December 2010 Vol. 65 No. 12
Features
Evolving Thermal Grouts Aid Growth of Underground Power Transmission Lines
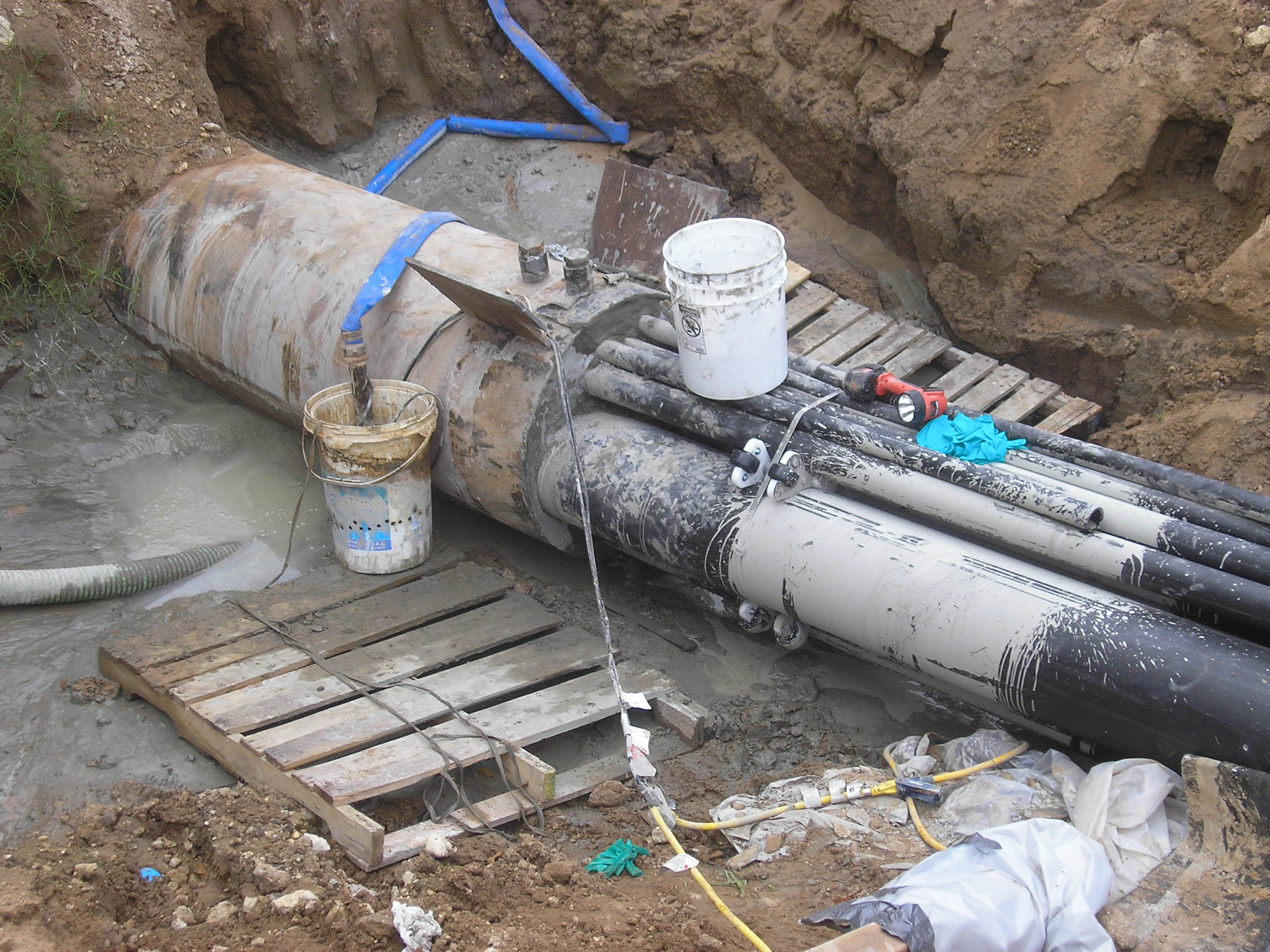
Grouts have a multitude of uses for many types of construction.
For utility construction, grouts are most often thought of for sealing leaks and joints in water and sewer pipe infrastructure, manhole rehabilitation and filling annular space between pipes and surrounding structures.
In addition, thermal grout is an essential part of the process of placing high-voltage power transmission and distribution lines underground, a trend that is becoming more common (see the June issue of Underground Construction). The use of plastics for insulation, advances in cable design and manufacturing, and other factors have made underground placement of high-voltage transmission lines a viable or necessary option in many situations.
