January 2013, Vol. 68, No. 1
Features
When ‘Old School’ is the Right School: Combined Grout, CIPP Effective Solution For Illinois City
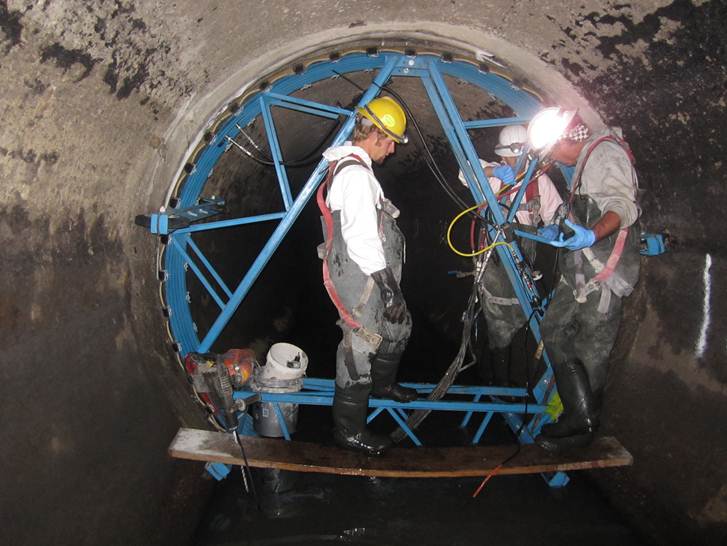
The American Bottom, or Bottoms, is a Southern Illinois area of 175-square miles in the flood plain of the Mississippi River, protected from flooding by a system of levees and canals. The cities in the American Bottom, such as Granite City, IL (population 30,000), have to contend with seasonally high, fluctuating groundwater, which can have a disastrous effect on underground facilities like sewers.
“As the groundwater changes from high to low and back, it can actually shift sewers around,” explains Steve Osborn, P.E. of Juneau Associates, Granite City’s engineering consultants, “If there’s no flow, for example, sewers can float up and in very wet weather they can be compressed.”
The results have been dramatic for Granite City. “The fluctuation has had a drastic effect here, and sewer repairs have been needed for some time,” says Osborn, “High groundwater in the last two years has created sewer failures, sinkholes and even a few blocks of collapsed roads.”
Compounding the problem is the age of the sewers. Many of the larger diameter pipes haven’t had any major work done since installation, about 100 years ago. This all added up to a huge financial burden. Between 1970 and 1985, for example, Granite City spent an average of $600,000 annually on sewer repairs. “Our city had a $10 or $11 million budget at the time,” says former mayor Von Dee Cruse, as quoted in the April 1993 Municipal Review. “The sewer repairs just devastated us. Sometimes a single joint repair would cost $50,000, and then we would have to turn around and repair the same spot a few months later.”
So, with partial funding from the Environmental Protection Agency, Granite City recently completed a massive sewer rehabilitation project. Granite City Sewer Lining and Rehabilitation Project B rehabilitated 15,600 lineal feet of large diameter concrete pipe ranging from 72-inches up to 108-inches in diameter.
The smaller diameter sewer, up to 54-inches in diameter, was repaired with cured-in-place-pipe (CIPP) lining as part of Project A. But Project B, the large diameter pipe, was rehabilitated exclusively with chemical grouting at failing joints. “That’s unusual for this region,” says James Bohn, Walden Associated Technology Inc., the grouting contractor for the project, “Sewer grouting is sometimes considered ‘old school’ because more lining is being done these days. This is the first big grouting job in this area in about 15 years.”
Why the reversion to an ‘old school’ technology? Osborn says it has everything to do with cost-effectiveness; “For large diameter pipes that are structurally sound, grouting is just as viable a solution, and it’s considerably more economical,” he says, “Especially for pipe bigger than 54-inches, the cost of handling and installing large liners gets expensive.”
