April 2014, Vol. 69 No. 4
Features
Selecting Correct Shielding, Shoring
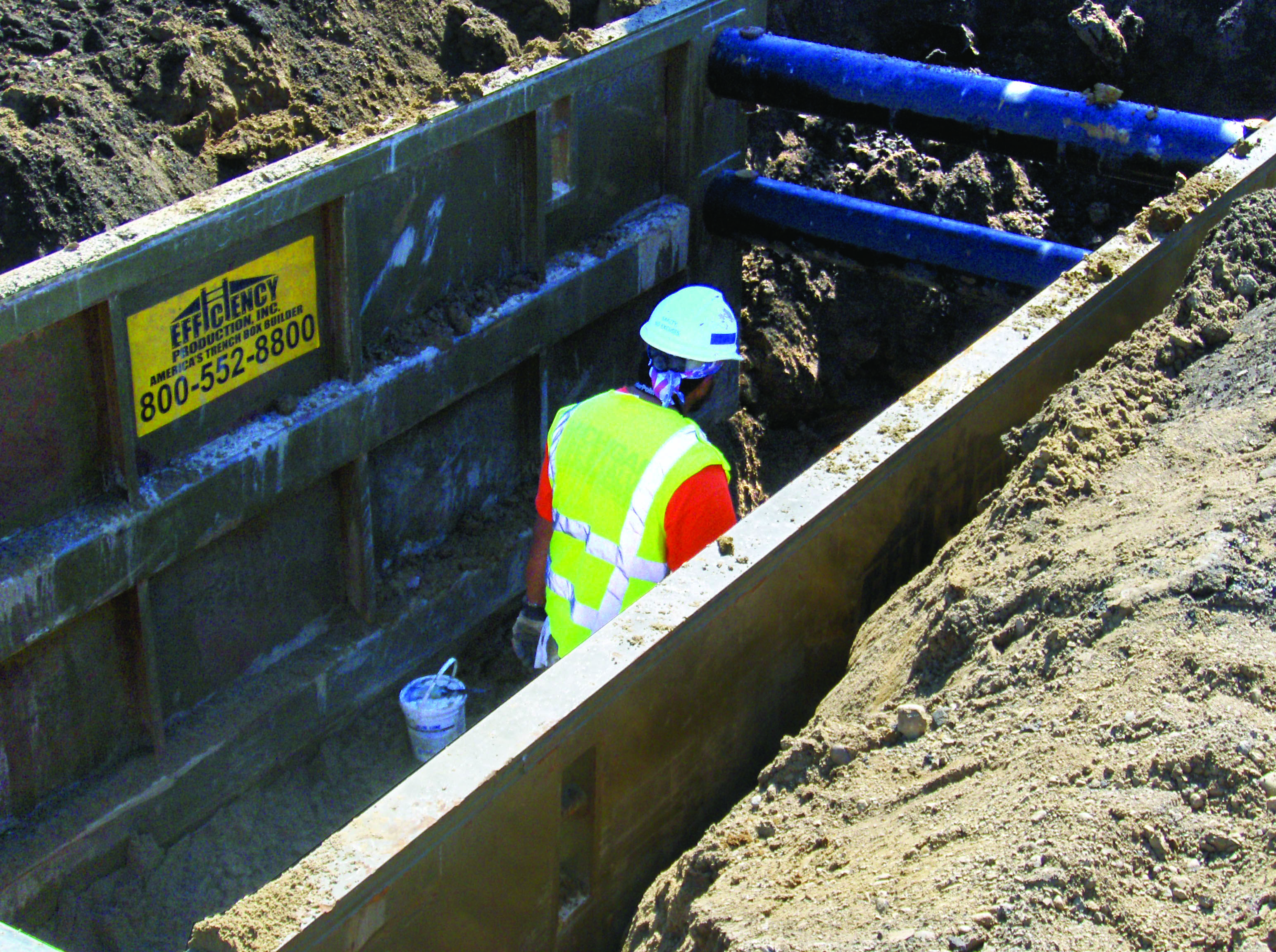
Underground utility construction today utilizes many “trenchless” construction and rehabilitation procedures that may greatly reduce the need to dig trenches or excavations to install and maintain buried infrastructure.
Even so, the bulk of utility work continues to be done by conventional cut-and-cover methods, and many trenchless procedures require launching pits where equipment is placed and receiving pits at the end of a trenchless segment. Much of today’s energy pipeline excavations require wide, deep, man-entry trenches.
Of course, earthwork is not limited to utility projects and preventing the collapse of walls of trenches and excavations has been a challenge since mankind first began digging holes in the ground.
Safety is the primary reason for shielding and shoring walls of excavations and government agencies enforcing standards applying to excavation safety. Trench shielding and shoring also is used to protect existing utilities from possible damage caused by nearby excavating.
Likely the first approach to preventing cave-ins is sloping trench walls, making collapse impossible. However, utility projects today are in locations where limited space does not permit sloping. Over the years, trench protective device options have evolved to meet changing construction needs.
