November 2012, Vol. 67, No. 11
Features
Quest For Innovation At The Trenchless Technology Center
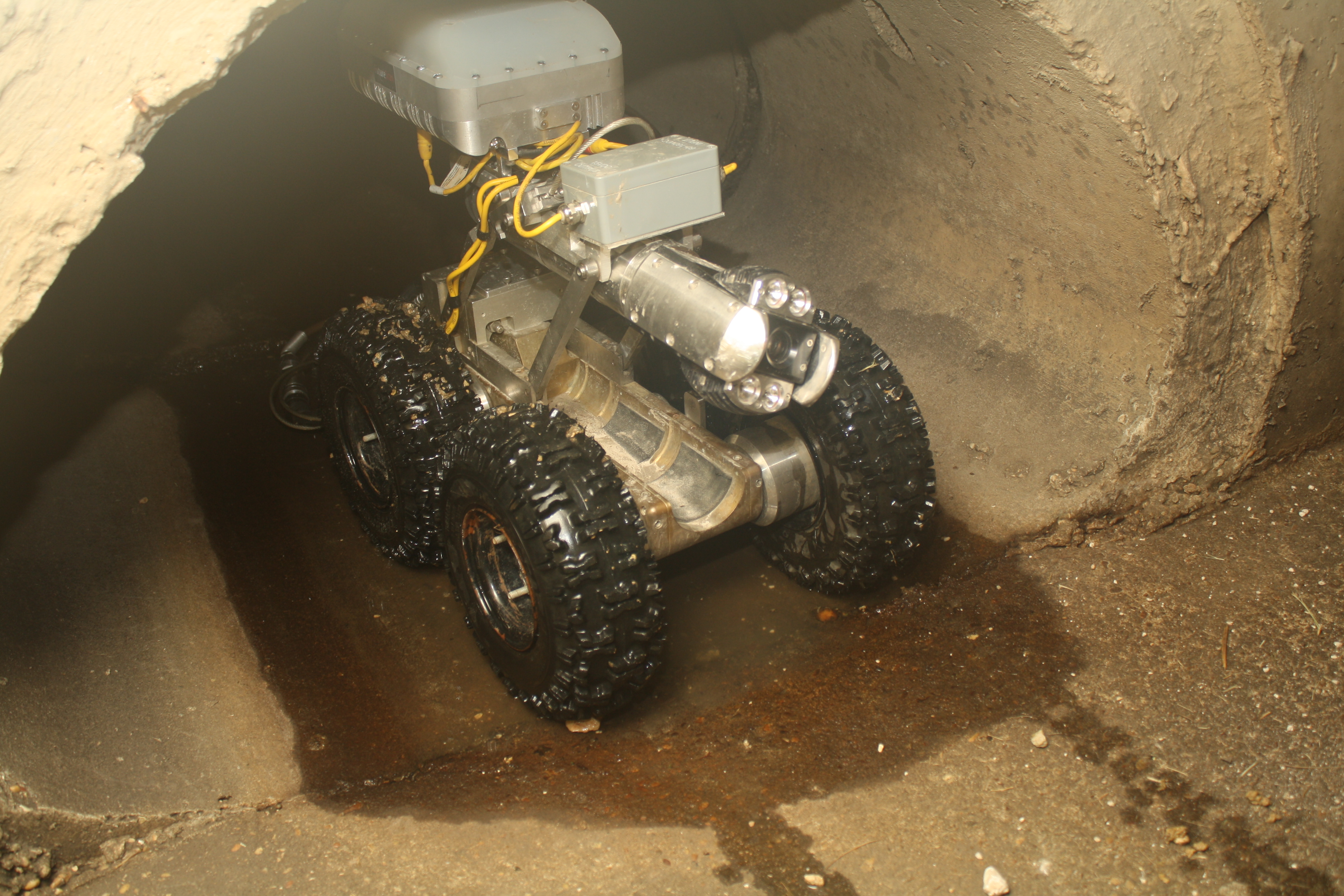
Since 1991, the Trenchless Technology Center (TTC) at Louisiana Tech University has been working to develop its role in support of the development of trenchless technologies and the more effective installation and management of the nation’s buried infrastructure.
Early projects tended to focus on improving the understanding and design of the core trenchless technologies applied to both installation and rehabilitation of buried utilities, and to support the various associations that were providing information to municipalities and other utility owners to encourage them to adopt the latest technologies.
With the basic trenchless methods widely accepted and well-enough understood for most applications, the role of the TTC has had the opportunity to shift in recent years. It now has a more active role as an innovation engine for the industry coupled with a continued quest to understand the fundamental performance issues associated with various trenchless methods. This work continues to be guided by the TTC’s Industry Advisory Board which is made up of representatives from municipalities and utilities, key industry companies in the trenchless technology field, consulting engineering firms and relevant associations (see sidebar).
The ability to conduct cutting edge research in most fields today requires the collaboration of various specialists that can combine knowledge in the application needs, sensors and instrumentation, simulation and computing and user interface development. It also requires extensive research equipment and testing capabilities both for sensor development and testing as well as for the pilot scale demonstration of the final product.
