May 2013, Vol. 68 No. 5
Features
Where There’s A Will, There’s A Way: Treacherous Terrain Tests The Skills Of An Arkansas Contractor
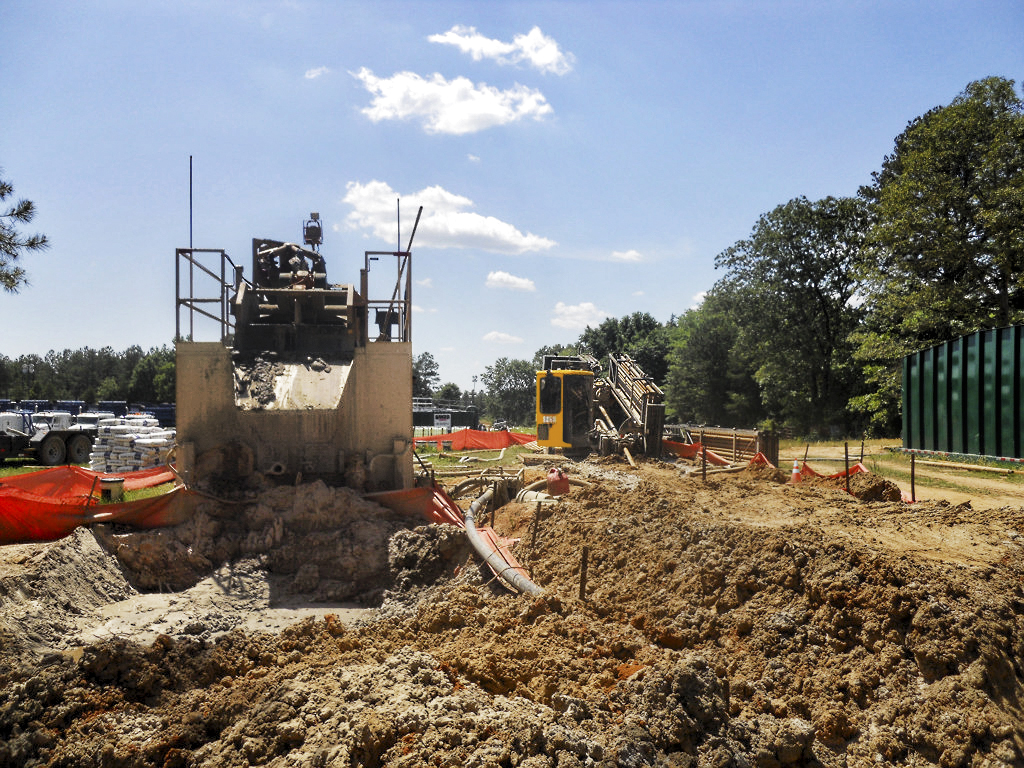
If Ronald Cline was the type to back away from a challenge, it’s entirely possible that a natural gas gathering line, now securely in place in central Arkansas, would likely not have been installed underground. But this conscientious and ingenious native Razorback devised a trenchless approach that resulted in the successful completion of a continuous bore amid some of Arkansas’ most treacherous terrain, and through some of the state’s toughest and trickiest rock.
More than 56 percent of the state — some 18,720,000 acres — is forest land, characterized by steep cliffs of varying layers of hard rock, with hundreds of clear streams and rushing rivers nestled within. Suffice it to say that Little Rock, the Arkansas state capital, is most appropriately named.
Cline, owner and president of Cline Trenching, headquartered in Bono, AR, just outside the city of Jonesboro (pop. 67,000), started his company more than a quarter century ago. In the early days — with assistance of an older-model used trencher — he got by installing water lines and digging house footings. Today, more than 25 years later, Cline Trenching has nearly 30 employees, and a loyal customer base that resembles a who’s who of energy and communication companies including AT&T, CenterPoint Energy and Crestwood Midstream Partners.
The company specializes in pipeline, fiber and, given the abundance of the hard stuff throughout the state, rock quarrying. Cline is personally present on every jobsite — in the trenches working right alongside his crews in addition to supervising their progress.
“I’m on the job every day and still involved with all aspects, from actual drilling to day-to-day operations,” Cline says. “I think my hands-on involvement, and the fact that my crews see me working as hard as I expect them to work, motivates them to do their best. We do quality work; and we do it on time. I tell my guys, ‘It’s not how much we get done today, but what we do get done has got to be done right.’ My word is good and our customers know that.”
One bore, multiple obstacles
Earlier this year longtime customer Crestwood Midstream Partners, headquartered in Houston, approached Cline about installing a natural gas gathering pipeline through the heart of Arkansas’ rugged, rocky terrain. The job involved installing a 12-inch steel line using horizontal directional drilling (HDD) through some of the hardest, most unpredictable layers of rock in the country — conditions all too familiar to Cline and crew.
The drill plan specified a 1,170-foot continuous bore that included a 100-foot underground river crossing at a depth of 150 feet approximately 480 feet into the route. Cline was confident that his Vermeer D80x100 Series II Navigator horizontal directional drill, with 200 horsepower and 10,000 pounds of rotational torque, could handle the rock as proven many times before. The only hesitance was his ability to provide Crestwood with an accurate cost estimate.
“At first I told them [Crestwood] this probably was not the job for me,” Cline says. “I knew the drill was capable of completing a bore of that length and in those conditions. But it was difficult to estimate with a lot of certainty the amount of time it would take, given all the unpredictable variables. We really hadn’t completed a continuous bore combining all those obstacles and challenges before.”
