July 2014, Vol. 69 No. 7
Features
Maintaining Gas Lines In The Gateway City
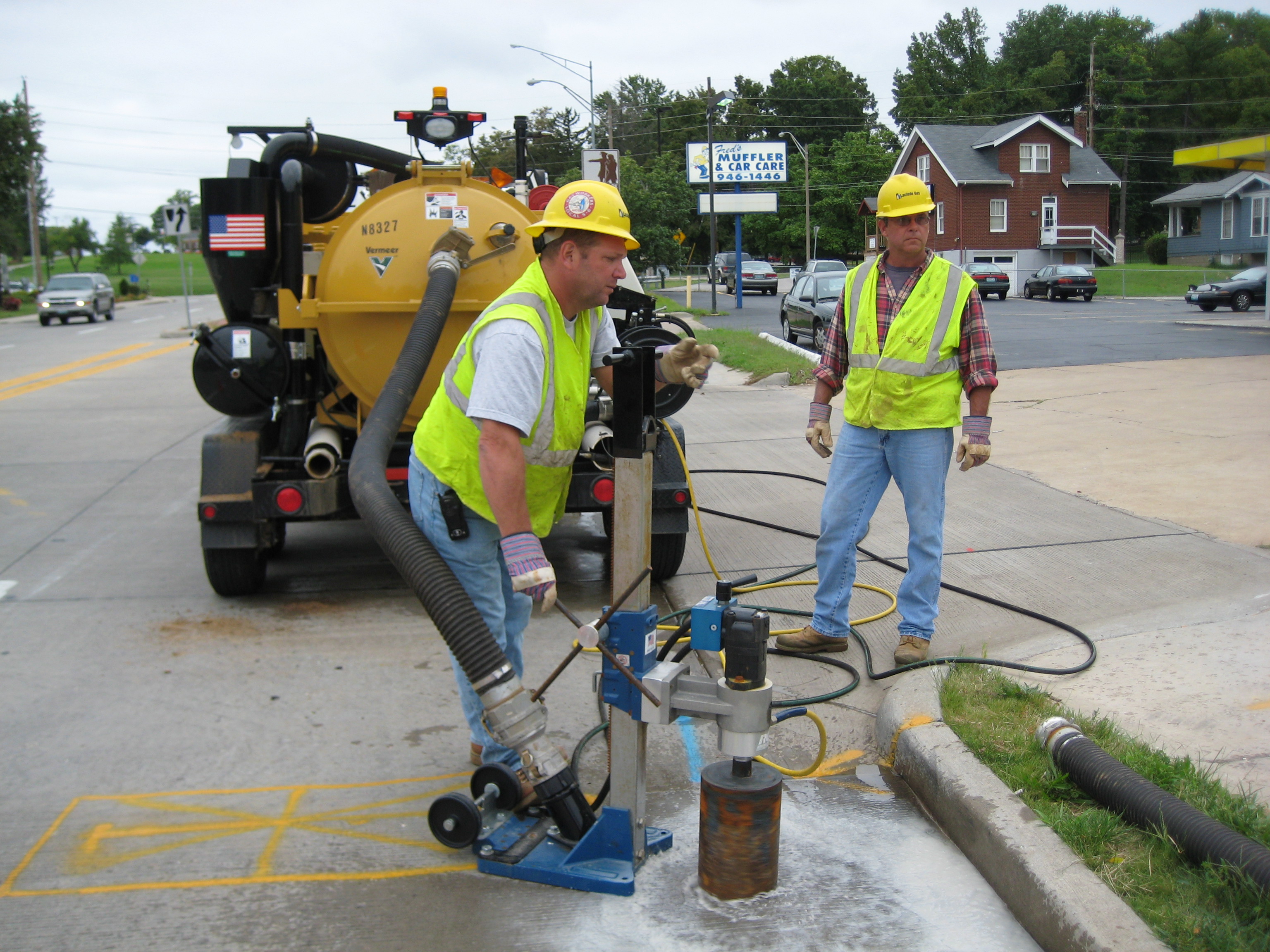
Ask any underground contractor what is the most crucial element to a successful utility installation operation, and you will almost always be told to follow proper utility locating procedures.
Best practices recommend “potholing” – using a locator augmented with a vacuum excavator to visually identify underground utility lines prior to digging.
Potholing is easily accomplished in dirt. However, when utility lines need to be visually identified underneath a street, it’s necessary to break apart the concrete or asphalt. This adds additional expense and time to a job. An alternative to jackhammers and replacing concrete sections is a technique called keyholing, which has been widely adopted by many utility companies and contractors.
Keyholing (or coring) is a process where a crew utilizes a vacuum excavator in combination with a core drill. The drill has a circular saw – anywhere from 6 to 12 inches in diameter – and is powered by the vacuum excavator’s hydraulic pump. The drill cuts a uniform hole into pavement or asphalt, minimally impacting the surface structure. Once the vacuum excavation process has exposed the existing lines and utility work has been completed, backfill material is used for reinstatement, the fill material is compacted and the core is grouted back in place, leaving the road surface with minimal disruption.
Laclede Gas Company is the largest natural gas utility in Missouri. The company provides natural gas service to more than 645,000 customers throughout eastern Missouri, including Greater St. Louis (combined statistical area), which is the 19th-largest metropolitan region in the U.S. According to its director of operations support, Steven Wahlig, Laclede has 138 crews who work throughout St. Louis and eastern Missouri.
The Laclede Gas construction and maintenance department employs more than 500 utility professionals responsible for maintaining more than 16,000 miles of gas lines. Wahlig says the division handles everything that is required in the natural gas industry.
“We install new mains and new services, cathodic protection, leak work – anything that you would have in the gas industry. I can run off 30 or 40 different scenarios. We do everything that’s out there that requires installing and maintaining our system,” he says.