Such developments have been possible in the TTC through collaboration with faculty across the College of Engineering and Science – including faculty in Civil Engineering, Physics, Chemistry, Electrical Engineering, Mechanical Engineering and Computer Science. It has also been made possible by major enhancements in the TTC’s research facilities – including a new research building dedicated in 2007 (which was built with major contributions from the trenchless technology industry) and substantial research equipment enhancements made possible by grants from the National Science Foundation and major research project investments. Investments in research equipment and instrumentation alone have totaled $2 million over the past eight years.
TTC Director Dr. Erez Allouche, who joined Louisiana Tech University in 2003 and became the TTC Director in 2012, observes that the TTC’s technology development and rapid prototyping capabilities are attracting growing interest from across the nation, as it allows the industry to develop unique technical solutions in a professional environment, while leveraging their limited research and development dollars with state and federal grants.
This article will focus on three current thrusts to give a flavor for the type of innovations currently under way at the TTC. These innovations, as well as other technologies under development at the TTC, are either patented or patent pending. A more complete listing of TTC activities and facilities as well as its extensive cyber based resources can be found at the TTC’s website, www.ttc.latech.edu and Facebook (http://www.facebook.com/trenchlesstechnology). A new feature which might be of particular interest is the TTC’s Trenchless Technology Electronic Reference Room (T2eR2), which is schedule to come on line in the first quarter of 2013.
Finding laterals more reliably after relining
Cured-in-place pipe (CIPP) is the most commonly used method for the rehabilitation of municipal buried pipes in the world. Over the past 40 years, millions of feet of CIPP were installed around the world. The vast majority of sewer liner installtions in the past used a felt fabric into which the resin was impregnated but incorporated no structural fiber reinforcement. Thus, when a liner was inverted and cured, an indention (or dimple) formed at the location of the lateral services, allowing an operator to properly position a cutter to restore the main-lateral connection.
As rehabilitation technologies have shifted, however, to the rehabilitation of pressure pipes and more efficient means of lining large diameter sewers, the need for higher hoop strengths in the liner has resulted in the incorporation of glass fiber, carbon fibers and other stiffer materials in the CIPP fabric. Furthermore, the service connections of water and gas mains are significantly smaller (one – 2-inches diameter) than sewer laterals (three – 6-inches diameter).
With visual inspection no longer reliable as the means of identifying the location of lateral services behind the newly installed liner, several indirect measurement technologies have been developed, including the use of eddy currents, thermal imaging, magnets placed in the lateral prior to relining and a pipe locator sonde. However, these methods can suffer from significant disadvantages depending on the method specifics including inaccuracy, incompatibility with some material types (e.g., thermoplastics), size limitations (e.g., cannot fit into a six-inch host pipe) and low productivity (up to six hours to locate a single lateral) or the need to place/retrieve an object in the lateral.
To avoid current problems, the TTC has developed a microwave-based, near-field sensor to pin-point the location of the lateral regardless of the material compositions of the main and the service line. The solution has used off-the-shelf components embedded into a custom-designed electronic board. This exciting technology, which is capable of entering a five-inch diameter pipe and locating a lateral in about two minutes regardless of the composition of the main and lateral pipe material, is expected to reduce the risk, and therefore the cost, associated with the rehabilitation of small-diameter pressure pipes. The prototype lateral locator is currently undergoing bench scale testing and in-pipe deployment is expected in the first quarter of 2013.
Figure 1: Sensor positioned inside a cast iron pipe (8-inch diameter) lined with a 0.25-inch thick CIPP liner
Figure 2: Surface plot of the signal from sensor: the circle represents the actual location of the lateral; green contours on the plot show the area which was discriminated by the sensor; blue color is the background
‘See through wall’ imaging technology
The impetus for this research has come from the needs in a wide range of commercial sectors for improved methods of “seeing” behind visually opaque objects. This is of special significance in the inspection of buried pipes where utility owners would like to understand the bedding conditions outside a pipe or the presence of soil voids without having to excavate from the surface down to the pipe level. In a now commercialized innovation, the TTC worked with Cues to develop a rapid deployment in-pipe radar system named ‘FutureScan’, which is incorporated with an advanced CCTV system and can scan for voids outside a sewer pipe without interfering with the speed and efficiency of the CCTV inspection.
FutureScan is an innovative in-pipe radar system that utilizes state-of-the-art electronics to generate extremely short electromagnetic pulses over a range of frequencies in the GHz range, enabling the user to image through solid surfaces, such as reinforced concrete, asbestos cement and clay pipe walls. Mounted on a robotic transporter, this in-pipe penetrating radar sends out signals in near real time that pass through the pipe wall and into the soil surrounding it. The reflections of these radar signals are then used to dimensionalize the pipe, i.e., to paint a picture of the pipe’s conditions similar to the way an MRI can depict the human body. The data captured can then be processed to provide information about the anomalies within and outside of the pipe wall, including the potential presence of anomalies, soil voids, external corrosion, defective joints and more. An image of the FutureScan is given in Figure 3.