Mike Ross, shoring specialist in the training section of shielding and shoring manufacturer Efficiency Production, said that “traditional methods such as timber shoring evolved from railroad and mining projects. The trench shield or box was a production tool developed in the Great Lakes region to combat the changing soil conditions created by glacial till. Lightweight hydraulic shoring was developed on the west coast and southwest where excavations were smaller due to shallower depths of pipe.”
Shoring product designs evolved to accommodate changing excavation needs and equipment. For example, smaller and lighter trench shields have become more prevalent since the expansion of the mini-excavator’s role in utility work.
“Today, different types of equipment are designed for different applications,” Ross continued. “All our equipment is matched to the excavation equipment used and task to be performed. Because of modular design, systems such as our Build-A-Box modular aluminum shielding system and slide rail shoring systems are most widely used across our distributor network.”
Challenges of underground utilities
Facilitating production and providing a safe work environment are primary goals of product designs, said Ross.
“One of the biggest challenges in underground utility construction,” he emphasized, “is crossing and working parallel to utilities already in place. Some equipment is designed to accommodate in-place utilities. Using methods taught by the manufacturer’s representatives, common systems such trench shields and hydraulic shoring can be efficiently deployed to accommodate and support utilities in conflict.”
Contractors play an active role is selecting the correct shielding and shoring for their projects, said Ross.
“Generally,” he said, “a project’s consulting engineers do not dictate means and methods of construction. The contractor is encouraged to use the most efficient method while staying within the limits of the specifications. The assigned competent person is often tasked with that responsibility.”
Based in Mason, MI, Efficiency Production manufactures trench boxes, slide rail systems, aluminum trench boxes. trench shoring, excavation support equipment and manhole shields.
In addition, Efficiency Production has engineering capabilities to alter tabulated data for specific sites as well as other site-specific engineering services.
The company also has a Special Operations Shoring Division staffed by personnel in underground construction and management. This division can provide efficient rental or purchase shoring recommendations for projects in the United States and specifications and geo-technical reports. During a project, the division can provide on-site technical assistance.
“Late in 2013, Efficiency Production introduced for field trial the Build-A-Box Panel Guide Frame,” Ross said. “Development is complete and the equipment now is available in North America. This system uses a waler connected to the inside front of a standard Build-A-Box to install one-foot-wide corrugated aluminum sheets around crossing utilities near bottom of excavations to allow fast and safe excavating around the conflict and easy closure of space around crossed utility.
FOR MORE INFO:
Efficiency Production
SIDEBAR
Types Of Shielding, Shoring
Whether a small trench box or large slide rail system for large excavations, shielding and shoring systems are available today for most types of utility excavations. This overview of basic products was summarized from information provided by Efficiency Production.
Steel trench shields, boxes
Trench shields and boxes consist of sidewalls separated by spreaders of various lengths to match trench widths. Shields provide a temporary protected opening in the trench for laying of pipe, providing a near vertical trench which is a very safe work space for in-trench workers.
Aluminum trench shields, boxes
Aluminum equipment serves the same function as steel shields but is made of lightweight aluminum and is designed for smaller excavations generally from rubber-tire backhoes and compact excavators. Included in this category are knock-down trench boxes of modular components consisting of two-foot high panels available in various lengths installed with corner posts. This option is effective for a wide range of excavations, including deep sewer and infrastructure projects.
Hydraulic shoring
Hydraulic trench shoring components are lightweight aluminum cylinders that shore or support the banks by utilizing hydraulic pressure arcs. This system is best suited for sites with smaller excavators as all components can be installed by hand.
Slide rail systems
Slide rail systems are made up of steel panels, which are similar to the sidewalls of a trench box, and vertical steel posts. T-Panels slide into the posts, creating a four-sided pit system. Using a “dig and push” method of installation, the panels and posts are pushed gradually into the pit as excavation progresses. Because a slide rail system is installed gradually, it prevents trench wall loss. With its ability to be used in a variety of arrangements, slide rail systems are considered by many to be the most versatile option available.
Slide rails come in several variations: four-sided systems have one panel length on all sides tied together by corner posts. Linear systems have panels on two sides which are extended in a line to keep a long trench open. Panel lengths vary by requirements. Clear span systems have linear posts, corner posts and waler beams inside and outside the panels to provide a clear area without crossing members. This area can be up to 80-feet in any direction and 40-feet in depth. Four-sided multi-bay systems allow for a four-side excavation with one panel of width and unlimited length achieved by adding additional bays in the same way as a linear system.
Manhole shields
Manhole shields have short return walls on the open sides to allow narrow spreaders for pipe laying and wider spreaders at the manhole shield when required to set manholes – this keeps pipe laying as efficient as possible when a manhole is installed.
Accessory equipment
Accessory and support equipment often used on projects requiring excavation shielding and shoring include bedding material containers, portable material separators and pipe pullers to pull large-diameter pipes together.
Comments