September 2011, Vol. 66 No. 9
Features
Threading The Needle: Precision Boring Required For Project At Underground LPG Storage Facility
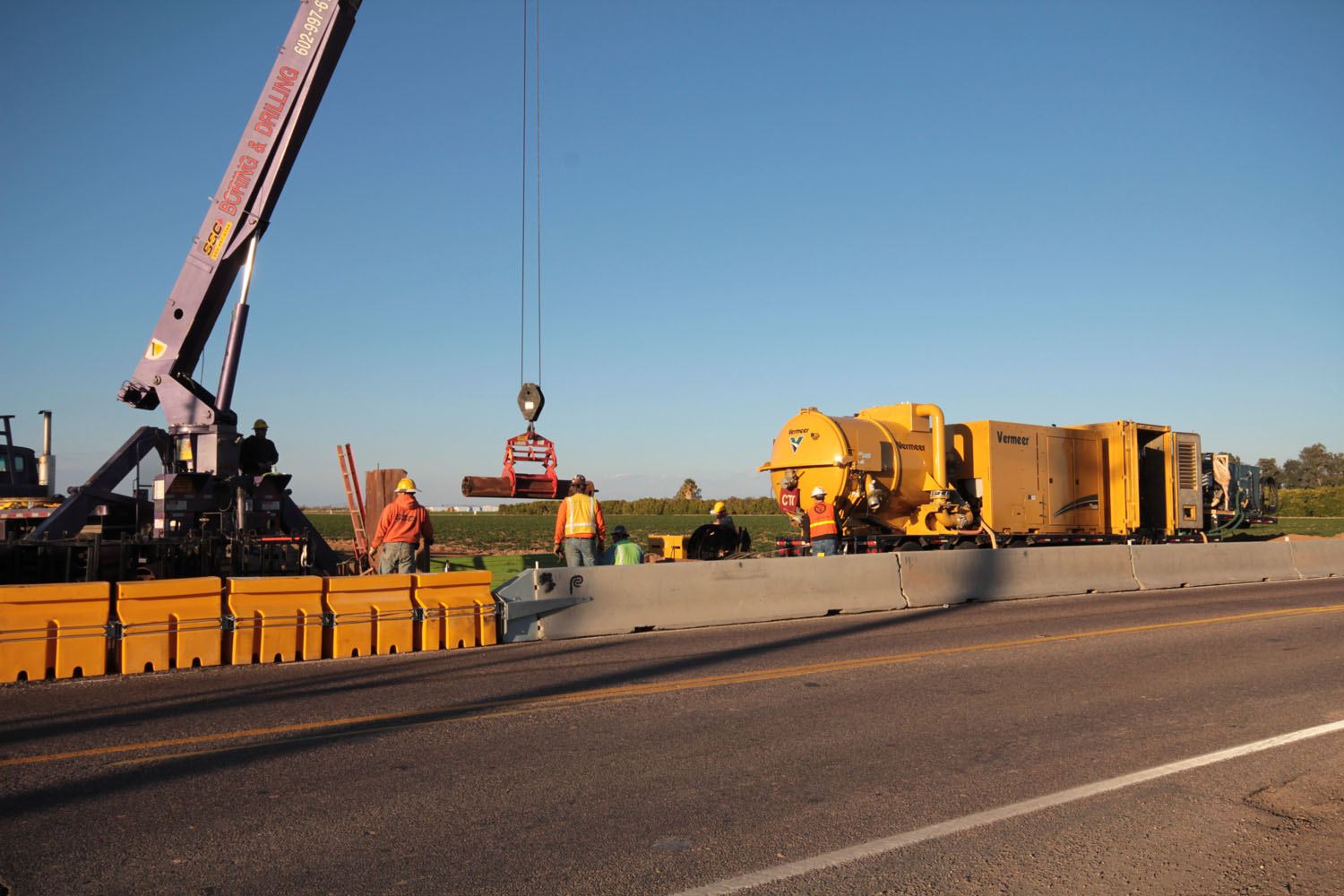
During the more than 40 years since Arvid Veidmark Jr. founded Specialized Services Company (SSC) a leading trenchless installation contractor based in Phoenix — members of the Veidmark family have celebrated many accomplishments. They now have another success story to attach to the list of firsts on the company’s well-documented resume.
