May 2015, Vol. 70, No.5
Features
Lump Of Rock Threatens Christmas Bore
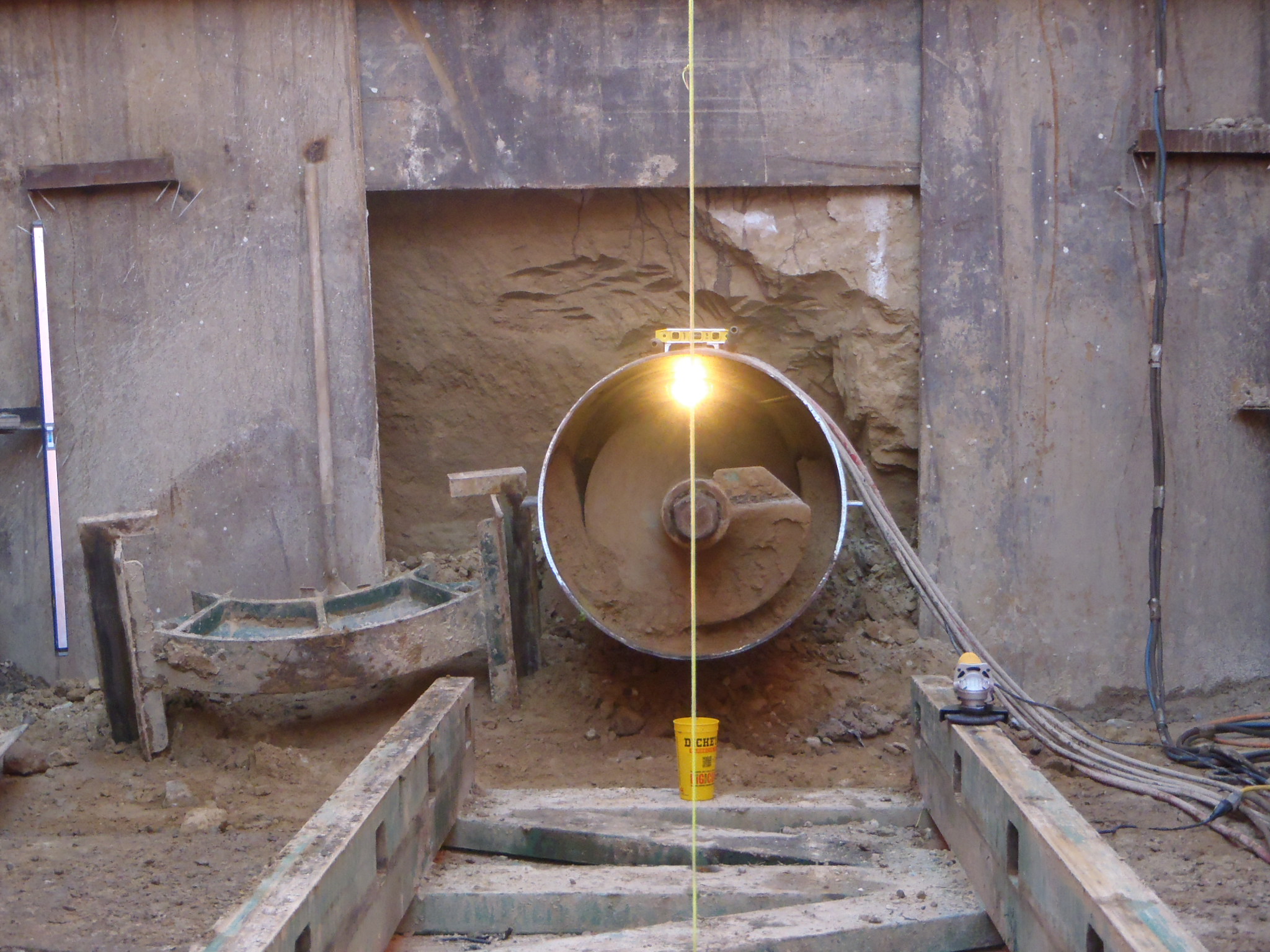
Underground construction jobs are sometimes like Christmas: You never know for sure what you’re going to get.
Nix Construction got a reminder of that last December. It was almost Christmas and an auger boring crew from the Utah company was pushing in pilot tubes for an on-grade sewer line project in their home state and then planning to break for the holiday.
The first bore had gone without issue and they had flipped the auger boring machine around and were starting work on the second one. About 130-feet in, they hit a refusal and couldn’t get through.
“The best I could tell is it might have been a pocket of nested cobbles that we hit perfectly and it just pinned that head and would not let it advance,” says Jon Nix, vice president and COO of the family-owned company. “It wouldn’t let the head push off from side to side, just pinned it and held it.”
