January 2013, Vol. 68, No. 1
Features
Ice Pigging: New Water, Sewer Pigging Method Offers Unique Benefits
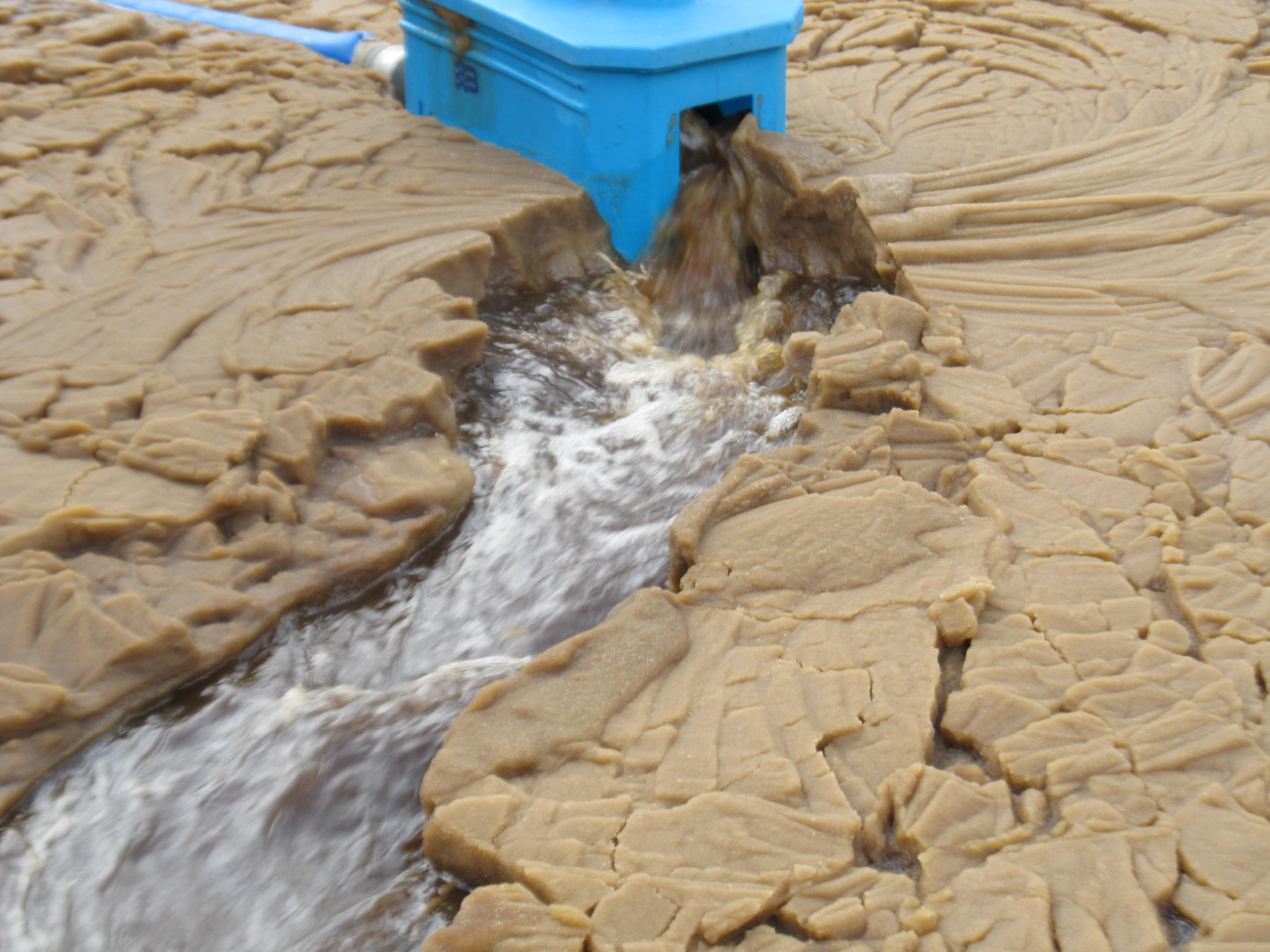
A new breed of pipeline “pig” has arrived in the United States.
“Pigging” to clean pipelines is an accepted procedure used by utility pipeline owners. The process is relatively simple: a device (pig) is inserted into a pipe where pressure forces it through the pipe, scraping the inside sidewalls and carrying debris to an exit point out of the pipe. A variety of pig designs are available.
A new type of pigging became available in the U.S. and Canada early in 2012 when Utility Service Co., Atlanta, GA, became the exclusive license holder for ice pigging for water and wastewater applications in the U.S. and Canada.
