January 2013, Vol. 68, No. 1
Features
Massive Excavation Project Required No Vibrations From Construction
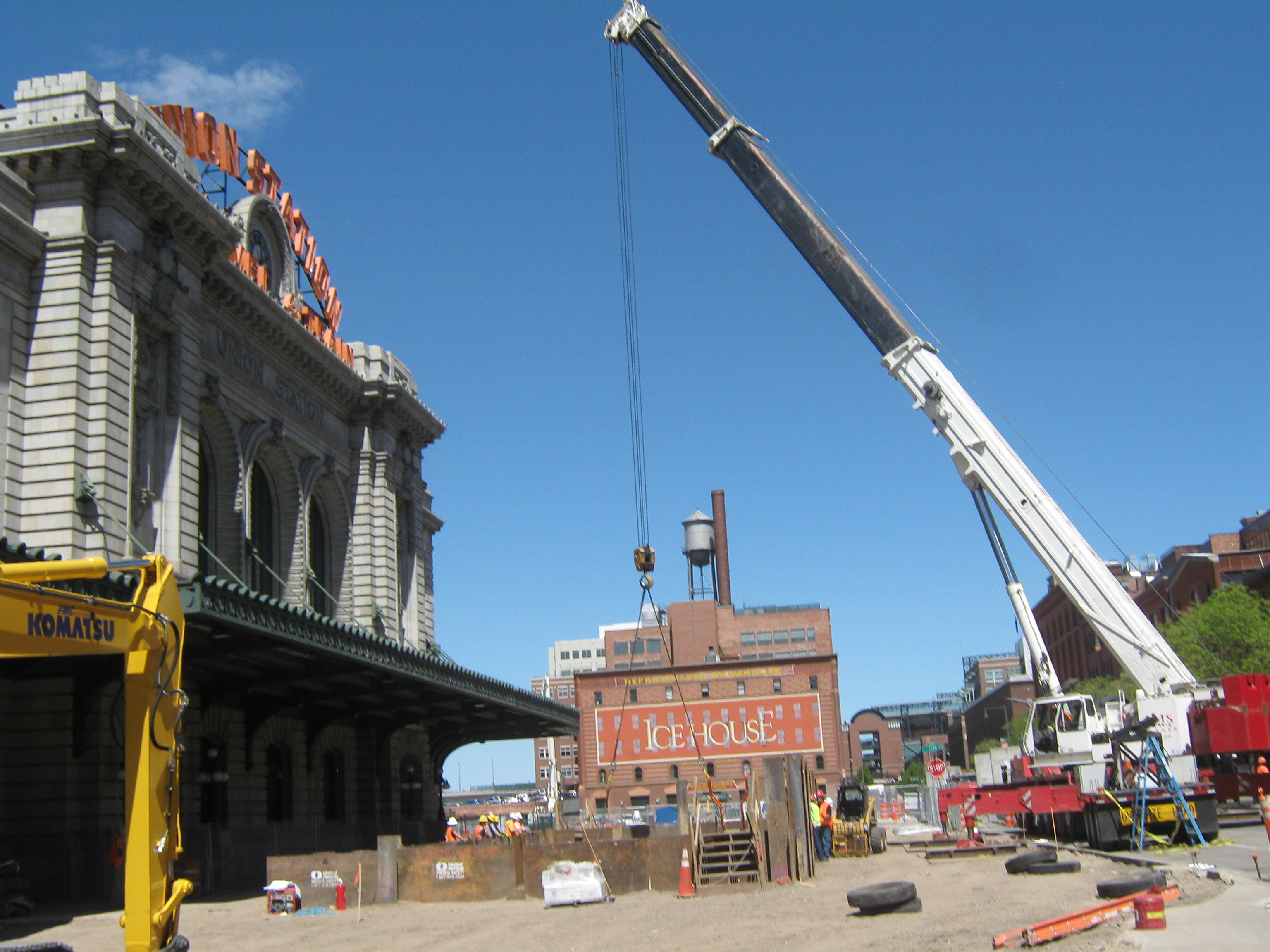
For most residents of Denver, CO, and surrounding areas, the Denver Union Station has been a city landmark for as long as they can remember.
