February 2013, Vol. 68 No. 2
Features
Emergency Pipe Bursting Project In Alaska Uses Chain-Drive System
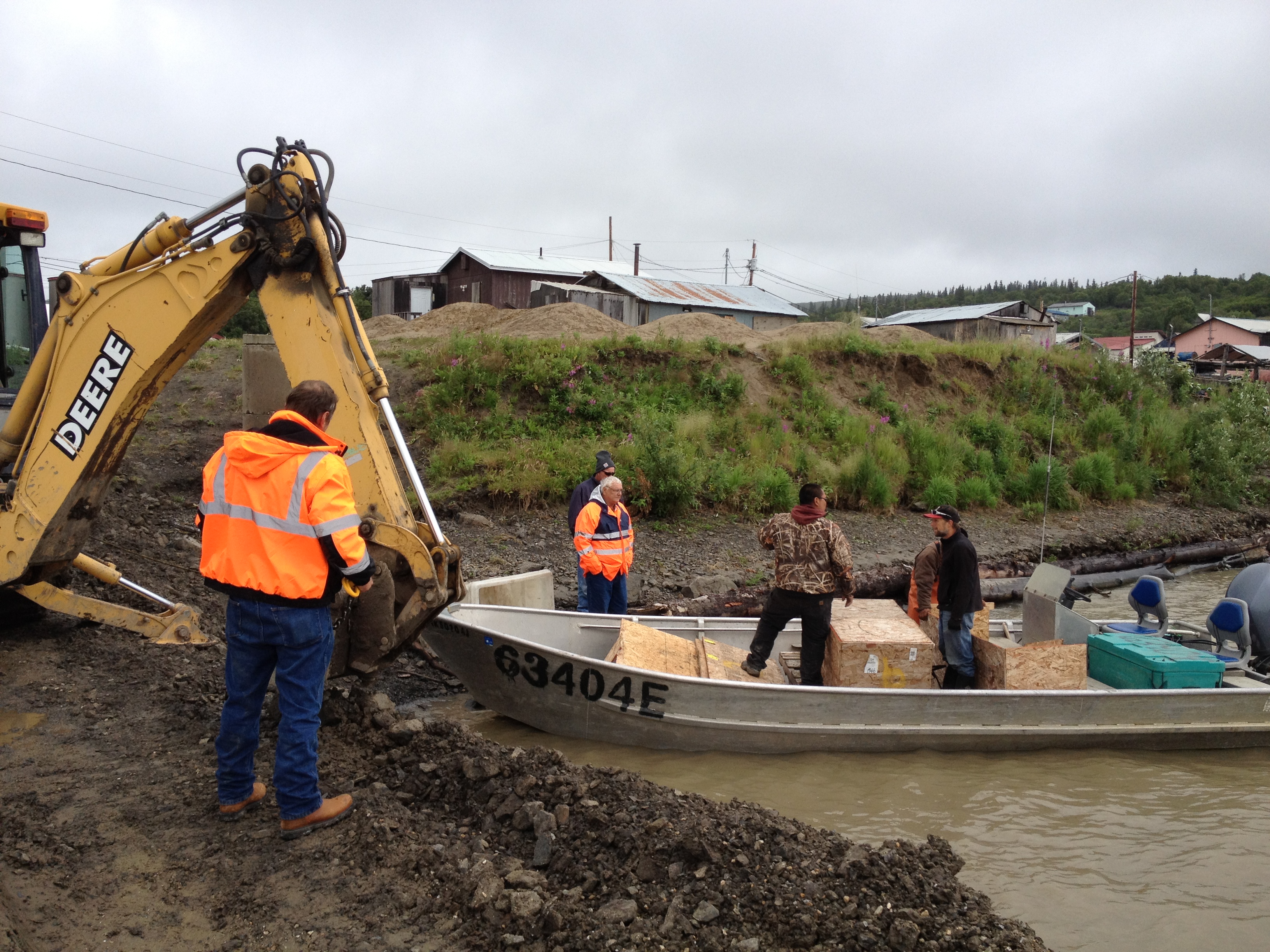
Those in the lower 48 U.S. states know that winters in Alaska are very cold and that everyday life for the hardy souls who live there is different in many ways.
Constructing and maintaining utilities there also has special challenges. Many cities and towns are very remote and extreme cold limits construction through much of the year.
The Yukon-Kuskokwim Health Corporation (YKHC) Office of Environmental Health and Engineering has a Remote Maintenance Worker Program that provides training and technical assistance to community water systems in the Yukon-Kuskokwim Delta.
In this service area, the towns of Bethel, St. Mary’s and Pilot Station in Southwestern Alaska, are off the state’s road system and the only way to reach them in summer is by air. St. Mary’s and Pilot Station are on the Yukon River, making them also accessible by boat.
Pilot Station’s water system is owned by the town, and water for homes and businesses is provided through a buried four-inch chlorinated polyvinyl chloride (CPVC) water main inside a larger insulated pipe with water circulated through a loop to prevent freezing. The loop was installed more than 30 years ago.
