September 2012, Vol. 67 No. 9
Features
Massive Spincast Culvert Rehab For INDOT
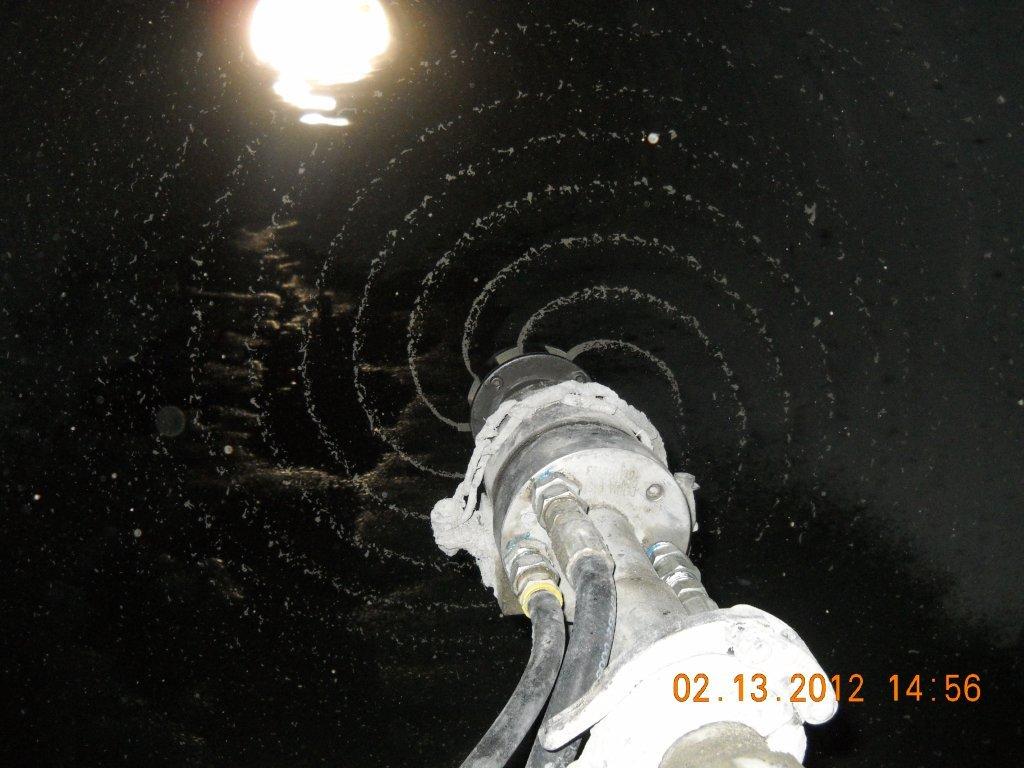
Among its many on-going highway improvement projects, the Indiana Department of Transportation (INDOT) is renovating failing culverts that are critical elements in the drainage systems that protect state and interstate highways.
Along a 63-mile segment of Interstate 74 between Indianapolis and the Illinois state line is the largest culvert pipe lining project ever undertaken by (INDOT) in terms of number of culverts and dollar value of the contract, said Karl Bates, project manager/estimator with Indiana Reline, contractor for the project.
Whenever possible, culverts beneath major highways are repaired and renovated, rather than replaced. Excavation to install a large-diameter culvert beneath an interstate highway is costly, time consuming and requires rerouting traffic during construction.
Indiana Reline currently is working on a $4.2 million INDOT contract to reline 43 ranging in diameter from 24 to 114 inches along this section of Interstate 74. Subsequently, three 90-inch and one 96-inch culverts designed to be relined by cured-in-place pipe were changed to centrifugally-cast-concrete pipe (CCCP) via value-added engineering.
Various lining methods are being used, depending on condition and inside diameters of the pipes, said Bates.
Thirteen large-diameter culverts are being lined with a CCCP liner, the first time this product and process have been used in the state, said Bates. Centri-Pipe is the product being used.
Centrifugally-cast pipe
“Three of the culverts represent the largest Centri-Pipe installations in the world,” he pointed out. “They are large, arched corrugated metal pipe (CMP) structures with round equivalents of 114 for one pipe and 108 inches for the other two. The culverts had been installed in the 1950s and had various issues including deformation, severe denting and rusted inverts. All were below seven to 10 feet of cover.”
The Centri-Pipe process uses a remote-controlled spincaster to apply a concrete coating inside the old pipe, said Bates. The spincaster travels at a speed to insure the uniform thickness of concrete as specified by each installation. The device can be started and stopped as needed without leaving joints or gaps, resulting in a seamless, high strength, fully structural pipe without reducing the pipe’s capacity.