The name Denver Union Station brings to mind the impressive stone structure dating from 1914. However, the first train steamed into Denver in 1870 and for the next few years, railroads built individual depots. In 1881, the first Union Station consolidated rail traffic under one roof.
In 1894, the original structure burned and was quickly rebuilt. Improvements made over the next several years changed the station’s look until the stone landmark of the last nine decades was completed in 1914 (see sidebar).
Today, Denver Union Station is undergoing the largest, most significant changes in its history. When complete in 2014, the new Denver Union Station complex will serve as a multimodal transportation hub, integrating light rail, commuter and intercity rail, as well as regional, express and local bus service, the 16th Street Mall shuttle, Downtown Circulator and intercity buses, taxis, other shuttles, vans, limousines and bicycles.
Project owner is the Denver Union Station Project Authority (DUSPA) which is responsible for the financing, acquiring, owning, equipping, designing, constructing, renovating, operating and maintaining the Denver Union Station redevelopment project.
Subcontractor Iron Woman Construction and Environmental Services, Denver, completed a large excavation in front of the main terminal building and formed and poured a concrete pad 83-feet long, 26-feet wide and two-feet thick, on which to position a precast, sectional, 8-foot-deep vault/tank with an 11,000 gallon capacity to capture rainwater and melting snow from the roof and parking lot of Union Station. Stored water will be released into the storm system in a controlled manner.
United Rentals Trench Safety (URTS) provided shielding and shoring for the excavation, which was installed by Iron Woman crews.
Evaluation
Shielding and shoring options were evaluated carefully during planning and design.
“Because one side of the excavation was only 26 feet from the front of Union Station, a primary requirement of the shoring system was to prevent any soil movement. No vibration was allowed,” said Kris Graham of United Rentals Trench Safety’s (URTS) Denver office.
Graham said sheet pile shoring was ruled out because of the vibration that would be created during the installation and removal. It was estimated that an I-beam system with timber lagging with soil stabilization would require one month to install – too much time to be accommodated by the schedule.
The solution was the installation of a 90-foot long by 33-foot wide by 16-feet-deep beam and plate pit with five sets of 80-ton Mega Brace struts.
Graham said the beam and plate system with the hydraulic Mega Brace struts provided by URTS required the drilling of only half as many caissons for the I-beams, as compared to a timber lagging system.
“This,” he explained, “allowed the shoring system to be installed, the concrete pad formed and poured, 10 precast concrete vault/tank sections installed, shoring components removed and the excavation backfilled, all within one month. And the entire system was recovered afterwards, whereas with a timber lagging solution, everything below five feet would have been left in the ground.”
Appears to be simple enough, but with an excavation this size so near an historic building in a highly-developed urban area, there were numerous challenges that required adjustments to the original design of the shoring (see sidebar).
Work on the excavation and shoring began with surveyors staking out 30 points for drilling holes 31 to 36-feet deep with eight-foot, 6-inch horizontal spacing. A skid-steer loader removed spoil and added a mixture of concrete and fly ash into each caisson. Water was added as drilling continued, turning the mixture into a slurry to stabilize soils in the caissons.
Iron Woman used a crane to set HP14 x 117 pounds, 45-foot long I-beams into the drilled caissons, and a skid-steer backfilled to the engineer-prescribed depth while crew members kept the beams aligned and square.
Careful procedure
United Rentals’ Graham describes the procedure Iron Woman personnel used to dig and shore the excavation.
“A 40-metric-ton-class excavator then dug the entire 90-foot-long, 35-foot wide excavation to a depth of five feet. An in-out ramp was constructed at one end. Twenty-by-eight-foot steel plates were placed between the vertical I-beams and pushed down by the excavator as it dug. Plates were one-inch and 1 1/4 inches thick.”
