July 2012, Vol. 67, No. 7
Features
Record Jacking Project In San Antonio
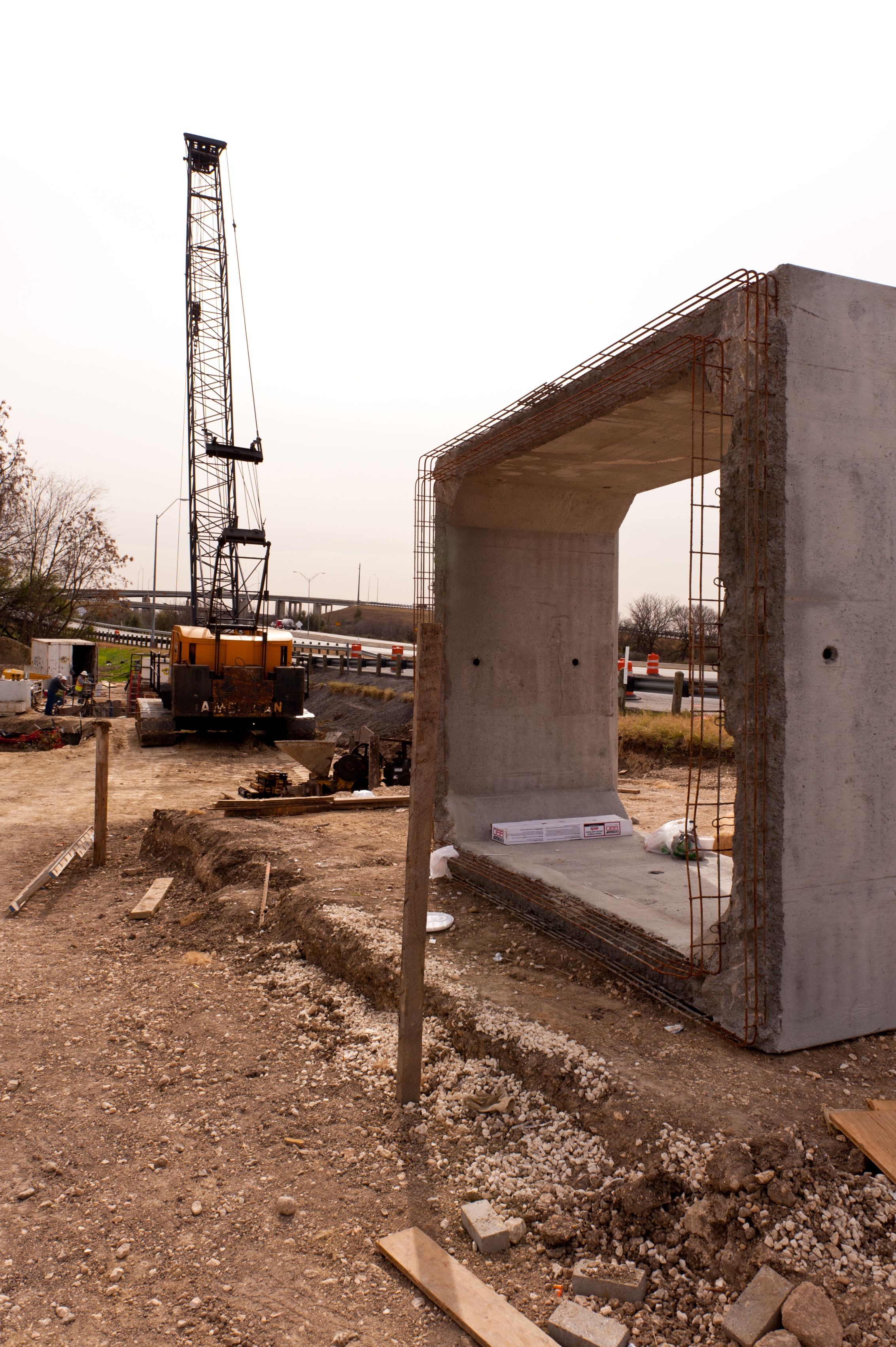
Culverts are essential components of highway drainage systems, carrying water beneath roadway surfaces to prevent flooding and erosion from washing away supporting soils.
In many situations, various methods of trenchless construction can rehabilitate failing culverts and installing new culvert pipes prevents making a deep excavation across a roadway, an option usually considered unacceptable because of the disruption of traffic it would cause.
However, rehabilitation methods won’t work in all situations and conventional trenchless replacement methods have limits to the size of culverts that can be installed.
The city of San Antonio faced such a situation when two, nine-foot-square concrete box culverts under Interstate 37 southeast of downtown were determined to be undersized and high velocities coming from them were causing erosion. The two existing culverts would be unable to accommodate a 100-year rain event.
