January 2013, Vol. 68, No. 1
Features
Keeping The Sewer Running In Saskatoon
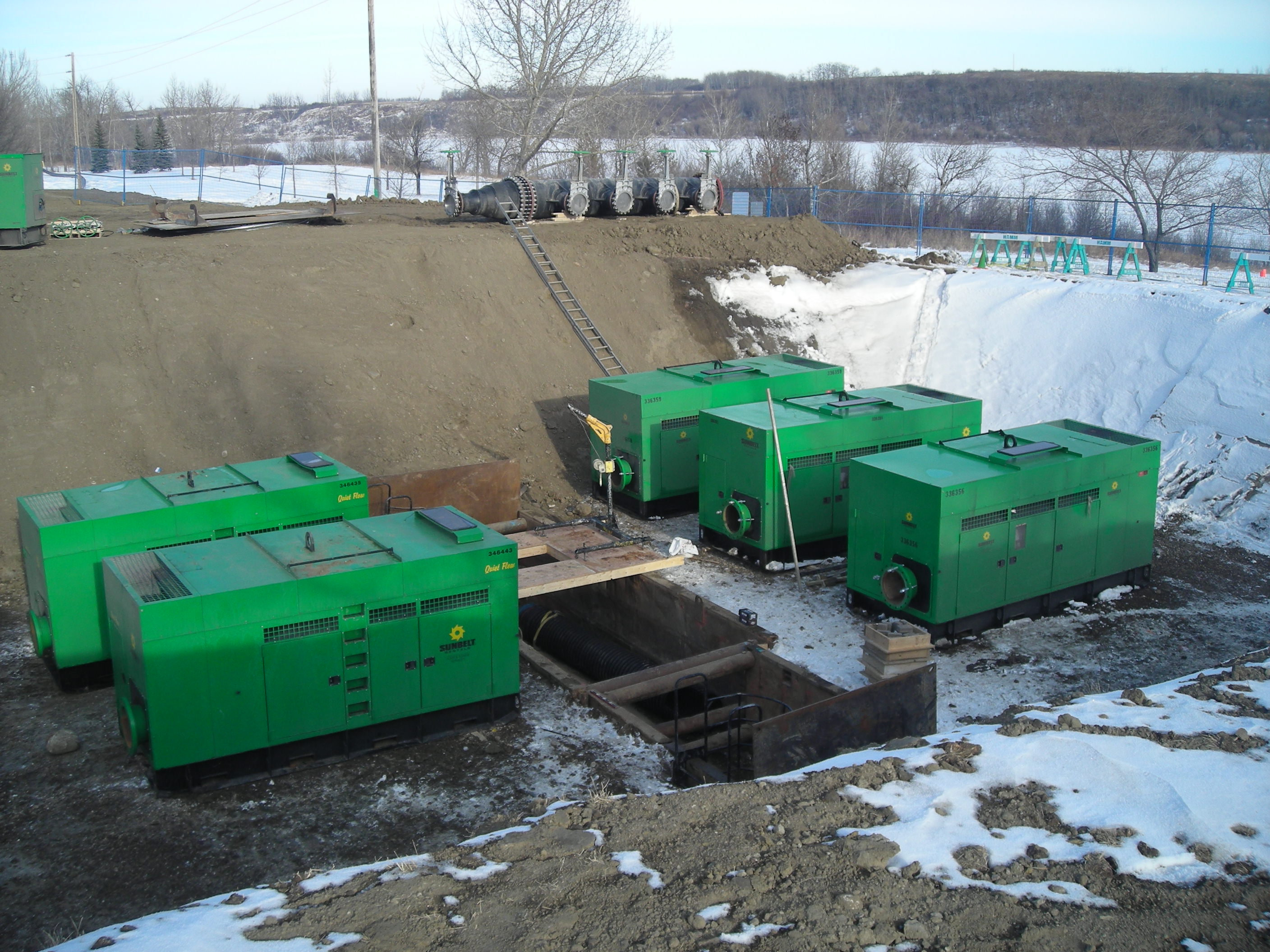
The purpose of every pipe bypass project is to construct a temporary pipeline around a section of pipe that is being repaired or replaced; however, no two bypasses are exactly alike — each is different and has its own special challenges.
Sunbelt Rentals is a national turnkey provider of pumps and equipment for large water and sewer line bypass projects. A project during the past winter was far removed from the nearest Sunbelt location in Denver, CO.
In Saskatoon in the Canadian province of Saskatchewan, Sunbelt’s task was to install and operate a temporary bypass for a 1,010-foot-long segment of 84-inch diameter sewer interceptor while it was rehabilitated with cured-in-place-pipe (CIPP) liner. The bypass was put in place in January and February 2012 and bypass components were removed in April after lining was completed and flow returned to the interceptor, the largest sewer interceptor in the city.
Project owner was the city of Saskatoon. Sunbelt assisted prime contractor Insituform in the construction of the sewer bypass by supplying a setup superintendent and personnel to operate and maintain the bypass.
“The geographic location and harsh winter climate brought many challenges,” said Ladd Gould, Sunbelt national strategic account manager.
Careful planning was the key to avoiding problems, Gould said. “Pipes and pumps would have to be kept from freezing,” he said. “Subzero temperatures became the biggest concern during advanced planning. Every detail had to be planned and scrutinized to mitigate any chance of failure.”