The 136 individual crews are specialized by type of work. There are 38 main line crews, 50 service and installation crews and 50 leak crews. With that many crews working to maintain the expansive network of gas lines, Laclede needs to stay efficient, yet the crews will expose utilities nonetheless.
“We have somewhere in the neighborhood of about 115 municipalities that we work in, as well as state and county roads,” says Wahlig. “They all have different requirements when it comes to breaking pavement. For the most part, most municipalities are on board with the coring method.”
“We could spot utilities by hand using a shovel, but the preferred method is to use a vacuum excavator,” explains Ray Hill, equipment foreman for Laclede. “Our type of work right now is upgrading the existing infrastructure. We have old cast iron low-pressure mains and we are replacing them with polyethylene pipe. Most of those older main lines are out in the street under some type of pavement, either concrete or asphalt.”
VacEx tech
In an urban environment such as the streets of St. Louis, locating utilities is a challenge with the network of lines below ground. Effectively confirming the exact location of existing utility lines requires more than contacting the One Call system or using a multiple frequency utility locator. It is imperative to expose and visually confirm the locations of underground lines. Vacuum excavators – or “vacs” – have surged in popularity with utility contractors as the most economical and least intrusive method to locate utilities.
Laclede has 15 Vermeer vacuum excavators, which are shared among the various Laclede crews. The vacs feature a McLaughlin core drill attachment that uses the vac’s hydraulic pump to power the saw, eliminating the need for a separate power source. Furthermore, the crew does not need to drill the base into the pavement because the vac’s suction pressure keeps the base securely in place.
According to Hill, the vacs are in high demand among the crews, because the methodology is preferred over breaking concrete and hand digging to expose and visually locate the utilities.
“When you core drill, the only pavement you’re disturbing is what you drill with either a 9- or 12-inch diameter core saw. You’re removing that core and vacuuming down and finding your utility, or doing your keyhole work. Then when we’re done, we put the same piece of concrete back so that you don’t have a discolored or mismatched surface there.
“When we break and hand dig, it usually requires breaking a larger area out. By breaking that, you’re usually fracturing the other concrete and asphalt around it. Instead of just replacing that nine or 12-inch hole, chances are you’re going to have to replace – let’s say if it’s in a sidewalk – you’re going to have to replace at a least a four-by-four-foot slab,” Hill says. “If you’re in the street, it could be as large as a 15-by-15-foot slab that, there again, you’ve got to break out, haul off, replace. Then there are traffic issues involved, such as flagging traffic and plating holes. Using a vacuum excavator and core drill saves quite a bit on cost.”
When directional drilling, Hill explains that crews will typically bore anywhere from 300 to 400 feet. In that stretch the crew will cut approximately 15 cores to expose utilities. He estimates approximately 2½-hours per hole to cut, locate, backfill and replace for each core. That time compared to breaking out concrete is fairly equal; however, it’s the cost savings and minimal disruption that provides the most benefit.
“There isn’t a whole lot of time difference because each crew is equipped with a breaker, so we can break fast,” Wahlig says. “It’s the hauling of the extra spoils. It’s the replacement of more street or sidewalk, whatever it is. But actually to dig it and to find it, we probably have maybe a half hour’s difference. It’s really all about restoration.”
Cathodic protection
Wahlig explains that crews will use the core drill when replacing anodes for cathodic protection. That process is typically handled by leak and maintenance crews with Wahlig’s group supplying equipment for their use.
Sacrificial galvanic anodes are used to control corrosion on steel gas distribution lines. Crews continually monitor the lines looking for indications of corrosion. If there is evidence of corrosion, the crew will take preventive measures.
This is done by installing a replacement magnesium anode and connecting it to the gas line. The anode provides a negative charge to the steel line, which enables the line to resist electrochemical corrosion. With more than 4,000 miles of steel lines to maintain, efficiency is crucial and crews typically use the keyholing technique to get the job done quickly. Once the core is drilled out, the crew will drop the anode into the hole and connect to the main line. Once the connection is made, the hole is backfilled and tamped to the proper depth, the core is then put back and grouted into place.
Having the proper tools and equipment is important to any successful project, but having the proper training on equipment and safety procedures is far more crucial with strong repercussions for the crew if not followed through.
Hill and Wahlig say training is a collaborative approach between their department and McLaughlin, who manufactures the vacuum excavators, and the Vermeer dealer who provides service and support. Training involves classroom discussion and hands-on training on the features and operation of the vac unit and core drill.
“We first go through the machine and point to all the safety components on the machine, such as the lockout systems. Then we will show them how to set up to core hole, cut the core out, and then how to expose the utility using the vac and grout the core back into the pavement,” Hill says.
Wahlig said the cooperation with the dealership is vital because they rely on the specialists to keep them abreast of new features on the vacuum excavators.
“They’re really the resident professionals. We’re not necessarily new at this, but because machines change every year, we need them to come in and help us keep up with technology, and they gladly do. Then we learn right along with our guys,” he says.
With the demands on their crews to maintain more than 16,000 miles of lines around the concrete landscape of St. Louis, Laclede relies on the combined forces of knowledgeable crews and reliable equipment to keep the gas flowing efficiently and safely.
“Although we have been using vac-excavators for many years, we just began the coring and reinstatement process five years ago when we purchased our first core saw to go with a vac unit,” Wahlig says. “Now every vac we buy has a core saw with it.”
FOR MORE INFO:
Laclede Gas, (314) 621-6960, www.lacledegas.com
McLaughlin, (800) 435-9340, www.mclaughlinunderground.com
Vermeer Corp., (888) 837-6337, www.vermeer.com
Comments