The solution was to install a new 294-foot-long, 11-by-9-foot box culvert by jacking 49, 6-foot-long, 11-by-9-foot reinforced concrete boxes, one at a time, through a 12 by 24-foot shaft, 19-feet deep at flow line beneath the highway.
Making a deep excavation across a busy interstate highway obviously was not an option for installing the new culvert, and the jacking method selected was used because it minimized impact on traffic during construction. The new culvert is adjacent to the existing culverts.
The project owner was the city of San Antonio with funding provided by a city bond program administered by the Capital Improvements Management Services Department (CIMS). Anibal Gutierrez, P.E., was CIMS project manager. The firm Fernandez Frazer White & Associates was project engineer. The contractor was Boring & Tunneling Company of America (BorTunCo).
Shaft construction
The project began with constructing the shaft. During planning, both the city of San Antonio and BorTunCo conducted geotech coring to determine the soil conditions on the site, said Dennis Ritchards, BorTunCo tunneling division manager.
“Unfortunately,” he added, “the results did not represent the actual subsurface content which was 90 percent rock and sandstone.
“The shaft was located on the downstream end of the pre-existing 9 foot box culverts due north of the new box culvert location,” he continued. “The northeast rear corner of the shaft fell within inches of an eroded river bank, further complicating shaft construction, forcing us to re-position the front of the shaft within inches of the access ramp to Interstate 37 north. In order to accommodate the diameter of the boxes, the width was increased to 18-feet wide by 24-foot in length. The overall shaft construction was completed in approximately five days; this included the jacking setup used to move the massive boxes underground. Spoil from the shaft was distributed around the job site for removal at a later date.”
The size and weight of the boxes (13-foot outside diameter, each weighing approximately 50,000 pounds) mandated the use of a 100-plus ton crane. Logistically, because of the geographical location, delivery of the box culverts was restricted to between 9 a.m. and 4 p.m. Each box had to be transported individually due to size and weight by the manufacturer from a plant located near Dallas.
Next came jacking the boxes in place. The process is quite simple, said Ritchards. Four 500-ton Rogers jacks, operating in unison, were powered by a proprietary hydraulic system. They moved the huge boxes through the shaft. A laser provided accurate monitoring of the line and grade of the string of boxes.
“Each individual box was jacked inline the total distance of 294 linear feet of the shaft, one at a time,” said Ritchards. “We did it the old-fashioned way — hand mining via pneumatic clay shovels. Once each box exited the shaft, another was placed directly behind and pushed through. We anticipated moving approximately one box per shift. Double shifting would come later when jacking pressure became a concern. However, the reality became approximately one to three foot per shift due to the rocky subsurface conditions.”
Massive weight
With each box weighing approximately 50,000 pounds, the entire string weighed in at about 2,450,000 pounds or 1,224 tons of reinforced concrete and steel.
A primary concern during the jacking was the location and angle in which the rear of the shaft came in contact with a river bank and created a difficult situation with regard to space and design. There was concern about blowing out the back of the shaft from jacking pressures.
“Subsequently, the back of the shaft was reinforced with one-inch thick ‘H’ beams, 1.5-inch limestone and 8 by 20-foot steel road plates,” Ritchards said. “This combination proved sound as jacking pressures reached 5,000 psi by the end of the project and there was no deflection in the backstop whatsoever.”
“When all were in place,” said Ritchards, “the string was only off by one-half inch.”
Installation of the new 11 by 9-foot box culvert was completed in January 2012, five months after work on the shaft was initiated. In addition to jacking the new culvert boxes, the project included installation of new concrete riprap for the drainage channel from Goliad Road to Interstate 37.
Ritchards said sizes of the boxes and length of the string set this project apart from others.
“Historically,” he said, “a string of boxes this diameter is much shorter, usually less than 100 feet. To my knowledge, no one has ever jacked a sting this size for a distance of 294 feet.”
Ritchards cited one man as instrumental in the successful completion of the project.
“BorTunCo Tunneling Superintendent Larry Robinson Sr. has more than 35 years of experience with hand mining operation,” said Ritchards. “His ability to plan and execute this monumental task was a direct reflection of his knowledge and determination to ensure this project was installed according to the spec. Larry never wavered in spite of the extenuating circumstances incurred that included ground conditions, weather, holidays and the work location and space constraints, all of which impacted the project at various times throughout construction.”
Founded in 1948, Boring & Tunneling Company of America first attracted the attention of the underground construction industry with its patented method of slurry boring. Over the years, BorTunCo has adopted other technologies as they developed and today offers services that include boring, tunneling, shaft construction, horizontal drilling, and construction consulting and management. The company is based in Houston, TX. The company’s founder, Gilbert Turner, held a long-time patent on slurry bore technology. In 2011, BorTunCo was acquired by Magnum Tunneling but still operates under the BorTunCo name.
FOR MORE INFORMATION:
BorTunCo, (832) 300-3333, www.BorTunCo.com
Comments