In early August of 2012, following years of intensive research and development effort, funded partially by the National Institute for Science and Technology (NIST), and performed by a joint dedicated research team consisting of Cues, a world leader in the manufacturing of CCTV and other pipeline inspection platforms, and TTC technical staff members, the first full-scale field demonstrations of the FutureScan technology took place. A total of 1,500 linear feet of pipes were inspected in the city of Slidell, LA, and an additional 500 feet of pipe were inspected in the city of Shreveport, LA. The demonstrations covered a range of pipe materials and geometries, from 18-inch circular VCP, through 24-, 30- and 42-inch circular reinforced concrete pipe, to 32 by 60-inch reinforced concrete arch pipe. Data can be collected at speed of 30-feet per minute, and radar images can be viewed both in real time and in a post-processing mode. CCTV images are collected during the radar inspection, corroborating the radar data observations made from the CCTV images. The raw radar data is exported into signal processing algorithms that extract the desired information and present it in a visual format.
The emergence of the FutureScan technology provides municipal engineers, consultants and city administrators with a new tool to assess the structural integrity of their buried infrastructure and ensure public safety. The FutureScan technology could also assist in detecting boulders or other objects that might apply point loads onto the wall of a buried structure, as well as detect concrete encasement zones prior to pipe bursting operations. The ability to ‘see’ into the pipe wall and beyond, will enable administrators, engineers, and contractors to make more informed decisions and reduce the risk associated with the operation, maintenance and rehabilitation of underground infrastructure systems.
Figure 3. FutureScan module in deployment
Figure 4. The radar module can be mounted on a range of existing CCTV platforms and enters the pipe via standard manhole access points.
eVortex: Energy harvesting from waste, storm water
There are thousands of sewer drop structures across North America ranging from five to over 300 feet in height, which convey flows of up to 4,500 cubic feet per second year round. Drop structures direct flow from shallow surface sewers to deeper collection tunnels via a vertical shaft. An advanced version of drop structure known as ‘vortex drop structure’ is becoming popular and its primary objective is to dissipate energy so that the otherwise free falling flow within the drop shaft does not erode the concrete base of the shaft and to minimize the water turbulence in the drop structure that would otherwise allow odor-causing dissolved gasses to escape into atmosphere. In this innovation, a novel low-cost turbine with an integrated electrical generator called ‘eVortex’ is under development for harvesting the enormous kinetic energy available in waste water passing through the municipal drop structures. TTC researchers Dr. Arun Jaganathan and Dr. Erez Allouche, supported by EPA, DOE and IPEX Inc., are involved in this research.
Figure 5 shows the photograph of a drop structure under installation and a prototype of the eVortex under development integrated within a commercially available Vortex Drop Structure. To demonstrate the technology, the research team completed and successfully tested a lab-scale eVortex prototype, which was integrated into the wall of a four-inch diameter drop structure. More recently the TTC fabricated a full-scale eVortex system (six-inch diameter, 30-foot tall drop structure) capable of handling flows of up to 800 gallons per minute. The full-scale system is equipped with an integrated turbine and power generating assembly. The power generated by the energy harvesting system is used to provide some of the electrical power needed to run the equipment that pumps the water from the reservoir at the base of the tower to the intake of the vortex 30-feet above it. The full-scale prototype will be used to develop energy-production curves for various flow rates and volumes.
eVortex technology provides an opportunity for municipalities to generate electricity from an energy source that would otherwise be wasted. This newly tapped power and/or revenue source can offset the costs of wastewater pumping elsewhere in the system, provide a new steady stream of revenue or used to power local systems (e.g., sensors, lights). It is worth mentioning that the major component of the infrastructure required for eVortex, namely the drop structure, is already in place.
Fig 5: (left) Field installation of Vortex Drop Structure; (right) eVortex prototype installed at the TTC
SIDEBAR:
HED: TTC Members Industry Advisory Board
Industry
* Aqua-Pipe
* IPEX
* LMK Enterprises
* Reline America,Inc
* Reynolds Inliner
* Sekisui-SPR
Contractors
* Insituform Technologies
* BRH Garver Construction
Associations
* LA CETF
* NASSCO
* UCTA
Media
* Benjamin Media
* Underground Construction
Consultants
* Boyer Inc.
* Brierley Associates
* Carollo Engineers
* CH2M Hill
* Jacobs Associates
* Jason Consultants
* Kleinfelder
* MWH Americas Inc.
* Parsons Brinckerhoff
* Pipeline Analysis, LLC
* PipeMedic+
* Southern Trenchless
Education/Research
* Battelle Memorial Institute
Public Works
* Boston WSC, MA
* City/Co of Denver, CO
* City of Columbus, OH
* City of Dallas, TX
* City of Houston, TX
* Citizens Energy Group, IN
* City of Los Angeles, CA
* City of Monroe, LA
* City of New York, NY
* City of Ruston, LA
* City of Shreveport, LA
* Miami-Dade County, FL
Comments