November 2012, Vol. 67, No. 11
Features
Jim Lee, Auger Boring Guru: Industry Profile
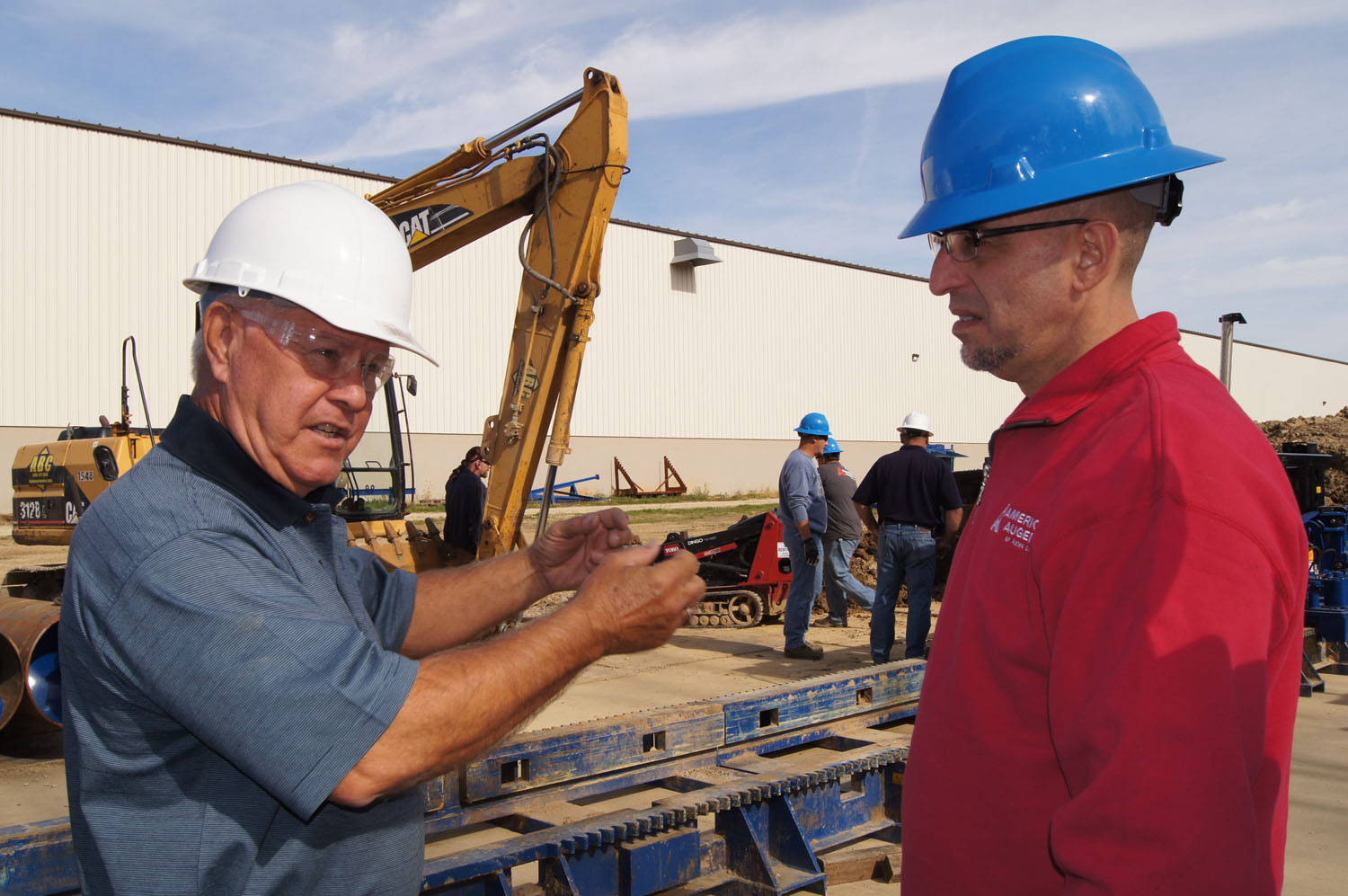
When he took the telephone call, Jim Lee was busy preparing to leave town.
He was at home in the Jackson, MS, suburb of Brandon and would leave the next day for an extended trip that would take him to auger boring job sites in New York, Wisconsin and Canada. Such a schedule is routine for Lee, a field service technician for American Augers.
The caller wanted to talk about Lee’s career in the auger boring industry, how he has come to be regarded by many as the most knowledgeable expert in the auger boring industry.
However, Lee would never describe himself that way. He’s been in the auger boring business since 1973, first with an auger boring contractor. Twelve years ago he joined American Augers. He knows about every brand of auger boring machine and encountered about every possible situation while making auger boring installations. He has a quiet confidence in his position with his company and within the industry and doesn’t find it necessary to boast.
