July 2012, Vol. 67, No. 7
Features
Synchronized SBUs Bore Below Mississippi River: Multi-Tasking Auger Bores Move Muck For Force Main
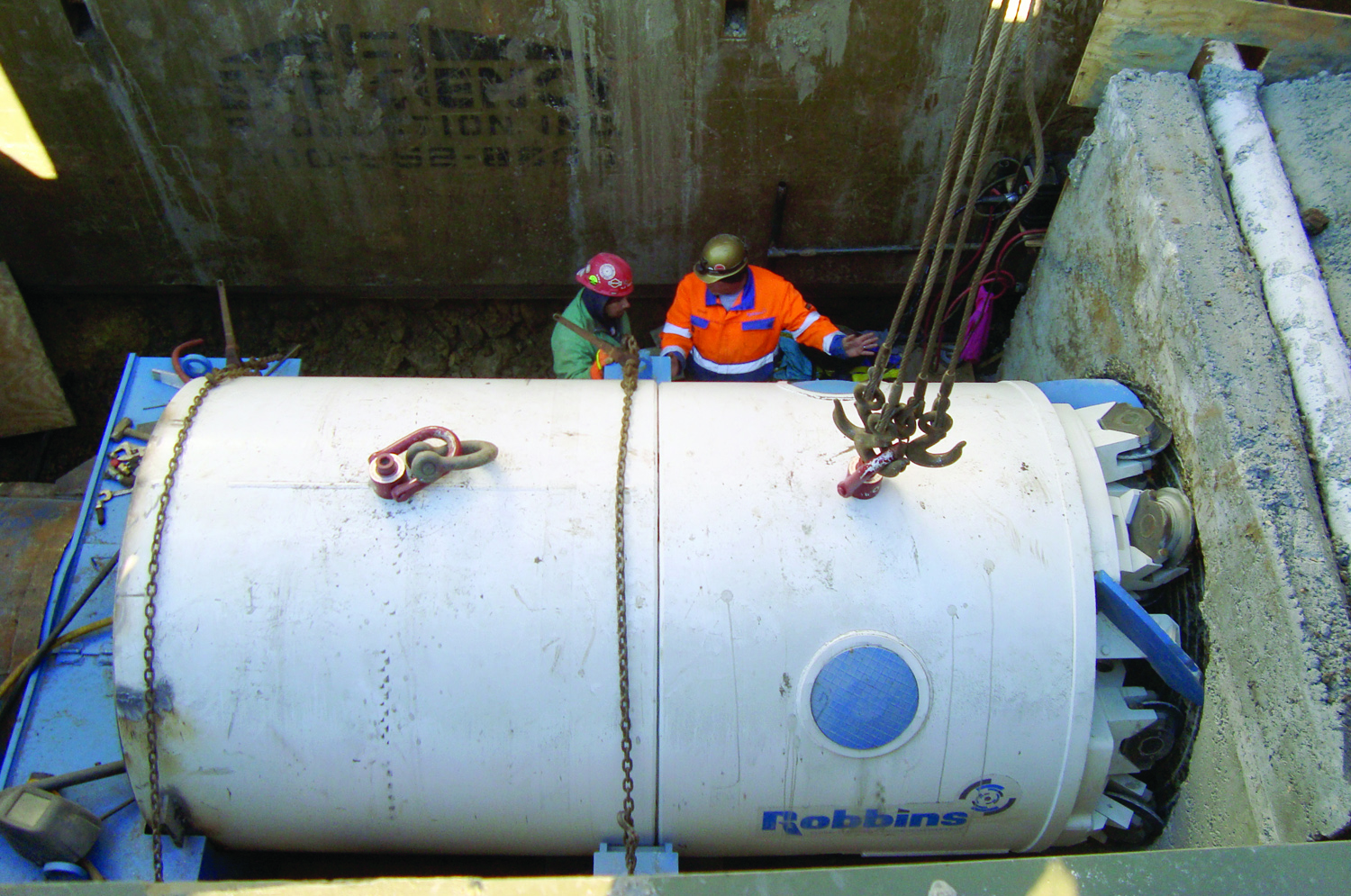
Illinois contractor L.J. Keefe Co. is no stranger to utility crossing construction, but a recent force main project in Clinton, IA, was no easy task, requiring six crossings below major highways and a channel of the Mississippi River. The simultaneous construction required hard rock and mixed ground auger bores as well as TBM tunneling, all within a short construction schedule of just five months.
