November 2015 Vol. 70 No. 11
Features
The Efficiency Of Thrust Restrained Joints
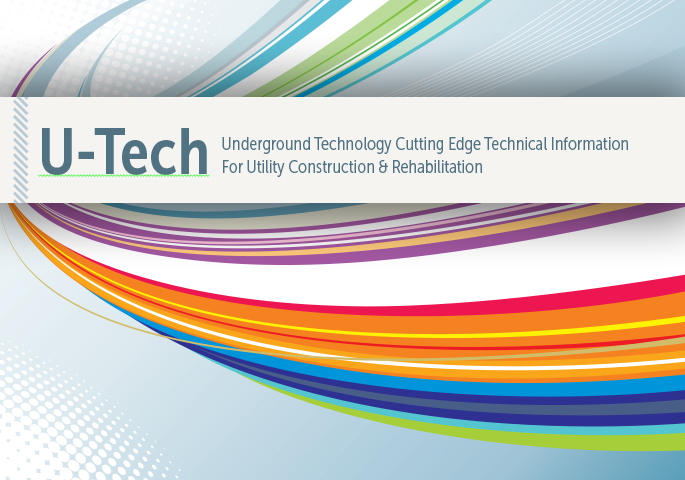
Many utilities and engineers prefer to use ductile iron pipe for their water and wastewater applications for a variety of reasons, primary among them being its strength and durability. Other attributes include its environmental advantages and versatility. Experienced professionals prefer working with a pipe material that offers flexibility in design and installation.
In underground applications, ductile iron pipe features the “push-on” joint, an extremely capable gasketed joint that is very easy to install. This joint has the ability to deflect in order to gently change the direction of the pipeline and, since the gasket is seated in the bell, it allows the pipe to be cut in the field. Both of these features minimize the need for fittings and allow bends for ductile iron pipelines to be standard rather than project-specific.
But pipelines aren’t always routed along gentle curves – and there are times when a pipeline will abruptly change direction or size, or branch off in multiple directions – and fittings are used. Elbows, tees, reducers and dead-ends are examples. While fittings are available in push-on or mechanical joints, they do not offer restraint against longitudinal separation. When these fittings are used, the pressure inside the pipeline creates a thrust force that would move the fitting and cause joint separation if not addressed.
For decades, the traditional way to counter thrust forces was to use bearing or gravity thrust blocks. Bearing blocks are designed to transmit the thrust force through the block with the result being a thrust pressure that is less in magnitude than the bearing capacity of the soil. The thrust force pushes the block; the block pushes into the soil and the soil “pushes back,” making it impossible for the fitting to move. Gravity blocks work by providing enough mass to keep vertical down bends from moving upwards. These methods work but present problems, especially when large thrust forces are involved.
In the 1960s a manufacturer of ductile iron pipe developed the concept of the restrained joint.
The idea is to keep the fitting from moving by restraining the joints so they cannot come apart. That allows the pipe and fitting to interact with the soil, engaging friction between the pipe and soil and, in certain cases, the resistance of the soil to movement. When designing a restrained joint system, an engineer will calculate the total length of the pipeline that must be provided with restrained joints. The friction (f) between the pipe and soil is modeled as a uniformly distributed force; while the resistance (Rs) of the soil to movement is modeled as a triangular distribution with its apex at the fitting. The length of required restraint will be a function of the pipe size, the internal pressure, the type of fitting, the depth of cover, and the characteristics of the soil surrounding the pipe; with additional consideration of the impact on pipe-to-soil friction if the pipe is to be encased, for example, with V-BIO® enhanced polyethylene.
The exact calculation depends on the fitting involved and may require consideration of the distance between adjacent fittings. For example, a horizontal bend would engage friction over the leading face of the pipe as it tries to move at an angle skewed from the pipe’s centerline and, as a result, there is soil movement . A vertical down bend involves the same friction force, but since the thrust force is upward, pushing against disturbed backfill above the pipe, Rs is not used .
Calculations for other fittings, such as tees where the joints at risk of separating are on the branch, recognize that friction is developed around the full circumference of the pipe while Rs is developed over the first joint on either side of the tee on its run.
There also are situations where fittings are sufficiently close that the length of restraint overlaps between those fittings. In that situation, one-half of the length between the fittings is assigned to each fitting and the length of the pipe outside of the fittings is increased.
Modeling variations
There are other combinations that can be modeled, keeping in mind that those situations involve static forces at each fitting. On its website, the Ductile Iron Pipe Research Association (DIPRA) offers a calculator program, “Thrust Restraint Design for Ductile Iron Pipe.” This popular program assists engineers in calculating the required lengths of restraint using the approaches described above.
It also is important to keep in mind that restrained joints are readily suitable for a strong pipe material such as ductile iron pipe, because the strength of the material can handle the stresses involved. Other pipe materials, such as PVC pipe, may require additional considerations, such as the long-term impact of the localized stresses that result at each joint. For example, restrained-joint mechanisms that would be available for PVC pipe can feature grooved or serrated edges that dig into the pipe wall, focusing the stress – a condition that PVC does not favor.
Restrained joints are used regularly to mitigate thrust forces in ductile iron pipelines. Their development continues, with a variety of proprietary joints available from DIPRA’s member company manufacturers. The technology has even progressed to allow their use in trenchless applications such as horizontal directional drilling. Each joint has its particular features and appropriateness for a given use, taking advantage of the attributes of ductile iron pipe. And, they exemplify the innovative nature of our industry, which has continually sought to improve the ability of ductile iron pipe to provide the long service lives engineers and utilities have come to expect. The more we learn to harness the strength and durability of ductile iron pipe, the more innovation results and the more we appreciate the attributes of ductile iron pipe.
FOR MORE INFORMATION:
Ductile Iron Pipe Association (DIPRA)
(205) 402-8700, www.dipra.org
Comments