Gearing up
Where CIPP is used to reline entire sections of pipe, from manhole to manhole, chemical grout is used to repair leaks and gaps where they actually occur, at joints. Since segments of large diameter concrete sewer pipe are only three to 8-feet long, several thousand joints needed to be sealed. This work is done with large, collar-like devices called packers.
Packers are quite versatile. In addition to pumping chemical grout into joint openings, they can also be used to air test joints. The basic work procedure was to lower the packer sections through the manhole and reassemble the packer at the bottom of the manhole. Once assembled, the packer could be moved between joints as needed for the test and seal operations. Each joint was air tested for soundness. Less than 1 percent of Granite City’s sewer joints passed.
For the joints that did not pass air testing, the packer was then used to pump solution grout until the soil could no longer absorb additional grout, known as refusal. After allowing the grout to set (or gel) for an additional 90 seconds, the packer was deflated, reinflated on the joint and used again for air testing to confirm that the joint had been sealed.
But packers do need to be sized to fit the pipe, which was a minor challenge for Walden Associated Technologies. “We had access to all sizes of packers that we needed, except for the 108-inch packer,” explains Walden’s Estimator and Project Manager James Bohn, “We had to have that one custom-fabricated for this project.” The custom, 108-inch packer was built by Logiball Inc. “We’ve already used that packer on several hundred joints,” says Bohn.
It wasn’t just pipe diameters that were big on this project; the sheer scale was also a challenge. To support fieldwork, Walden’s staff designed and customized a 48-foot, temperature-controlled semi-trailer. “We set it up so that we could mix two, 120-gallon batches of grout at a time and keep them warm in the trailer until they were transferred to the grout truck just before pumping,” Bohn explains, “We also used the trailer to store all chemicals and safety equipment. We even had the inspector’s desk in there, with video monitors and hardwired audio communications right at the desk — our crews were never out of touch with surface support.”
With the custom trailer and the right equipment in place, Walden was able to stick to a very productive schedule. Working in two, 12-hour shifts per day, five days per week, Walden crews were able to test, grout and re-test 20 joints per shift on most of the sewers, and 12 to 14 joints per shift when working on 108-inch pipe.
“Most of that time was devoted to moving the packer between joints and doing the pre- and post- air testing,” says Bohn, “Actual grout application goes quickly.”
One accommodation made for the larger diameter pipe was to extend curing times. Whereas small diameter joints can set up in as little as 30 seconds, 90 seconds were allotted for full cure times on the large diameter pipes. “On larger pipes, it’s important to slow down a bit,” says Bohn, “That way, it sets up well, and you get a good grout band around the outside of the joint.”
Pumping out the work
Work began on Jan. 10, 2012, and continued through summer. “Sewer work is a little easier in winter and summer, when the river—and, consequently, the groundwater—is relatively low,” Osborn says, “But chemical grouting could be done in spring as well, and we had no problems sticking to our schedule.”
The solution grout used was AV-100 acrylamide grout from Avanti International. The exact mix was 50 pounds of AV-100 dissolved in 30 gallons of water providing a 20 percent solids mix. This becomes a 10 percent solids mix when an equal volume of ammonium persulfate solution (used as a catalyst) is added. This grout mix was supplemented with two gallons of Avanti AV-257 Icoset per 60-gallon batch — the AV257 is a latex-based product that increases the flexibility of acrylamide grout, and was added for additional protection against groundwater-induced movement in the Granite City sewers.
On average, about 21 gallons of grout were used on each 108-inch joint, depending on how much grout was accepted under high-pressure pumping. The acrylamide grout was pumped through joint leaks, under pressure, so that it completely filled voids in the soil outside the pipe. It then set permanently into a solid but flexible exterior band that seals the leaks, stabilizes the pipe, and permanently fills voids to minimize groundwater flow around the joints. A small grout band was left on the inside of the pipe and could easily be removed.