But Crestwood was persistent. Cline had always been their contractor of choice on jobs located within reasonable distance of his home base. Because Crestwood personnel were well aware of the complexity of the bore, they really wanted Cline to be the one to handle it. Yet before committing, Cline consulted with his sales representative at Vermeer Heartland, based in Murfreesboro, TN, for an objective perspective. After their conversation, Cline decided to accept.
“I have as much experience with the conditions here in Arkansas as anybody,” Cline says. “And I didn’t want to put a loyal customer in a bad situation with a contractor from outside the area who was not familiar with the conditions. The rock here in Arkansas is different than anywhere else. I’ve seen contractors from outside come in here unprepared, low-ball their price, then pack up and leave. I didn’t want to see that happen to Crestwood. They trusted us to complete the job as quickly and efficiently as possible. The upfront bid didn’t matter; they just knew we’d get the job done right.”
Challenge No. 1 — Cadron Creek
In devising his drill plan, Cline started by taking GPS readings. First to the bottom of Cadron Creek — a popular scenic paddling stream that flows in a westerly direction from its origin near Heber Springs in central Arkansas — followed by a second reading at the site where the Vermeer D80x100 drill would be positioned. Measurements from the edge of the creek up the side of the hill toward the drill site were then registered so Cline’s crews could accurately calculate drilling depths and distances.
Bordered by fields, farmsteads, bluffs and canyons, the majority of the 59-mile-long Cadron Creek lies out of sight, quietly nestled more than 140 feet below the horizon. While the rocky shoals and rugged bluffs on each side create spectacular scenery for paddlers, the sharp drop and subsequent steep incline in elevation from the drill’s launch site — necessary to hit the exit target — wasn’t all that pretty of a picture for Cline.
“What really made the bore difficult was the elevation change created by the creek,” Cline says. “The drill plan required the depth of the bore to drop quickly within a relatively short distance to make the underground creek crossing, followed by a sharp 110-foot incline to make the target. Also, keep in mind this was one continuous bore through multiple layers of hard rock and in a dense forest. It was a very complicated job.”
Challenge No. 2 — the rock
Drilling through solid rock is one thing; drilling through varying layers of solid rock with areas of void in-between the layers is something altogether different. Having encountered layered rock formations previously, Cline and crew knew how to best prepare.
“The rock here consists of hundreds of layers of different types and varying densities,” Cline says. “To further complicate the situation, there are voids, cracks and spaces between the solid rock layers. Few drilling conditions are as unpredictable as boring through Arkansas rock.
“Cement is the remedy,” Cline says. “Once you start losing an extraordinary amount of drilling fluid, you know you’re drilling through a void. Pumping cement into the area fills the void. After the cement sets up and hardens, it functions like soft rock and drilling can continue. The cement prohibits additional drilling fluid from escaping.”
This was the fourth jobsite where Cline’s crews were required to pump cement into the void between rock layers to better secure the bore path and restrict the loss of drilling fluid. It was the first occasion, however, where it was necessary to add cement at four different points.
“Normally you pump in one spot, drill through it and just complete the job,” Cline says. “We pumped in four places on this project. We would drill for a ways, hit a void, start losing fluids, pump cement in and let it set, then go back and drill through the cement. We repeated this process four times. It really affected our production rates. It had nothing to do with the capabilities of the drill; it was all about the conditions, which is what I was concerned about before I agreed to take on the job.”
Challenge No. 3 — rock reaming
Having been involved in HDD since the trenchless installation method was first introduced, and his trade territory is situated near some of the hardest, most complicated rock in the country, Cline has learned a thing or two about tooling; specifically, reamers. Early on, he had some frustrations with what he considered to be inefficient reamer tooling — especially for boring through rock. “Upsizing capacity for reamers then was limited to two to 3 inches per ream, often requiring multiple passes for a single bore. Most reamers were also hard on equipment with a tendency to steer off course,” he says.
So Cline got proactive.
“I wanted a reamer that would take out no less than five inches of material on a single pass and be easier on equipment,” Cline says. “We worked on a design change by increasing the size of the rollers situated on the front and back of the hole opener. Consequently, on this job, instead of having to ream multiple times, we reamed one time with the new larger roller design. It’s a design approach that we’ve found to be highly successful and more efficient.”
Rarely does any contractor face such diverse and demanding — not to mention unpredictable — circumstances as underscored by the fact that it took Cline more than three months to successfully complete the 1,170-foot bore, a length that under “normal” circumstances, would likely have taken less than 30 days.
Halfway through the bore, the body of the mud motor Cline was using wore out forcing him to pull back and replace it in mid-bore. It took five drill bits to complete the bore and five 18-inch reamers. Despite having lost location of the drill head on three separate occasions, Cline’s crew emerged on the exit side within 30 inches of their target — a testament to the skill, experience and diligence of his drill operators and supporting cast of underground experts.
“I believe in buying the best equipment and hiring the best crews available,” Cline says. “When the guys go out to do a job, they’re able to do it without having very many breakdowns. Our Vermeer drill has been a very reliable, capable piece of machinery. But we also take good care of our equipment and make sure it’s properly serviced. Equipment that’s properly cared for will always take care of you.
“The other thing is that we’re all about the environment,” Cline says. “We try to make everything look just like it did before we arrived on-site. All around, everything we do, we try to do it the best that we can. Just pretend like you’re doing it for the good Lord and he is always looking over your shoulder.”
FOR MORE INFO:
Cline Trenching, (870) 972-6111
Vermeer Corp., (888) 837-6337, www.vermeer.com
Comments