October 2012, Vol. 67 No. 10
Features
Solar Farm Uses Underground HDPE Conduit For Longevity, Quick Install
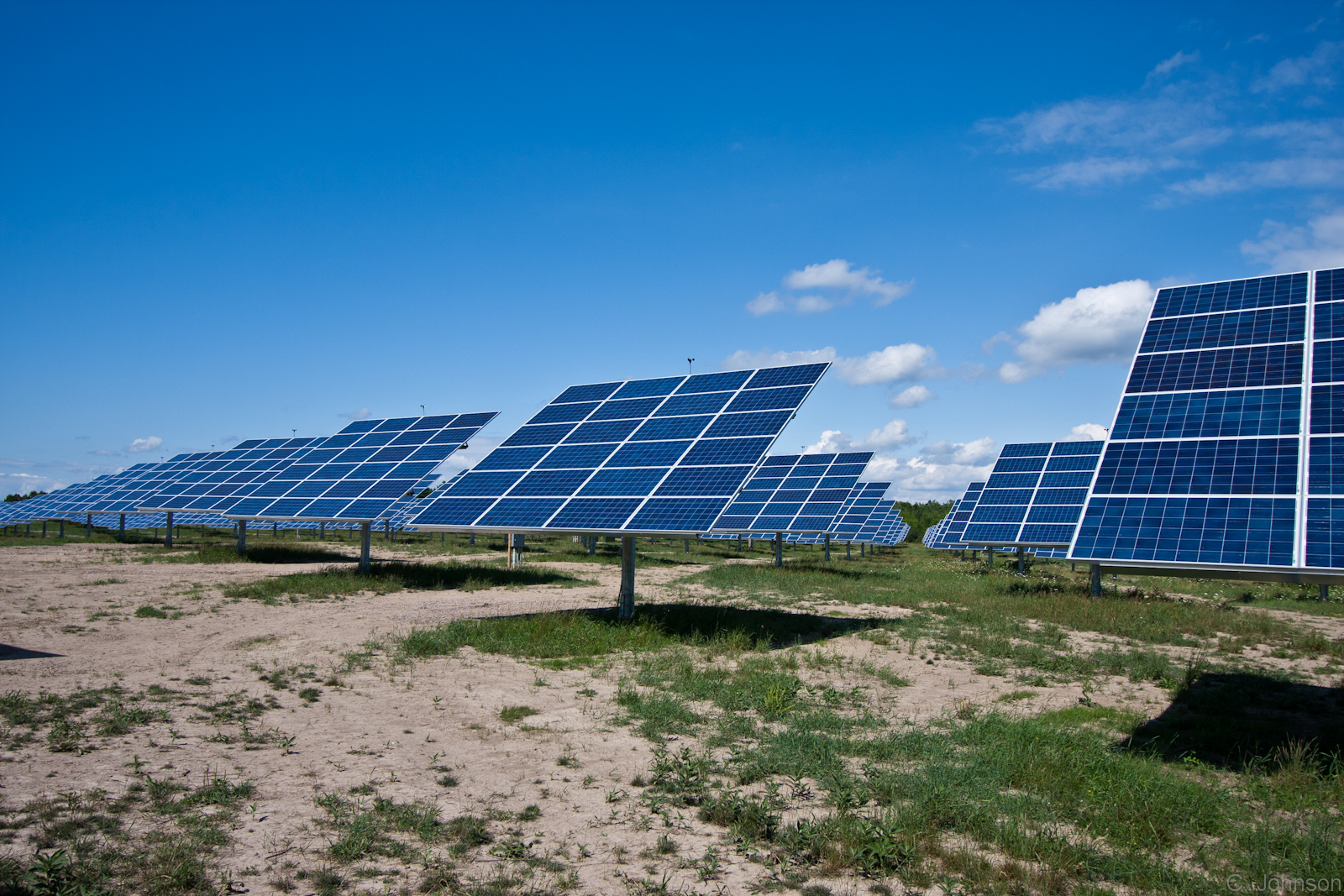
The largest solar farm of its kind in North America elected to locate power and control cables in underground conduit made from high-density polyethylene (HDPE) as a way to increase the life of the facility. The 2.2 MW solar farm covers 25 acres and includes 382 solar trackers.
