October 2014, Vol. 69, No. 10
Features
Hallmark Project Makes Strong Case for Pilot Tube Guided Auger Boring
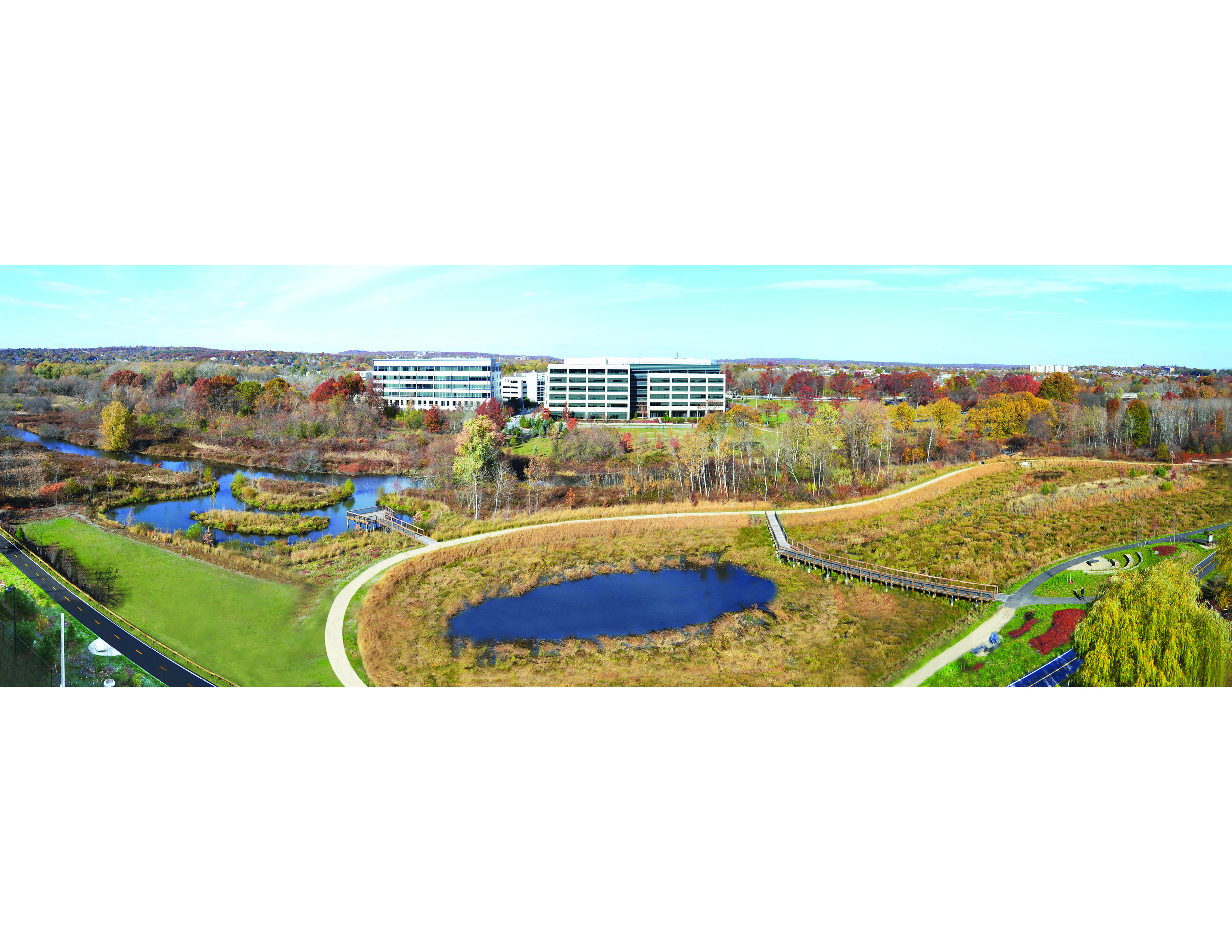
Given the remarkable capabilities of trenchless technology, crossing a body of water known as the Little River in Massachusetts using horizontal directional drilling (HDD) doesn’t seem like it would be all that difficult.
Yet as engineers and design consultants involved in planning details of a utility relocation project beneath the Little River discovered, what may appear – on the surface – as a fairly conventional HDD project would be anything but “routine.”
Relocating a series of existing underground utilities was necessary for constructing a 3.4-acre wetland in the Alewife Reservation, a 120-acre park located in Cambridge, MA, and nearby Arlington and Somerville, MA. This is one of many initiatives specified in the overall plan developed and initiated by the Massachusetts Water Resources Authority (MWRA) to replace a decades-old combined stormwater/sanitary sewer. The projects are necessary to control flooding overflows created by significant weather events. Over the years, as the volume of sewer waste and stormwater entering the combined sewer increased, the capacity of the antiquated system had become incapable of managing the increasing volume as overflow events had become more frequent, contributing to the pollution in downstream water bodies while also creating a public health hazard.
