February 2011, Vol. 66 No. 2
Features
Annual Gas Distribution Survey
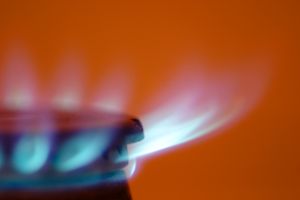
Each day, close to 70 million customers in the United States depend upon the nation’s natural gas distribution network, including gas distribution companies and pipelines, to deliver gas to their home or place of business. These customers currently consume approximately 20 Tcf of gas per annum, accounting for about 22 percent of the total energy consumed in the United States each year.
This end use customer base is 92 percent residential units, 7 percent commercial businesses, and 1 percent large industrial and electric power generation customers.
However, the large volume users, though small in number, account for more than 60 percent of the gas used by end users. The more than 1,500 companies that carry out the gas distribution process are varied in size and type. They include gas local distribution companies (LDCs) serving millions of customers, as well as those that serve less than 100. They also include mainline gas pipeline companies that provide direct service mostly to large volume end users, although the bulk of the gas transported by pipelines usually reaches end users via LDCs.
A recent report from the Energy Information Administration (EIA) indicates that the nation’s more than 1,500 local distribution companies are facing challenges in the coming year. While U.S. natural gas consumption is projected to rise, prices are not expected to follow.
The EIA’s Short Term Energy Outlook, released Oct. 13, 2010, projects an increase in U.S. gas consumption of 4.6 percent and 0.1 percent in 2010 and 2011, respectively.
Annual Mileage for Natural Gas Distribution Pipelines 1984-2009
Historical totals may change as PHMSA receives supplemental information.
According to the report, consumption of gas in the industrial and electric power sectors makes up the bulk of the year-over-year increase in consumption in 2010.
The report notes that the 0.1 percent increase in total gas consumption in 2011 is the result of about a 1 percent increase in residential, commercial, and industrial gas consumption, offset by a 1 percent decline in electric power sector consumption. The projected increase in residential and commercial consumption next year is the result of a forecasted 1.7 percent increase in U.S. population-weighted heating degree-days. As noted in the report, industrial sector gas consumption growth is driven by the projected 2 percent increase in the natural-gas-weighted industrial production index. Despite a slight decrease (0.3 percent) in electricity consumption in 2011, projected electric-power-sector natural gas consumption falls by 1 percent primarily because of forecasted increases in nuclear and renewable-based electricity generation.
Price concerns
Uncertainty over future gas prices is lower this year compared with last year at this time. As a result, the EIA report indicates gas prices for 2011 are expected to be at $4.58 per MMBtu, which is $0.18 per MMBtu (4 percent) lower than earlier anticipated, primarily due to a stronger domestic production forecast.
While some trends offer strong business opportunities for the LDC, the industry is facing new legislation that requires each operator of a gas distribution system to develop a written Distribution Integrity Management Program (DIMP) plan no later than Aug. 2, 2011, under a rule issued by the Pipeline and Hazardous Materials Safety Administration (PHMSA).
The most costly aspect of the new legislation is likely the requirement to install Excess Flow Valves (ESVs) on all new and replaced service lines serving single family residences if practical.
Gas Distribution System Operators Incident Summary Statistics by Year 1/1/1986 – 12/31/2009
Oct 13, 2010
As a result of legislative and regulatory changes and increased consumption, overall LDC spending in the coming year is projected to rise. Underground Construction’s latest survey figures indicate gas utility spending to serve new customers, and rehabilitate, repair and replace the nation’s 1,217,160 miles of distribution mains and 65,514,933 services, meters, valves, regulators, cathodic protection, SCADA networks and peak shaving facility will total approximately $12.1 billion in 2011, compared to $11 billion this year.
Plastic pipe
Polyethylene (PE) has been widely used in fuel gas distribution piping systems since the late 1950s. Today, polyethylene accounts for 97 percent of all new gas distribution piping installed each year.
These tough, durable piping products offer tremendous advantages to the gas piping engineer for the design and installation of a highly cost-effective, reliable and safe fuel gas distribution system. Highly flexible and light-weight, PE piping systems are chemical and corrosion resistant thereby reducing the need for cathodic protection of the underground piping infrastructure. The heat fusion method of joining these systems provides the potential of leak-free system performance. A full range of diameters from ½-inch CTS to 24-inch IPS is available in a variety of wall thicknesses or SDR’s.
According to the Plastics Pipes Institute, a new thermoplastic piping material has been introduced to the fuel gas distribution industry. Polyamide (PA) piping systems offer a new range of performance capability. The PA piping systems possess a higher hydrostatic stress rating than the traditional PE piping systems, and, as such, provide a perfect complement for higher pressure operational needs. Like the PE piping systems, the PA systems are available in a broad array of sizes and with a full complement of fittings. Similarly, the PA piping systems are joined using heat fusion methods which provide, once again, for the potential for leak-free system performance.