Although some of the faces have changed at SSC since 1969, the vision of the founding Veidmark — to provide a valuable service to the community — is still very much intact today, evidenced by the vision and dedication of wife Marcia, along with sons Arvid III, Aaron and Abe. SSCs recognition, and much of the company’s success for that matter, can be attributed to a close-knit family committed to embracing new and innovative underground technologies. Most recently, a laser-guided boring system was used to complete a delicate trenchless installation for Plains Midstream Canada.
Faster fill flow
Project owner Plains Midstream Canada, headquartered in Houston, is involved in crude oil transportation, gathering, marketing, terminals and storage as well as marketing and storage of liquefied petroleum gas (LPG). Plains Midstream selected SSC to install sleeves at three locations to accommodate a new line being added to the underground infrastructure used to load and unload LPG from tankers and railcars at the Bumstead facility, an underground LPG storage cavern located along the Interstate 10 corridor between Phoenix and Los Angeles.
Situated some 2,000 feet underground at the juncture of a major rail line and tanker truck transit point, the 133-million gallon facility is composed of three underground salt-dome storage caverns, a 24-car rail rack and three truck racks on the surface with the capability to unload six trucks simultaneously. To expedite the loading and unloading of tankers and railcars more quickly, Plains Midstream installed an additional 6-inch high-pressure gas line.
The component of the project awarded to SSC involved installing six separate 12-inch steel casing sleeves with a 3/8-inch wall thickness, at three separate locations. Abe Veidmark, vice president of the auger division for SSC, explains the challenges faced and the decision to use an innovative approach for completing these intricate bores.
“It wasn’t so much the ground conditions or pitch, but rather the pinpoint accuracy of the line grade we needed to achieve for us to succeed,” Abe says. “When installing smaller material with standard auger boring, it is nearly impossible to steer with the accuracy required for all of these bores. In all likelihood, there would have been a good deal of drifting [with auger boring], something inherent with this method for shorter distances. All of these bores were less than 200 feet.”
Precision-fine boring
After reviewing the specifications and intricacies they would face at each of the three sites, Arvid Veidmark, executive vice president and senior estimator for SSC, recommended an innovative, alternative approach. Months prior, Arvid attended a demonstration facilitated by trenchless experts with Vermeer highlighting a new laser-guided boring system that had the capability to complete smaller-diameter bores with pinpoint accuracy and strict on-grade precision. Although designed primarily for sewer and water projects, the two felt the AXIS guided boring system was just the answer they were looking for.
AXIS is a pit-launched trenchless installation method designed to achieve precise, on-grade accuracy while eliminating some of the difficult steps associated with other installation techniques. The system was designed to install 8- to 18-inch pipe at lengths up to 350 feet though larger diameter and longer length bores have been completed. AXIS is also capable of maintaining the strict tolerance and accuracy required for the types of installations facing SSC as specified in the Plains Midstream job. The system requires an entry pit where the core of the AXIS system is placed, composed of the rack, drill casings, drill head and pipe laser. Located outside the launch pit is the vacuum power unit, vacuum tank and the rack power unit.
Once lowered into the pit, the drill head, with self-contained camera connected to a monitor on the operator console, projects the laser beam on the target. With the camera viewing the laser beam on the target, the operator can accurately monitor the target grade and make adjustments, ever so slightly, along the bore path, if the drill head begins to move off course. Rotation and thrust from the carriage assembly resumes as the first drill casing is pushed through the hole, and the process is repeated with subsequent sections of drill casing until the drill head reaches the exit pit.
“The only way we would have attempted it using a jack and bore approach would have been to upsize to a 30-inch diameter bore casing, then steer the 30-inch casing back through,” Abe says. “Accuracy was of paramount importance. It was also such a small footprint that it would have made it difficult to initially set up one of our big rigs there.”