Getting equipment into Canada also required careful planning.
“Before submitting a bid, Sunbelt hired a consultant to account for the foreign tax implications guaranteeing the bypass bid cost for our client, Insituform, would be covered,” Gould continued. “To calculate import and local taxes, each piece of bypass equipment was categorized. Each and every loose nut and bolt was taken into account, making this a lengthy process. While this was under way, Sunbelt personnel who would be working on the project were interviewed by an immigration attorney to avoid any entry issues into Canada.”
Record cold
Two weeks prior to Sunbelt’s arrival in Saskatoon, the temperature dropped to a record low -36 degrees F. However, careful planning ensured Sunbelt personnel were ready for the extreme cold.
“Significant research went into the winterizing of the 10- and 18-inch Quiet Flow pumps that were slated for the project,” Gould explained. “First Sunbelt identified the key components of the pumps that would require heat to reduce the possibility of freezing — the priming tank, check valve and volute, the casing that receives the fluid being pumped by the impeller.”
Next, heating options were considered.
“Sunbelt’s first choice was custom heat blankets,” he said, “but the manufacturer could not deliver within the required timeframe. As a backup choice, which turned into a significantly more cost effective alternative, we utilized electric heat tape strategically placed in those critical areas. The heat tapes were AC powered so a generator and power distribution was factored into the bid.”
Crew members had necessary protective equipment and cold-weather gear.
Site preparation began in December 2011, with Insituform’s earthwork subcontractor, Hamm Construction Ltd., beginning construction of the suction pit and other site work to accommodate the CIPP liner installation. Hamm constructed the excavation and cut five suction access ports into the top of the 84-inch sewer to greatly reduce the bypass static suction lift. Hamm also cored the discharge points into the influent channel at the treatment plant for the three 18-inch bypass discharge lines.
Equipment put in place included six 18-inch Quiet Flow pumps. “Three of the 18-inch pumps were required to maintain the 36.5 million gallons per day (mgd) specified by the city of Saskatoon,” said Gould. “Two additional pumps were tied in as backup providing 66 percent of bypass redundancy. Because of the remoteness of the project, an additional 18-inch pump was placed just out of the bypass system in the event of a total catastrophic pump failure.”
The five pumps were tied into a large, 40-foot-long manifold containing five,18-inch ports with knife gate valves for the bypass pumps, and three 18-inch ports with valves for the three 1,500-foot, 18-inch HDPE discharge lines. Bypass flow was discharged into the headworks of the Saskatoon Waste Water Treatment Plant.
Clear route
Routes of bypass lines often complicate their construction and operation, but the Saskatoon project location gave personnel a break.
“For bypass pumping, this project had exceptional site access,” Gould said. “The majority of the project was located in a large park adjacent to the South Saskatchewan River, providing full access to the suction location and discharge path. Where the discharge terminated at the treatment plant, the work area could be easily accessed by driving through the treatment plant grounds.”
Fortunately while constructing the bypass, the weather ‘warmed.’ “We never saw temperatures drop below -22,” said Gould.
Still very cold, but all pumps and the manifold were enclosed in a temporary structure made of insulated fabric with heat pumped into the enclosure.
“It worked so well,” Gould said, “technicians performing pump watch were able to work in t-shirts.”
One of the technical challenges of this bypass design was the depth of the 84-inch sewer at the bypass system’s suction point.
Gould said that it was determined that in order for the bypass pumps to achieve the required design flow, the sewer level would be required to surcharge approximately 10-feet above the sewer line because the ground elevation was almost 18-feet above the pipe.
“This was the most efficient static suction lift level corresponding to the required net positive suction head for the selected bypass pumps,” he explained.
Hamm Construction dug the 13-foot-deep, 72- by 49-foot excavation and cut the five suction ports in the top of the 84-inch sewer.
Operations
Gould said that before the plug was installed to divert the sewer line’s flow to the bypass, all pumping equipment was checked and rechecked.
“Once the bypass was in operation,” said Gould, “it could not be shut down because of the risk the three discharge lines would freeze. The bypass system was air tested instead of hydraulically tested to avoid freezing the unprotected HDPE discharge lines. After successfully passing the air test, a pneumatic sewer plug was installed after the plant’s influent lift station reduced the 84-inch line surcharge.”
Operating the bypass began with Sunbelt performing round the clock pump watch with one technician onsite in three, 8-hour shifts.
“However,” said Gould, “this was short lived because it was discovered that the pumps were being clogged with an abnormal amount of debris, causing them to be cleaned constantly. In response, Sunbelt sent another technician to assist in the round-the-clock debris removal. The pump watch was then adjusted to two techs onsite in twelve hour shifts.”
After completion of the CIPP rehabilitation, the bypass plug was pulled after 26 days of continuous operation and flow restored to the 84-inch line.
“Despite all the challenges, the teamwork among the city, Insituform and Sunbelt resulted in the successfully executed construction and operation of one of the largest sewer bypasses in Western Canada,” Gould concluded.
FOR MORE INFO:
Sunbelt Rentals, (800) 667-9328, www.sunbeltrentals.com
Insituform, (800) 234-2992, www.insituform.com
Hamm Construction Ltd., (306) 931-6626, www.hammconstruction.ca
Comments