September 2012, Vol. 67 No. 9
Editor's Log
Benefits Of Equipment Diversity
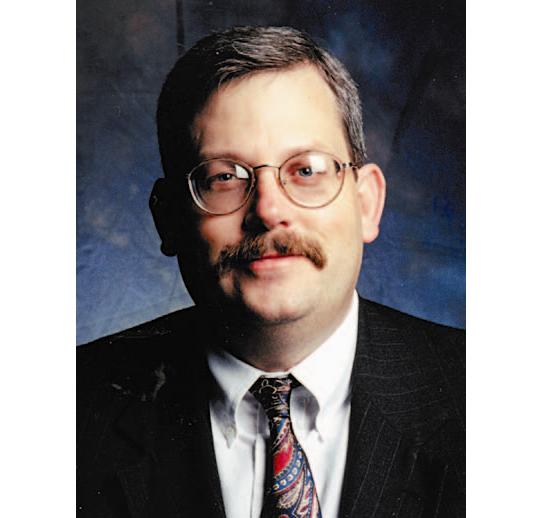
In this issue of Underground Construction, there are several project stories that all feature radically different equipment technologies or applications. Some have been around for many decades, others just a short period.
But these wildly different examples of construction and rehabilitation technologies represent fast-developing and diverse applications that the modern underground infrastructure industry demands for various markets.
Therein lies the future of our market – a buffet of boutique solutions for virtually any kind of problem that can be encountered in the underground infrastructure. It seems there is no end to the challenges and solutions that contractors, engineers and owners have shared with me over the past couple of years – often using both trenchless and traditional construction methods.
In discussions with owners and consulting engineers, I’m seeing a confidence level in the ability of modern construction methods and contractors to that didn’t exit just 10 or 15 years ago. Back then, trepidation was more the rule when an approach outside the traditional mainstream was proposed.
Now, we’re seeing just the opposite. Hard rock or boulders in the ground? That’s okay, just go ahead and drill it! On page XX, an article with Brotherton Pipeline relates a problematic project in Colorado that included “boulders the size of trucks. Drilling through these conditions doesn’t get easier but we have learned and continue to get better.” And that’s the point: as an industry, we continue to excel and find solutions that were unthinkable just a few years ago.
Another example comes from Kamloops in Canada (see article on page XX). A huge auger boring machine – probably the world’s largest – has been busy in Western Canada on projects with a variety of conditions. If wasn’t very long ago that such a machine generating 1.8 million pounds of thrust was thought to be too ambitious and unwieldy to be practical. But Kamloops made the investment and continually finds applications for the machine, allowing them to tackle jobs others have to pass on.
On the rehabilitation arena, culvert renewal used to be remove-and-replace only. Today, several technologies allow for renovating corroded culverts in place. Contractor Indiana Reline has found a profitable niche using a newer centrifugally-cast-concrete pipe technology to line culverts up to 114 inches.
Trenching on steep, slippery slopes; extremely tight line and grade tolerances; deep, precise excavation in a hurry: today’s construction equipment has the power and sensitive handling for almost any job.
The examples are endless as are the solutions for the problems of current-day underground infrastructure. Of course, there are a few remaining limitations and sometimes such broad capabilities may be considered a curse when a project goes bad for whatever reason or owners have unrealistic expectations. But for the most part, the industry can take pride in its ability to deal with demands of the varied and complicated underground infrastructure market.
Big is back
America’s shale play for oil and gas has been well-chronicled. “Fracing” technology has allowed horizontal wells to release heretofore unimaginable quantities of oil and gas upon the U.S. market, all produced domestically for primary use within America’s borders. Just a few short years ago, no one would have dreamed that kind of energy security was possible. Now, depending upon how we react to our vast new energy treasure trove, the U.S. has a real chance of obtaining substantial energy independence in a relatively short period of time.
Of course, connecting all of the new wells requires a vast, new or expanded infrastructure bringing contractors a wealth of work. And horizontal directional drilling is playing a key role. In fact, in some ways, HDD has now come full circle.
HDD started out as a “big rig” technology for installing large diameter oil and gas pipelines across major rivers. As the technology caught on and evolved, it was “downsized” to become applicable for the telecom boom of the 90s along with about every other type and size of pipe/conduit installation imaginable.
With the rebirth of America’s energy industry and the need to install thousands of miles of medium to large pipelines, HDD has played an integral role in this massive construction endeavor. For most of the work, mid to large HDD units are the most efficient and expeditious method of executing the hundreds of crossings being let each month.
Shale has been – and will continue to be – very good to America. HDD contractors couldn’t agree more.
Comments