“We had an extremely tight time frame, but we were able to work with the general contractor, engineer and manufacturer to encompass multiple different soil conditions and tight tolerances,” said Larry Keefe Jr., general manager of L.J. Keefe Co. Three crossings were ultimately excavated using hard rock Small Boring Units (SBU-As) as well as a large diameter mixed ground, motorized SBU (SBU-M)), both manufactured by the Robbins Company.
The city of Clinton Contract B Force Main Project consists of a new treatment plant and wastewater lines serving the cities of Clinton, Camanche and Low Moor. Wastewater from all three communities does not meet current standards for effluent discharge, and the systems themselves are inadequate and often over capacity.
Project funding came from a $20 million allocation of the statewide construction project initiative known as I-JOBS. Clinton was one of three towns to receive the funds, which were set aside for water treatment improvements in towns of more than 10,000 people.
Clinton named HDR Engineering Inc. as the project designer and Illinois-based Merryman Excavation as the general contractor for 17,200 feet of new sewer pipe. The $9.5 million contract, which called for six crossings below roadways and rivers, was awarded to L.J. Keefe Co. Three, 200-foot long crossings in silt and sand below Union Pacific Railroad tracks utilized tunnel boring machines, while other crossings in hard rock required different methods. “We anticipated rock for two crossings under the river, so the clear choice was the Robbins SBU-A for these,” said Keefe. While the 250- and 270-foot long crossings were anticipated as rock bores, a third, 395-foot crossing below a major highway was not so clear cut.
Robbins and L.J. Keefe crew members set the alignment of the SBU-M during its January 2012 launch.
Choosing equipment
Testing of the 395-foot crossing below Highway 67, the busiest roadway in the area, revealed a mixed face of silty, watery sand, clay and 10,000 psi UCS hard rock. “We opted to use SBU technology, even though other contractors said it could only be done with microtunneling. They thought this because of geology rather than crossing lengths,” said Keefe. Additionally, strict line and grade requirements were required to link up to the rest of the force main — within six inches of line and two inches of grade, thus requiring a machine that was highly accurate. The company owned a Robbins 36-inch diameter SBU-A, and had leased several SBUs on at least a dozen projects over 15 years. “We were looking for the right project to use the SBU-M, and with the mixed ground, tight tolerances and longer length, we thought this would be the perfect opportunity,” said Keefe.
The contractor opted for a Robbins 72-inch diameter Motorized Small Boring Unit (SBU-M) with mixed ground cutterhead, used in conjunction with a 60-inch auger boring machine. The 72-inch machine, the largest SBU-M yet built, would install steel casing of the same diameter to allow room for three bundled force mains — two 18-inch lines and one 24-inch line — as the carrier pipe. “The ability to expedite the owner’s schedule by using the SBU-M and SBU-A simultaneously with a TBM was a big advantage for us,” continued Keefe.
Excavation with the 72-inch SBU-M began on Jan. 3, 2012, from a 25-foot deep launch pit. Crews encountered an unexpectedly long drive of hard clays about 15 feet into the bore, but were able to keep mining through the clays by adding water through the cutterhead. “We started with a vacuum assist for spoil removal, but when we got into the clay right away, we had better success when we stopped and switched out to the auger,” said Keefe.
The L.J.Keefe crew celebrates the successful completion of a 395-foot highway crossing to nearly exact line and grade.
“The main challenge while in the clays was in getting that softer ground material out without contaminating the cutting discs. We not only added water through the cutterhead, but also to the casing itself, up in front, to make sure the material kept coming through,” said Steve Lilo, operator/foreman of the SBU-M for L.J. Keefe.
Using added water, crews were able to maintain advance rates of 20 feet per day in the clays. Ultimately the machine excavated 200 to 240 feet of clays, and then hit solid rock for the final 150 to 170-feet of the run. Rates increased while in the rock, to about 30 feet per day in one, nine to 10 hour shift.
One of the biggest advantages of the Robbins SBU-M, as mentioned by the contractor, is in its ability for real-time alignment control through articulation cylinders and laser guidance. “We were within ¾-inch to an inch of line and grade the entire time and there was very little drift. I’m used to steering articulated machines, because we use a lot of TBMs. In the softer ground, the weight of the casing helps with control. Keeping on line and grade was easy, particularly when we got into the rock,” said Lilo.
The SBU-M broke through into a receiving pit on Feb. 14. “The SBU-M finished within its tolerances, with almost no deviation whatsoever, even going through the mixed face ground,” said Keefe.
