October 2011, Vol. 66 No. 10
Features
What Is Necessary For Manhole Rehabilitation Success? Correct Application, Use Of Manhole Rehab Technologies
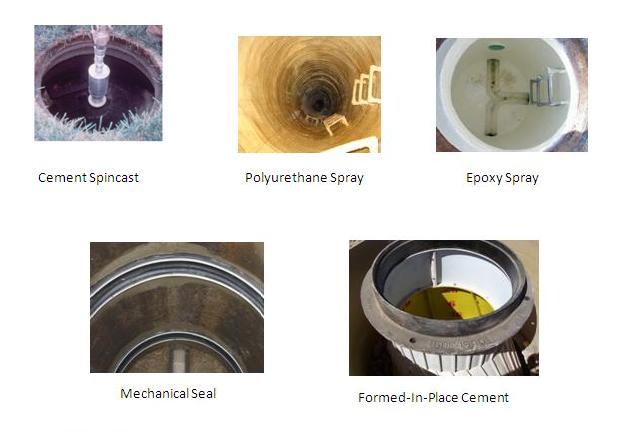
Editor’s Note: This is the second of three articles focusing on the current state of manholes, manhole assessment and manhole rehabilitation. Part three will be published in the November edition of Underground Construction.
Manholes consist of multiple components and are made of different materials, each serving a different purpose but contributing to the complete manhole structure. Each component typically has its own set of defects and deterioration mechanisms. Each component therefore has specific repair or renewal requirements due to the various depths at which manhole components are installed and the materials used for construction.
The most common materials used to construct manholes fall into two major categories; bricks and mortar or precast concrete. Newer materials are being innovatively used in manhole construction today, such as high density polyethylene, polymer concrete and fiberglass, but these are not the traditional materials that will be renovated in older collection systems. Other types of structural materials have been used in different regions, such as segmental block, but these generally are more limited in their use or confined to specific collection systems where that material or approach was incorporated in the system. Manholes are also access points for the wastewater collection system, so each is typically finished with a cast iron frame and cover.
There may be dimensional differences between manholes constructed of brick laid in the field versus factory precast concrete manholes. Brick manholes tend to be more conical in shape from the manhole rim to invert and more slender than precast concrete manholes. The brick manhole wall is typically thicker at the base than a comparable precast manhole in order to support the traffic and loads necessary for deeper manholes. Despite the differences between various manhole materials, the terminology for describing each manhole component is consistent.
Shallow manholes located at the surface or within four feet of the ground surface can be refurbished or replaced at a relatively low expense since they are readily accessible. Manholes deeper than four feet below grade are more often repaired or renewed as opposed to being replaced.
There are many technologies available for rehabilitating the different components of existing manhole structures without the need for excavation and replacement. These can include cementitious, polymer, cured-in-place, panel, grouting, mechanical and more, for both internal and external coating, lining and sealing techniques.
Due to the various types of materials used to construct a manhole, it is not uncommon, for a customer to require that multiple rehabilitation techniques be applied to properly repair or renew an existing manhole.
It is important to understand that no single product fits all rehabilitation needs. Not every product is compatible with another, different manhole products require specific structure preparation requirements, and adhesion characteristics will vary for different products. Also, quality assurance is a must, and testing should be performed for all products.
The questions that arise frequently, from customers, are: which system works best under given conditions and how long will it last? Most products and technology systems have verifiable applications and longevity histories and have been proven effective over time for rehabilitating manholes. When the results do not meet expectations, customer confidence, in manhole rehabilitation technologies and products can diminish. Was the wrong product installed or improperly applied? Was the structure prepared incorrectly for long-term product performance? Was the applicator properly trained? What should be changed to ensure long term performance?
The initial step in choosing the right technology is to identify all of the existing manhole defects and defining the extent of rehabilitation required to achieve the customer’s requirements. Is the application for structural reconstruction, for corrosion protection, to stop leakage from entering the system through the manhole components or a combination of all? Once the need is identified an evaluation of available technologies can be undertaken to determine which product will do the job at the most competitive cost.
Several industry professionals, provided input for this article, including William Shook of APM/Permaform, Lee Haessig of Cretex Specialty Products, Larry Kiest of LMK Enterprises, Chip Johnson of Sprayroq and Jane Warren of Warren Environmental.
A series of key question were asked of these industry professionals.
For what type of structures is your system best applicable?
Shook: Because manholes suffer from a variety of problems, we offer multiple solutions, including Permacast structural cement liner, Permaform no dig replacement system, Cor+Gard 100 percent solid epoxy coatings, Cor+Roq structural epoxy, Conshield additive to Permacast, Permaform CIPP liner, I&I Barrier plastic chimney liner, and Cor+Flex and Cor+Seal flexible urethane sealants.
