September 2009 Vol. 64 No. 9
Newsline
JEA Takes Lead In Proactive Sewer, Water Maintenance
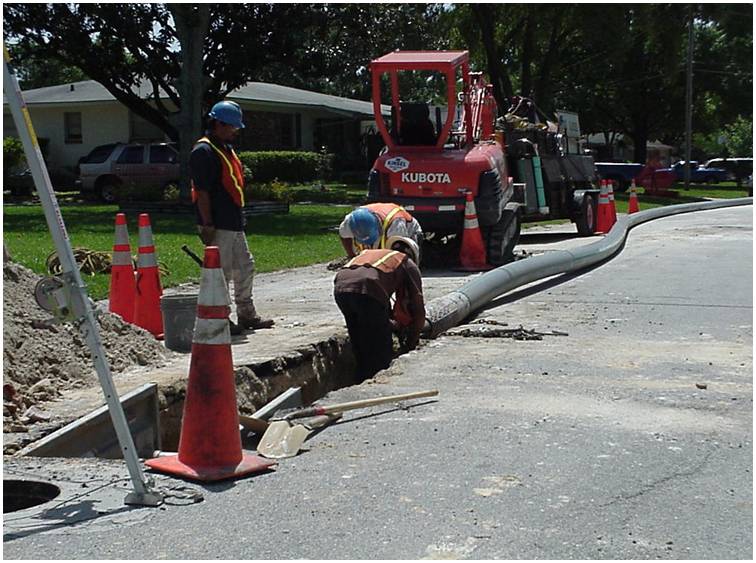
Most major American cities today face multiple challenges to provide basic water and sanitary services.
Short on funds and under Environmental Protection Agency (EPA) mandates, many municipalities struggle to keep systems operational and expand them to meet increasing demand. It must seem to many system owners and managers that they are too busy reacting to crises to ever develop a program within budget limitations to make necessary repairs, maintain operations and plan and fund construction for future needs.
In Florida, JEA, the city of Jacksonville’s municipally owned utility, provides a textbook example of how modern planning tools correctly employed can be used to develop comprehensive programs and perform repairs and rehabilitation to keep services running smoothly and customers satisfied.
While the focus of this report is on JEA’s sanitary sewer system, the authority also provides reclaim water and electrical services to Jacksonville and portions of three adjacent counties in the northeast section of the state. JEA is the eighth largest public electric utility in the United States and second largest water/wastewater utility in Florida.
The wastewater system serves 229,000 customers. It has a 124 million gallon per day (gpd) treatment capacity and accommodates an average daily flow of 78 million gpd. The system has 15 wastewater treatment facilities, 1,246 pump stations, five vacuum stations, 64 biosolids pelletizing facilities, 3,400 miles of pipe and 54,000 manholes.
Six Sigma
JEA planning is based on root cause analysis to determine the best use of available funding, said Scott Kelly, P.E., JEA vice president of water and wastewater systems. The word “root” in this context doesn’t mean the roots that invade sewer pipes, but the primary sources or origins of problems.
“It is very complex,” Kelly continued. “JEA incorporates a Six Sigma approach to problem solving and how to address problems. It involves the extensive use of statistical analysis, starting with locating problems all the way through estimating project costs.”
Six Sigma is a business management strategy widely used to improve processes and identify and correct system deficiencies. JEA uses teams of full time specialists identified as “Black Belts” from within JEA, who are trained in the use of Six Sigma.
In 2007, JEA was recognized by the International Productivity and Quality Center (IPQC) for the best Six Sigma Project in a government agency. IPQC also recognized JEA in 2008 for Best Fast Track Project and, in 2009, for Best Service Project.
“Six Sigma embraces a philosophy of continuous improvement through a deepening understanding of root causes of problems and targeted approaches to maximize improvements,” Kelly explained.
An example of how Six Sigma is applied to sanitary sewer system management is the way JEA responds to sanitary sewer overflows (SSOs) and sanitary sewer events (SSEs). Under Florida law, SSOs are overflows that reach waters of the state. Overflows are defined as exceeding 1,000 gallons or that could impact public health. While SSEs do not meet these criteria and are not reportable, JEA gathers data as part of the Six Sigma data driven approach to address the underlying root causes of problems.
