May 2015, Vol. 70, No.5
Features
Water Project Includes On-Site Pipe Manufacturing
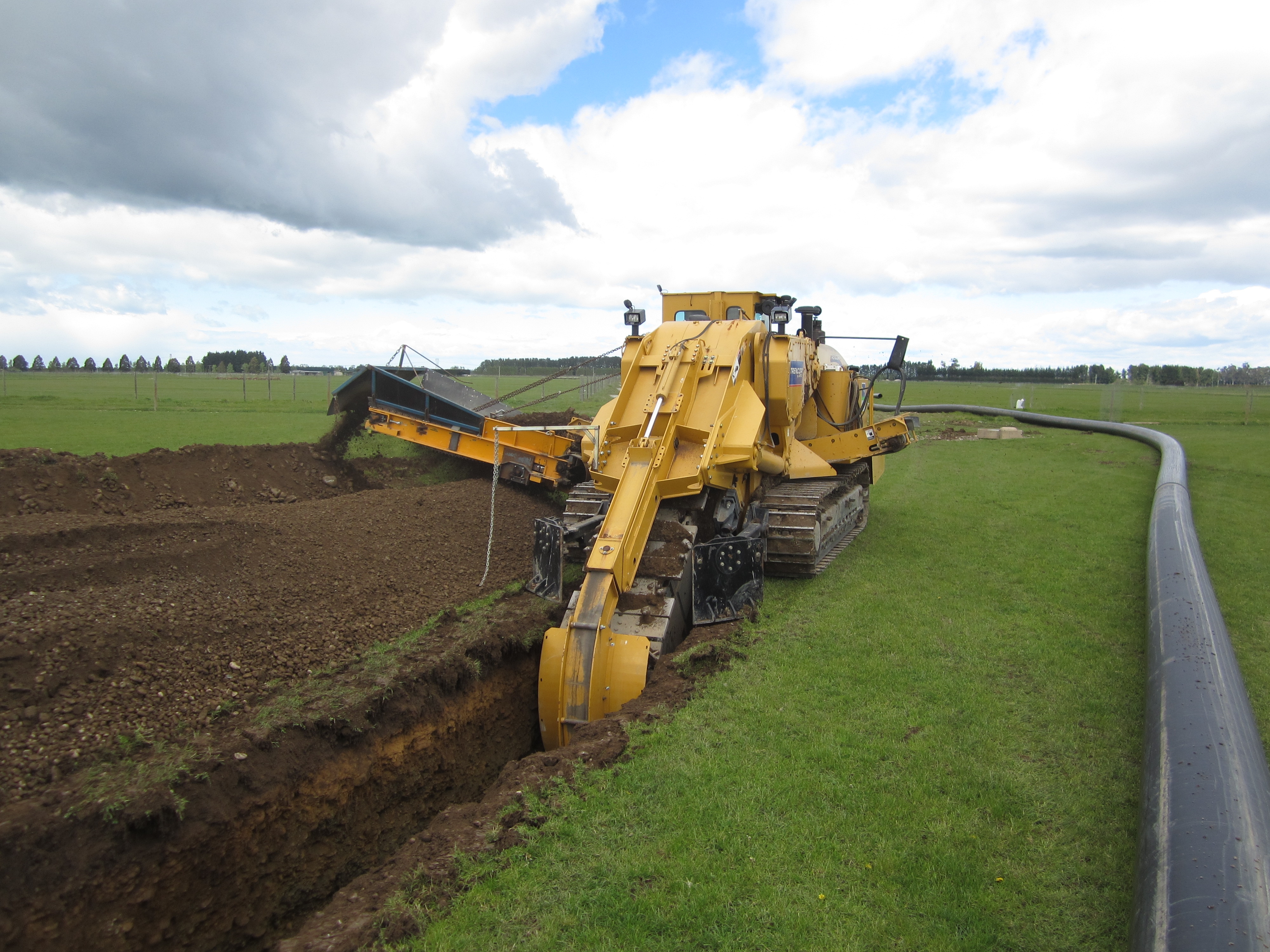
New Zealand polyethylene pipe manufacturer Aquaduct NZ Ltd. recently completed a project to convert an open channel irrigation system to a closed polyethylene pipe system to provide water to farmers on the Canterbury Plains of New Zealand’s South Island.
The Valetta District Irrigation Project serves farms in a 32,000-acre area and is capable of delivering water at a rate of 2,000 gallons per minute. The water supply comes through an open channel of the Rangitata Diversion Race. The race was started during the 1930s depression as a job creator to carry irrigation water across the landscape from the Rangitata River to the Rakaia River, watering the Central Canterbury Plains along the way via a series of open channels.
The Aquaduct Large Bore PE project is believed to be a world’s first of this size pipe produced on site in a re-locatable manufacturing plant. The Valetta Irrigation Scheme is owned and operated by the Valetta Irrigation Company, the shareholders of which are the farmers connected to the project.
“The main driver for the Valetta project was the desire to eliminate water loss and allow more land to be irrigated from the same quantity of water,” said Gerard van den Bosch, entrepreneur and founder of Aquaduct.
Restoring the economic potential of water lost from the open channels was an irresistible challenge, he continued.
“Meeting that challenge required multifaceted innovations and efficiencies,” explained van den Bosch. “The result will bring significant savings by recouping the evaporation and seepage loss of channeled water, saving on-farm pumping costs and also allowing electricity generation. Another strong motivation was the potential of using gravity to eliminate pumping requirements which could save farmers huge production costs.”
