March 2014, Vol. 69 No. 3
Features
Laney Find New Tech Solution For Challenging Crossing
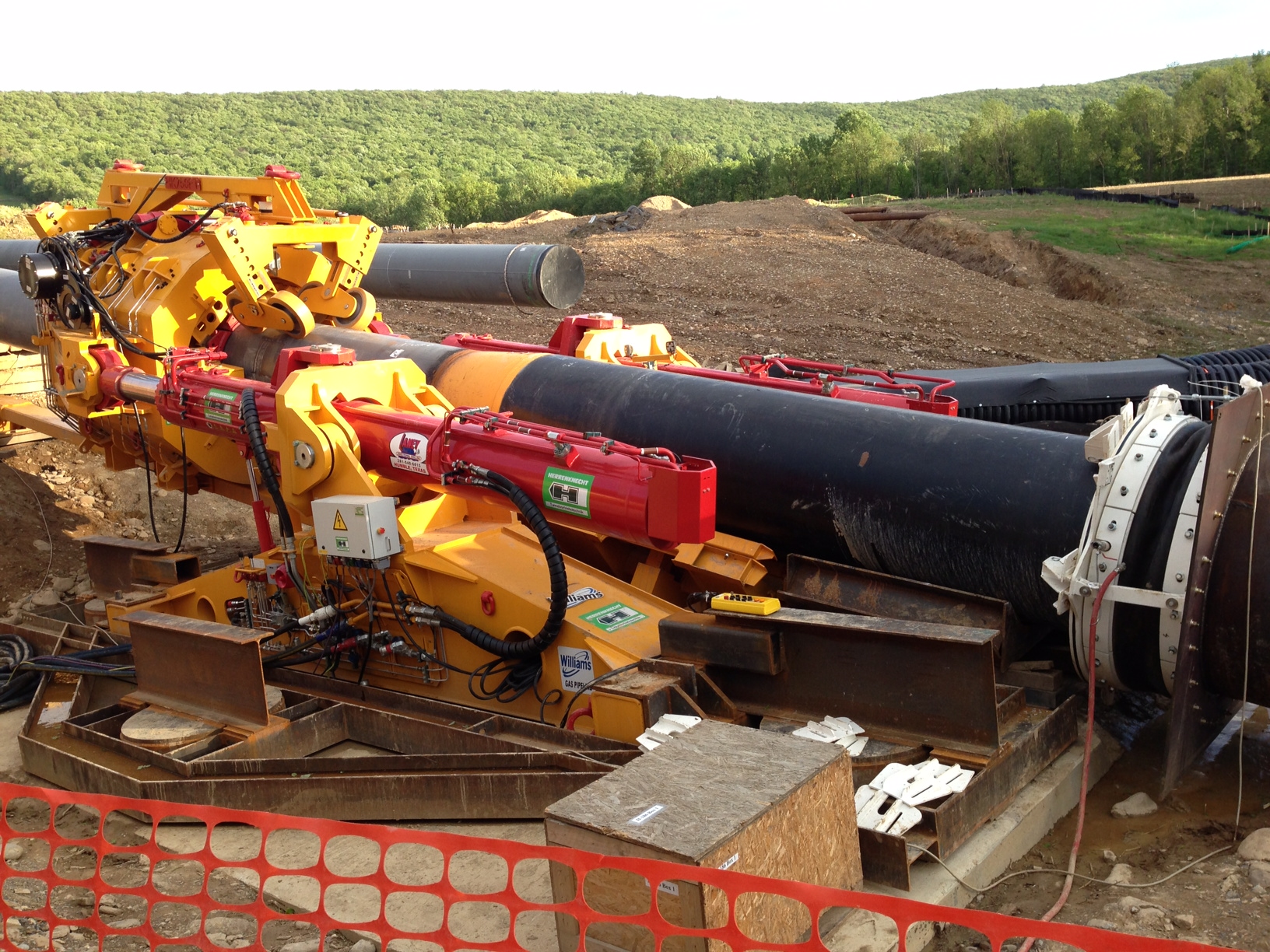
Texas-based contractor Laney Directional Drilling recently employed Direct Pipe technology to make an underground wetlands crossing on a segment of a major pipeline project in the Northeast United States.
It was the longest application to date of the process in the United States.
The Direct Pipe (DP) process is described as combining the advantages of horizontal directional drilling and microtunneling. DP technology and equipment for the project was developed and manufactured by Herrenknecht AG, Allmannsweier, Germany.
Laney used the DP trenchless method to install 1,350 linear feet of 42-inch diameter steel pipe to cross Aquashicola Creek in Monroe County, PA. The crossing was in a conservation wetlands easement considered a habitat for bog turtles, a critically endangered species.
The project owner is Williams with the DP segment a part of the Palmerton Loop pipeline project. Laney was the prime contractor. GeoEngineers provided design consultation and on-site construction representation with Laney’s engineering division providing a feasibility analysis and initial design oversight. Laney also handled construction services for the DP crossing. The installation also was supported by mainline contractor, U.S. Pipeline.
Use of Direct Pipe technology was necessary because of recognized environmental, geological and topographical concerns, said Alan Snider, P.E., Laney vice president of engineering.
“Aquashicola Creek flows through a valley with steep ridges on either side,” Snider explained. “That made topography of the area challenging for directional drilling. An HDD design would have to be significantly longer in order to get the pilot bore under the creek at a sufficient depth to alleviate risks of hydraulic fracturing and inadvertent returns.”
