November 2010, Vol. 65 No. 11
Features
Logistics Is Key During Pre-Design For Linear Pipeline
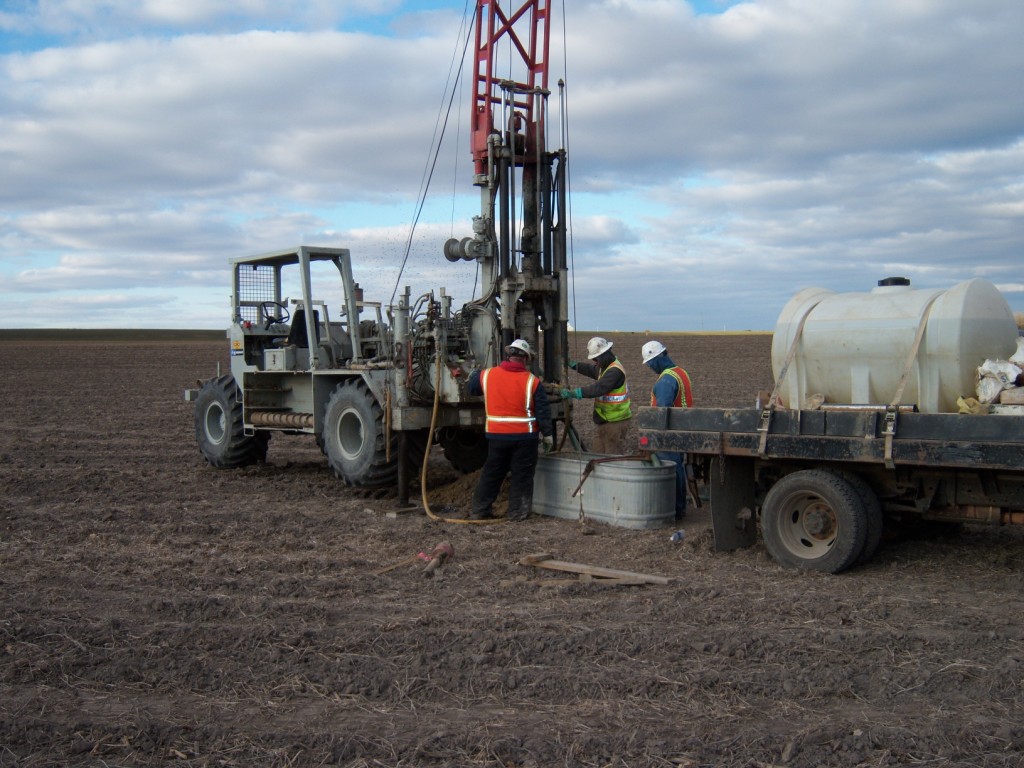
When faced with a project that is 133 miles long, spans two states and dozens of counties and features a tight schedule, logistics can be a serious foe. Communicating to many design team members and being responsive to the many challenges encountered in the field only complicate the efforts to successfully complete a project on time and on budget. Developing organizational and coordination skills into a serious strength and planning appropriately are paramount to operating efficiently, performing well and providing quality results.
This is just the approach taken when Geotechnology Inc. was chosen to be the geotechnical consultant to support the design and construction of a proposed pipeline.
Geotechnology is a professional corporation offering a comprehensive range of consulting services in applied earth and environmental sciences, including geotechnical and environmental engineering, construction materials testing, geophysics and drilling. Geotechnology, Inc. is headquartered in St. Louis.
Underground product pipelines are a typical means to transport liquids over long distances. They are built between production areas and refineries or tank farms, tank farms and refineries, or from any of these facilities to distribution points. Pipelines are usually constructed with plastic or steel depending on the diameter, which may range from four to 48 inches. In overland areas buried pipelines are constructed in trenches varying from six to 15 feet in depth. At significant crossing locations, such as interstate highways, railroad tracks or rivers, pipelines are installed using horizontal directional drilling (HDD). This proposed project featured 20 and 42-inch diameter steel and plastic pipelines to carry oil from a production facility to a tank farm. Geotechnology developed a geotechnical program for the 133-mile long alignment, which featured more than 500 borings and 14 HDD sites.
Project scope
Geotechnical subsurface exploration involved drilling borings at one to 4-mile spaced intervals along overland areas and drilling four borings to predetermined depths at HDD crossings. The project team included several owner-representatives who served as project managers, as well as contract negotiators, right-of-way agents, safety inspectors and other consultants providing technical and logistical support for the project. The effort required effectively communicating with all project team members.
Observations in the overland borings focused on concerns related to trench excavation and backfill such as depth to bedrock within the excavation zone, groundwater level, soil stratigraphy and corrosion potential. Laboratory testing included index tests and soil corrosivity tests. Index test results are used for soil classification and in situ characteristics. Corrosivity test data are used in assessing buried pipe material type and the need for or extent of corrosion resistant systems to protect the pipeline. Environmental-related construction permits included strict controls on replacement of top soil in trench backfill. Therefore, boring logs included topsoil thickness at each boring. During construction this material will be set aside and replaced as the final course of trench backfill.
