May 2010 Vol. 65 No. 5
Features
Cool Crossings
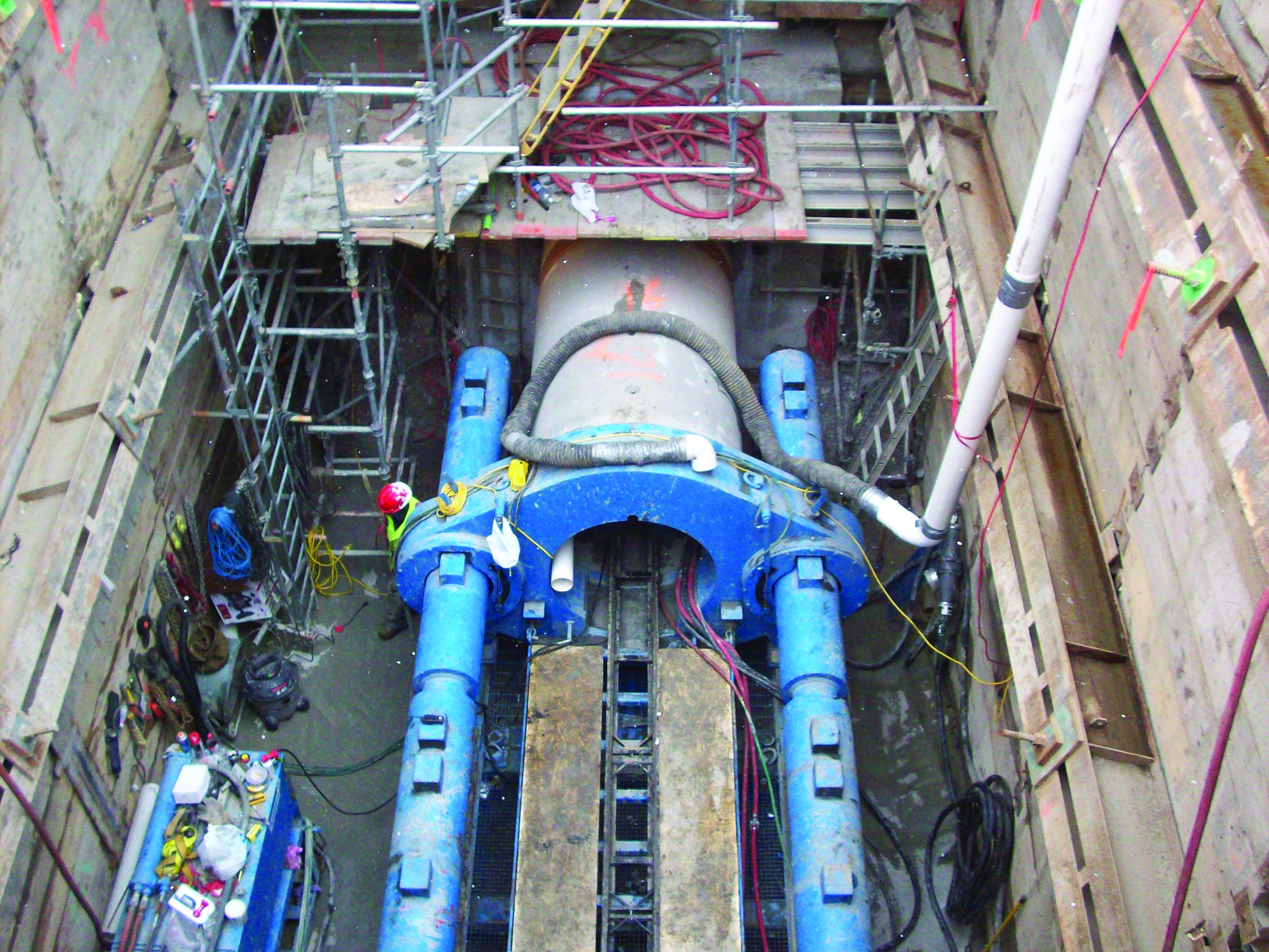
With typical daily temperatures barely topping 5 degrees Fahrenheit, winters in Calgary, Alberta, can easily hinder trenchless operations. Liquids in machinery can freeze solid, while expanding groundwater can potentially warp rails and other equipment in launch pits.
Recently, Edmonton, Canada sub-contractor In-Line Contracting needed a durable, cold-resistant solution to effectively dig through the mudstones and clays common to the area, while maintaining the strict line and grade requirements needed for a gravity sewer.
The 690-foot-long crossing for a trunk sewer upgrade involved the launch of a self-propelled boring machine, known as a Robbins Rockhead, in December 2009. Crews covered the top of the pit each night and pumped heat into the 20-foot deep launch pit to prevent fluids from freezing and water from expanding.
Project background
The new pipeline, known as the Confederation Sanitary Sewer Trunk Upgrade, is set to increase capacity to overused lines in northwest areas of the city. “The city of Calgary has been growing quite rapidly over the last number of years, so all of the pipes need to be larger. This is all part of an ongoing project to upgrade the city’s infrastructure,” said Bill Stace, crew foreman for In-Line. The new line replaces an old trunk sewer installed in 1905 that is currently over capacity, particularly during heavy rain events.
The entire pipeline, being construction for the city of Calgary’s Water Resources Department, is approximately 1.25-miles long and ties in with existing trunk sewers in the region. From the crossing site, the trunk sewer will tie in with an existing 66-inch diameter sewer line, which will combine with other gravity sewers. All of the material is then conveyed to the city’s largest treatment plant at Bonnie Brook. By December 2009, nearly the entire pipeline had been completed, except for a 690-foot crossing below 32nd Avenue, a busy thoroughfare just outside the downtown area.
