December 2010 Vol. 65 No. 12
Features
Wet, Cold Can’t Stop Metro St. Louis Microtunneling Project
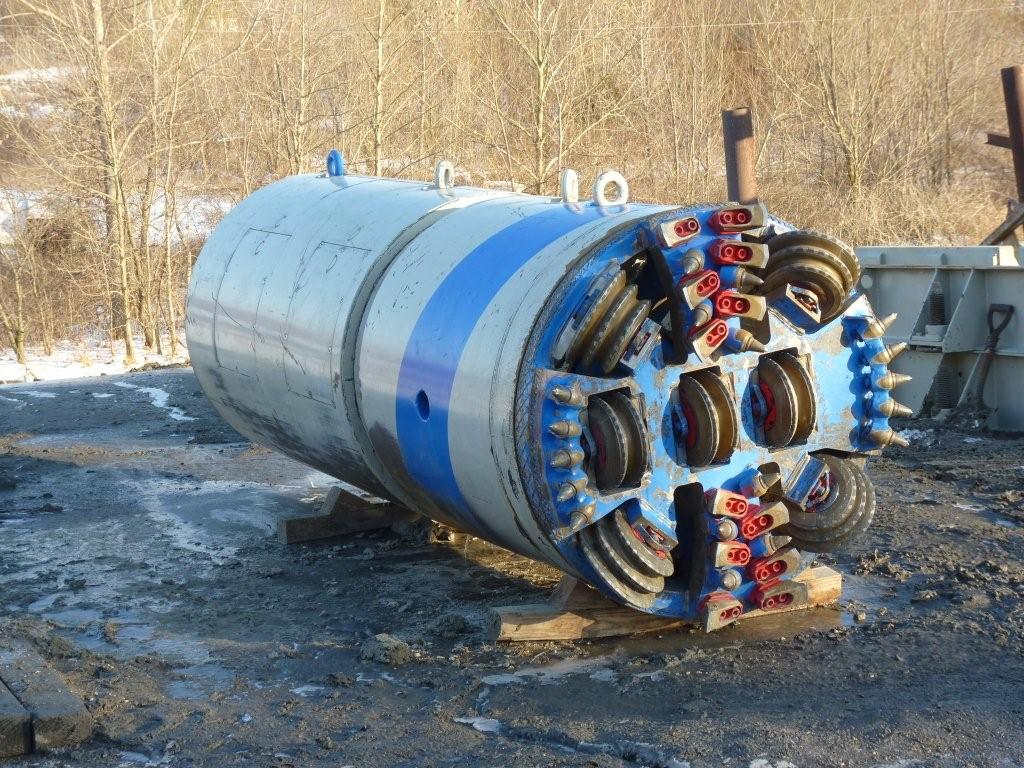
The Metropolitan St. Louis Sewer District (MSD) is in the midst of a multi-million dollar, multi-year capital improvement and replacement program that is expanding and rehabilitating the district’s entire wastewater collection and treatment system. It is the largest, most extensive improvement program in the history of the district.
MSD’s boundaries cover 525 square miles and encompass all of the City of St. Louis, MO, and approximately 80 percent of St. Louis County, serving a population of 1.4 million people. The system has 519,000 single-family residential, multi-family and commercial/industrial accounts.
MSD operates and maintains 9,649 miles of sewers with ages ranging from less than a year old to 150 years old. It has 311 miles of sewers predating 1890, and another 524 miles of sewers predating1930.
At any given time, there are many capital improvement projects under way throughout the MSD service area employing a broad range of construction and rehabilitation technologies.
One key project recently completed was a 1,034 linear foot segment of 48-inch steel casing constructed by microtunneling. It was a segment of the Infrastructure Repair Project 087P Caulks Creek Sewer Line “A” (P-750) Phase IV Section B in Chesterfield, MO. The project included approximately 5,771 linear feet of sanitary sewer force main varying in size from 23 to 36 inches in diameter.
Crawford, Murphy & Tilly Inc. of St. Louis was project engineer with Gershenson Construction Co., Eureka, MO, serving as the general contractor. The microtunneling subcontractor was J & J Boring Inc., Winfield, MO.
Two segments
Microtunneling segments for the two tunnels totaled 1,034 linear feet made in two drives under a creek and levee. This trenchless method of construction was required by the levee district to protect the integrity of the levee.
For the first tunnel, surface conditions at the site were a wet and muddy farm field which froze when cold weather came. The site for the second tunnel was a grassy area adjacent to a shopping center.
The first drive was 434 feet long, said Denny Heisler, P.E., vice president of J & J Boring.
“The access pit was approximately 34-feet deep with the water level in the pit at about 15 feet,” said Heisler. “These conditions required a dewatering system operated 24/7 at both the work pit and come-out pit. Drilling Service Co., Bridgeton, MO, installed the dewatering system.
“The work pit was approximately 40-feet long and 15 feet wide interlocked with sheet pile with steel beam walers. The come-out pit was shored with a trench box and pushed in sheet pile.”
The second tunnel of approximately 600 linear feet was about a half mile from the first tunnel.
“Again, an interlocked sheet pile with walers was used for the work pit which also required a continually-operated dewatering system,” Heisler said. “The come-out-pit was a 12-foot diameter drilled casing with the lower 18-feet in solid limestone. No dewatering was required for the excavation.”
Drives were made with an Akkerman SL44 microtunneling machine with 400 tons of thrust capacity.
“The guidance system was laser mounted outside the tunnel at the back of the pit and projected to a target mounted on the front of the machine,” Heisler said. “It was monitored and steered from a control station on ground level positioned next to the pit.”
Joints of 48-inch steel pipe were 20-feet long and hoisted into position and welded to the previously-installed pipe. A 20-foot Derrick Modular Separation System, placed about 25 feet from the work pit, processed slurry which discharged into a settling pond adjacent to the machine.
Wet and cold
Heisler said the 434-foot tunnel was through very wet, silty sand. The 600-foot tunnel began in very wet, silty sand conditions but the last 100 feet was in solid limestone.
“Wet and cold conditions were a factor throughout the project,” Heisler said. “The project was scheduled to start in August 2009, but was delayed until December due to permits and easements. Freezing weather added a degree of difficulty that would not have been encountered in warmer conditions. Extreme cold affected the mud slurry entering and leaving the separation plant.”
Construction of the tunnels was completed in February 2010.
J & J Boring began operations as a horizontal boring subcontractor in 1983. To meet changing customer needs, the company has evolved to include pipe jacking, horizontal tunneling and liner plate tunneling.
J & J Boring has completed more than 1,000 projects, most for water, sanitary and storm sewer systems. Typically the company works as a subcontractor, but has the capability to turnkey boring and tunneling projects. J & J Boring is a certified WBE, DBE contractor.
FOR MORE INFORMATION:
Akkerman Inc., (800) 533-0386, www.akkerman.com
J & J Boring Inc., (636) 566-6766, www.jjboring.com
Comments