April 2015, Vol. 70, No.4
Features
Styrene Still Meets Needs Of CIPP Industry
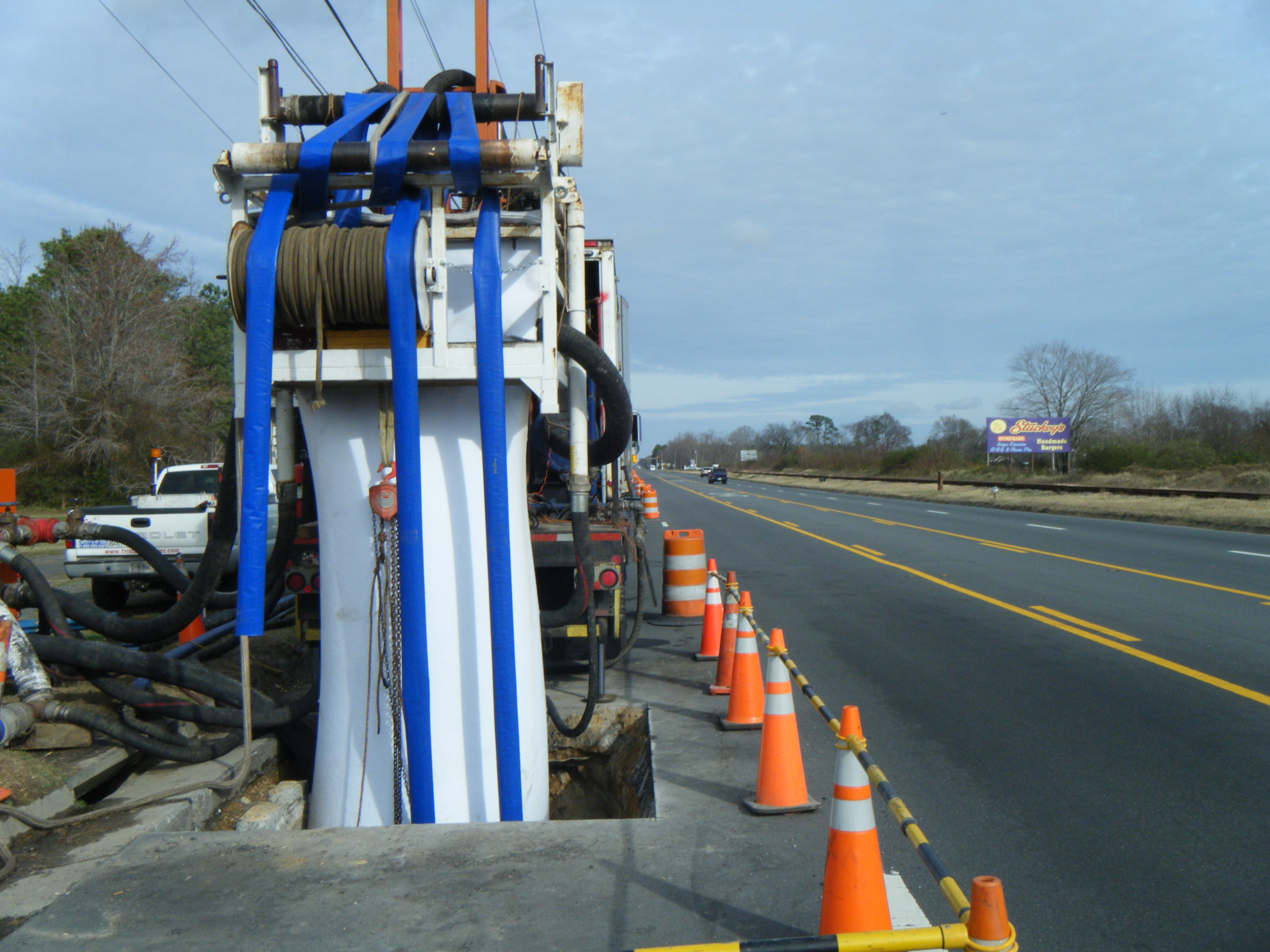
Five years ago when the federal government announced its intent to designate styrene as a “possible” cause of cancer in humans, makers and sellers of a wide range of products containing styrene were seriously concerned, including those in the sanitary sewer rehabilitation industry.