Based on a similar experience several years earlier, Nix concluded renting the On Target steering system by McLaughlin was the answer. The system allows auger boring crews to do grade corrections in all directions plus also swallow large material during the bore, and it let his crew displace the cobble rock and advance when the system he was using could not.
That let them work through what ended up being a significant amount of rock and finish the job.
“We had a pretty good feeling that even when we hit the refusal that we could get the job done and take care of the client,” Nix says.
Transitioning to trenchless
The client was the South Valley Sewer District, which provides public sanitary sewer service in the Salt Lake City area. It has about 860 miles of pipes over an area of 105 square miles and the district reports that it has grown greatly in the past four decades.
The project Nix Construction worked on was related to the area’s growth, bringing sewer service to new construction. The bid documents called for approximately 2,300 feet of 18-inch SDR 35 PVC sewer pipe to be installed under a divided freeway. The PVC pipe was to be housed in 509 feet of 30-inch steel casing, which Nix Construction was subcontracted to install.
The company had worked for the sewer district before and is also based near Salt Lake City in the town of South Weber. Jon Nix’s parents, Claude and Barbara, started the company in 1974 as an open-cut contractor primarily installing sewer lines but frequently water as well.
In the late 1990s, they transitioned into trenchless work. The first job came when Nix Construction got a project in Wyoming that included a couple of water line bores, and the Utah boring contractor Jon Nix had lined up for the work told him he didn’t want to go to Wyoming and Nix Construction should do it itself.
The company did just that, renting a Vermeer pneumatic hammer to get it done. It found the economics worked out in its favor and being able to do that work opened it up to other jobs. Today, the company uses a variety of methods, including pipe bursting, microtunneling, pipe ramming, pipe jacking, open cut and of course, auger boring.
Straightforward first bore
The South Valley Sewer District job in December started out normal enough. Nix Construction’s portion of the work was under a new freeway called the Mountain View Corridor on the southwest side of the metro area. The pit was dug about 20-feet deep in the grassy area between the northbound and southbound lanes.
Nix Construction set up for two bores, one in each direction. It used a pilot tube system, which carried the advantage of allowing them to bore downgrade, on grade. The design slope for the sewer line was 0.3 percent.
The crew did the downgrade bore first. A small jacking frame was built in front of the auger boring machine which allowed the auger machine to be used for thrust.
Then the crew jacked the pilot tubes through the ground using, as Nix puts it, “brute force.” There’s no drilling. They go all the way to the reception pit, which in this case was 230 feet away.
For this job, they pulled the pilot tube jacking frame out, put a 30-inch reaming head on the lead piece of casing, and then it became an auger boring job, with the pilot tubes acting like railroad tracks for the casing.
Solution
The first bore had no major issues. Then they turned around and went upgrade. When the pilot tubes got about 130 feet, the jack ran out of force. It didn’t feel like rocks, but they couldn’t get past it.
“We’re careful not to bend or damage the equipment, but the operator was pushing hard enough on it that it was lifting the auger bore machine up off the tracks, and our auger bore machines are 48 inches so they’re 14,000- or 15,000-pound machines,” Nix says. “And he took it as far as he felt comfortable without really causing a problem.”
After retracting the pilot tubes, they noticed some of the lead tubes had a chalky substance on them. It wasn’t clear what it was, however, and they initially did not think it was rock because there was nothing pushing the steering head off to the side.
That’s when Nix made the call to rent an On Target auger boring system. With it, the steering head can be kept on the proper cutting path with hydraulic actuated flaps that open and close, allowing for lateral movement. It also has a built-in vertical alignment sensor and twin line projection halogen lights for improved accuracy.
The On Target system’s active cutter head was the most beneficial feature to Nix Construction. The machine abrades the soil and ingests it through the throat of the steering head, compared with the pilot tube system, in which soil is displaced to the sides of the head.
On this job, the cobble Nix Construction confronted could not be displaced, whereas the On Target system was able to swallow and dislodge the rock, allowing the head and the casing to advance.
When the crew started boring again, they realized it was rock that they’d hit, and not just a little bit.
“We started going through a pretty massive amount of rock,” Nix says. “We had a lot of 6- and 8-inch cobbles come out of the discharge on the auger bore machine, which were able to come through that 30-inch head, thank goodness.”
Nix says that staying up to date on the tools that are available is an important part of being a good underground company.
The crew was a little cautious with that second bore and took its time to ensure the job got done right.
“The customer always remembers when you mess up,” Nix says. “They don’t always remember when you do a good job.”
FOR MORE INFO:
Nix Construction, (801) 479-9000, http://www.chnix.com
McLaughlin, (800) 435-9340, http://www.mclaughlinunderground.com
Comments