In addition, these combined flows from nearby streams and rivers within the Cambridge watershed eventually empty into Boston Harbor – one of the many sources contributing to the horrific pollution that transformed the once pristine and historic harbor into an environmental nightmare.
In 1983, the U.S. Environmental Protection Agency (EPA) filed a lawsuit citing the Boston area Metropolitan District Commission (MDC) for violation of Massachusetts’ water quality regulations. As a result of the court’s decision, several important cleanup initiatives were implemented in an attempt to curb the amount of pollution entering the historic harbor. Among these was the massive $3.4 billion stormwater sewer project which was implemented by the MWRA and the Commonwealth of Massachusetts to radically improve the outdated Cambridge system. When construction is completed in December 2015, the Alewife wetland, designed as a natural system to attenuate and treat stormwater before being discharged into nearby Little River, is projected to reduce combined sewer overflow (CSO) by 84 percent, a reduction of more than 43.6 million gallons annually.
Construction of a natural wetland on an area within the Alewife Reservation once referred to as “the Great Swamp” quickly became the centerpiece of the Alewife stormwater project. By restoring the land, owned by the Massachusetts Department of Conservation and Recreation (DCR), to its original state, the newly constructed wetland will serve as a natural filter for stormwater, while also providing a host of recreational amenities and educational opportunities for local residents. Several local, state and federal agencies joined in cooperation to implement the project, including the DCR, the city of Cambridge, the Massachusetts Water Resources Authority (MWRA), and several local community groups, area residents and property owners.
Changing technology course
The design-bid-build plan specified relocating an existing network of underground utilities to build the Alewife wetland. To accomplish this, the utilities would need to be relocated from one side of the project, across the wetland area and the Little River to the other side, where each utility would then be reconnected to existing infrastructure. Initially, HDD was recommended as the installation approached, but engineering consultants with Kleinfelder of Cambridge, MWH Americas Inc. of Boston and Brierley Associates, of Manchester, NH, later altered the plan after extensive soil investigations that included 17 test bores – drilled to depths of 18 to 30 feet – revealed the presence of varying layers of fill, organic deposits, marine sand and marine clay below the surface.
“The properties inherent in any one of the various soil types present beneath the surface would have been challenging enough,” says Jay Perkins, geotechnical consultant with Brierley Associates. “Crossing the nine sets of railroad tracks in the area, including two commuter rail lines, with minimal impact on their systems and schedules was a challenge in and of itself. But combined with the many varied soil compositions beneath the surface presented several potential challenges given that the properties of these types of soils are very loose and porous and don’t hold together very well.”
“Maintaining the integrity of several underground bores within close proximity of each other using HDD was of great concern,” says John Struzziery, P.E., with Kleinfelder, with northeast headquarters in Cambridge. “Since HDD requires the use of drilling fluids (mud) pumped at a high pressure into machine tooling to transport cuttings out of the bore path, there was potential risk of inadvertent returns.
“A change in ownership of the property where the HDD equipment staging area was to be located, along with a court ordered completion deadline and concerns by property owners about potential construction disruption using HDD, were considerations that prompted the project team to recommend an alternative installation method after the project was bid,” Struzziery explained. “Using pilot tube guided auger boring would allow us to set up all the necessary staging and equipment, including launch and receiving pits, within the confines of upland areas, not part of environmental or wetland areas and owned by the city, all of which helped expedite completion more efficiently to meet our deadline. But more importantly, the auger boring process would allow us to more effectively mitigate risks we would have faced using HDD.”
Monumental and model design-bid-build
More than two decades of study, engineering and planning was involved in formulating the design for upgrading the former system of underground stormwater pipeline and sanitary sewer lines to create a new series of interdependent, complementary elements for treating stormwater, managing flooding and meeting pre- and post-peak discharge requirements. In addition, the project would restore the area to its original wetland state, which over the years had deteriorated into an “ecological wasteland.”
After reviewing the many soil samples and identifying the various properties, it was back to the design drawing board for the city, Kleinfelder, hydraulic consultant MWH, geotechnical consultants Brierley Associates and contractor P. Gioioso & Sons, Inc. of Hyde Park, MA. All demonstrated great responsiveness and a proactive and collaborative approach to the project, always mindful of anticipated results and anticipating challenges obtained by the geological survey. Selecting an appropriate trenchless method – in this case a shift from HDD to pilot tube guided auger boring – to effectively overcome the many challenges associated with boring through soft organic and marine clay deposits at relatively deep excavation depths, was an integral component of completing the job without incident.
The project management team selected a Bohrtec BM6000LKS auger boring machine with 265 tons of jacking force and 22,500 foot-pounds of torque along with a Theodolite guidance system to tackle the complex and intricate project. Double wall 5.5-inch outer diameter pilot tube rods, a bentonite lubrication system, a 250-psi bentonite mixing pump and 3,000-psi high pressure water pump station for jetting, rounded out the inventory of auger boring equipment for the job. In addition, a four-inch pulling adapter, designed and manufactured by ICON Tunnel Systems and an eight-inch pulling adapter/expander cone manufactured by Bohrtec were also required. Specific to the eight-inch diameter HDPE gas line, NSTAR Gas, the local utilities provider, required that the forces acting on the pipe not exceed a certain threshold. A special TensiTrak sensor system, manufactured by Digital Controls Inc., proved instrumental in effectively monitoring force being placed on the HDPE pipe during installation.
