June 2012, Vol. 67 No. 6
Features
Frequent Challenges For Winter Ocean Drilling In Maine
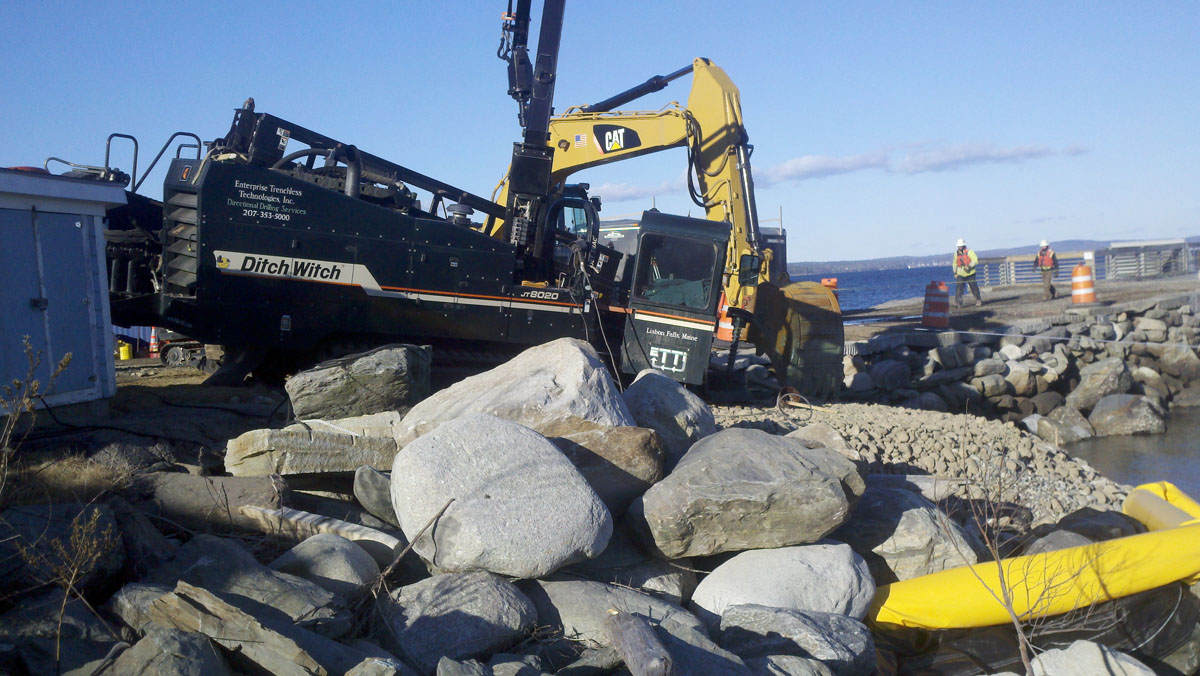
Water crossings — installing utilities under streams, rivers, lakes and other bodies of water — are among the most significant benefits offered by horizontal directional drilling technology.
Perhaps the most challenging water-related installations are those with the pilot hole launched from the shore and extending beneath the water of a bay or ocean, exiting through the floor of the body of water.
The past winter, drilling contractor ETTI, Lisbon Falls, ME, completed a project to take a 12-inch diameter HDPE sanitary sewer outflow line from a pump station into the Atlantic Ocean at Northport, ME. The project owner was the Town of Northport. The Town operates under a Maine DEP permit to discharge treated effluent into ocean. This project extends the outfall line an additional 300 feet to allow better mixing and dispersion of the treated discharge, said Tim Folster, vice president of operations, Sargent Corp., primary contractor for the project.
The project was designed to be constructed in the winter because the area has many high-end seasonal homes used from spring through fall, and the outfall was located adjacent to the municipal pier which is a gathering spot for tourists.
The design length of the outfall, from the pump house on land to the underwater exit point of the outflow line, was approximately 300 feet with an additional 300 feet laid upon the ocean bottom.
The original plan called for burying the pipe by open-cut construction using 100,000-pound excavators with extended booms working off barges, to excavate a trench underwater and allow the pipe to be installed and then backfilled.
“Without question, the plan was risky and would be very time consuming to execute,” said Kelly.
Expert advice
The Sargent Corp. approached ETTI seeking the HDD specialist’s input about whether directional drilling could be utilized.
“Actually,” said Kelly, “the first site visit raised major concerns. Drilling in Maine in January itself poses many issues with cold temperatures and short workdays. Structures are necessary to keep the mud systems warm and lines must be broken down quickly to keep them from freezing. Add to that the drill unit would have to be set up in a spot where tides average 11 feet. And moving 600 feet of 12-inch diameter pipe across the water in those rising tides and high winds seemed almost impossible.”
However, Kelly said Sargent is a bold and progressive company, always ready to think outside the box.
“We have worked with Sargent on many occasions,” Kelly said. “The previous year we had completed another shore approach project with Sargent which won a Build Maine Award from the Associated General Contractors of Maine. So the two companies had an experienced team in place well-suited to the Northport project.”
Ultimately, it was decided to use HDD on the project.
