November 2011, Vol. 66 No. 11
Features
Direct Pipe Method Proves Comes To U.S.
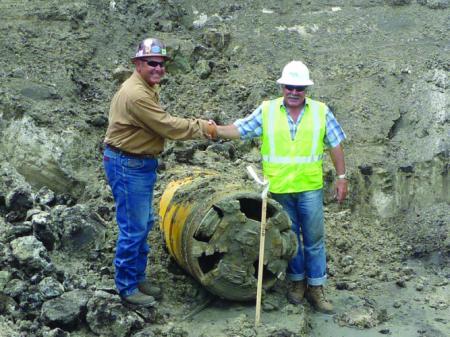
REM Directional successfully installed three underground pipelines using the Direct Pipe method for the first time in the United States. The systems was used on a Florida horizontal directional drilling project that installed a natural gas pipeline under a highway.
The project started with crews setting up a launch pad on a sod farm in Arcadia, FL, in preparation to install a 705‐foot, 30-inch diameter natural gas pipeline under Highway 70. This successful pioneer run was completed in just three days. During the installation, REM also implemented the use of a Pipe Thruster, which can apply an additional 500 metric tons of pushing and pulling power when used to aid HDD rigs.
Herrenknecht AG in Germany designed both the Direct Pipe method and Pipe Thruster equipment. Said Theo Hundertpfund, manager of after sales service for Herrenknecht AG, Utility Tunneling Division, “First and foremost we would like to thank REM Directional, Inc., who placed their trust in us. We know that it is only possible to set new milestones in technological developments when all parties involved work together to continue the story of innovation in mechanized tunneling with smart concepts and strong determination.”
Originally making its debut in September 2007, the Direct Pipe method was successfully tested at a crossing of the Rhine River near Worms, Germany. This method is comprised of two traditional drilling methods: microtunneling and HDD.
Known for being a rapid, single‐step process, Direct Pipe is more accurate than using traditional methods alone and is considered optimal for precise installations required for projects leading to oil and gas refineries and power plants.
Accuracy
The accuracy of this method is based on instrumentation and includes the use of a gyrocompass and hydrostatic water level to help guide the AVN machine and product pipe to their destination by monitoring vertical depths and horizontal deviations. This curve monitoring is conducted from an above ground drill cab, which allowed REM to monitor the bore closely and make necessary corrections to both vertical and horizontal paths to keep the machine and product pipe on target.
The microtunneling head of the machine also monitors the annular pressure at all times, which eliminates mud frac outs from rising to the surface. This operation too is conducted from the drill cab.
Another advantage is that the annular gap created with the Direct Pipe method is only one-to-two inches larger than the product pipe which allows the borehole to be much smaller than using conventional methods which reduces the risk for road collapse. It is also recognized for being able to maneuver around underground utility lines that may obstruct the path of the pipeline.
The Direct Pipe method was chosen for the Highway 70 site to allow REM Directional to cross under the roadway and five canals. To avoid breaching the canals and/or causing any disruption to this sensitive environment, they had to achieve minimum soil coverage of six feet from the bottom of the canal down to the top of the pipe.
The REM team successfully completed two additional bores on the West side of Florida. The purpose of these installations was to provide natural gas to a power plant to generate electricity for approximately one million households in each region. This particular installation required obtaining authorization from the Florida DOT to commence work. Since it was the inaugural installation, REM Directional went directly to the DOT, explained the Direct Pipe method, presented an informational DVD along with machine specifications and gained approval to proceed with the installation.
Perhaps one of the best advantages of using the Direct Pipe method is it only requires a minimal amount of room for set up on the launch side of the bore. In fact, the average space for set up of the launch pad is only a 6 feet x 20 feet x 80 feet sheet pile pit. Once the launch pad has been erected, the product pipe is set on rollers behind the launch pit. The Direct Pipe set-up results in using less manpower and equipment and causes less disruption to the environment. Regarding the first installation, Joel Colgrove, owner of REM Directional said, “It took a lot of thought process prior to the initial setup; however, once we implemented the method in the field, it went very well.
Advantages
Additional advantages of using the Direct Pipe method include the following: reduction in exposure to environmental hazards, elimination of road settlement, prevention of potential damage to any infrastructure and a reduction in the amount of stress applied to the product pipe during installation.