The ice pigging process pumps ice slurry — the pig — into a pipe, filling it to 10 to 20 percent of its volume capacity. System pressure carries the ice downstream to an exit point.
“The ice works much like a glacier,” said Kirt Ervin, P.E., Utility Service’s vice president of water quality. “It does not bulldoze the sediment; rather it picks up the sediments within the slurry and carries them out of the main, greatly reducing the amount of water used in the process. Cleaning by ice pigging is comparable to swabbing, and it provides up to 1,000 times more cleaning effectiveness than using water alone.”
Ice pigging can be used to clean pipe in diameters from 1/4 to 24-inches.
Utility Service Co. provides ice pigging services directly to water and wastewater utility system operators, but also will work with engineers and general contractors where appropriate or as part of a larger project, said Ervin. The company does not provide pipe rehabilitation or installation services.
Education challenges
Clearly the need for large quantities of ice sets this type of pigging apart from other pipe cleaning technologies, and educating potential customers is a primary activity of the company.
“The utilization of ice pigging in water distribution lines has been slow to expand because the equipment necessary to generate and deliver the quantities of ice at the quality needed for successful operations is all custom made,” Ervin said. “The equipment is not currently available on the open market in the U.S. We are working with several U.S. manufacturers to determine whether we can use their equipment with the ice pigging technology.”
[inline:=A series of sample bottles collecting the waste. The samples are collected from left to right during the operation showing the clean water before the pig, the waste removed by the pig, and the clean water after the pig has been removed from the water main.]
Utility Service Co. has two ice pigging rigs in the U.S. and has performed demonstration projects in seven states — most along the east coast — and completed full scale projects in New Hampshire and North Carolina.
Ice pigging technology requires an ice-making facility, storage tank, flow analysis unit and delivery pump, Ervin continued. The ice is generated on-site using local potable water and a freezing point depressant, typically National Sanitation Foundation International (NSF) certified table salt. Other freezing point depressants are available depending upon the situation. Ice-making equipment must be mobile, but large enough to generate more than 10 tons of ice.
Ice pigging usually is performed with a two-person crew. The only support needed is for traffic control, personnel to operate valves to isolate the main and a tanker truck, if the waste cannot be sent to the sanitary sewer.
Comparing ice pigging to other pipe-cleaning procedures, Ervin said unidirectional flushing typically uses between four to seven pipe volumes of water, swabbing often even more.
“Ice pigging usually uses less than two pipe volumes during the process,” he said. “Because the ice pig is a slurry and not a solid pig, it virtually cannot get stuck. If the pig would get stuck, we allow the ice to melt and flush from the system. This prevents the utility service provider from having to take the main out of service to extract a lost or stuck pig.
“Ice pigs can negotiate bends, changes in diameters, broken gate valves and in-line butterfly valves while still providing an effective cleaning effort. Therefore, this technology would be very advantageous for highly-sensitive areas or critical pipes that may be located under railroad crossings, river crossings or high traffic downtown areas where the risk of getting a pig stuck would be extremely costly or dangerous to operations.”
Also, he added, ice pigging could provide water systems the first opportunity to clean service lines. “There isn’t any good technology that exists for water systems to clean the service line from the water main to the meter,” he explained. “This technology will travel from the water main through the service line without issue.”
The greatest benefits of ice pigging relate to operations, Ervin continued.
Ice pigging technology can enter and exit from any two-inch or larger connection to the main, he explained. Typically live hydrants without modifications are used, but access can be made through air valve connections and even smaller corporation cocks. No excavation or special launching or extraction stations are required.
Water main ice pigging
Ervin describes the steps in cleaning a segment of potable water main with ice pigging:
“First we stage the delivery tank at the entrance hydrant and then put the flow analysis unit at the exit hydrant to monitor flow, pressure, conductivity, temperature and turbidity.
“For a potable water main, the hoses and connections are disinfected and connected to the water main. The flow analysis unit (FAU) is connected to a dechlorination unit to flush water displaced during the process. While the operator at the FAU monitors the water main, system operator personnel would perform a shutdown of the water main.
“The FAU operator is in communication with the delivery unit operator, and confirms when the main is isolated. Before the water pressure in the main drops below 20 psi the ice delivery pump is started to deliver ice to the main. Both operators would communicate to control the ice injection rate and pressures in the main.
“A prescribed amount of ice would be delivered to the main. The delivery unit and FAU then close the hydrants, and the upstream mainline valve is opened. This step would provide some additional ‘packing’ to make the ice slurry a little more solid. The FAU operator then opens the exit hydrant allowing the system pressure to push the ice pig to the exit station while dechlorinating the displaced water. He controls the flow and pressure in the main.
