December 2011, Vol. 66 No. 12
Features
Pipe Bursting Large Diameter Pipe - Class C Pipe Bursting
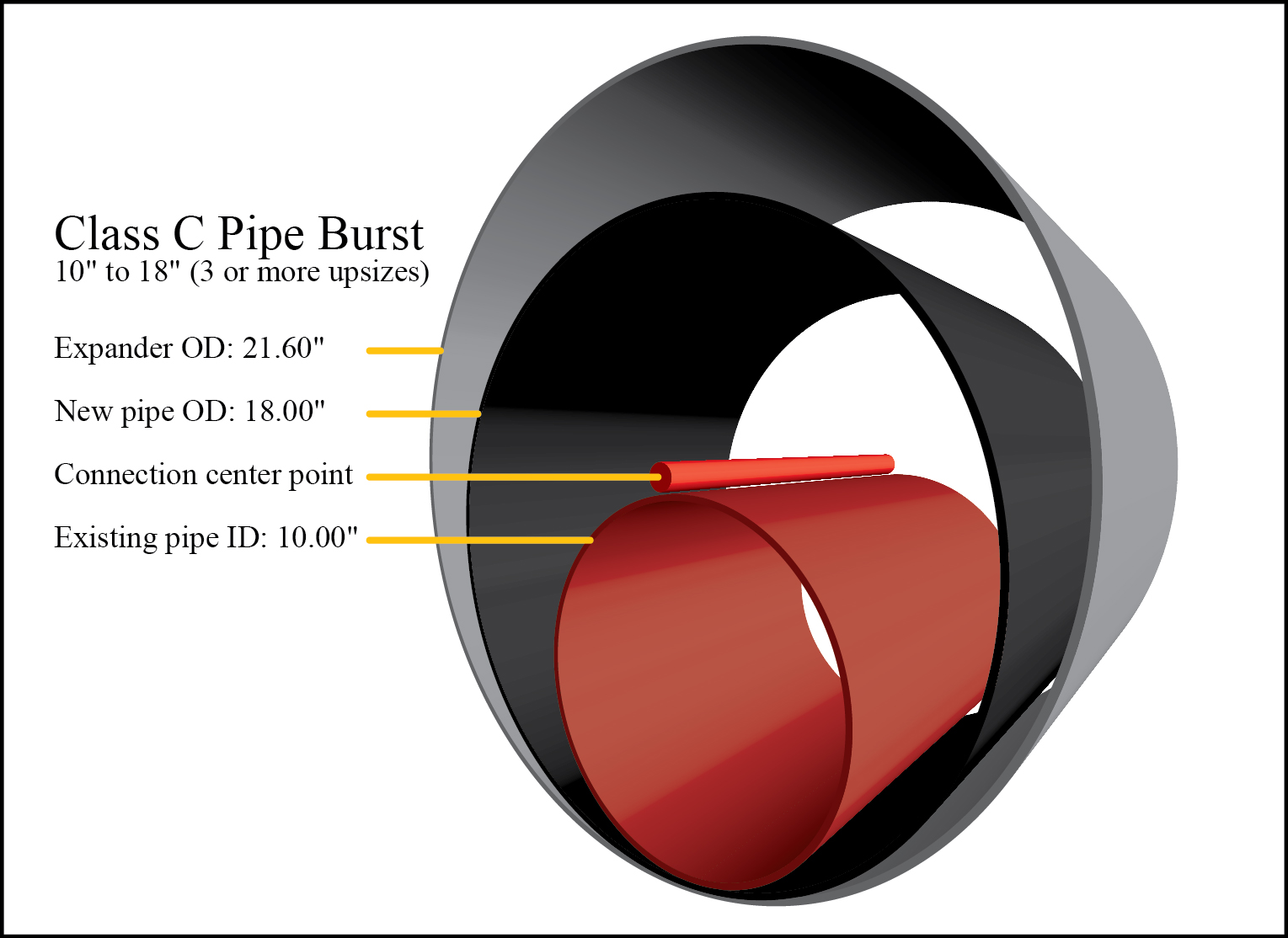
Editor’s Note: The International Pipe Bursting Association (IPBA), a division of NASSCO, is presenting a series of articles in Underground Construction that will provide the reader with a better understanding of the technology. Many myths and misconceptions exist regarding this proven rehabilitation method for replacing existing underground utilities.
Pipe bursting is a proven method for replacing underground pipelines and is the only method of pipeline rehabilitation and replacement that can increase the size of an existing utility without trenching. This article will discuss the replacement of large diameter pipes.
In pipe bursting terminology, large diameter bursting refers to existing pipe sizes larger than 20-inches in diameter and the IPBA classifies large diameter pipe bursting as Class C Pipe Bursting.
The most common application for pipe bursting in the United States is smaller diameter pipes generally in the six to 10-inch range which represents up to 80 percent of the market. However, large diameter pipe bursting is a proven method and is increasingly used as pipes like interceptors, trunk lines and main distribution mains are in need of replacement due to deterioration or increase in hydraulic demands. The passage of the Clean Water Act in 1972 caused interceptor sewers to be built in older U.S. cities, many of which are located in remote easements and in close proximity to waterways. Now, nearly 40-years-old and failing due to structural defects or corrosion and in many cases undersized due to population growth, these larger diameter pipes are in need of replacement. Pipe bursting offers many advantages when compared to traditional dig and replace or other more common rehabilitation methods like CIPP.