HP14 by 117 pound I-beams were used as walers, hauled into the excavation and held in place horizontally by the excavator while a welder tacked them to the vertical beams in the caissons. Four, 20-foot long I-beams were cut as braces in the corners and welded to the horizontal waler.
The second stage of the excavation began as I-beams continued to be welded into place, with the Komatsu excavating to a depth of 17 feet. As the depth was finished in one section, the five sets of Mega Brace struts were pressurized with a gasoline-powered pump. United Rentals Trench Safety imported the Mega Brace system from England, where it was originally developed as a time- and space-saving solution for urban excavations in close quarters.
In total, United Rentals Trench Safety provided the steel I-beams, steel plates, hydraulic Mega Brace struts and engineering to build a 90-foot long by 35-foot wide by 16-foot deep beam and plate shoring system with the ability to pressurize, de-pressurize and re-pressurize hydraulic Mega Brace struts to facilitate the installation of precast concrete tank sections.
With the shoring system in place, concrete crews constructed forms for the two-foot thick floor to support the holding tank. The concrete floor was poured and cured. After the required curing time, the forms were stripped and concrete seal applied, and it was time for the precast concrete tank sections to be set.
Ten pre-cast tank sections with a maximum weight of 25.6 tons per section were set in place by a 220-ton crane. As sections were added, the Mega Brace struts were repositioned in five pre-engineered sequences to create space for new tank sections, while at the same time keeping the shoring system safe. The total capacity of the storage tank is 10,940 cubic feet.
With the tank in place, crews sealed joints of the sections and the concrete floor.
Backfill
The excavation then was backfilled to the level of the horizontal walers. Next the Mega Brace was removed using pumps to de-pressurize the struts, which were lifted out with a bridle. The welds from the horizontal walers to vertical I-beams were cut. Finally, the shoring system’s 20 by eight-foot steel plates were lifted out by a Komatsu excavator. After the removal of all the steel shoring I-beam and steel plates, and hydraulic rams, backfilling was completed and access hatches installed.
To make the excavation, install the shoring system, pour the concrete floor, construct the large holding tank, fill the excavation and remove shoring components required an amazingly short period of time.
The system was delivered to the job site in mid-March 2012 and was returned to URTS the third week of April, said Graham.
The only time any maintenance was required was when it was necessary to release hydraulic pressure from the five, 80-ton struts to relocate them during installation of sections of the vault/tank.
I-beams and plates came from United Rentals Trench Safety locations in Denver, Riverside, CA, and Las Vegas, NV. The Mega Brace struts came from the company’s Oklahoma City branch.
Installation of the system was done by Iron Woman personnel. Lone Star Welding, Sedalia, CO, did the certified welding of the I-beam walers. Ludwig Drilling, Inc., Castle Rock, CO, was responsible for the caisson drilling.
URTS’ Graham was on site as installation advisor to confirm that the site specific engineered design by D. H. Charles Engineering was being installed in accordance with the design, and he was on site to be available to contact the engineer as questions or variables arose. The system was inspected daily by an Iron Woman designated “competent person” as required by OSHA.
Graham said the project illustrates the value of renting shielding and shoring for large, unique projects.
“We estimate the cost to purchase the steel beam and plate shoring for this project would have been more than $250,000,” said Graham. “The Mega Brace struts would have cost another $150,000. We were able to provide a rented solution at a savings of more than 85% below the purchase cost.
“If a Mega Brace system had been purchased for this project, six-to-nine months lead time would have been required by the English manufacturer. URTS was able to provide necessary shoring components from inventory with eight truckloads from our Denver facility and another eight truckloads from other locations.”
United Rentals is the largest equipment rental company in the world, with an integrated network of more than 800 rental locations in 48 states and 10 Canadian provinces. More than 10,000 employees serve construction and industrial customers, utilities, municipalities, homeowners and others. The company offers for rent approximately 3,000 classes of equipment with a total original cost of over $7 billion.
