June 2011 Vol. 66 No. 6
Features
Taking Water Pipe HDD To Extremes
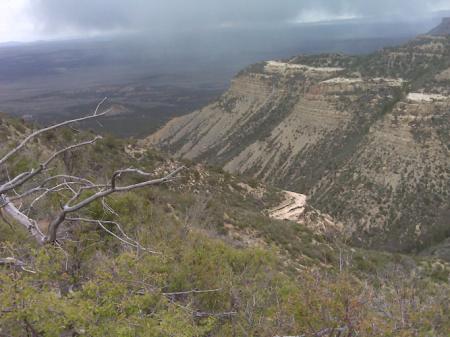
Mesa Verde National Park is located in the relatively isolated southwestern corner of Colorado, near Durango. More than 1,000 years ago, the area was home to Pueblo-dwelling people, and the park contains more than 4,000 archeological sites — including 600 cliff dwellings — which are among the most notable and best preserved in the United States.
The terrain in Mesa Verde (“green table” in Spanish) is dominated by rugged ridges and valleys with elevations ranging from about 6,100 to 8,400 feet.
In these difficult conditions, Laney Directional Drilling installed two horizontal directional drilling (HDD) segments of six-inch-diameter stainless steel pipe to take water to a one million gallon storage tank atop Navajo Hill. The water source is Jackson Lake several miles away. Water feeds from the lake into a treatment plant before being pumped to the storage tank.
The two Laney bores were made to replace a 40-year-old pipe attached to the side of the escarpment, a practice that is no longer permitted for environmental reasons. Each bore required extreme elevation changes and one had a sharp side bend, said Grady Bell, Laney vice president of business development.
The project owner was the U.S. Park Service of the Department of the Interior. The primary contractor was Triad Western Construction, Cortez, CO. The main crews welded, tested and assisted Laney with the difficult task of laying out a mile of steel pipe in very restricted right-of-way. Triad Western also shared with Laney personnel its knowledge of local site conditions.
The point where the new pipe was to connect to the pipe bringing water from the treatment plant was just inside the park’s boundary with no right-of-way available to set up the big drill rig to launch a bore. Therefore, it was necessary put the drill unit up on the mesa, drill down hill and exit at the connection point. The drill pad was about 50 feet off the main park road. When that bore was completed, the drill unit would be turned on the pad to bore further up to the storage tank.
Slow go
“Moving the drill rig and support equipment to the set-up site was difficult because the road to the set-up location ran though on-going drainage construction, and the two-lane road was closed to one lane in some areas because of resurfacing,” said Bell.
Travel time for getting equipment and personnel from the park’s entrance to the launch site was about two hours, depending on delays, and a 15 mph speed limit that was enforced.
“Extreme elevation changes set this project apart from other projects,” Bell continued. “The first bore dropped 1,500 feet from starting to exit point. That is the biggest elevation change we have ever encountered on a conventional directional drilling installation. In addition to elevation changes, the second bore had a sharp right turn and multiple direction changes.”
Bell said the park service had been considering ways to replace the old pipe for some time, and there had been discussions about whether the work could be done by directional drilling. One plan was to drill a portion of the route and use open-cut construction for another segment. Laney devoted several months planning and engineering to the project.
The HDD unit used was a Laney-manufactured LDD 753 powered by dual Caterpillar diesel engines, each developing 550 horsepower. The machine produces 683,000 pounds of pullback. The fluid system was a Laney designed and built Dragon tank with M-I Swaco shakers.
The first bore was 5,244 feet from the top down to the exit point at a grade that reach 45 degrees in some places. It followed the path of the park’s main road which led up to the drill unit’s location. The pilot hole was drilled with a 9 7/8-inch roller cone TCI bit and six-inch mud motor rented from J.T. Miller Inc. A Laney owned and operated Tensteer wireline system guidance system and rented SlimDril Drillguide GST gyroscopic tool were used to guide the bore.
“Environmental restrictions prohibited us from clearing any land in the park, and there were areas where we were unable to layout a True Tracker grid for the wireline system,” Bell said. “In those situations, we used gyroscopic guidance.”
The pilot hose was completed in approximately six weeks through interbedded layers of sandstone, claystone and shale. The pilot hole was completed in approximately six weeks.
Restrictions
Laying out and welding the six-inch stainless steel pipe in preparation for pullback was a challenge for Triad personnel.
“Pipe stringing and welding was restricted to a winding dirt trail and only minimal disturbance of the terrain was allowed,” said Bell. “The job required several weeks. As the string was laid out, temperature changes would actually move the pipe when it heated and expanded a problem because there was so little space. When the pipe cooled, it would contract.”
Prior to pullback, the pilot hole was reamed to a 17 1/2-inch hole with a TCI hole opener and then swabbed to ensure the hole quality.
Bell said the drill rig was then turned about 45 degrees for the start of the second crossing which proceeded to bore upward to the storage tank, following the path of the main park road part of the way. The second bore was 4,394 feet long with a 600-foot upward elevation changing to a 76-degree side bend throughout the entire crossing.
“We could not shoot straight to the tank because of sharp drop-offs on the sides of the old road,” Bell explained. “In addition to the sharp turn, there were multiple side and up-and-down changes. It was a very difficult installation.”
Soil conditions were similar to those on the first bore. Average depth was 70 feet. The same size mud motor, drill bit and hole opener were used as on the first bore.
“The waterline stringing and welding area was limited to less than 1,000 feet until a few days before pull back, so the pipe was welded in several sections then pulled out to its full length just prior to installation,” Bell said. “This layout area had multiple “S” curves and elevation changes of over 120 feet. It was extremely challenging.”
The bore was completed in three weeks. With logistical issues to deal with, pipe pullback took two days.
Limited excavation was required at exit points of the two bores to connect the two installations at the top of the mesa. Two large concrete thrust blocks were constructed at each end of both installations to stabilize the pipe, and the first 200 feet of each end of the pipes were grouted.
From start to finish, the project was completed in about three months, with winter snow falling near the end of construction.
Challenges met
In spite of the complexity of both installations, along with terrain conditions, and limits on disturbing the park land, Bell said the project essentially went as planned. He praised Laney personnel for their performance and Laney Project Superintendent Kyle Orum.
“We did have several frac outs — something park service people never want to see,” Bell said. “Some we were able to access and address, on others, the fluid simply dissipated. The park service was very good to work with, but we had several levels of government administrators and environmentalists concerned about pollution and damage to the land and plant life, and naturalists who were looking out for the animals.”
Based in Humble, TX, Laney Directional Drilling has HDD capabilities to install pipe in diameters of four to 60 inches to distances of more than 7,000 feet. Over the years, Laney crews have earned the reputation of being able to complete long bores to install large-diameter pipes in extremely difficult conditions.
Laney designs and builds its own directional drilling equipment, and currently operates 12 drill units ranging in size from 300,000 to 1.7 million pounds of pullback. The 1.7-million pound machine, powered by two 1,000-horsepower Caterpillar engines, is believed to be the largest HDD rig in existence.
Laney has all the necessary equipment to support its HDD equipment, including fluid recovery systems, and trucks and trailers to transport the large machines.
FOR MORE INFO:
Laney Directional Drilling, (281) 540-6615, www.laneydrilling.com
Tensteer LLC, (512) 670-0447, www.tensteer.com
M-I Swaco, (832) 295-2652, www.miswaco.com
J T Miller, Inc., (936) 447-2929, www.jtmillerinc.com
SlimDril International, (281) 391-5800, www.slimdril.com
Comments