August 2013, Vol. 68 No. 8
Features
Who Should Perform Your Compact Machine Maintenance: You or Your Dealer?
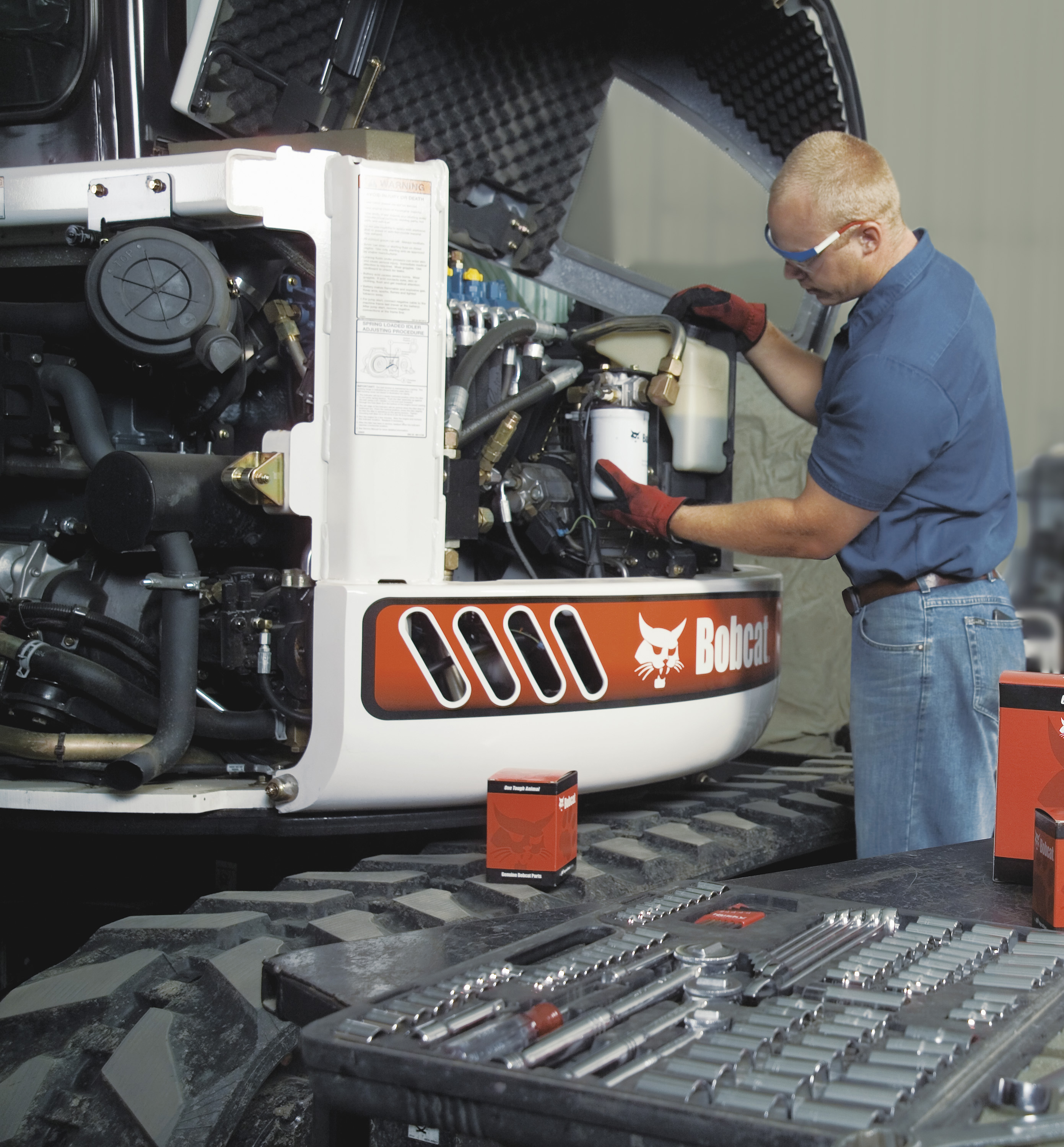
The pace of business is picking up with the summer construction season. Combined with an improving economy, you may already be stretched thin to stay ahead of the curve with routine maintenance. Plus, any new compact machines you’ve purchased in the past three years typically have more sophisticated service needs than their predecessors.
These are factors that directly impact your uptime when business is good. That’s why it’s important to re-evaluate who can most cost-effectively maintain your compact excavators and loaders — you or your dealer? Perhaps your business is large enough to justify dedicated technicians, up-to-date tools and ample shop space. If you’re a smaller operation, you may be tasked with doing most of your own work after hours out of a shop trailer with hand tools.
For example, machines in use four hours a day or more will typically need a 250-hour service interval every three months, or four times annually. “You need to analyze and decide whether the manufacturer’s recommended maintenance intervals can be accomplished efficiently at your location, or if the work should be done by trained dealership technicians who have the time, tools and know-how,” says Mike Fitzgerald, loader product specialist with Bobcat Company.
Fitzgerald and other industry experts say it’s important to weigh your productivity against factors such as your company’s capabilities, your dealership’s capabilities and your opportunity costs. Evaluating these core competencies can help you make the right decision about the type of maintenance that you can manage versus what you might need a dealership’s assistance to complete.
Assess capabilities, efficiencies
One of your first tasks is to review a machine’s operator and service manuals and then evaluate your company’s technical skill sets and efficiencies. Fitzgerald says fewer companies are doing more than daily maintenance and visual checks if they don’t have a staff technician.
