June 2011 Vol. 66 No. 6
Features
Rigonomics Supplement: Tips From A Rock Drilling Specialist
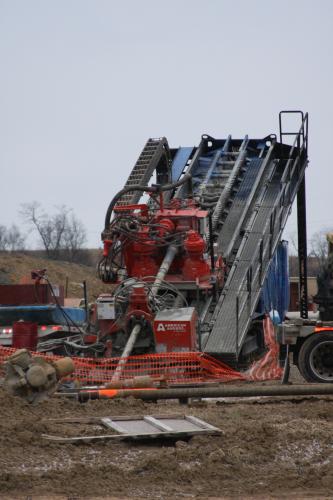
H&H Enterprises is a HDD contractor specializing in rock with 15 years of experience working primarily in the Northeastern United States.
H&H operates three American Augers HDD units ranging in size from 60,000 to 440,000 pounds of pullback and all required support equipment, including mud pumps, mud recycling systems, vacuum truck, crane trucks, pipe layers, excavators with pipe-handling equipment and haul trucks.
A recent project employed two drills: a 60,000-pound drill unit and a 220,000-pound model to drill 1,200 foot holes. One was for a 16-inch HDPE water line and the other a 12-inch steel gas line. Rock hardness was 25,000 psi. A 4 3/4-inch Adtech mud motor was used with 6-inch sealed bearing tri-cone bit and multiple Sharewell low torque hole openers in sizes ranging from 14 to 30 inches.
The first step in a successful HDD project is understanding its specifications in order to prepare a realistic bid, especially when rock is a factor.
“Standard industry bidding practices and procedures apply to all projects, but rock drilling takes significantly more time to correctly bid compared to projects in dirt,” observes Jason Hockran, H&H vice president/owner. “On rock projects, it is crucial to recycle drilling fluids and to include the costs of fluid recovery and disposal. This applies to most HDD projects, but usually is more costly on rock projects.”
Hockran emphasized that every successful HDD project should begin with planning, especially those in rock.
“The busy rush of almost every directional drilling project may cause contractors to overlook basic planning steps,” said Hockran. “Taking the time to think through the steps for the HDD process, utilizing the capabilities of your equipment and knowledge of your crews, and focusing on safety all lead to an effective project plan.”
Client communications
Because many customers are not familiar with HDD in general and less with HDD in rock, Hockran said communicating with the customer regarding the specifics and limitations of HDD rock drilling is important.
“Typically rock projects require longer drill lengths than dirt, so communicating about scheduling and drill path limitations are a key to establishing and meeting expectations for directional drilling in rock,” he said.
Matching equipment to project needs is important. Whether or not a job calls for a mud motor is an important decision for the contractor.
“Many factors must be considered when determining the type of rock drilling equipment to utilize,” Hockran said. “They include length of crossing, diameter of product, geological conditions (whether rock is consolidate or unconsolidated), drilling rig, environmental considerations for fluid/air use, experience of the drill crew and type of steering tool.”
When drilling with a mud motor, one of the critical components is mud pumping capacity, which is determined by the drill string’s inside diameter and mud pump and mud recycling system combination.
“For this reason when drilling with a mud motor typically the smallest drill rig used is a 60,000-pound machine, Hockran said. “This size drill typically uses 3 1/2-inch drill pipe which will provide the necessary mud pumping capacity with a minimum 200 gpm pump and mud recycling system. The larger the diameter of the drill pipe, the larger the mud motor, pump and mud recycling system required.”
H&H uses tri-cone sealed bearing bits for pilot holes and low-torque hole openers to complete the hole opening process in rock.
“In our experience,” said Hockran, “the mud motor and traditional hole openers have proven very successful and consistent in the northeast region of the U.S. Typically, we own the mud motors we use. For a company that drills in rock the majority of the time, it is best to purchase mud motors, but at times we will rent them as needed.”
For rock drilling without a mud motor, Hockran considers two primary options:
• Conventional heads with TCI inserts for cutting efficiency and wear; and
• Air hammers.
“The conventional TCI drill head is effective and efficient in rock formations less than roughly 15,000 psi,” said Hockran. “Harder rock decreases the ability to steer effectively and reduces production. These drill heads are excellent for gravelly and or unconsolidated rock formations as they will not wear out as quickly as a standard ‘dirt’ drill head.
“Air hammers are increasingly becoming a more popular alternative in the HDD rock drilling market. They are very effective for drilling plus-or-minus 6-inch pilot holes in hard rock more than 15,000 psi, and in certain very hard rock exceeding 25,000 psi rock, an air hammer will be more effective and efficient than a mud motor. A limitation with air hammers is that steering is not very effective in unconsolidated formations, and it is sometimes very tricky to keep the drilled hole clean.
“While air hammers are great for pilot holes, the hole-opening capabilities of hammers are very limited and do not seem to be as efficient and effective as traditional hole openers that require fluid.”
Hockran emphasizes that each of the methods described are project specific — no one tool or method is suited to all types of rock drilling.
In closing, Hockran said failure to properly plan is the most serious mistake to avoid for rock drilling projects. It also is important to have a “Plan B” for unforeseen circumstances, including weather.
“Proper planning and contingency design are the most important steps in minimizing mistakes or unknown obstacles for successfully completing a project,” Hockran concluded.
Comments