In January 2012, approximately 1,000 feet of the return loop froze and cracked, clearly an emergency. The pipe was buried at depths ranging from five to 6 feet.
Pilot Point water plant operators immediately contacted YKHC’s lead remote maintenance worker, Alan Paukan, for assistance. The decision was made to cap the return loop and have customers on the last service lines on the supply side run their water so as to keep water moving through the main to prevent freezing while plans were initiated to repair the cracked segment of main.
Brian Lefferts, director of YKHC’s Office of Environmental Health and Engineering, contacted Utility Construction Management Company, (UCMC), Bellevue, WA, to discuss options for replacing the pipe. UCMC, distributor of TTS chain drive pipe bursting equipment, provides subcontractor, consultant and management services for pipe bursting projects.
Bursting decision
Open-cut construction was considered and ruled out because of the logistics of getting equipment and materials to the remote location. It was estimated that the cost to install the pipe by excavation would be $250 per foot or $250,000.
There was interest in pipe bursting, but the broken pipe was enclosed inside a 12-inch diameter corrugated metal (CMP) pipe with the void between the water pipe and inside of the larger pipe filled with poly foam to protect the water line from freezing.
“To our knowledge, bursting a pipe within a pipe surrounded by foam had never been done,” said Jerry Currey, UCMC president. “Testing was conducted to determine whether pipe bursting would be successful. We obtained a 20-foot section of arctic pipe and set up a test burst at our storage yard. The test was successful, and the decision was made to proceed.”
The old CPVC pipe would be replaced by HDPE pipe pulled behind a bursting tool that would crack and break the old pipe.
YKHC made arrangements to purchase the pipe bursting equipment and materials that would be needed to replace the failed pipe, and planning proceeded to do the work when warm weather arrived. Lefferts said the investment in equipment ensures that it will be immediately available for future use.
Equipment used on the project was a TTS 40, a 40-ton system which included a TTS hydraulic power unit which was driven by a 30-horsepower gasoline engine, 360-linear feet of 3/4-inch anchor chain and links; and four- and 6-inch bursting heads. Currey explained that chain drive bursting equipment uses a hydraulic puller and chain to draw the bursting head and new pipe through old pipe being replaced, rather than rods employed by conventional pipe bursting equipment.
Currey said TTS chain drive bursting equipment with an hydraulic puller eliminates rods, constant make-up and break-out of threaded rod connections and bulky, expensive, low-powered winches.
Complex delivery
“All equipment for this project had to be flown in,” said Currey. “The pipe was flown from Anchorage to Bethel to Pilot Station. All other materials were flown from Anchorage to St. Mary’s and then brought upriver to Pilot Station on skiffs. Larger planes can land in Bethel and St. Mary’s, making this the most cost effective method of transportation.”
The plan called for the 1,000-foot run of pipe to be installed in three separate pulls requiring four pits three-feet wide, 10-feet long, and four to five-feet deep. Pits were dug by a John Deere 310 rubber-tire backhoe. The second pit served as the exit pit for the first pull and starting pit for the second.
YKHC crew members fused lengths of the HDPE pipe while the launch pit was dug and bursting equipment moved into place and set up.
The first 330-foot pull had gone approximately 250 feet when the head pulled off the pipe, said Currey.
“The location of the broken head was determined by measuring the distance from the exit hole to the new pipe,” Currey explained. “We then dug down approximately four feet and reattached the puller head. We determined that the problem was caused by drag from the insulation foam which required a longer tail section where the pipe bolts to the bursting head.”
The pull was completed, and the problem did not occur during the remaining two segments. The three segments were completed over a period of three consecutive days. The installation was made with Currey and two UCMC team members, four YKHC employees and four employees of the city of Pilot Station. The project served as training for the personnel who would be operating the equipment on future jobs.
By the second pull, Currey said the YKHC and Pilot Station personnel were capable of setting up and operating the equipment.
With most pipe bursting installations, pieces of the old pipe are displaced into surrounding soils as old pipe is broken and the new pipe is pulled into place. Currey said there was space in the foam-filled outer pipe to accommodate fragments of the old PVC, but they came into the pits the last approximately 20 feet of the bursts because there was less resistance. He added that if the old water pipe and its replacement had been of a larger diameter, that could have been an issue.
“With chain drive bursting, work proceeds continuously,” Currey said. “There are no interruptions to make-up and break-out rod connections and no need to handle rods one by one. Continuous chain can be installed between machine and insertion pits at up to 600-feet per hour, more than twice as fast as when using rods. On pull back, when pipe bursting, chain drive operates faster than rod systems, to more than 300 feet per hour, also much faster than compressor powered systems.
“Chain drive combines chain strength with the power to handle the biggest jobs with ease, and the smallest with economy through simplicity of equipment and operation,” concluded Currey. “And with chain drive systems, bursts can be made through curved sections of pipe.”
FOR MORE INFO:
UCMC, (425) 641-2926, http://pipeburstingnw.com/
John Deere, (309) 748-0114, www.johndeere.com
Comments