For the HDD alignments, two borings were typically located on each side of the feature, such as a railroad crossing, highway or river, and were cored into bedrock to an elevation approximately 10 feet below the proposed HDD placement. One boring was near the entrance point, one each at the one-third and two-thirds points and one at the exit point. The borings at the third points were near where the vertical HDD alignment was deepest. Physical access features led to field adjustment of boring locations from the ideal positions.
In the deliverable reports for the HDD sites, Geotechnology provided foundation recommendations and addressed footing loads from the directional drill and associated equipment. Design and construction recommendations for the mainline overland sites included trench excavation considerations, suitable trench backfill recommendations and temporary shoring recommendations.
Getting the work done
It was important to understand the client’s schedule for the various aspects of their project and the work was planned accordingly to complete the 500-plus bores. Twenty-four reports were delivered as produced over a 1½-year period. Organization of reports fell into two categories: site-specific HDD reports and per-county reports for the overland borings. The field work and report preparation and delivery was executed in the sequence preference identified by the owner.
The boring locations ranged from 100 to nearly 300 miles from Geotechnology’s office. As the borings were completed, an employee was periodically designated to deliver samples back to Goetechnology’s laboratory for testing. A portion of the lab work was subcontracted and this presented another logistical task to manage work orders, make test assignments, deliver samples to the subcontract lab and manage and incorporate the results into the reports.
The client and Geotechnology both have strong safety cultures. These cultures were meshed and reinforced on this project with a two-hour safety orientation meeting for all project field staff conducted by the client’s corporate safety officer at Geotechnology’s office before mobilization. While conducting field work, each day began with a safety-tailgate meeting when the plan for the day, general safety measures and any specific hazards expected that day were reviewed. Geotechnology and its subcontractors completed the project without first-aid incidents, OSHA-recordable incidents or lost-time accidents.
Challenges & solutions
The field services, laboratory testing, and reporting on this project were on a very tight schedule. Scheduling resources for multiple drill rigs for which all these criteria had to be met before the rig arrived at the boring location, while keeping all of the data straight as numerous reports were prepared was the largest challenge of this project.
Numerous tasks performed by various individuals on the project team had to be completed for each boring prior to the arrival of the drill rig, such as clearing utilities, coordinating right-of-way, acquiring private property access permissions and locating borings. Geotechnology used its own drill rigs and subcontracted others. At times there were eight drill rigs working in numerous counties on a single day. A Geotechnology employee visited each boring site, staked the location, made a utility clearance call and coordinated with the owner’s right-of-way (ROW) agent for the area. Geotechnology coordinated efforts with government entities and private property owners through the ROW agent. Many tasks, being simultaneously executed in several areas, had to be completed for a group of relatively closely-spaced borings before mobilizing the drill rig in order to minimize drive time between distant locations, and in some instances, just marching down the line drilling borings in a logical and efficient sequence.
Borings on government property required some combination of bonding, insurance certificates, excavation permits and/or traffic control. Borings on private property required close communication with the owner, scheduling to avoid crop damage in agricultural fields, or scheduling to follow successful completion of the property owner’s alignment right-of-way negotiation with the project owner.
Successes & lessons learned
Crews developed a rhythm in their field activities that led to an efficient execution of widespread borings. Crews worked 10 days on, four days off, which reduced time spent driving to and from the sites and facilitated a higher, average production rate per shift. Periodically, a driver would carry samples from drill rigs back to the Geotechnology office so sample assessment and lab assignments could begin rather than waiting for the end of the 10-day shift.
One item that would have lowered the overall cost of the subsurface explorations is a longer execution schedule. Four field crews were often hop-scotching along the alignment to boring locations that were cleared for access. A longer schedule or the capacity to get more right-of-way clearances sooner would have simplified field execution and lowered the associated cost. Inability to secure access to all overland borings in a county, for example, led to drilling those that were available, issuing a report and, upon the owner access and review of those reports returning to the area and completing borings, and issuing a subsequent, complete report that included all gathered data.
Conclusion
Design work on this project is essentially complete. Findings in the geotechnical borings did affect pipeline design. In one rather long HDD crossing where six, rather than the typical four borings were drilled, voids, some filled with pressurized gas, were encountered in the upper 50 feet of the bedrock profile. The inability to accurately locate 100 percent of potential voids along the HDD alignment led to a decision to not use HDD in this area and go to a more costly pipe-buried-in-trench alternative.
However, due to economic conditions at this time, pipeline construction is delayed.
About the author
Dale Smith, P.E., is currently the branch manager for the Geotechnology, Inc. – Collinsville, IL, office — and is responsible for the management of geotechnical investigation and design projects. He has extensive experience in geotechnical engineering investigation and foundation design related to the construction of building structures, roads and highway/railroad bridges, and industrial facilities. His experience includes foundation investigation and design for existing dams and levees, stormwater/sewage systems, buildings and industrial oil/gas facilities. He holds a masters degree in civil engineering from the University of California at Berkeley and a bachelor’s degree in civil engineering from the Missouri University of Science & Technology.
Comments