Centri-Pipe’s manufacturer says the product and process are designed to provide waterproofing, sealing, structural reinforcement and corrosion protection for sanitary and storm culverts without trenching and at a significant savings in costs. It can be used in pipes of diameters from 30 to 120 inches.
CCCP was specified on selected culverts because pre-qualified CIPP contractors were not capable of installing liners in these sizes, said Bates. The INDOT pipe committee already had researched CCCP and was interested in utilizing it on a project, he added.
Process
Bates describes the CCCP process.
“The first step,” he said, “is determining the condition of the host pipe and taking accurate measurements of its dimensions and depth of cover. Because no water can pass through the culvert during CCCP installation, a bypass pumping system must be set up.”
Next is a thorough cleaning of the host pipe invert and removal of all debris in pipe configurations. The entire inside surface then is pressure washed to remove loose material.
For inverts missing portions or deteriorated to the stage where structural integrity is lost, crews pump in self-consolidating mortar to fill damaged inverts and permanently seal the bottom of the pipe making a new, watertight base and providing a new floor that can be flat or contoured to the pipe’s shape. For the I-74 projects, AP/M PL-12,000 is being used. A day’s curing is necessary before proceeding to the spincasting application.
“The equipment,” explained Bates, “includes the spincaster machine itself, mortar mixer and pump, a computerized winch, an air compressor, various hoses, centralizers, and the equipment to unload pallets of Centri-Pipe’s PL-8,000 material to be applied by the spincaster.”
Usually the high-speed spincaster is placed in the center of the pipe at its downstream end.
“The material is applied via the equipment in varying lifts of 1/4 to 3/4 inch,” said Bates. “Generally one application is made per day. Upon completion of the final lift, a curing compound is applied to the entire surface of the rehabilitated structure.”
PL-8,000 is a high-strength, abrasion- and corrosion-resistant fiber-reinforced mortar based on advanced cements and additives plus mineral, nano and polypropylene fibers. PL-8000 can be applied to concrete, clay, metal and brick culverts,
The final product should have the same life as a concrete pipe section of similar diameter and thickness, said Bates. The new pipe is 100 percent environmentally sound, waterproof, fully sealed from end to end, and provides highly-effective corrosion protection that can double the life of the pipe.
First project
Bates said the first INDOT culvert rehabilitated with the Centri-Pipe process was a 128 by 83-inch (102-inch round equivalent) pipe completed in approximately 2½ weeks of work, including establishment of the bypass pump system, cleaning and pressure washing of the host pipe, application of 1.6 inches of PL-8,000 material and general clean-up. Other structures using the CCCP process are expected to require approximately the same amount of time.
“We are pleased to be the company that used this product for the first time in the state,” said Bates. “At this time, the three liners in the original contract represent the largest CMP pipes relined by CCCP spincasting technology in the U.S. We have completed one other culvert project with CCCP on Interstate 70 outside Indianapolis, and we are scheduled to use the process to rehabilitate a 117- by 79-inch (102 equivalent round) culvert on SR (State Road) 160 in Southeastern Indiana later in the year.”
Bates estimates that by the end of the year, Indiana Reline will have completed approximately 15 CMP culverts in the state.
Depending on size and shape and condition of pipe, open end requirements and hydraulic capacity, other culverts in the basic contract are being rehabilitated by HDPE sliplining, CIPP and deformed HDPE sliplining using specialized hydraulic equipment to compress circular HDPE liner to an oval shape.
Indiana Reline was incorporated in 2000 and initially specialized in sliplining and cellular grouting. Today the company is one of the largest sliplining contractors in the Midwest, providing design services, construction and on-site technical support. In addition to sliplining and grouting, the company offers pipe bursting and pipe ramming services, HDPE fabrication, PVC segmented lining, centrifugally cast concrete pipe lining, hand-mine tunneling and lake and spillway rehabilitation. Indiana Reline is based in Sulphur Springs, IN.
Centri-Pipe manufacturer Action Products Marketing AP/M, Johnston, IA, began rehabilitating manholes in 1985 with its patented Permaform system and developed the high-strength, cast-in-place sealing and Centri-Pipe technology employing Permacast specialty mortars.
INDOT is responsible for construction and maintenance of state roads, interstates and U. S. highways in the state, including adjacent overpasses and ramps on these roadways, and signs and traffic signals. INDOT maintains more than 11,000 centerline miles.
In addition, INDOT is responsible for maintaining nearly 6,000 bridges across the state and regulating approximately 4,500 railroad miles and more than 110 public access airports and 560 private airports.
FOR MORE INFO:
Centri-Pipe — AP/M Permaform, (515) 276-9610, http://permaform.net/site/
Indiana Reline, (877) 533-5040, www.indianareline.com
Comments