Undercutting the Mississippi
At the same time as the highway bore, two SBU-A operations were ongoing 30 to 35 feet beneath a tributary of the Mississippi River. The 60-inch and 42-inch SBU-As, launched in November and December of 2011, utilized two 60-inch diameter ABMs to excavate hard rock over 10,000 psi.
“We had some challenges with the first crossing, because we had some tight tolerances to match the invert on the receiving side — it had to be a 0.16 slope. We had to do quite a bit of work to correct grade as we were tunneling across. We pulled the casing two or three times to make sure alignment was accurate, and were able to match it to within an inch and a half to two inches of design elevation,” said Keefe.
Scott Dixon, operator/foreman of the SBU-A for L.J. Keefe, elaborated on the line and grade process: “We were in hard rock with a lot of fractures in it, but it was manageable. Line was very good, but the grade we had to play around with. The 60-inch went fairly well, but with the 42-inch SBU-A we fought a little. We pulled back the casing and adjusted it. We did have a water level earlier on, but we lost it in about 100 feet because of the hard rock.”
Despite the challenges, Dixon was able to average 20 feet per day with the machines, and as much as 40 feet per day on the 60-inch bore in nine to 10 hour shifts.
“These are the longest crossings I have done with the SBU-A. There tends to be a little torque buildup on the augers at long lengths, so you need to have very good augers when you are doing it. Other than that, the SBUs work great for rock. When we used the old style heads with bullet teeth, every 40 feet you had to pull the head out, change the teeth, and still the wing cutters would wear down even more. That’s the nice thing about the SBU — you put it in the ground, it starts boring, and it keeps going,” said Dixon.
The city of Clinton Contract B Force Main will provide improved wastewater capacity for three Iowa communities.
Both SBU-A bores were completed within the project schedule and within line and grade specifications. The 60-inch bore wrapped up on Dec. 20, 2011, while the 42-inch bore broke through on Feb. 10, 2012.
Overall, L.J. Keefe and the companies involved were pleased with the crossing construction, citing both quality equipment and an experienced work crew. “It’s dedicated employees like my superintendent Frank Keane, with 30 years of experience, that ensured a successful outcome for this project. We didn’t find any production drop off as the bores progressed,” said Keefe.
The contractor also made use of technical assistance provided during SBU-M startup and throughout the bore. Field Service Consultant for Robbins, Scott Fisher, came to the site to advise on aspects of machine operation.
Keefe says the company has more plans to use SBUs on projects in the area and throughout the Midwest: “The biggest benefit is in being able to mold our current technologies with SBUs, using them in conjunction with ABMs, or in conjunction with our existing tunneling equipment. We can use our existing equipment with the specialized Robbins equipment to lower costs and shorten project schedules.”
FOR MORE INFO:
L.J. Keefe Inc. (847) 577-7715 http://ljkeefeco.com/
Robbins, (440) 248-3303, www.therobbinscompany.com
Merryman Excavation, (815) 337-1700, http://merrymanexcavation.com
How Small Boring Units Work
The Robbins SBU-A is a type of hard rock and mixed ground cutting head mounted with disc cutters and used in conjunction with an auger boring machine (ABM). The SBU-A, available in diameters from 24 to 72 inches, consists of a circular cutterhead mounted with single disc cutters capable of excavating rock from 4,000 to over 25,000 psi. For excavation, the SBU-A is welded to the lead steel casing. The ABM provides both torque and thrust to the cutting head, while a full-face auger is used for spoil removal.
In hard rock, disc cutters penetrate the rock face and create a “crush zone” through which fractures propagate. Material is then chipped from the face into openings in the cutterhead called muck buckets, which transfer the material to the auger. In mixed geology operation of the machine is the same, though the cutterhead is fitted with a combination of tungsten carbide insert cutters, disc cutters and drag bits to excavate the ground.
The Robbins SBU-M operates similarly to the SBU-A. It is designed as a manned entry, hard rock boring machine for use on both long utility installations (300 feet and over, depending on geology) and crossings with specific line and grade requirements.
At machine launch, the SBU-M is bolted to the lead casing and a small invert auger inside the casing provides spoil removal. An in-shield motor and drive train provide torque to the cutterhead, while forward thrust is provided by an ABM or pipe jacking unit through the casing.
The machine can be steered throughout the drive from an operator’s console inside the rear shield. Control of line and grade is made possible through articulation cylinders and adjustable stabilizer pads, while a laser targeting system provides accurate monitoring of the machine’s position.
Comments