Styrene is a primary ingredient used to manufacture the thermoset resins used in cured-in-place-pipe (CIPP) to rehabilitate sewer pipes.
Would project owners refuse to allow liner containing styrene to be used in their infrastructures? Would a styrene substitute make CIPP too costly to use at a time when it was established as a cost-efficient trenchless rehabilitation method?
Turns out the answer to both questions was “no,” at least for the present.
The possible carcinogen classification has been in place since mid-2013:
• CIPP is doing fine, with CIPP documented to be the most-used trenchless rehabilitation method in Underground Construction magazine’s 18th Annual Municipal Survey (published in the February 2015 issue);
• Most CIPP installations continue to be made with liners containing styrene; and
• Styrene-free liners are available in circumstances that require their use.
“Generally, it has been business as usual,” said Lynn Osborn, technical director of NASSCO (National Association of Sewer Service Companies). “Styrene’s classification as a ‘reasonably anticipated carcinogen’ has not significantly affected the use of CIPP liners containing styrene.”
A rehabilitation industry review has found that the levels of styrene exposure to workers and the public during field installation of CIPP are significantly lower than standards set by the NIOSH (National Institute for Occupational Safety and Health) and OSHA (Occupational Safety and Health Administration) in a typical manufacturing or plant facility. Also, once the installed product is cured, it becomes essentially inert with no long-term associated styrene issues.
Osborn is experienced with CIPP products and process from his 31years of experience as an engineer with Insituform. He now is an industry consultant.
“After the Department of Health and Human Services ruling,” he continued, “the CIPP industry kept waiting for the other shoe to drop, but that has not happened. There has not been any noticeable reduction in projects due to the styrene issue. There have been some jobs switched to non-styrene resins, and also some jobs specified non-styrene resin only. In changing to non-styrene resin, the project owner has to consider the increase in material costs.”
Styrene issues reported to NASSCO members, Osborn continued, usually relate to odor complaints – styrene fumes entering a house because of a dry drain trap or through the foundation: “Questions such as ‘What’s that smell?’ Concern over the unknown, things of that nature,” he said. “Periodically there may be an issue that requires more attention.”
As far as any changes to the CIPP industry as a result of the ruling, there have been some new labeling requirements for resin containers and also changes in safety data sheets.
“It is important that CIPP contractors use good housekeeping practices and installation procedures on job sites to prevent styrene from entering the environment,” Osborn added. “I suspect that styrene changes/issues can be expected to increase in the future, but I don’t expect styrene to go away. The public depends on too many products manufactured with styrene based resins.”
However, Osborn has a word of caution.
“We should not minimize the ‘styrene issue’,” he concluded. “It could be huge for CIPP contractors because they don’t work in a closed plant; they are outside with the public. Although all the evidence seems to indicate that styrene in the concentrations found on CIPP projects is not a hazard, perception can be reality, and it is something we will continue to address.”
Representatives of three manufacturers for the CIPP industry that use styrene provided their perspective.
What major products are using or will be using non-styrene resins as a result of styrene’s designation as a “possible carcinogenic agent”?
Bill Moore, product leader – CIPP, AOC: Resins are used in a vast array of products. Because of cost and performance characteristics, styrene-based resins are the preferred choice when using unsaturated polyester and vinyl ester resins. There are already low styrene and non-styrene based resins available in many of these applications. I am not aware of any concerted effort to move away from styrene based resins based on the change in styrene classification. There is certainly some additional effort in developing non-styrene options, but I still see styrene based products remaining the resins of choice.