The right thermal grout mix correctly applied is a critical element in constructing segments of underground power transmission lines. Thermal grout is used to transmit heat from underground electrical cables into the surrounding soil or rock, said Guy Dickes, president, Constellation Group LLC, who over the past four years has been responsible for planning and executing grouting for four major underground power transmission projects from 13.6 kV to 230 kV with segments from 100 to 2,000 linear feet in length.
Heat is the enemy of electric transmission, Dickes said. Heat increases wire resistance and shortens the lifespan of the cable insulation. Cross-country transmission lines suspended high in the air from steel towers are not insulated and heat is easily dissipated into the air. But for cable buried in a conduit under the ground, heat is confined.
“Thermal grout surrounds the individual conduits holding each cable and fills the casing completely,” Dickes explained. “This grouting technology is rapidly advancing.”
For example, Dickes said horizontal directional drilling and thermal grouting is used in underground applications where open-cut-and cover construction cannot be utilized. Some examples where open cut construction cannot be used are under creeks and rivers, expensive golf courses, developed properties, urban areas and many other conditions.
Misunderstood
Of all the elements contributing to successful underground power transmission construction projects, grouting is arguably the least understood and has been considered by many contractors to be “difficult.”
“Indeed, there are stories of project failures attributed to ‘bad’ grouting,” Dickes said. “In my experience, few contractors like to grout and unfortunately, grouting is left to the end of the job and given to the low man on the totem pole with little oversight. Untrained personnel pumping the wrong mix design into an expensive underground casing can be a very expensive mistake. A correct grouting operation starts at the planning stages of a project, should be fully developed prior to construction and properly executed by skilled personnel.
“Thermal grouting should be treated like any other technical part of the project — properly designed from thermal performance and constructability standpoints. In all its forms, grouting is a sophisticated technology that requires a specialist to perform. It is an operation that needs to be properly planned and executed. The mix design needs to be correct for the application.”
There is no one thermal mix design. Each grouting project has its own unique characteristics and must be planned accordingly.
“Thermal grouting is an engineered solution,” Dickes emphasizes. “There are no ‘cookie cutter’ specifications or mix designs. Often, we try to use locally available materials in order to minimize costs. Manufactured materials are available, suitable for long distance thermal grouting, but their thermal properties may not be as good as quarried aggregates and the cost is higher. Grout costs using these manufactured materials can run as high as $300 or more per cubic yard. The advantage of the manufactured materials is the ability to design grouts for pumping over greater distances.”
Dickes said his experience and role on thermal grouting projects is as a consultant and job-site manager. He considers Deepak Parmar, president of Geothermal Inc., the foremost scientist on thermal grouting.
“Deepak has been designing thermal grouts for underground power transmission projects for more than 30 years,” said Dickes.
Specific characteristics
Parmar said no product should be marketed or promoted as ‘thermal grout’ unless its thermal characteristics are defined and acceptable for the intended use.
“Each mix design of thermal grout is different and is based on several requirements: thermal conductivity, flow (time of efflux), strength, rate of hardening and heat of hydration,” said Parmar.
Two essential characteristics of thermal grout for underground power projects are flowability and pumpability, terms that are not interchangeable. A mix may “flow,” but not be easily pumped.
From the installation viewpoint,” Parmar explained, “flow and pumpability are related and are the governing factors for limiting pumping pressure and rate of pumping. Various other factors such as the total distance to be pumped, size of the casing, number of ducts, spacers, change in elevation, etc., must be taken into account because they all contribute to the total resistance to pumping. From the grout installer’s view-point, flow and pumpability are of primary importance for any project.”
For most civil engineering applications only the flow and strength may be of interest, Parmar added.
“In order to specify/spec a thermal grout the engineer must have a clear understanding of what is required (material), why is it required (performance) and how it should be installed (process). Design of the thermal grout must be conducted by ‘experienced’ person; taking into consideration the thermal, mechanical and project specific requirements. The material supplier and installer must be equally knowledgeable and experienced to understand the requirements and means of delivering them. A successful demonstration of the material and the process prior to the actual installation will gain the confidence of the owners and consulting engineers.”
Industry sources expect the number of projects including underground power transmission lines to steadily increase. Buried 230 kV lines are not uncommon in the United States, and several 345 kV have been made. In Asia and Europe, transmission networks are in operations that contain 400 kV and 500 kV underground segments.
“One thing I can say for certain,” said Dickes, “the amount of knowledge developed in thermal grouting construction technology has grown by orders of magnitude over the last several years. Owners and engineers need to know that long distance thermal grouting of underground casings has been performed successfully in the United States.”
Dickes is participating in planning of a project now that will include 3,000 feet of 230 kV underground transmission lines in an uncased bore. Geotherm and Constellation Group have developed the specified thermal grout for this project during the summer of 2010.
FOR MORE INFORMATION:
Constellation Group LLC, (410) 484 0672; www.cgllc.us
Comments