Quality assurance was provided by continuous onsite inspection, continuous video recording and the air testing which preceded and followed all joint rehabilitation. Osborn says the only real hitch happened during summer months when “the trailer got a little warm!”
One of the biggest dangers of sewer work is the air quality hazards of confined spaces. Walden Associated Technologies has gone to extraordinary lengths to ensure a safe working environment. Each crewmember is certified in confined space rescue and carries an air monitor at all times. Air is also monitored remotely during work. Ten-minute escape tanks and 30-minute breathing apparatuses are attached to custom brackets right on the packers. Audio and visual monitoring from the grout trailer was hardwired and continuous.
Weather was also monitored to guard against sudden storm water rises in pipes. “We actually had a surprise rainstorm come through one day,” says Bohn, “We immediately pulled our crews and the packer and other equipment out. Fortunately, what we found was that it takes an hour or so for the water level to rise significantly, even in a heavy rainstorm — still, there was some intense scrambling and we’re glad we had the policy in place.”
More to do
Project B is completed, with all joints successfully passing air testing. But in the course of work, a surprise was uncovered — about 2,000 lineal feet of 112-inch cast-in-place pipe. This pipe has no circular joints. Instead, it has long seams that run along the pipe sections at 3 and 9 o’clock. “They would pour the bottom half, and let it set,” Bohn explains, “Then frame up the top half, and pour that.”
Like the rest of the system, this pipe is also about 100-years old, with lots of leaks and gaps along the seams. Osborn says it will also be grouted; “We’re looking at our options,” he says, “But it’s in generally good condition, for 100-year old pipe, and we feel grouting will work well.”
A different technique will be used for this sewer pipe. Instead of setting up packers, holes will be drilled along the seams and acrylamide grout will be injected with hand-held injection guns connected by hoses to the grouting trailer. But as with the packing technique, grout will still set up outside the pipe, filling the soil voids that exacerbate sewer leaks.
The Granite City Sewer Lining and Rehabilitation Project combines two types of rehabilitation techniques, CIPP and chemical grouting, as a means to maximize the footage rehabilitated within the available dollars. This approach makes perfect sense and is becoming more frequent; CIPP is fast and cost-effective in smaller pipes, but can become expensive for larger diameter pipe. “We talked to suppliers and found that CIPP would have worked for the larger diameters,” says Osborn, “But sewer grouting was just as effective in this situation, and much more economical at larger sizes. It was fast, we could test it for quality assurance immediately after application, and it will seal the joints effectively for a long time.”
Looking just at the 108-inch pipe, costs for joint testing, sealing labor and materials, taken from the project’s official bid tab, totaled $610 per joint. There were minor changes in the actual final contract price due to changes in field conditions. There was a total of 3,600 lineal feet of 108-inch pipe, which contained 600 joints for a cost of $366,000.
In terms of ‘feet per dollar,’ it’s clear that grout sealing joints when possible comes out ahead of total pipe replacement for the large diameter pipe. This isn’t the whole story of course, because it isn’t really an ‘apples to apples’ comparison; after all, a sewer rehabilitated with CIPP is essentially new pipe from start to end. But Granite City engineers had determined that the pipe itself was structurally sound and that leaking was confined to joints. That being true, there was a compelling case for simply sealing the joints with solution grouting, which salvaged the existing pipe by using grout to stop infiltration and stabilize the 108-inch sewer pipe bedding soil.
Even though some may have considered the grouting solution as old school, Granite City’s engineers could see that it was the right solution in this context. For municipalities around the world, it’s a good lesson in combining technologies for optimum results, and avoiding a ‘one size fits all’ approach to infrastructure rehabilitation.
FOR MORE INFORMATION:
Avanti International, (281) 486 5600 or (800) 877 2570, www.avantigrout.com
Walden Associated Technologies, (800) 495-6036, http://waldntech.com
Logiball, (800) 246-5988, www.logiball.com
Comments