Haessig: Our primary focus is on internal and external mechanical manhole frame chimney seals and internal manhole barrel joint seals, plus a wide variety of manhole related products including applied chimney seals, chemical grouts, exterior joint wraps, cover vent hole plugs, inflow dishes and lightweight plastic manhole grade adjustment rings.
Kiest: We furnish the universal, stretchable, one-size-fits-all CIPMH (cured-in-place manhole) system.
Johnson: Our core product is the structural polyurethane, SprayWall. We also offer two elastomeric polyurethanes, SprayShield Green I and SprayShield Green II for corrosion protection (non-structural).
Warren: One hundred percent solids, zero VOC structural high build epoxies which are applied with a patented solvent free spray system making the process much safer to use in confined spaces.
When products are selected it is important to understand how each product is applied and what level of surface preparation is required for the host structure. Product application is typically by hand spray, spin casting, liner insertion or hand applied.
The cleaning and preparation of the host structure, however, becomes one of the most important applicator work items. Existing manhole structures can exhibit defective conditions that will affect the installation and longevity of the product. Defects can include such categories as structural, maintenance, construction and miscellaneous. Defects such as water leakage must be temporarily stopped, partially missing walls may need to be structurally rebuilt, corroded or soft materials must be removed to underlying sound base material and corroded or broken components must be removed and in some cases replaced.
The level of cleaning and surface preparation becomes significantly more important when applying those products that are designed to bond to the existing manhole structure.
How important is structure preparation for your products? What preparation do you recommend?
Shook: Permacast cement liners are structural by themselves and they adhere well to existing masonry and concrete substrates after pressure washing to remove laitance and contaminates. Cor+Gard coatings adhere extremely well over our own Permacast cement liners which provide the structural value of a composite. Primers are used over new, precast concrete.
Haessig: Surface preparation is a very important part of the process in order to have a successful installation or application. The level of surface preparation for our chimney seal is dependent on the age, condition and type of construction used for any given manhole. Upper and lower sealing surfaces must be reasonably smooth, circular and free of any loose material or excessive voids. Surface preparation will generally require wire brushing the lower three inches of the manhole frame casing to remove any loose rust or scale. If the seal is to be installed in a brick manhole, the surface of the brick will require the use of a non-shrink, polymer modified repair mortar. On precast manholes, form offsets and any excess honeycombing in the area that the band will compress against should be repaired using the same non-shrink repair mortar to provide a uniform sealing surface on the manhole cone. If the manhole is a candidate for relining with a cementitious material, the surface area directly below the casting can be made vertical and circular by the cement applicator, which reduces or eliminates the need for additional surface preparation on the masonry.
Kiest: Surface preparation is key to allowing mechanical bonding of the thermo-set resins. All structure surfaces should be clean and free from debris. High pressure blasting, with grease dissolving additives are used to remove debris, fats, oils, and grease.
Johnson: As with all spray applied resin chemistries, a clean dry substrate is best. Generally this is done by high pressure power washing with water and/or degreasing agents, if needed. The wash should expose good, stable (i.e. no corrosion byproduct) substrate. Sometimes at this stage dry, hot air is blown into the structure to enhance drying.
Warren: Surface preparation is very important. High-pressure water blasting with a diluted solution of HCL and/or detergent, followed by correction of the surface pH is recommended for brick and concrete substrates.
One of the key properties of each coating and lining system, is the ability to chemically bond, mechanically bond or not bond at all to the existing structure. Both types of products are used in the industry to rehabilitate manholes.
Does your product bond to a host structure, or does it form a structure within a structure?
Shook: Cor+Gard, is a coating that adheres well to the properly prepared substrate. Permacast and Cor+Roc structurally reinforce the existing manhole to which it bonds. The Permaform system is a totally independent structure within the old one.
Haessig: Because our product is a mechanical compression type seal, it does not bond to the manhole at all and also does not provide any structural strength. The purpose of the chimney seal is to provide a flexible, watertight seal between the manhole frame casting and the top of the manhole cone or corbel to prevent inflow.
Kiest: Because our liner is thermo-set resin based, we have options for various resin systems, i.e. epoxy, polyester, vinylester and silicate. Polyester is the most user friendly resin and is the most economical. Although polyester resin may mechanically lock into cracks and voids, it does not chemically bond to the host structure. However, our epoxy system is designed to mechanically and chemically bond to the host structure and our inflation bladder provides constant pressure forcing the liquid resin against and into the structure walls providing a superior bond.
Johnson: All the Sprayroq products bond to properly-prepared substrate. In structural applications of SprayWall, we know we are getting adhesion but the ASTM 1216-07 design guide does not assume an adhesive bond to the substrate for its thickness calculation for either partial or full deterioration. Our adhesion capability gives further conservativeness to the design.
Warren: Our product forms a tenacious bond to both porous and non-porous substrates, usually resulting in the breaking of the concrete/brick, or glue on the dolly before the test is complete. We can apply to damp surfaces as well as dry.