Railroads, right-of-ways and a rose garden
Two of the three installations involved railroad crossings that required strict adherence to very narrow right-of-way tolerances established by the railroad. The first site required SSC to complete two 148-foot bores at approximately 10- feet deep, while the third location — two 180-foot shots — called for crossing beneath seven separate sets of tracks, to the terminal site where natural gas is offloaded from the transporting railcars. Positioned close by was a large underground fiber optic cable that limited the position and excavation depth of the bore pit.
“The location of the reception pit was sort of questionable, but we really didn’t have much leeway because of where the fiber optic cable was positioned,” Abe explains. “This was a situation that reinforced the need for pinpoint accuracy — something that would have been difficult to accomplish using traditional auger boring. We had to hit the target pretty much dead on, stopping within inches short of the cable.”
Although the two railroad crossings presented the SSC crew with significant accuracy challenges, it was the second leg of this three-fold installation project that the Veidmark brothers, despite their extensive experience in trenchless construction, had not previously encountered – a one-of-a-kind rose garden.
“When we surveyed the second site to identify where the entry and exit pits should be dug, we discovered an irrigation canal that supplied water to this immense rose garden,” Abe says. “The plan specified two bores within relative close proximity parallel to the canal. We came to find out this was no ordinary rose garden, but rather the only one in the world where this special variety of roses are grown. This itty-bitty plot contained tens of millions of dollars-worth of these roses. If we would have tried the traditional auger bore approach, there’s a good chance we could have drifted right into this multi-million-dollar garden of roses.”
Abe reiterates the need for precision, comparing the boring process and subsequent installation at each of the three sites to that of a double-barrel shotgun.
“We had to complete two bores, side by side, within two inches and maintain that same accuracy for 200 feet,” Abe says. “Think of it as a shotgun with two 12-inch barrels extending 200 feet that we needed to keep at least two feet from the irrigation canal, the lifeline to a multi-million-dollar rose garden. I was very thankful to have the accuracy of the AXIS system.”
Equipment staging and footprint was also a consideration for the Veidmark crew as they reviewed the options facing them to select entry and exit pit locations at each of the three sites. According to Abe, aside from the additional space needed to stage the various components of the AXIS system (compared to auger boring or horizontal directional drilling), the area required for excavating staging and receiving pits is minimal.
After determining locations and excavating the launch and exit pit, the SSC crew shored up the walls with metal bracing, set the laser to the desired grade and depth and lowered the leveling frame and rack assembly into the launch pit. The first 6.5-foot drill casing was then placed in the rack carriage and drilling was underway.
“It’s a relatively quick process once everything is in place,” Abe says. “Ground conditions were ideal so that wasn’t a factor. We completed the first two bores without any problems and the second in less than four hours, which is really good. We popped through precisely on target in the exit pit, then disconnected the bit, attached the pulling head and pulled the casing back through.”
Vacuum excavation
Abe explains that the vacuum excavation unit utilized by the AXIS system requires a fair amount of water to facilitate the removal of spoil. However, he goes on to say that the vacuum system ultimately enhances production rates because the need to suspend drilling operations to manually handle spoil within the launch pit is eliminated. The system also helps provide a cleaner pit environment.
Installing the casing was a breeze at two of the three locations — bores of 200 feet and 180 feet respectively — as the SSC crew was able to weld the entire length of casing segments together, allowing them to pull the material back through the bore path in one continuous shot. This was accomplished by digging a ditch beyond the exit pit and placing the entire expanse of material within, a strategy that wasn’t possible at the final location due to the position of the large fiber optic cable.
“At the third location, since the fiber [cable] was in direct line with the bore path, we were limited to pulling back the steel casing in increments of 10 feet,” Abe says. “This required us to weld each segment together in the pit, repeating the process until the entire 150-foot shot was complete. We were also required to pressure test each weld, which slowed the process down quite a bit.”
With the exception of a few minor learning-curve glitches that Veidmark explains were quickly rectified by the AXIS system experts at Vermeer, the six bores were completed on-target, on-line and on-grade.
“The capability to maintain the target so precisely and the confidence to know that you will hit your end target exactly where intended is a huge advantage for the AXIS system,” Abe says. “The cost is another huge advantage.”
FOR MORE INFO:
Specialized Services Company, 602-997-6164, http://sscboring.com
Vermeer Corp., (888) 837-6337, www.vermeer.com
Comments