“When the ice pig arrives at the exit, the conductivity will spike due to the salt. At this point, the operator reroutes the waste stream to the sanitary sewer or waste tanker to dispose of the water, sediments and biofilms removed from the main.
“Once the turbidity, conductivity and temperature have started to return to normal, the operator diverts the water back through the dechlorination unit to allow more flushing until all the readings return to normal or better than normal. At this point, all closed valves are reopened and the process is complete.
“A typical project will take less than three hours from mobilization to demobilization.”
Sewer force main ice pigging
The process for cleaning a force sewer main is similar. The pump supplying the force main is shut down and depending on the temperature; the main is flushed with water to cool the pipe. This flushing can be completed simply by running the pump and wet well.
The pipe is accessed on the pressure side of the pump through an air valve or other opening, ice is injected into the pipe and the supply pump activated to push the ice through the pipe to the end of the main.
The ice slurry continues through the system to the wastewater treatment plant.
History
Ervin said ice pigging was invented by Prof. Joe Quarini of the University of Bristol in the United Kingdom, and patented in the U.S. in 2005. The technology has been used in Holland, United Kingdom, Germany, France, Japan, Spain, Australia, Chile and Saudi Arabia. To date, approximately 175 miles of pipe have been cleaned. The longest single run has been 2.67 miles of a PVC pipe in Wales.
Relatively new to North America, details about ice pigging technology are not widely known in the U.S. and Canada.
“Water operators are very familiar with flushing operations,” said Ervin. “Some operators also realize that flushing is not solving their problems and that a more aggressive solution is required. However, operators are not very familiar with ice pigging as a solution. We are making great strides to educate these operators and have presented numerous presentations, demonstrations, papers at organizations such as AWWA, NRWA and at the 2013 UCT show.”
Ervin describes response to the company’s presentations as “extremely positive” from water systems people and an even larger response from the wastewater industry where options for cleaning force mains are limited.
Summarizing the benefits of the technology and its application, Ervin said ice pigging is a more sustainable technology than other cleaning methods because it uses significantly less water during the operation. The waste can be easily collected and disposed of eliminating contamination of nearby streams or ponds, and the waste stream can be easily identified and quantified.
“From a social and economic standpoint, there is no risk of excavation that would damage landscaping or create expense to the water system,” he added. “Due to the short project duration, there is no need for temporary service lines and that added cost.”
The future for ice pigging in North America is great, he said.
“We are prepared to work with stakeholders on projects where ice pigging is a good fit,” said Ervin. “We are endeavoring to establish relationships with general contractors in the pipe cleaning industry, consulting engineers who may design these projects and directly with end-users. We have the capabilities to design and engineer these projects with professional engineers licensed in over 35 states. Recently joining our staff is Ice Pigging Project Manager Paul Treloar, who came from the U.K. and Aqualogy, the worldwide license holder for ice pigging. Paul has completed ice pigging services across the globe for the past 2½ years.”
Utility Service Company is a subsidiary of Suez Environment North America. Established in 1963, Utility Service is best known as a major provider of full service potable water tank asset management programs offering a full range of distribution system maintenance and management programs in most of the contiguous 48 U.S. states.
FOR MORE INFORMATION:
Utility Service Company, (800) 223-3695, http://utilityservice.com/
[inline:=This picture from Stokes County, NC, shows pre and post pig – a section of pig cut out before and after the operation showing the effectiveness of the pig to remove the film on the pipe. The customer had flushed the area prior to the pigging which could not remove the film.]
North Carolina Project
To address problems with odor and taste in Stokes County, NC, drinking water, Utility Service Co. employed ice pigging to clean approximately 17,500 linear feet of six-inch diameter PVC water main, said Kirt Ervin, P.E., Utility Service vice president of water quality.
“The county Water & Sewer Authority obtained quotes for both swabbing and ice pigging,” said Ervin. “Costs were nearly identical for each technology. Ice pigging was selected based on shorter project duration, limited involvement required of county personnel, less water demand and lower operational risks.”
The project was split into two runs. Work began just before Labor Day 2012. The first run of 9,500 feet was completed in about three hours. The second of 8,000 feet was completed in about 2½-hours two days later, the Friday before the long holiday weekend.
“Normally, a water main cleaning project wouldn’t be scheduled prior to a Labor Day weekend due to the possibility of losing water service for an extended period of time,” said Ervin. ”However, the county believed the risks of a disruption were extremely low, and no disruptions to water service were experienced.”
County personnel cut out samples of the PVC before and again after the clean process.
“Inspecting the pipe samples showed that heavy, black manganese residue on the pipe walls was completely removed,” said Ervin. “As a result of the cleaning, customer complaints have been eliminated.”
Comments