October 2013, Vol. 68 No. 10
Features
Internal Corrosion Prevention ‘HDD’ Style
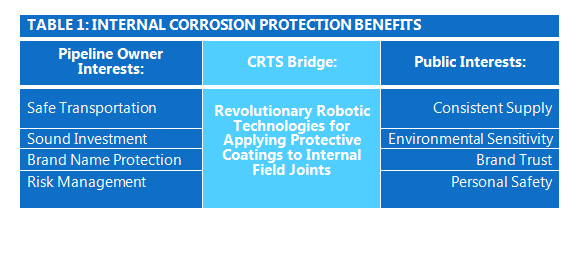
Internal corrosion creates problems wherever it lurks or even flagrantly exists, and with the Floridian Surficial Aquifer System being the sole water provider for Jacksonville, FL, residents, corrosion prevention is absolutely vital.
The Jacksonville Electric Association (JEA) in Duval County, FL, worked with several renowned engineering firms to develop its Total Water Management Program – Segment 2, River Crossing. CRTS Inc. was contracted to apply its corrosion prevention coating service inside and outside the pipe to drastically mitigate corrosion in the pipeline’s notorious weakest link: the internal field joints (IFJs).
This potable and raw water project’s use of horizontal directional drilling (HDD) came with public-interest benefits such as minimal surface damage and traffic disruption, minimal environmental impact and other local advantages. These public benefits were matched by the long-term pipeline owner benefits of CRTS’ internal corrosion prevention coating service.
Internal corrosion prevention is a key player in new construction because it greatly improves pipeline longevity, decreases leaks and overall positively impacts the environment, lessening the chances of devastating environmental setbacks. Both the pipe owner and the end user have vested interests in clean water, but the pipe owner has the advantage of designing and building the pipe to prevent corrosion, and in this case, delivering a pure product to the consumer’s tap. Table 1 demonstrates how IFJ coating bridges the common gap between the pipeline owner and the public, especially for this JEA project, one of the longest HDD projects in CRTS’s HDD history. Michels Corporation of Brownsville, WI, was the HDD contractor.
Project challenges, solutions
Compared to most of the 60-plus HDD projects CRTS has robotically coated, the number of JEA river crossing welds was relatively few, but the obstacles were many. The project involved connecting water systems on either side of the St. Johns River. Eight on/off ramps were closed along Arlington Expressway during the coating portion of the project as a pipeline was placed underneath the Mathews Bridge. One of the geographical challenges was the river itself, with a total drop from beginning to end of less than 30 feet, or about one inch per mile, making it one of the “laziest” rivers in the world.
However, the usual 66,000-plus daily drivers that cross the Mathews Bridge were not lazy. The many lane closures kept drivers busy looking for alternate routes, and often meant that CRTS field technicians were working when there was the least amount of traffic, sometimes at 2 a.m.
Mother Nature brought unusually rainy weather, but CRTS field technicians and robots have endured geographical and environmental nuisances from dust storms to ice storms, onshore and offshore. The JEA’s 36-inch pipe was 1.27 miles long and weighed 2 million pounds, but CRTS’ custom robots easily navigated the monstrosity, as six pipe lengths were strung together, then readied for the full train of robotic equipment: a crawler, a battery cart, a cleaner-vacuum, an FBE coater and an inspection machine.
Coating IFJs follows a simple process: the general contractor pre-cleans and welds the pipe and then the pipe string is X-rayed. CRTS loads its train of equipment into the pipe trough, and then re-cleans each IFJ to create an anchor profile on the fresh weld metal for the coating. Next, the IFJs are coated with liquid or powder epoxy as specified and then inspected visually. Visual inspection is followed by a final dry film thickness and high-voltage holiday inspection. The inspection process enables welds to be repaired before any product is put in the pipe, thus greatly minimizing repair and/or rehabilitation.
For the JEA, the IFJs were coated with a project-specified FBE coating, 3M 6233. After the coating cured, the internal field joints were robotically tested for compliance to the dry film thickness specification and finally, a high-voltage holiday inspection brush was passed over the coated IFJ, detecting any anomalies in the applied coating. The customer was able to view all steps in real time and received a DVD copy of all activities as part of CRTS’ quality assurance pledge.
After protecting the IFJs, CRTS applied the same FBE coating to the OD field joints and topped it off with project-specified PowerCreteJ, an abrasion resistant overlay (ARO) that further protects the OD field joints. ARO was especially warranted because HDD projects are nearly guaranteed to encounter rocks and other natural debris that can damage the external coating as the pipe is pulled. The ARO layer provided a Shore D hardness of more than 85, whereas the normal FBE hardness hovers around 74, sufficient for the IFJ where no rocks or stones are likely to cause damage. Despite the extra cost, ARO coatings are much less expensive than the cost of replacing or rehabilitating pipe, and this benefit is also realized by coating the IFJs.
Protecting residents’ water pipeline
Why all the trouble to internally coat the field joints? Like most conscientious pipeline owners, the JEA coated its pipe with high quality epoxy coating. But to meet the project’s goal of a continuous, fresh water supply to customers, corrosion prevention was arguably mandatory, not a luxury. Coating the IFJs was the first and most important step in transforming the pipeline’s weakest link into its most resilient.
Even without corrosion prevention in place, HDD projects have potential failure modes such as drill pipe shearing, hole instability while reaming and seepage from drilling fluid. Citizen concerns range from sink holes to infrastructure failure such as a highway collapsing. Regardless of the risks, once the pipe is strung together, it is highly vulnerable to internal corrosion if the IFJs are not protected also. There are some other reasons for mitigating corrosion.
For the public: Eliminating corrosion in water pipelines is a win-win investment strategy all the way around.
• The environmental impact on the ecosystem and surrounding neighborhoods should always be negligible. Eliminating leaks at the pipeline’s weakest joint ensures minimal impact;
• Water quality will diminish and leaks increase when internal corrosion is abundant; and
• Decreased water production due to corrosion holes leads to reduced water pressure and increased customer complaints.
For civil engineers: The importance of the Hazen Williams coefficient cannot be understated.
• The higher the coefficient, the smoother the pipe surface and the less energy required to move a volume from “point a” to “point b.” The result is less required energy, less repair and less rehabilitation costs to the pipeline; and
• The smoother the pipe surface the faster the media can flow and stay in a laminar state.
Ultimately, the result is a better product to the consumer, lower OPEX for the owner and coating the IFJs helps attain these desired results.
FOR MORE INFORMATION:
CRTS, (918) 877-5210, http://coatingrobotics.com
Michels Corporation, (920) 924-4300, www.michels.us
Project at a glance
Location: Jacksonville, Duval County, FL
Owner: Jacksonville Electric Association
Design/Build: Haskell
Engineer: Jacobs Engineering
Contractor: Michels Corporation
No. of welds: 168
Pipe diameter: 36-inch
Coating material: ID-OD ~ 3M 6233
ARO: PowerCrete J
Flow product: Water
Comments