While polyamide piping products have been used in various energy-related applications for over three decades they have only recently been introduced to the fuel gas distribution industry. Today, 4-inch IPS SDR 11 Polyamide 11 is the only plastic pipe that is approved for use in fuel gas distribution at pressures up to and including 200 psi by the Department of Transportation. The Plastics Pipe Institute says this illustrates the potential use of PA piping systems as a durable, corrosion-free, chemical-resistant and leak-free alternative in the operating ranges of steel pipe.
Pipeline incident prevention
According to the PHMSA, the vast majority of America’s pipeline network is underground making pipelines vulnerable to “dig-ins” by third-party excavators. While excavation damage is 100 percent preventable, it remains a leading cause of pipeline incidents involving fatalities and injuries. Three-quarters of all serious consequences from pipeline failures relate to distribution systems and more than one-third of these failures are caused by excavation damage.
PHMSA notes that one of the primary tools for avoiding damages to pipelines and other underground facilities is timely communication between excavators and those who operate or own buried facilities. When contacting One-Call Centers, excavators should be able to properly identify areas of planned digging activities to ensure all utilities are accounted for before work commences. The One-Call Center then contacts utility companies, which can dispatch crews to locate and mark the exact location of their utilities to avoid.
Survey Results
Once again, LDC managers were queried for comments on several subjects, including the cost of finding and repairing leaky mains. The cost figures and comments from industry participants on these and other topics follow.
This year’s figures provided by survey participants on main costs report that two to 4 inch-diameter PE pipe continues to be widely used in the gas utility industry, accounting for 95 to 98 percent of new mains installations in developed areas. While the cost per foot for steel main installations appears to be dropping, the cost per foot for plastic main installations has increased.
Those reporting plastic main installation costs per foot ranged from $9.54 to $23.54 for 2-inch; $12.96 to $33.00 for 4-inch; and $45.70 to $64.00 for 6-inch.
While a number of companies indicated they no longer used steel mains for new installations, others provided the following as costs for protected steel main installations: 2-inch, $4.75 – $18.50; 4-inch, $13.90 – $17.85; and $14.75 to $64for 6-inch.
As in past year, the respondents cited leak location – street vs. lawn – as driving the finding and repair cost of leaky mains. Some 45 percent of the respondents gave location as a major cost factor. Those providing finding and repair costs per occurrence, regardless of size, placed costs between $350 and $2,800. However, more than 76 percent of this year’s respondents gave $350 to $1,500 as an average costs for finding and repairing leaky mains.
One utility almost 1.1 million customers provided the following as the company’s average cost for finding and repairing leaky mains: 2 to 8-inch, $350; and 12- to 24-inch, $900.
Integrity management
A significant number of this year’s survey participants expect the Distribution Integrity Management Program (DIMP) to be enacted next year to be costly and burdensome, particularly for small LDCs. More than 75 percent of those surveyed said they expected the legislation to be more costly for the LDC and ultimately the customer than the PHMSA has suggested.
A sizeable number of the recipients cited the following as contributing to the increased costs: Documentation and record keeping and the requirement for Excess Flow Valves (on all new and replaced service lines serving single family residents if practical), which was cited as adding cost to service.
A gas utility in Florida sees the integrity management legislation as creating a need for additional tracking and reporting burdens and associated costs to document actions. The respondent also indicated that the additional cost to comply with a standardized government format, for most companies, would far exceed any benefits.
With older systems blamed for several recent explosions, companies say they are continuing with long-term programs to replace unprotected steel service lines installed in the 1960s, 70s and 80s.
Atmos Energy has been replacing the steel service lines in its Mid-Tex Division since it acquired the gas distribution system from TXU Corp. in 2004. In July 2010, the company reported it had 57 contract crews dedicated to doing this work and replacing, on average, 500 steel service lines a week. The steel service lines are being replaced with polyethylene lines and are joined with modern fusing technology.
According to the company, the Mid-Tex Division replacement program typifies the preventive maintenance and continual renewal that Atmos has carried out on its gas distribution system in all 12 states in which they operate. The company has reportedly completed, or has under way, similar pipe replacement programs in other states they serve.
As to survey results, 66 percent of survey indicated they have replacement programs in progress while 16 percent indicated they had no cast iron or unprotected steel in existing system. Of the 15 percent reporting bare steel in existing system, the following was the most cited as the risk assessment used to select main and service lines for replacement each year: leak history, pipe materials, maintenance history and location. Only 3 percent of this year’s respondents indicated they had not yet started a long-term program to replace bare steel and cast iron in existing systems.
Respondents reporting on the use of contractors indicate that contractors continue to provide a major portion of new distribution construction to install gas utilities. Although about 10 percent of those reporting indicated they did not rely on contactors at all, approximately 80 percent rely on contractors to carry out 85 – 100 percent of all new construction on projects, while 10 percent rely on contractors to perform 20 to 73 percent of this work.
Comments