In addition to shielding and shoring equipment, United Rentals Trench Safety branches also carry confined space ventilators, air monitor detectors, and other shoring equipment, and offer 24-hour emergency response and professional safety training.
Iron Woman Construction and Environmental Services is a Native American-owned, multi-disciplinary, heavy haul trucking and underground utilities company. Iron Woman employs a team of highly-qualified professionals with extensive experience in transportation, environmental remediation, and utilities.
FOR MORE INFO:
United Rentals, (203) 622-3131, www.unitedrentals.com
Iron Woman Construction and Environmental Services, (866) 792-0144, http://ironwomancon.com
Denver Union Station: A Glorious History
Railroads played a key role in the settlement of the Western United States, and Denver Union Station has been the central terminal for rail traffic since the first station was built on the present site in 1881.
As the population of Colorado and other western states increased, rail traffic through Denver kept pace. After the original Union Station was destroyed by fire, it was immediately replaced by a new building. As did the first, the second facility had a clock tower. That building subsequently was demolished and the central portion rebuilt with a lower profile – the Beaux-Arts landmark that remains today was completed in 1914.
The 1920s and 30s were the glory days of Denver Union Station, a time when as many as 80 trains a day passed through the station. In the 1940s, many of those trains carried soldiers fighting in World War II. Even though rail passenger service was declining, Denver Union Station accommodated more passengers than Stapleton Airport until 1958.
Then came a period when the elegant station was a quiet ghost of what it had been. Its great waiting room was often empty, accommodating only passengers for two Amtrak trains that passed through on a regular basis.
However, that time is past, as the Denver Union Station project passes its halfway point with the historic station the keystone of a modern transportation hub emerging that combines multiple modes of transportation.
A Challenging Project
The Denver Union Station project has involved numerous challenges, one being the construction of an 11,000-gallon capacity underground vault to capture and store rainwater in close proximity to the historic Union Station Building.
The first steps of digging the large excavation for the vault required shoring not only to protect the workers, but to prevent soil from shifting and damaging the 98-year-old building.
Kris Graham of United Rentals Trench Safety (URTS), provider of the shoring components, explains that the challenges began early in planning.
“An early issue was finding as-built plans of the Union Station Building,” says Graham. “D.H. Charles, design engineer for the beam and plate shoring system, needed to know if Union Station had a basement or whether the walls were built on a concrete footer and of what depth.
“After several weeks of searching, the needed as-built plans could not be found, so subcontractor Iron Woman hired a vacuum truck to do pot holing around the foundation. We found that Union Station had both basements and foundations on footers, depending on the section of the building and when it had been built. This information gave the engineers something to work with.
“The original design had our shoring pit approximately 20-feet from the front of Union Station. However, the cast iron awning that extended from the building did not give the caisson driller, excavator and the cranes enough room to work. The design pushed the pit out six feet, providing the minimum amount of clearance for the construction equipment.”
As work continued, a decision was made to change the size of the crane used for setting sections of the concrete in place for the storage tank.
“The original plan called for a crane smaller than the one used for excavation — that would require repositioning several times during the setting of the concrete tank sections. At the last minute, a larger crane was substituted so that all the concrete tank sections could be set without needing to reposition the crane.”
The shoring design had calculated weight and sizes based on the smaller crane. D.H. Charles Engineering redid the calculations based on the size, weight and footprint of the outriggers, and needed to move the crane 18-feet away from the shored pit, where it would still be able to handle all the picks.
“United Rentals brought-in four, 1-inch thick, 8-by 20-foot steel road plates to place under the crane’s outriggers and distribute the weight over a larger area. The engineer developed a design that kept the adjacent street open and allowed the larger crane to be set up just once. This was all resolved in record time while the equipment, crews and precast concrete delivery trucks were at the job site.”
Comments