December 2010 Vol. 65 No. 12
Features
Cobble Presents Unusual Complications For Drilling
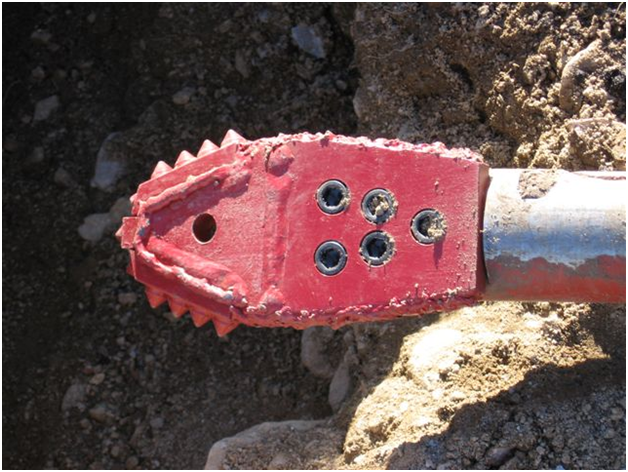
Cobble — usually rounded pieces of rock that can range in size from a marble to a basketball — is considered one of the most difficult and challenging soil conditions for making a directional drilling installation.
“Cobble is not fun,” said Boyd Simon, P.E., field services division manager for Ranger Directional Drilling.
“It’s hard to work through both for the pilot hole and during pullback — cobble lodges in the bit or reamer. It’s hard to keep the hole open because loose pieces keep falling in. It’s also hard to get mud where it needs to be, and cobble is very difficult to bring out of the hole.”
Special downhole tools are available for cobble projects, and using the right fluid additives properly mixed is more important when drilling in cobble than in “dirt” formations.
Representatives of three manufacturers discuss cobble and products available to drill in cobble conditions.
Ditch Witch, Richard Levings, senior product manager: Glacial till — popularly known as cobble — was created by rocks rolling in glaciers which formed a rounded and hardened rock. It is usually in layers and can be quite difficult to penetrate and hold open when directional drilling. These formations sometimes will have soil, sand or loam in between them. They are present all around the world, but are most prevalent in the northwest and southeast U.S., southwest and southeast Canada and Alaska, and in some mountain regions of the U.S.
Cobble is extremely hard and very difficult to cut, making directional drilling difficult. During drilling, cobble pieces move and therefore rock bits cannot penetrate them because of the constant movement; instead of being cut, pieces of cobble roll away and do not stay in place. Ditch Witch offers both drilling bits and backreamers designed to be effective in cobble, but most effective, we believe is the All Terrain drilling system.
The cutting structure of the reamers are designed to have low contact points to be more of a displacement and wear mechanism rather than an actual cutting surface on the reamer. As stated before, cobble is displaced, not cut; therefore, trying to use dirt reamers in cobble is futile.
The most effective way we know for drilling in cobble is the All Terrain (AT) drilling system. With this two-shaft system, the power of the inner shaft, combined with slow rotation, helps maintain a straight bore path in cobble with the outer pipe controlling steering. In addition, we offer a cobble pipe that is close to a flush pipe which reduces the drag when the cobble falls back in on the drill pipe.
The amount of cobble in a bore path will limit the effective bore length on a directional drill — the longer the bore, the more the exposure to the risk of bore hole collapse. It is wise to keep the bores to 250 to 300 feet, if possible.
Drilling fluid mixes are important in every directional drill application, but the proper additive mix is absolutely essential when in cobble. Most difficult are cobble formations that have no soil or sand to hold in fluid.
The cost of drilling in cobble can be excessive due to extremely high wear of ground-engaging components. Therefore, it is important to take this into consideration during the bidding process.
When considering a job with cobble in an area where a company has no experience, local drillers and equipment dealers can be sources of information about what’s required to be successful.