Core samples of the crossing area found clay with layers of fractured, hard mudstone 20-feet below the surface. The alignment of the tunnel was lowered in the hopes of excavation in comparatively stable siltstone bedrock. “We opted for a trenchless crossing because open cut of the main road, 32nd Avenue, was not an option. The ground was also shown to be somewhat unstable, and not conducive to open cut tunneling,” said Ali Rafih, superintendent for general contractor Volker Stevin.
The crossing for the gravity-fed trunk sewer also came with strict line and grade tolerances — an upward slope of 0.126% was needed, while the line needed to be within two inches due to the limited size of the receiving pit. The requirements meant that the contractor needed a tunneling machine that could be steered continuously.
Volker Steven and In-Line ultimately chose a Robbins Double Shield Rockhead with a breasted plate cutterhead for potentially abrasive ground and 11.5 inch disc cutters to effectively excavate potentially hard rock. The project is the first instance of this particular machine type being used in Canada. “The Rockhead was the most economical option for us. Though we believe microtunneling would have worked as well, the microtunneling setup is much more costly,” said Rafih.
The sentiment was echoed by Bill Stace of In-Line: “In these particular project conditions, the Rockhead can not only equal but exceed the efficiency of microtunneling.”
Excavation in fractured ground
The launch site, consisting of a 20-foot wide by 35-foot long pit, was excavated deeper than expected due to the geology. “We had anticipated an open pit excavation, but once we started excavating, we found that the bedrock was quite fractured. Instead we now have a 23-feet deep shoring and shaft replacing the open pit,” said Dwayne Giesbrecht, Calgary Water Resources Department.
The Rockhead was launched in December 2009 with a pipe jacking unit for initial thrust at startup. The short pit length required that the machine be launched as a Single Shield machine, without a rear shield and gripper cylinders. After boring ahead 20 feet, the final gripper shield was bolted to the modified machine, consisting of a front shield, thrust body and shortened conveyor. Crews then added the remainder of the conveyor section, making the machine’s total length 39 feet.
Crews worked eight to 10-hour shifts, managing wet ground conditions. “At the start of each shift, ground water is an issue, as it collected overnight. We slowed the rate of machine advance to allow the friction of the cutterhead to dry out the tunneling face. This allowed the material to move through the cutterhead and onto the machine conveyor without clogging the hopper area. The method worked well as long as we took our time during startup each morning,” said Scott Fisher, SBU field service manager.
At the end of the drive, the machine hit watery, soft mudstone that slowed progress. Crews added an intermediate jacking station to keep the gripper machine progressing in the soft material. In addition, bentonite was injected outside of the casing to make the pipe easier to push, as the soft material tended to collapse in around the casing.
New pieces of 8-foot long, 66-inch diameter pipe were installed every 45 minutes during the drive. The four-inch thick reinforced concrete pipe was jacked in behind the machine to serve as the primary liner. Muck was transferred through the cutterhead to a machine belt conveyor, which emptied into a single track muck car. Each muck car took about 10 minutes to exit the tunnel through the casing, where it was lifted out of the launch pit using a crane and emptied at a storage area on the project site before reentering the tunnel. Crews pumped heat into the pit nightly, in order to prevent water in the pit bottom from expanding and warping the rails or pipe jacking system.
Future tunneling
On completion of the Confederation Trunk Sewer Crossing in mid-April, the machine broke through into a receiving shaft at the side of a parking lot and near the main road at 32nd Avenue. “We will be doing some pipeline rehabilitation in the area, as well as restoration of the jobsite,” said Rafih. “This is a special project for us. The residents in western areas of the city have had issues with sewer surges any time there is heavy rainfall. They have had flooded basements and insurance costs in the area are now very high. We have the opportunity to change that for them.” The pipeline is scheduled to be operational later in 2010.
In-Line is positive about the future use of tunneling machines in the Calgary area. “I think I first heard about Robbins machines maybe 15 years ago, when we rented an SBU-A for an auger boring job,” said Stace. “The equipment allowed us to get through some very hard ground that we couldn’t get through with our conventional auger boring equipment. We’ve been renting them off and on ever since, and hope to continue using the equipment.”
How The Equipment Operates
The Robbins Double Shield Rockhead (SBU-RHDS) is a tunneling machine for use on longer utility installations (usually over 600 feet) and in unstable ground. It also typically used for line- and grade-critical installations such as gravity sewers, as the machine can be continuously steered from an in-shield operator’s console.
The machine, available in diameters from 54 to 78 inches, consists of a circular cutterhead mounted with single disc cutters much like those on larger diameter tunnel boring machines. These disc cutters are used to excavate hard rock ranging from 4,000 to over 25,000 psi UCS. In mixed ground, two-row tungsten carbide insert cutters and carbide bits can also be used.
As the cutterhead rotates, disc cutters ranging from 6.5 to 15 inches in diameter penetrate the rock face and create a “crush zone” through which fractures propagate. Material between adjacent crush zones is then chipped from the rock face. Muck scrapers scoop the muck into openings on the cutterhead called muck buckets, which transfer the material to a machine belt conveyor. Muck removal from the site is by either a belt conveyor or muck cars.
The machine is typically launched from a pit, and can be either self-propelled using a gripper system or pushed forward with a separate pipe jacking system. During excavation, the tunnel is lined with a primary liner of the contractor’s choosing, including steel casing, ring beam and board, reinforced concrete pipe and four-flange liner plate.
FOR MORE INFORMATION:
Robbins, (440) 248-3303, www.TheRobbinsCompany.com
In-Line Contracting Ltd, 780-448-9638
Comments