“Sargent,” Kelly said, “entrusted a great deal to our team, and we moved forward together to tackle one of the most challenging projects we’ve faced.”
To launch the HDD segment of the installation, the ETTI crew used a Ditch Witch JT8020 HDD unit powered by a 275-horsepower liquid-cooled diesel engine. The machine develops 80,000 pounds of pullback, 10,000 foot pounds of torque and spindle speeds to 210 rpm. The HDD portion of the project was 250-feet long under the ocean floor.
The drill unit was set up in a position extremely close to the point reached by high tides.
“Cold temperatures — the low-to-mid- 20s in the day and single numbers at night — required that drill steel pipe had to be protected from drill fluid freezing and splitting the pipe,” Kelly said. “This was accomplished with antifreeze and thermal blankets.”
Kelly called subsurface conditions “brutal.”
“Eighty percent of the drill was through heavy cobble and massive boulders,” he said. “The pilot hole was made with a five-inch Railhead Incredibit which fractures rock in a random elliptical pattern, ‘dancing’ in the hole to produce a larger-diameter bore than that of other bits of comparable size. On this project, the five-inch tool produced a 10-inch diameter hole. We tracked the drill head using a Ditch Witch 752 tracking system operated from a boat. A Ditch Witch FM50 fluid mixing system was used. The pilot hole was completed in a two-day period, working from 4 a.m. until dark.”
After the pilot hole was complete, construction divers, working from barges, changed out the downhole tools, using air bags to float them into position.
Floating pipe
The most complex part of the project was floating pipe into the water, positioning it, sinking the pipe in the correct position, and then connecting it to the drill string for pullback.
“The extreme tide cycles made moving 600 feet of 12-inch pipe into the ocean in January with heavy winds almost impossible,” said Kelly. “After several days of attempting to move the pipe with multiple large boats, we waited for a calm early morning and succeeded in moving the pipe into position and anchored it to the shore. Concrete weights had been attached to the pipe in the area where it was to rest on the ocean bottom. The pipe was flooded and air bags were attached to sink it to a neutral buoyancy position just above the bottom. Divers removed the drill bit and connected the backreamer and pipe behind it. Setting the turbidity curtains to keep silt and drill slurry from the ocean in such a tide cycle was also a challenge, but with the patience and experienced earthwork crews, ultimately we were successful.”
The pilot hole was enlarged and the product pulled in behind it in one pass.
“The soil had so much rock that we did not pre-ream the hole for fear of losing the shot,” said Kelly. “We gambled and utilized a new 18-inch Ditch Witch Kodiak reamer which performed flawlessly for the conditions.”
The installation was completed in less than 14 hours.
“The length of pipe was floated into the ocean and reached the final outlet point,” Kelly said. “The drill exit came out on the ocean floor and the remaining footage was placed directly on the ocean floor with concrete weights. The final portion from the drill entry was open cut back to the pump station.”
In its 17th year, “ETTI is primarily a directional drilling contractor, but also performs natural gas work for one of the local utility companies,” said Kelly. “We run two full-time drill crews, two natural gas crews, a shop/maintenance crew of two, a development crew working on a 50-acre parcel of land that will be a business park by the close of 2012, and an office staff of six.”
Kelly said the company has continued to grow throughout the current recession.
“To do that, we’ve had to get more creative in the marketplace since 2008,” he continued. “It should be no surprise that prices for work have changed in our industry with heavy competition and contractors who have been willing to cut prices. Despite the challenges we’ve kept focused on our markets of water, sewer and natural gas, all of which have been excellent industries to be involved in. Water and sewer infrastructures in New England are among of the oldest in the country, continually needing upgrades regardless of the economy. And natural gas has been so cheap in comparison to other fuels that it’s been in high demand. Overall, the course we set in the early years and the risks we took have paid off big during this period.”
ETTI’s sister company, Enterprise Electric has been in business 45 years, and Enterprise Designs is a two-year-old landscape/hardscape company.
FOR MORE INFORMATION:
ETTI, (207) 353-5000, www.hdd-etti.com
Ditch Witch, (800) 654-6481, www.ditchwitch.com
Railhead, (888) 313-7455, http://railhead.com
How To Survive A Recession? Refuse to Participate
ETTI President Scott Kelly said he often is asked how his company has continued to grow during a serious recession.
“My answer is we have leaned on our people,” he said. “From the start I’ve told all our employees that I’m choosing not to participate in the economic downturn, and we would accomplish that by a heavy emphasis on training, efficiency and utilizing technology to continue to be profitable.”
ETTI people give 100 percent each day, said Kelly.
That has gotten us through many tough spots,” he continued. “We accessed every facet of the business to cut waste, challenged our employees, shared financial data, set goals and maintain transparency from top to bottom in order to get everyone involved with ideas and decisions. We hire the absolutely best people in our industry, hold everyone accountable and establish mandatory employee goals each season.”
Kelly said the company also avoids poorly-designed projects or high-risk jobs without the financial return to cover the risks.
“Too many companies we see take huge risks for really cheap numbers and many have to pay a high price for the gamble, including bankruptcy,” he concluded.
Comments