Big system
The Valetta underground system contains more than 50 miles of pipe in diameters ranging from 200 mm to 1.6 m (approximately 8 to 63 inches). Most pipe was produced in 400-foot lengths. Bulk handling raw material to produce the pipe averaged as much as seven 18-ton shipping container loads per day.
The re-locatable plant to manufacture the pipe was situated at a central point in the construction area to facilitate distribution of pipe where needed. The plant is in itself an impressive engineering feat (for details see the adjacent sidebar).
To install the underground pipe for the project, a team of installers worked with a track-mounted Trencor Model 1360 trencher powered by a 440-horsepower turbocharged diesel engine. The machine has mechanical chain drive with maximum chain pull of 54,300 pounds. A custom-designed screening device carried coarse material away, leaving the fines for pipe bedding.
Surface conditions were open farmland. Subsurface conditions were a bed of rich alluvial soil laced with glacial cobblestones.
Pipe runs were to lengths of 800 feet, moved to the field on a series of rubber tired dollies. Pipes were joined on site using Aquaduct’s portable PE butt welders which plane, heat and pressure weld the pipe. Pipe was installed to grade manually on the Valetta project, but GPS units have since been installed on the company’s three trenchers.
Innovation
Another innovative aspect of the project was the use of vibrating technology to bed pipe in fine material to protect the pipe from damage and increase its longevity. This was done by the pipe itself while pouring the fine material into the trench with a hydraulic plate compactor on a 20-ton excavator.
Van den Bosch said Aquaduct SuperPipe used on the project is made from material that has a tensile strength 25 percent stronger than the minimum strength required to be classed as PE100 and has a thinner wall than standard pipes, although at this point the pipe is unrated.
“SuperPipe is lower in price because less raw material is required,” he explained. “It is lighter in weight, so is easier to handle and installation is faster. Thinner walls provide faster weld cooling times. Larger internal diameter means lower friction losses.”
Each end user had a ‘turn-out’ which consists of an isolation valve and a pressure/flow regulation valve that is connected to a PLC which in turn is connected to the main control computer via a radio network.
Actual irrigation of cropland is accomplished with spray irrigation, using center pivots.
The 50 miles of pipe on the Valetta Scheme was produced in just over two months and installed, complete with storage dams, outlets and controls, in approximately 12 months. A control gate and screening systems on the Rangitata Diversion Race allows water into the pipe system.
Reflecting on the Valetta irrigation project, van den Bosch observed that the future of the sustainable world relies on clean water and energy.
“Valetta’s piped gravity-fed irrigation scheme created and delivered efficient use of both,” he concluded.
New challenges
Subsequent to the award-winning Valetta project, the Aquaduct team is working on the Central Plains Water Scheme. Stage one of this project is 80 miles of pipe, also from a water source between two rivers. Equipment on the project includes three big track-mounted Trencor machines: the T1360 used for the Valetta project; T1060 with a 350-horsepower, 63,405 pounds maximum chain pull, and a T1860 with the digging chain powered by a 1,200-horsepower diesel engine and all other functions powered by a 350-horsepower diesel.
Aquaduct NZ specializes in the manufacture of large-bore, long length PE pipe in diameters up to 1.6 m (approximately 63 inches)
Always passionate about watering the earth, young Gerard van den Bosch attracted the attention of university professors when he was only 13 years old for Australia’s first commercially viable drip irrigation system built for his father’s horticultural business.
As an award winning dairy farmer and irrigation specialist, van den Bosch was keynote speaker at a North American Grasslands Conference before 750 delegates.
“The challenges of cost effective efficiency and taming water flow for productive land use, motivate my team at every turn,” he said. “The pleasure of seeing lush pasture, vigorous crops and prosperous land users cannot be underestimated.”
FOR MORE INFO:
Trencor, (419) 869-7107, http://www.americanaugers.com
Aquaduct NZ Ltd., +64 3 2616768, http://www.aquaduct.co.nz
Portable Pipe Manufacturing Plant
Pipe manufacturers produce pipe which is typically shipped to a warehouse location, then shipped to the purchaser for transport to the job site.
Aquaduct NZ changed the process by taking the manufacturing process to the job site for the Valetta rural irrigation system on New Zealand’s South Island. Producing pipe on site greatly reduced shipping costs and reduced the chance of damage during handling and shipping.
It is believed the re-locatable manufacturing plant on site is an industry first. The mobile plant was set up on railway lines with timber sleepers in a massive 21,500 square-foot tent. The plant has three extrusion lines and it takes between six to eight weeks to move to a new site. The plant can produce up to 132 tons of pipe per day.
Valetta Project Wins Prestigious Award
Aquaduct NZ Ltd. received the 2014 Award for Innovation from Irrigation NZ, an organization leading efforts for sustainable irrigation in the nation with a primary focus of addressing irrigation challenges and opportunities and water resource management at national and local levels.
Irrigation NZ Chief Executive Officer Andrew Curtis said Aquaduct deserves national recognition for setting a high bar for other irrigation projects.
“The newly-piped scheme provides better water allocation through the gravity-fed pressurized pumps which improve water efficiency and the amount of land that can be irrigated in this part of Mid Canterbury,” Curtis elaborated. “What Aquaduct and Mr. van den Bosch achieved is literally a world first for manufacturing pipe on site. Their contributions to reduce the environmental footprint of the scheme also can’t be overlooked.”
Comments