A longer crossing route also would have added logistical issues regarding the pipe stringing area, Snider continued. Complex subsurface conditions included rock, shale with layers of gravel, and cobbles which would pose additional challenges if directional drilling was used.
Alternative solution
Snider said DP technology eliminates the requirement for deep entry and exit pits. It allows pipe to be installed from a surface entry point (with entry casing or a shallow entry pit) to a surface exit point or shallow exit pit. The product pipe is pushed using an above-ground thruster along with a slurry microtunneling machine. Horizontal steering also is possible, if required. The process significantly reduces risks of bore-hole collapse. Pipe is installed by steering an articulated Direct Pipe machine vertically down to desired depth and then up to desired exit elevation.
Because of a low risk of hydraulic fracturing, the DP method can be designed at lower depth of soil cover.
The project is the first time Williams has used the DP procedure for an installation, said Angela Williamson, P.E., Williams’ senior engineer.
“The complicated geology, topography and environmental sensitivities were major concerns for this project,” Williamson continued. “DP is a technology that has had little exposure in the United States. Williams was willing to use the technology because it was well suited to this particular project. Not only was the pipe successfully installed but a record was set for the longest DP installation completed in the U.S.”
DP tech
The Herrenknecht Direct Pipe system consists of a pipe thruster and steerable tunnel boring machine (TBM). A gyroscopic compass is used as the guidance system in addition to a traditional water level to aid in navigating the TBM.
“The pipe thruster clamp is used to thrust the pipe inside the tunnel being mined by the TBM,” Snider continued. “The thruster also provides the face pressure required by the cutter head. The narrow annulus is filled with viscous slurry for lubrication only and is not under significant pressure. A launch seal at the start of the tunnel prevents annulus fluid from coming out of the tunnel.”
Because of the low annular pressures typically measured during installation, the potential risk of hydraulic fracture of the formation and creating an inadvertent return is greatly reduced, said Snider.
On-site preparations were a major part of the project.
“Set-up began with foundation work, welding of the product pipe and installation of an umbilical inside the product pipe,” Snider explained. “Then the pipe thruster and launch cradle were placed on the foundation. The DP machine components were assembled on the launch cradle. After the DP machine was completely assembled, the umbilical hoses and pipes were assembled inside the product pipe and welded to a transition piece attached to the TBM.”
Tunneling started after the welding was complete and all umbilicals were connected.
Due to limitations of the pipe stringing areas, the project required two pipe string sections of 702 feet and 741 feet for the construction of the crossing (additional length was required on the entry side between the DP machine and entry point). The second section was welded to the first section and X-rayed after the first section was tunneled and installed.
“To stay within the project tolerance, man-entry, in-pipe surveys were made at 700 and 950 feet,” Snider explained. “After breakthrough on the exit side, coatings on the two sections of product pipes were checked. The checked product pipe coatings were inspected and found in good condition.”
The cutting solids obtained from the tunnel were separated using a cleaning system. Solids were tested and then transported offsite to a manufacturing facility to be used to make modular blocks for retaining walls and pavers.
Laney started demobilization of the site after the product pipe passed the owner’s post installation testing.
The Aquashicola Creek project took about three and half months including mobilization and demobilization.
The overall expansion project involved the construction of 13 miles of additional 42-inch pipeline loops and additional compression and existing facility modifications.
Passing the test
Snider said Laney will use DP technology again on projects in situations where it is the best option.
“We would use DP for the crossings which are difficult to be installed by HDD,” he explained. “One of the main advantages of DP is its very low hydraulic fracture and inadvertent returns potential. Therefore, it can be used in weak soil formations where hydraulic fracture risks are high. With DP, higher factors of safety against hydraulic fracture can be achieved without increasing depth and length of the crossing.”
Williamson said Williams will consider DP technology when faced with the requirement to perform trenchless installations where the typical HDD installation process is not feasible.
“In essence,” she concluded, “Direct Pipe is a new tool in our toolbox when the circumstances are appropriate to utilize it. We will consider such utilization if all other conventional types of installation are deemed infeasible.
Williams is one of the leading energy infrastructure companies in North America. It owns interests in or operates 15,000 miles of interstate gas pipelines, 1,000 miles of NGL transportation pipelines and more than 10,000 miles of oil and gas gathering pipelines. The Williams’ Transco pipeline delivers natural gas to its customers from Texas to New York.
Based in Spring, TX, Laney Directional Drilling has HDD capabilities to install pipe in diameters of four to 60-inches to distances of more than 11,000 feet. Over the years, Laney crews have earned the reputation of being able to complete long bores to install large-diameter pipes in extremely difficult conditions.
Laney designs and builds its own directional drilling equipment, and currently operates 14 drill units ranging in size from 100,000 to 1.7 million pounds of pullback. The 1.7-million pound machine is powered by two, 1,000 horsepower engines.
Herrenknecht is a leading manufacturer of mechanized tunneling equipment for working in all diameters, geologies and in all areas of application, including railway, metro, road, utility, pipelines, hydropower, mining and exploration.
FOR MORE INFO:
Laney Directional Drilling, (281) 540-6615, http://laneydrilling.com
Herrenknecht Direct Pipe, +49 (0) 7824-302-0, http://www.herrenknecht.com
Williams Companies, , http://co.williams.com/
Comments