One of the most important aspects of manhole rehabilitation is the testing and inspection performed during all phases of the application process. A performance based specification will typically contain specific language about quality assurance and testing of the installed product. Quality assurance requirements are usually expressed in measureable terms, and therefore should be measured by applying industry standard test procedures before the product is accepted by the customer. The specifications will define the end product or deliverable that is required by the contract documents based on inspection and test results. Testing during and after product installation may include dry and wet film thickness testing, holiday or spark testing, adhesion testing, pre-installation substrate testing as well as visual inspection of the structure before and after coating or lining application.
Have product failures occurred and, if so, what were the cause and remedies?
Shook: Failures can occur whenever proper preparation and/or application procedures are not followed. We strive to eliminate field problems by requiring certification training with annual updates so applicators demonstrate proven performance standards. In rare instances when defects are discovered, an investigation is made to discover the cause then defects are corrected and reports issued to eliminate recurrence. Our company has provided solutions since 1976 without a single failure to correct defects. No matter how rare or costly.
Haessig: While no material failures have ever occurred or been documented, leakage related failures have occurred. The cause of these leakage related failures is most often associated with improper surface preparation, not following recommended installation instructions, specifically, the lack of use of the supplied expansion band lubricant. Remedies for leakage related failures are as simple as removal of the seal and performing any necessary surface preparation or repairs and reinstalling the seal and bands making sure to use the expansion band lubricant.
Kiest: During the development of the CIPMH liner system, we did experience failures due to ruptured inflation bladders. Although the installer must take precautions not to puncture the inflation bladder during insertion into the manhole, we have developed a very robust bladder, and today failures are not common.
Johnson: The only cataloged failures have been in corrosion applications, 125 to 150 mils, with the failure due to improper substrate preparation. All Sprayroq products are hydrophobic and will have an adverse reaction if applied to a substrate that does not meet the proper moisture threshold. The reaction is immediate with the primary reaction being a vigorous outgassing resulting in a scaly, “popcorn” looking foam. Operators are trained to stop and find out why the substrate is not dry enough, and the remedy is to remove the improperly applied SprayWall, recheck the stoppage of the moisture, and reapply on to the newly prepared substrate. SprayWall, our structural polyurethane, has never had a latent structural failure — meaning, after proper ASTM design and proper application, no failure has ever been reported.
Warren: After curing, we use Elcometer testing for adhesion, ultrasonic testing to verify millage and Positestor testing, for pinholes.
When specifying a coating or a lining, it is important to implement post installation inspection and testing as well as performing inspections during or just before the maintenance period expires. Coatings and linings, when properly applied, will protect the host structure from further deterioration provided no defects exist that allow corrosive elements to penetrate behind the applied coating. If defects occur, the host structure will continue to corrode and in some cases the deterioration process accelerates significantly.
In applications, it is not uncommon to experience some minor defect formation in the installed product where a pin-hole remained undetected or coating was applied thinner than required. If the defect remains unrepaired it will, over time, continue to spread towards total product failure.
Maintenance inspection of coatings and linings is very important. A defect left unrepaired will spread and fail. A defect, repaired in a timely manner, will ensure that the product will perform for its expected life.
After completion, when should your installed product be re-inspected to verify that no potential defects will occur that will affect long-term performance of the product?
Shook: It is best to perform tests immediately upon completion. Follow up inspections should be made during routine maintenance of the manholes and following major storm events or similar harsh events which impact the sewer system.
Haessig: The recommended acceptance test is a live water test during or after installation of the seal.
Kiest: Inspection can occur at any time. We have inspected liners that have been in use for more than five years, and they show no change from the time of installation.
Johnson: Adhesion testing should be done four-to-six hours after application which is the time needed to reach complete cure. Sprayroq products cure similar to concrete, outside to inside.
Warren: One to five years. Our product has passed the California Redner test, CIGMAT in Houston, by the European IKT test and the Department of the Navy testing.
Coatings and linings are effective tools for rehabilitating manholes through trenchless means, without digging and replacing the entire structure. The selection and application of each system is important. The correct technology must be selected to provide the end results desired by the customer and the application must be performed by an experienced, trained and certified applicator. Specifications should be performance based and clearly spell out, in measurable terms, the quality that will be expected. Inspection and testing must be enforced to measure the quality of the installed product as required in the contract documents.
In November, the third installment of this series will discuss such topics as: How is a new product designed for a manhole? How is a product designed, using industry appropriate design equations? What does it mean when a product is termed structural versus non-structural or structurally enhanced? What testing should be performed to verify proper application? Should the level of applicator training be improved through advanced training, education and certification? Should third party inspection, by certified inspectors, become part of the technology or product application process?
Editor’s Note: Senior Editor Jeff Griffin contributed to this article.
FOR MORE INFORMATION:
NASSCO, (410) 486-3500, www.nassco.org
Comments