Cables convey power from the solar trackers to the electric grid. AllEarth Renewables Inc. (Williston, VT), designed the solar farm and manufactured the AllSun Trackers Series 24 solar trackers.
“From a sustainability standpoint, HDPE pipe and solar power are a unique partnership,” stated Tony Radoszewski, executive director of the Plastics Pipe Institute, Inc. (PPI), the major trade association representing all segments of the plastic pipe industry.
“Like solar, a plastic pipe system is a sustainable and environmentally responsible choice that will serve generations to come. The HDPE conduit is ecologically efficient during manufacturing. The conduit is also strong, durable, light-weight and flexible while providing excellent protection for the power and fiber cables inside, and requires significantly less energy to fabricate, transport and install than other pipe products. And here in Vermont, HDPE conduit is the perfect choice to stand up to the extreme cold weather and frozen earth, plus it was the key to a successful trenchless run in one section.”
Installation of the HDPE conduit was done using cut and cover, and horizontal directional drilling (HDD) under a forested area. All low voltage wiring used UL 1990 certified Cable In Conduit (CIC) provided by Blue Diamond Industries.
Major pipe order
The AllSunTracker conduit included nearly 70,000 feet of 3/4 inch CIC pipe with three 6AWG and 5,000 feet of 2.5-inch diameter CIC with 4/0 wiring for the panel feeder lines. Blue Diamond supplied Cable In Conduit on reels ranging from 2,000 to 10,000 feet. The company is listed by UL for specification UL 1990, Nonmetallic Underground Conduit with Conductors and its CIC is manufactured under ASTM D 3485.
“Most solar farms use underground PVC pipe,” stated Doug MacDonald, engineering technician for AllEarth. “Wire is pulled onsite after conduit installation. For this project, the HDPE conduit came preloaded with the wire, so it was really just a one step process after digging the trench. It also enabled us to use a smaller conduit size, reducing the cost of materials.”
“Typically when other types of conduit are used, it can turn into a very labor-intensive project,” explained Radoszewski. “This is because a trench must be dug, the conduit installed and then a pull rope is blown through the conduit so that each wire can be pulled back through. Because the HDPE conduit can have the wire installed when the pipe is being extruded, it comes to the job site ready to go. This saves considerable time.
“Custom lengths can be ordered and sometimes a single reel will hold thousands of feet, which puts more conduit at the site to further expedite installation,” he continued.
Total power produced by the South Burlington Solar Farm is estimated to be approximately 3 million kilowatt hours a year — 45 percent more than the amount of electricity that could be produced by a fixed roof-top photovoltaic system of the same size. The project is owned and operated by the Chittenden County Solar Partners LLC. The value of the electricity generated by the farm has been tagged at $924,000 a year and is enough to power more than 400 homes.
While most of the installation was accomplished using cut and cover, the HDPE conduit also provided the solution to go under a heavily forested section of private property and a section of wetland.
“We directionally drilled two, 400-foot runs of five-inch diameter HDPE pipe used for the main power feed and communication cables,” explained Aaryn French, project manager for Engineers Construction, Inc., Williston, VT.
French agreed having CIC was a benefit. It took his four-person crew just a month to install all the low and medium voltage conduit at an average depth of three feet. “The trenching, which was the majority of the work, went very smoothly as well. It was nice because we’d just start pulling the wire out and leave the proper length at the end and just lay it right in the ground.”
“We’re seeing more and more power and fiber optic cables being put underground,” Radoszewski said. “This is especially true of new housing and building construction. CIC is also very popular for installing FAA lighting for airport applications. Plus, there is a strong move today for communities to take existing overhead lines and bury them to eliminate ‘wire blight’ and provide safer and more secure power and telecom systems, which are also protected from severe weather.”
FOR MORE INFO:
Plastics Pipe Institute, (202) 462 9607, www.plasticpipe.org
Blue Diamond Industries, (859) 224-0415, www.bdiky.com
Comments