Utilities relocate
The utilities relocated consisted of three, 4-inch-diameter HDPE lines for AT&T Telecommunications, one eight-inch HDPE line for NStar Gas and a 36-inch Hobas pipe acting as a carrier pipe for six 6-inch diameter HDPE ducts for high voltage cable bundles for NStar Electric. The three 4-inch HDPE lines were first to be installed, followed by the eight-inch HDPE gas line, and finally, the 36-inch electric conduit with bores measuring 430 feet in length. The invert (largest pipe) was positioned approximately 23-feet below surface grades surrounding the Little River.
A launching pit measuring 26-feet long by 20-feet wide by 24-feet deep was constructed where the pilot tube machine was positioned, followed by complimentary 20-foot long by 20-foot wide by 20-foot deep receiving pit. The four- and 8-inch HDPE installations were completed using a two phase method. Once the pilot tube auger boring machine was assembled and positioned securely in the jacking pit by installation contractor P. Gioioso & Sons, the pilot bores were initiated and successfully reached the receiving pit on line and grade. The pilot bore head was then replaced with the pulling adapter and attached to the HDPE pipe for pullback. The process was constantly monitored by the TensiTrak sensor unit to assure the pipe was pulled into place accurately and securely.
Monitoring the forces exerted on the HDPE pipe during installation was essential because if the pilot tube system is subjected to too much pulling force, the pipe can elongate and reduce the wall thickness. Pullback forces measuring from 7,000 to 8,000 pounds were common during the pullback process, well below the pre-established threshold of 18,000 pounds.
Lastly, installation of the 36-inch Hobas pipe required the installation team to perform a traditional three-phase pilot tube installation process, beginning by first establishing the pilot bore successfully on line and grade. The 16.5-inch auger head was then attached to the last pilot tube to expand the bore path diameter, followed by the installation of steel casing using augers that followed the auger head until reaching the receiving pit. The process was concluded successfully by attaching a 38.3-inch hydraulic extension kit to the last 15.5-inch steel casing to increase the bore diameter to its final size. Lastly, the 36-inch diameter Hobas carrier pipe would follow the 38.6-inch hydraulic extension kit on line and grade on route to its final destination at the reception pit – all without incident.
“Pilot tube guided auger boring proved successful in many ways,” says Struzziery. “This installation method proved it is a flexible approach and capable of installing five pipes on line and grade in close proximity from one launch pit while significantly reducing risks of possible inadvertent returns under the river, which were concerns using HDD. Also, using auger boring, we were able to greatly reduce the staging footprint and stay within the parameters of the easement and stay outside of designated wetland areas. Given the success of the pullback installations on this job, we can also safely say that the pilot tube guided auger boring process is 100 percent effective for installing HDPE or other plastic pullback pipe materials successfully.”
The 48-inch-diameter pilot tube guided auger bore, was designed by Kleinfelder and Brierley Associates, and is one of largest and longest auger bore of its kind.
Environmental model
“Alewife is a prime example that demonstrates how the quality and safety of our infrastructure can be accomplished in an environmentally sound way,” says Massachusetts Energy and Environmental Affairs (EEA) Secretary Rick Sullivan. “The project represents years of cooperation among federal and state agencies working together with local communities to achieve common goals, and also serves as an extraordinary example of what can be accomplished when new methods of stormwater management are undertaken with creative design and effective funding.
“Flexibility, tolerance, patience and perseverance demonstrated by all members of the team of diverse agencies, environmental interests and local communities were instrumental in achieving success at Alewife,” says Struzziery. “It’s a powerful example of how innovative science, engineering and ecology can work concurrently to not only resolve infrastructure challenges in an environmentally sound way, but also create recreational amenities and educational offerings for the greater benefit of residents and the community.
“All of us involved in the project came away with a deep sense of pride and accomplishment. These combined efforts, along with numerous other enhancements, have improved the condition of one of Cambridge’s most notable amenities in a remarkable way.”
Ongoing underground upstream sewer separation projects are currently underway as the team of engineering, consulting and regulatory agencies look ahead to the final completion of this impressive, award-winning project, currently on track for anticipated completion in December 2015.
FOR MORE INFO:
Kleinfelder, (617) 498-4685, www.kleinfelder.com
ICON Equipment, (800) 836-5011, www.iconjds.com
Digital Control Inc., (800) 288-3610, www.digital-control.com
Hobas Pipe USA, (800) 856-7473, (281) 821-2200, www.hobaspipe.com
Brierley Associates, 617.714.5784, www.brierleyassociates.com
P. Gioioso & Sons, Inc. (617) 364-5800, www.pgioioso.com
Comments