The other aspect to consider is the ability to match technical aptitude to the age of the fleet, says Tom Sams, service director for Bobcat Enterprises, an Ohio-based equipment dealership. There’s more to servicing today’s machines than changing filters and fluids. “It makes a difference whether a knowledge base is needed to maintain an older-generation machine or a new machine with more complex procedures for advanced electronic systems, diagnostic packages and EPA-compliant emissions controls that require specialized — and sometimes proprietary — electronic testing equipment,” Sams says.
Future equipment owners and mechanics could be at an even greater disadvantage going forward. Sams points out that while young people are entering the work force with enhanced digital proficiencies, they often lack hands-on mechanical skills. “High school graduates are not as technical as they were 25 or 30 years ago,” says Sams, suggesting that companies will have more responsibility for technical training. On the other hand, with affiliate programs and community vocational programs, dealer technicians have dedicated learning resources to meet manufacturers’ technical requirements and increasing environmental standards.
Adds Fitzgerald, “You may have the time, facilities and skill set to do a certain type of maintenance, but not another. Analyze your company’s capabilities and ask yourself if you can manage the maintenance intervals adequately — or does it require a trained specialist?”
One of the biggest advantages to utilizing dealership service is having trained technicians with access to the latest information resources and tools. “Dealership technicians know what to inspect. We understand the machines’ electronics and their iT4 and Tier 4 systems, and we can do calibrations and check diagnostics with tools and software not available to customers,” Sams says.
Equipment dealerships can provide a variety of planned maintenance contracts on purchased or leased machines. Some dealerships have hundreds of machines under contract with participation that ranges from performing warranty work, to providing monthly, quarterly, annual or even biennial services. Additionally, GPS devices can be installed to continuously monitor machine activity and location.
A growing option that more dealerships are implementing is mobile field service. Some dealerships stock service trucks with key parts and components to conduct on-site routine maintenance and repairs. Sams states, “We can replace high wear items like bucket cutting edges and teeth and carry along a couple of thousand part numbers on the trucks. In our area, we do more mobile service than shop work.”
Sams cautions those who only seek service from general automotive shops to offset higher dealership labor rates or parts costs. “There’s an idea that the guy down the street who works on their trucks can work on their compact equipment and charge $50 to $75 an hour for a service versus $90 to $125. Yes, their rates may be lower, but they may take two days to complete the service. They can’t do warranty work and often don’t have the service manuals or necessary tools,” he emphasized.
Evaluate opportunity costs
An overlooked element of consideration in the maintenance decision is an opportunity cost calculation. This involves an analysis of savings gained from performing your own maintenance with the revenue that can be generated from being on the job longer. Fitzgerald says opportunity costs can vary based on rates and accurate time estimates.
“If it takes you four hours to change oil and you’re making $150 an hour in your operation, that’s $600 of lost opportunity costs. The same work may take two hours at the dealership at $100 per hour,” Fitzgerald says. “It may not make sense to take a machine out of service for half a day when a dealer can do it in significantly less time. Utilizing the dealership is appealing not because it’s the cheapest option, but it may return the best opportunity cost, be the most convenient and reduce downtime,” he adds.
The bottom line with maintenance decisions is to properly calculate the value of your time and the level of your expertise. You may determine that by staying on task with billable projects when work is available, you could afford to outsource maintenance and come out ahead financially.
Sums up Sams, “Do what you do best. If you dig trenches, then dig trenches, and let your dealer take care of your equipment.”
Compact Equipment Inspection Checklist
Visual:
Frame/house
Lift arms/boom
Attachment quick-tach mechanism
Workgroup
Pivot pins
Tires/rims/tracks
Axle seals
Cylinders
Quick couplers/hoses
Rollers/idlers/sprockets
Track tension
Leaks
Bucket teeth/cutting edges
Operational:
Drive and hydraulic functions
Pedals/controls
Auxiliary functions
Preheat system
Gauges, dash panel
Active codes/warnings
Lights
Heating and cooling systems
Cab
Throttle
Engine:
Hoses/connections
Exhaust system
Radiator/cooler
Battery level/connections
Belts/idlers
Leaks
General Maintenance:
Engine oil and coolant levels
Engine air filter
Hydraulic fluid level
Chaincase fluid level
Debris build-up
OEM Parts Protect Uptime
‘Parts is parts.’ You’ve probably been hearing that old adage ever since you’ve been in business, but it’s simply no more factual than it is grammatically correct. Not all parts are created equal, and it’s easy to get distracted by the growing number of bricks-and-mortar parts supply stores and the explosion of online aftermarket parts outlets. It can be tempting to cut costs with lower priced alternatives, but in an age of increased environmental regulations, cheaper options can easily cost you far more in lost time and revenue than using genuine original equipment manufacturer (OEM) parts.
To most owners, the quality of wear items like fluids, filters, tires and tracks is as important as the quality of steel itself. There are several clear advantages to installing OEM parts that are tested and proven. First, your machine’s parts are built to OEM specifications and often carry a warranty that can help protect the overall value of your machine.
Equipment manufacturers are monitoring the additional requirements resulting from EPA-compliant emissions standards that are placing greater restrictions on the types and quality of oil that are formulated for exhaust treatment systems. The use of OEM parts can also help reduce breakdowns. For example, something as simple as the use of an improper hydraulic filter may lead to an increase in contaminants. This can cause premature wear to pistons in the pump and potentially lead to a catastrophic failure in the hydraulic system.
Comments