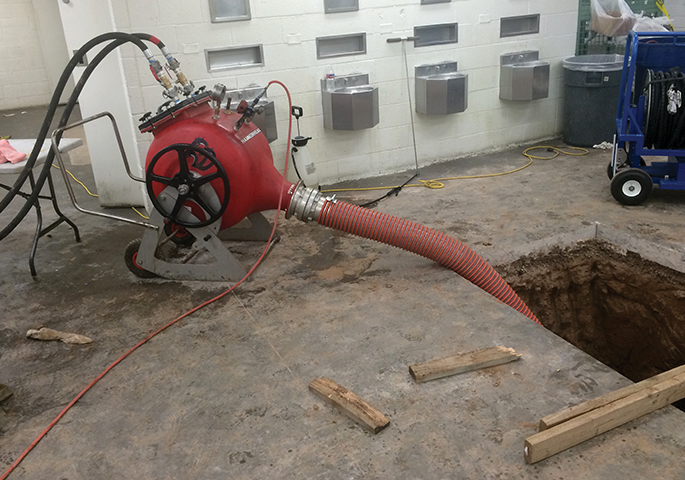
Heating things up
HydraLiner resins can be cured with ambient-temperature air or hot water. On the vertical branch work, Irontree had performed previous to the main, they were able to complete 16 inversions and reinstatements a night using air-filled calibration tubes maintaining 10 psi. The air pressure ensured the liner smoothly bonded with the pipe during its cure time.
Irontree sped up the cure time for rehabilitation of the main using water they heated and maintained at 176 degrees. The HydraLiner calibration tubes used in this application contain internal filling tubes that fill the liner from the end of the run back to the installation access. Filling from the far end this way also allows for a continuously cycling flow that maintains a uniform temperature the full length of the liner throughout the cure time.
Though the water can be heated after the calibration tube has been fully filled and inverted, in this case it was heated to temperature even as it was inverted. The heat immediately activated the resin, lowering overall cure time. Within about one-and-a-half hours, Irontree could remove the calibration tubes and begin reinstatement to return the line to service.
Liner inversion had incidentally sealed off risers junctions as it passed them. These riser junctions needed to be re-opened. HammerHead lateral tools technician Joe Walsh, who was on site to provide consultation for this job, handled reinstatement of the 8-inch runs using Picote’s flexible lateral Smart Cutter system. HammerHead is the North American authorized dealer of Picote.
Manning the two 65-foot-long, 8-inch-diameter reinstatement operations left Irontree to focus on the 50-foot run of 6-inch pipe and 100-foot run of 4-inch pipe, insuring completion of a run by the 5 a.m. deadline to restore service.
The Smart Cutter stand-alone system consists of a cable-operated, self-centering hub with side-grinding panels matched to the dimensions of the joints. The cutter opens and also smooths out any inconsistencies at the joint.
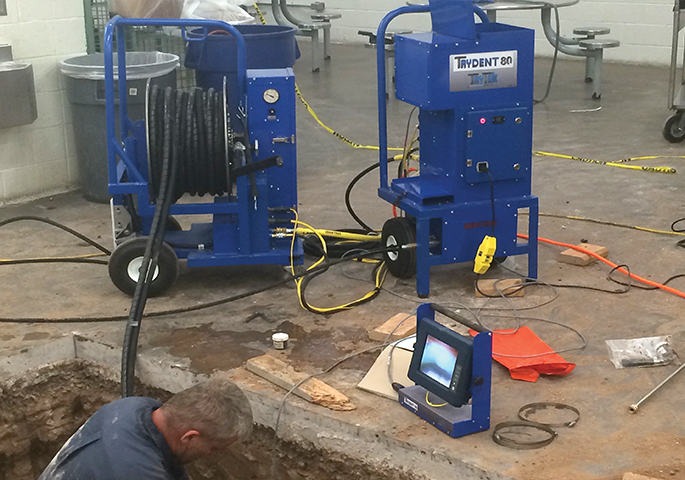
For the 4- and 6-inch reinstatements, Irontree utilized their recently purchased TryDent 80 from Try Tek Machine Works. The TryDent 80 is a small, bend-capable, hydraulic lateral reinstatement tool for 3-, 4- and 6-inch pipe. Using this cutter allowed the Irontree crew to reinstate the services from the sewer main without requiring access to the branch lines. Wood said he was pleased with the water-powered robot.
Work was completed on schedule and within budget. When Wood was asked if the sewer repair could have been done using any other method, given the constraints of this job, he said, “No way.” The job went so well, Wood said, that two more dormitories were slated for sewer rehabilitation.
FOR MORE INFORMATION:
HammerHead
(800) 331-6653, www.hammerheadmole.com
Try Tek Machine Works
(717) 428-1477, http://trytek.com/
Picote, www.picotesolutions.com/
Comments