Throughout the bore, a maximum pressure pushed was only 70,000 lbs., which reduced stress on the equipment and pipe.
The Direct Pipe method was also used at the Highway 39 site in Plant City where an existing water main obstructed the prescribed bore path. At this location, REM was faced with the challenge of drilling under the 5-1/2‐foot water main, which was located on top of a two‐foot gravel bed. The method was successfully used with only a 6‐foot launch pad and without compromising the stability of the utility gravel bed. On the launch side, REM also had to drill parallel to an existing 30‐inch natural gas line. On the exit side, they ended up crossing under the same 30‐inch line.
If a conventional method had been used in this scenario, REM officials said they would have had to dig a pit up to 21‐feet deep, which would have posed a potential threat of road collapse, given the typically sandy soil conditions that are prevalent in Florida.
Also, clay material was encountered in the soil during this bore and drilling was drastically reduced to two-inches per minute. In an attempt to resolve this issue and speed up the process, REM used a water blaster and was able to increase the penetration rate to nearly double the typical speed. As this bore was being completed, the team used the next three days to demobilize the site and begin set up at the third bore site. This proactive approach allowed REM to streamline their resources effectively to coordinate multiple crews to save the owner time and money.
REM began their third bore in a Lutz, FL project that required drilling under existing power poles located at the center of the actual ditch line. The team was not required to utilize a method of transportation at this site, so adjacent roadways did not need to be shut down. The first challenge REM encountered at this site was setting bore calculations to go around an existing cemetery.
The site was also adjacent to a busy roadway and a local neighborhood. REM’s surveyor designed a proposed direct pipe profile, which included a compound curve of 10 degrees (3,200 feet) horizontal curve and 11 degrees vertical curve (3,200 feet). The deepest point of soil coverage was approximately 29 feet. The degree of this angle was designed to alleviate cutting beneath the cemetery. As a result, REM was able to successfully maneuver around this obstruction in addition to existing fiber optic lines.
Because of an existing parking lot and nearby veterinary clinic, the team had only a 10‐foot exit pit off an existing 30‐inch line, leaving a very small margin for error in the pipe arriving on target. Pipe segments were supplied in 40‐foot sections and were joined on site. In this scenario, a method such as HDD would not have been an option due to the lack of room on both sides of the bore. HDD requires construction of a pilot bore plus multiple hole opening in preparation for the product pipe installation.
More complications
As an extra complication, REM’s team encountered a solid rock mix of coral and limestone at 293 feet into this bore. Since the machine stopped cutting at that point, REM was faced with the challenge of pulling the machine back and replacing the cutting head with the AVN-800, a mixed soil cutting head that is specifically designed for rock.
The original head used for the two previous bores was the AVN‐600, a soft formation cutting head that is designed to be used to cut sand and shell. Due to local geological risks, REM also preferred this method for its ability to cut through virtually most types of soil while maintaining an accurate alignment with the intended course.
During the two hours it took the team to remove and replace the cutting head, the bore path was left open but it did not collapse. The team proceeded with drilling back through the original 293 feet and an additional 90 feet. The Direct Pipe method also kept REM from having to perform an open cut at two locations, which resulted in a cost savings for the owner. Even through this challenge, the team was able to speed up the drilling process efficiency by utilizing the Herrenknecht Pipe Thruster.
If needed, the pipe thruster applies up to 500 metric tons of additional pushing and pulling power and increases feed rates up to five meters per minute. Overall, REM found they only had to apply a maximum 100 tons of pushing force during the rock installation.
To supplement the use of the Pipe Thruster, REM Directional has recently designed a pre‐fabricated anchoring assembly to expedite the time it takes to set up a Direct Pipe bore site.
After three successful pipe installations using the Direct Pipe method, REM Directional officials say it is a cost effective, simple method of trenchless pipe installation.
REM Directional, Inc. is a privately owned, directional drilling company based in Boligee, AL. They have served the needs of the private and commercial sectors of the construction industry for over 19 years and are considered an innovative industry leader. To find out more information on the Direct Pipe or REM’s HDD operations, visit www.remdirectional.com.
FOR MORE INFO:
REM Directional Inc., (205) 336-9919, www.remdirectional.com
Directpipe Herrenknecht, directpipe(at)herrenknecht.de, www.herrenknecht.com
Comments