Dave Kozman, product manager, RS Technik: For sewer applications, epoxy resins and styrene-free polyesters and vinyl esters are commercially available and utilized extensively.
Kaleel Rahaim, business manager remediation polymers, Interplastic Corp.: The largest conversion from styrene-based resins to styrene-free resins is in the CIPP market. Other markets that may see change are the flooring industry and gel coats. In those areas, the same factors influence the need for an alternative due to odor and environmental concerns. One must be careful when discussing alternatives to styrene based resins: styrene-free does not necessarily imply odor free or environmentally friendly.
Does your company produce non-styrene resins for these products?
Moore: All major resin suppliers have resins that are non-styrene based but not all may offer these types of resins for the CIPP market. Epoxy resins are also available and used in the CIPP market. AOC is well known for its leadership in the development of new products to meet our customer’s needs. AOC has developed low styrene and non-styrene based resins for many years and will continue to be at the forefront of new product development. I do not think that the change in styrene classification will have a major impact on the various markets but as our customers require new products AOC will be in a position to provide the necessary solutions.
Kozman: Most major CIPP resin manufacturers offer a styrene-free product. Since 1994, RS Technik has specialized in CIPP solutions for water and sewer applications, with a specific emphasis on epoxy resins. We utilize epoxy resins because of their flexibility in use for gravity and pressure applications, superior performance and mechanical properties. The evolution of styrene as a “reasonably anticipated carcinogen” has enhanced awareness of epoxy resins which have been utilized in practice for CIPP applications for over 20 years.
Rahaim: Several producers of thermoset polyester and vinyl ester resins, including Interplastic Corporation, manufacture styrene-free resins in one form or another. Our company is a leader in developing VOC (volatile organic compound) free and HAP (hazardous air pollutant) free alternatives for styrene based resins. We continue to develop and fine tune products that are user friendly for various industries.
The belief is that replacing styrene resin with non-styrene resin is significantly more costly. Is that true?
Moore: Styrene is one of the largest volume chemicals produced today, and the cost is significantly lower than any of the replacement reactive diluents which are produced in significantly smaller quantities. The cost of a non-styrene resin can range from 50 percent higher to easily three or four times the cost of a styrene-based resin. The cost difference will vary based on the replacement monomer chosen for the application. Vinyl toluene is the lowest cost alternative but others, including non-VOC monomers, are significantly higher in cost. Because of the chemistry and the necessary physical properties needed with the polymer, costs will vary with the product.
Kozman: As a direct comparison of raw material costs, styrene-free resins are more expensive. However, material costs can be greatly offset by utilizing more efficient installation methods, curing procedures, as well as by eliminating the need for proper treatment and disposal of contaminated curing water.
Rahaim: Styrene is the least expensive reactive diluent that we have. Styrene is a first derivative from oil and natural gas and is produced in very large quantities by numerous producers worldwide. The replacements for this reactive diluent that work well and eliminate the odor and environmental concerns are much, much more expensive, therefore the resultant polymer is more expensive.
Are CIPP liners with non-styrene resins available?
Moore: Non-styrene resins have been available to the CIPP market for many years. Epoxy resins have been used for over 25 years and non-styrene based polyester and vinyl ester resins have been available for 15 or 20 years.
Kozman: Yes, there are several CIPP resins that are commercially available.
Rahaim: Several contractors are using the styrene-free products from Interplastic and other resin producers. Projects using styrene-free resins have been successfully completed in several states in the U.S. and several provinces in Canada. The results have been successful. The products were used either to mitigate noxious odor concerns or because of regulatory issues regarding the release of regulated chemicals in public waterways.
What is the cost difference for CIPP liner?
Moore: The cost difference for a CIPP liner will vary based on the size of the liner as the percentage of cost attributed to the resin is not the same for all liners. There is, however, certainly an increase in cost when using non-styrene resins.