Melfred Borzall, Peter Melsheimer, marketing director: When drilling the pilot bore, the main problem is maintaining grade or making changes in direction — the cobbles bounce around the bit making it very difficult to hold line and grade. During pullback, the main problem coming back through cobble is with hole stabilization. Sometimes it is not possible to make the drilling fluid thick enough to keep the hole entirely open. Special backreamers and pulling heads must be utilized to force the cobbles into the wall of the hole while the product pipe is being pulled in.
Tooling for cobbles is different from those designed for dirt conditions in several ways. First, they must be built incredibly tough. They have to not only wear well in abrasive conditions, but also be able to withstand impact and shock against rocks. Next, they need to be able to attack the rock gradually. A bit should have a taper, gradually increasing in diameter.
Our Steep Taper UltraBit 3 blade comes to a steep point to help “wobble” through the cobbles. The point, combined with the position and type of carbide cutters, allows the operator to rock the bit back and forth and wobble in between the cobble stones. There is a massive amount of carbide granule-impregnated hard facing on all wear edges to help increase the life of the bit.
The Ogre backreamer is unlike any other reamer on the market. There a large number of carbide cutters spiraled around the reamer so that each cutter is only doing a portion of the work. This helps ensure that even in cobble conditions, the reamer runs as smoothly as possible. The gradual taper also aids in forcing any cobbles that cannot pass through the deep flutes to be pressed into the wall of the borehole.
When estimating costs for jobs that contain cobble, contractors must be careful not to bid too low. Expect production to go slow and expect more than normal wear on tools. Be proactive and get the right tools to provide an edge from the start. Be patient, and ask for help from tooling, rig and drill mud suppliers.
Vermeer, Chris Fontana, cutting edge/attachment parts sales manager: Cobble can define many different conditions. It may be a loose conglomerate of glacial stones or glacial till sized from pea sized to basketball sized, mixed with sand and soils to create the condition, or packed tightly from thousands of years of compression which we term “cemented cobble.” Or it can be a conglomerate of broken or fractured sandstone, limestone or other rock that has been reclaimed, replaced or used for fill in construction or other similar application.
Maintaining the pilot bore plan in cobble is difficult as the bit deflects off oversized cobble, thus changing the bore path. Great care and patience is needed as to not deflect and oversteer drill pipe, thus damaging, breaking and potentially loosing pilot bore tooling. Vermeer offers several varying sizes and styles of pilot bore bits designed not only to provide maximum performance in cobble, but added wearability. In addition, a higher-end product specifically designed for cobble pilot bores is effective and designed to minimize deflection in the hole. It gives the operator greater control of the bore path requiring fewer corrections.
The challenges during backreaming and product installation are dependent on product size of the majority of the cobble. Most of the time in cobble, the hole will not stay open during backreaming. No matter how much drill fluid and other additives are used, the viscosity will not be stout enough to hold large rocks and stones to the bore wall and bring them out of the hole. Also, it must be determined that the product being installed can withstand the weight and pressures the cobble presents. A bore may have to be broken up in several shorter segments as to minimize the damage to the product installed as it is “muscled” through the ground as the cobble temporarily is displaced.
Vermeer offers several variations of reamers that are effective in cobble, from fluted cast-bodied reamers with oversized carbide tooling to gradual tapered reamers with less aggressive tooling. Vermeer also customizes reamers to the specific ground conditions, including cobble, to match machine, product and bore path. For larger-sized product, we suggest adding a long pipe extension welded to the reamer to bridge the gap from product to reamer. Cobble will tend to fall in between and create higher pulling forces, potentially locking swivel and product.
FOR MORE INFO:
Ranger Field Services,(337) 837-5447, www.rangerdirectional.com
Ditch Witch, (800) 654-6481, www.ditchwitch.com
Melfred Borzall, (800) 558-7500, www.melfredborzall.com
Vermeer Corp., (888) 837-6337, www.vermeer.com
Comments