“Jimmy Lee has years of real-world experience, and that certainly gives him an advantage when he goes in the field to help crews troubleshoot difficult projects,” says John Hoffman, American Augers product support manager, and Lee’s boss.
“A lot of people in the boring business rely on Jimmy and what he knows,” continues Hoffman. “When they get in trouble, they say, ‘It’s time to call Jimmy.’ Much of Jimmy’s knowledge comes from literally living auger boring for all these years. He knows what to do because he’s been there, done that.”
In the Navy, Lee was a welder in a shipyard. After leaving the service, he went to work as a welder for Fornea Road Boring in Jackson. He quickly took an interest in boring machines and the auger boring process and became a boring crew member. He’s been immersed in auger boring ever since.
Old days
Auger boring was among the first trenchless technologies, in use for years before the term became popular. Auger boring provided the means to make short, relatively large-diameter bores of 50 to 100 feet.
“In the old days,” says Lee, “you dug a pit, set the machine in at the right elevation, and hoped it would come out right on the other side. In the ’60s and ’70s an old ‘hound dog’ locator would be used to track the path of the bore — it beeped when you got over the bore head.”
While with Fornea Road Boring, Lee’s skill stood out; he had the “feel” for what was happening under the ground and seemed instinctively to know what to do when something unexpected happened. Auger boring is a specialized field and those in it know others in the business. Lee’s reputation for expertise spread and demand grew for his advice about making boring installations.
“This industry is made up of good people who have a lot in common,” Lee says. “We respect each other, and we help one another whenever we can. Through those years, I learned from others and learned about other brands of boring machines in addition to those we operated. I never said anything bad about anyone or about the equipment they had.”
Lee has seen many changes in auger boring equipment.
“Compared to machines when I got started,” he said, “today’s models are easier to use, make much longer bores, and have features that allow them to compete with other types of trenchless equipment. Jobs that not long ago would require microtunneling can be done much more economically by today’s auger boring machines.”
In his time as a contractor, Lee also became involved in horizontal directional drilling (HDD), and he gained knowledge of other methods of underground construction, including the use of drilling fluids. However, his niche always remained in auger boring.
Moving on
Following the death of the owner of the contracting company where he worked and changes in the organization that followed, Lee concluded it was time to move on.
“There were several opportunities open,” he says, “and I chose American Augers. At first I was a district support manager and I went everywhere, not only boring jobs, but HDD jobs, too. Later I was shifted back to concentrate primarily on auger boring.”
Currently Lee averages 40 weeks of the year on the road.
“When Jimmy arrives at a job site, he takes charge to solve whatever prompted the call for help,” says Hoffman. “Jimmy’s not very big — maybe 5 (foot), 9 (inches) –but he’s a whirlwind of activity. His energy, expertise and work ethic bring respect. Jimmy loves and respects equipment, and I believe he retains a sense of ‘ownership’ in every American Augers machine, even after it’s been sold. And he can’t stand to see a machine abused or neglected. If he finds a boring rig that obviously hasn’t been maintained or is in need of repair, the crew and maybe the company’s owner will hear about it.”
Lee values his time at home in Mississippi, but Hoffman said he never really stops working.
“Jimmy always gets up early, 5 a.m. or so,” says Hoffman. “He shakes the rooster awake, and he’s ready for the day. Much of his off time at home is spent on the telephone advising boring crews.”
Lee says that’s true — he’s always on call.
“My wife and I took a trip to Gulfport,” says Lee, “and she said we never said a word to each other on the drive — I was always on the phone. Many problems I can solve by telephone. I just have to have complete information about the situation. Sometimes a crew chief will leave out a mistake that led to the situation, and that complicates knowing how to proceed. I need to know everything, and then I can offer practical advice to get them going again.”
Lee still maintains his always-on-the-go schedule, but it hasn’t prevented his career taking a new turn — he’s now actively involved in product planning.
“Jimmy knows so much,” Hoffman says, “we try to mine his experience in planning for product improvements and new products.”
For example, Lee is credited with a key role in the design and development of American Augers new 36GM8000 guided auger boring system. American Augers conducts hands-on boring schools at its facilities in Ohio, and Lee is there to teach and advise.
“I believe management and engineering listens to me and values what I know,” Lee says. “From being in the field, I can identify features that are needed to improve equipment, and users tell me what they believe is needed that could help them do their work better. That’s important information when planning machine designs. I respect that our company wants to put out the best possible products and that I am able to participate in achieving that goal.”
Now in his 60s, Lee is at the peak of his career. He admits the pace can be tiring.
“Sometimes I do get tired physically,” he says, “but I’m not tired of the job. I love punching holes through the ground . . . it’s a thrill of accomplishment to get from one side of the road to the other.”
Comments