Kozman:The cost difference will depend on a number of factors that are product and job-site specific. From a product standpoint, cost is driven by CIPP diameter, thickness, tube design and construction. From a project perspective, site conditions, contractor approach and economies of scale have a direct impact on the overall cost.
Rahaim: Because of the chemistry and the necessary physical properties needed with the polymer, costs will vary with the product. It’s hard to answer that question because the contractor establishes pricing for the liner installation. The raw material (resin) cost may be two to three times the cost of a standard styrene based polymer, but the installation costs are very similar to the cost of installing a styrene-based system.
Are liners with non-styrene resin as “good” as liners containing styrene? Better?
Moore: For the CIPP market, non-styrene resins must be developed to meet the same corrosion requirements established by the various ASTM standards. They also must meet the required mechanical properties and have the same basic processing characteristics as the styrene-based resins.
Kozman: Absolutely. Styrene-free resins are already viable today, and epoxy resins have been used extensively in the CIPP industry for more than 20 years. All resin systems have their own features and benefits. When deciding on what type of resin to use, a comparative analysis should be performed to determine which resin is best suited for a specific application.
Rahaim: The properties in styrene-free resins must meet the same standards as the properties of a styrene based system. ASTM F1216 is the most commonly referenced document in this matter. The products in the marketplace must meet the corrosion resistance, mechanical property and expected service life requirement referenced in that document and when designed properly do. These alternative resins meet all of the requirements and also tend to be as user friendly for the contractor wetting out and installing the liners as the styrene-based product.
Has the possible-carcinogenic-agent designation impacted the use of CIPP?
Moore: I have not seen any impact on the use of CIPP due to the change in styrene designation. The market continues to experience excellent growth. There has been a significant amount of testing over the years that show that the exposure levels to styrene for the CIPP workers and the public is far below any established OSHA safety limits. I do not see the styrene based CIPP resins used today or the CIPP rehab market in general becoming a non-viable option. If a particular specification does not allow styrene for any reason, there are and will continue to be alternatives available.
Kozman: So far we have not seen a big impact on the industry.
Rahaim: No.
For CIPP liners, where do you see non-styrene products going in the next 12 months? Twenty-four months?
Moore: In the short term I expect non-styrene resins to continue to be more of a niche product in the CIPP market. The biggest reason non-styrene resins are occasionally specified today is the potential for odor issues in certain applications. Styrene odor can be detected at extremely low levels and the general public is not familiar with the styrene odor, and it can occasionally become an issue even though the exposure levels are too low to pose an actual safety concern. Looking further down the road, non-styrene based resins may have the potential to meet the requirements for use in potable water CIPP applications. This approval could significantly expand the use of non-styrene resins in this growing segment of the CIPP market.
Kozman: That is hard to say, as it will be driven by federal, state and local regulations. As awareness increases, I believe that styrene-free CIPP products will see a steady increase in market share.
Rahaim: The use of these alternative products will remain a niche market because of the price difference. Contractors have options for reducing the migration of styrene into the environment on less critical projects. On projects where styrene being released into a public waterway or the noxious odors of styrene is causing severe complications, the alternative styrene-free option is a viable alternative. The use of the styrene free option will continue to grow as contractors and owners assess its benefits. Perhaps the largest potential market for the styrene-free product is in the renovation of drinking water lines. Currently the only option available using the CIPP process is in the use of epoxy resins. Epoxy resins offer advantages and disadvantages in the CIPP process. These styrene- free alternative resins may provide an answer to the disadvantages of epoxy based CIPP systems in some applications.
FOR MORE INFO:
NASSCO, (410) 442-7473 (PIPE), http://www.nassco.org
Interplastic Corporation, (800) 736-5497, http://www.interplastic.com/
RS Technik, (919) 481-1977, http://www.rstechnik.us
AOC Resins, (901) 854-7291, http://www.cippresins.com
Comments