Both static and pneumatic pipe bursting are common in large-diameter pipe bursting and the capabilities have increased significantly in the past 10 years as contractors have gained real world experience, manufacturers have improved the systems available and owners/consultants have been willing to consider pipe bursting on their projects. The concept of pipe bursting does not change as the diameter increases. However, the experience required and considerations made are much more detailed as they are with almost any construction method as pipes get larger.
Calculations
This article primarily focuses on replacement of large diameter sewer mains as that makes up the majority of large diameter pipe bursting. Proper project planning is critical to success and as pipe sizes increase the calculations required to manage the installations become more complex. A project team must have a clear understanding of the forces required to install pipe with bursting technology. The primary calculation is the force required to install a new pipe from point A to point B. Pipe bursting is accomplished in three steps that are all occur simultaneously as the pipe is installed. These steps are represented in the following equation as A, B and C.
A. The amount of energy required to burst or split the existing pipe — plus (a) the amount of energy required can increase in areas where pipe repairs were made, or there are some types of pipe joints or other factors with the existing pipe material.
B. The energy required to expand the existing soil to +/-20 percent larger than the OD of the newly installed pipe – (b) this is a volumetric calculation and the displaced volume is directly related to the difference from the ID of the existing pipe and the OD of the expander head. The energy required to expand the existing soil will vary with changes in soil conditions or original trench construction.
C. The drag that is placed on the new pipe as it is pulled into place – (c) drag can increase as the installations get longer, soil conditions or groundwater table causes the annulus to revert the pipe contact state, or a number of other factors.
Also, another factor that must be consider is lubrication (L) which is often used on Class C pipe bursting projects to reduce pipe drag by maintaining hole stability or friction caused by the existing soils contacting the new pipe. Lubrication mixtures are often similar to that of horizontal directional drilling mud. However, the project team must have a true understanding of fluids in order to truly manage drag forces and maintain a safety factor. This is generally the amount of power that is desired to be in reserve during normal conditions.
All this equates into the following formula: (A) x (a) + (B) x (b) +(C) x(c)-(L) = Required Force + (safety factor %) = Equipment Required.
The biggest difference between a small diameter and large diameter burst is that the expansion force is a volumetric displacement formula which is directly related to the amount of soil that must be displaced and the energy required to do so.
As the soil is expanded up and out, the center line of the new pipe will change in relation to the center line of the existing pipe. The invert in most soil conditions will follow that of the existing pipe elevation and slope. As the center line of the new pipe changes considerations must be made for reconnecting service laterals or other connections. Depth of cover calculation can be taken to determine if the expansion upwards has the potential to cause ground heave, this calculation is dependent on the volumetric displacement calculation which is a direct relationship between the ID of the existing pipe and the OD of the expander so when upsizing of the existing pipe is being performed the depth of cover must be greater. (See insert image)
Make data available
In the design stage of a project, it is essential that all applicable information is made available to the project team or potential bidders as this data will help the team determine the type and size of equipment that is best suited for the specific project, as well as begin building contingency plans for construction activities. Job site logistics and pit locations are critical to any trenchless project and considerations must be made for actual location, size and specific requirements of pipe bursting pits. Large diameter pipe bursting project will require detailed geotechnical data as actual soil conditions will impact both the expansion force and drag calculation.
The two most common types of pipes installed for large diameter pipe bursting are HDPE and fusible PVC (FPVC), both of which are installed in continuous segments, although FPVC can only be installed by static means. Handling, fusing and inserting large diameter pipes is much more challenging than as is common with smaller diameter pipes.
It is important that everyone involved have a good understanding of the pipe being installed and the considerations that must be made in the field for an installation of a continuous length of pipe and the tools, hoses, etc. that are attached to it during the installation. Resources and manpower required for maneuvering pipe into the insertion pit and maintaining the proper insertion angle should be a defined part of the installation plan. Actual insertion pit lengths are calculations based on the bend radius of the pipe being installed and the depth of the existing pipe. These calculations vary by pipe size, SDR and pipe type, and should again be a defined part of the installation plan.
By-pass and isolation of the existing flows is essential to managing a safe and successful project. All details should be determined in advance of any field work including the dry and wet weather flows, where the flows will be isolated to and from, and the layout of the by-pass system and designing it so it does not conflict with the pipe bursting or handling of the new pipe as it is prepared. In most cases, the flows are isolated at least one manhole upstream and downstream of the project. It is not practical with large diameter pipe bursting to restore flows at the end of each shift as is sometimes common with smaller diameter projects.
Connections that are made to large diameter pipes such as service laterals, manhole terminations and connecting two plain end pieces of pipe must be clearly defined in the project specifications and work plan. With HDPE pipe, the ability to fuse in the trench is much more difficult with pipes larger than 18-inches in size and couplings available are most often electrofusion or mechanical types. A number of styles of lateral connections are available from mechanical saddles to Inserta-Tees that allow a PVC sewer lateral to be connected to the new HDPE or PVC mainline. A clear understanding of these connections to the newly installed pipe will reduce the chance of confusion in the field or rework by the contractor.
Class C pipe bursting projects are being successfully completed with greater frequency throughout the U.S. and should be a part of your rehabilitation toolbox.
Do your homework, select a quality project team and go pipe bursting! New pipe, more capacity: for pipe bursting the time is now.
FOR MORE INFORMATION:
IPBA (NASSCO), (410) 486-3500, www.nassco.org
Comments