“JEA has significantly advanced the development and implementation of the management, operation and maintenance programs to achieve its goal of zero preventable overflows,” said Kelly
ID problems, solutions
JEA has established a formally functioning Root Cause Committee.
“This committee meets biweekly to review every SSE and SSO,” Kelly said. “They identify the root cause and determine short- and long term corrective action to prevent reoccurrence. They also identify any improvements that can be made to reporting procedures. This information is tracked in the PCAN (preventive and corrective act notification) data base through to completion of remediation steps.”
Kelly describes the process: When a complaint or notice comes into JEA, a first responder checks on the incident, notifies the ERC, and works with a follow up crew to determine what must be done to alleviate the situation. If it involves an SSE or SSO, a crew recovers the spill and cleans up the area using lime for disinfection and odor control. The First Responders arrive within 45 minutes of the initial call. They have special equipment that is capable of unstopping sewers and preventing or minimizing SSEs or SSOs. If the event is an SSE or SSO, proper reporting follows. If the spill has reached a water body, appropriate water quality testing is performed.
SSEs are reported through the Discharge Monitoring Report (DMR) to the Florida Department of Environmental Protection (FDEP) and are recorded. SSOs are reported to the State Warning Point within 24 hours and are also recorded.
These reports are made by JEA’s Environmental Services Department. Reports include the location of the SSE or SSO, name of the surface water body if applicable, date and time of the incident, the initial suspected cause, estimated volume involved, and steps taken during the incident and subsequent to it. The FDEP makes decisions as to any other notifications that are needed for the specific incident. In cases that pose a potential danger, warning signs are posted as appropriate to the incident. Records of each incident are retained in the PCAN data base. The department uses an online PowerPoint training course that helps first responders estimate overflow volume.
JEA’s Environmental Services Department conducts monthly quality control checks on all events to ensure all events and agency notifications are documented. A quarterly meeting is held to review and evaluate notification processes for all reportable events during the previous quarter. This meeting includes JEA, city of Jacksonville’s Environmental Resource Management Department and FDEP.
The scope of Six Sigma impact extends far beyond SSO and SSE responses. Kelly describes several other initiatives identified from data analysis:
Other initiatives
The “Pop Top” manhole inspection program is designed to detect potential problems and to take corrective action before a SSO or SSE occurs. Targeting high risk areas by using JEA geographic information system (GIS), in a period of one year 27,747 manholes were inspected by the program and more than 3,000 were repaired.
Rehabilitation of manholes is made with fiberglass liners and polyurethane spray. When conditions dictate, manholes are replaced.
JEA implements an aggressive gravity line inspection and repair program that includes scheduled cleaning of pipes and sewer line replacement.
For many pipe rehabilitation and replacement projects, trenchless construction technologies are utilized. Between 2000 and 2007, more than 280 miles of gravity flow mains were replaced by pipebursting at a cost of more than $200 million. In the same period, more than 50 miles of pipe were lined by cured in place pipe (CIPP) procedures at a cost of more than $20 million.
The authority maintains contracts for CIPP and pipebursting for short term response situations.
Kelly said trenchless construction allows replacement of underground pipe with minimal disruption of the surrounding community and environment. It also is more efficient than the traditional open cut method. By using trenchless methods such as pipebursting and CIPP, JEA has improved sewer service to more than 18,000 customers with minimal disruption.
Other elements for sustaining JEA’s sanitary sewer system include air release valve testing, SCADA enhancements, methods of determining and marking flow direction in gravity flow mains, and programs to limit grease related SSOs.
Kelley advises that companies considering using Six Sigma should understand one thing: you can’t buy Six Sigma.
“You must buy into Six Sigma,” he explained. “The buy in must begin at the highest levels of the organization. Change and improvement do not normally occur by chance. Companies get better and stronger because people make a commitment to improve quality and the business processes that deliver it. Executive leaders must recognize that difficult and complex problems often have multiple root causes and are not often solved overnight.
“Six Sigma is a philosophy that involves setting stretch goals and continuing to improve processes and move performance closer to perfection.”
FOR MORE INFORMATION:
JEA, www.jea.com
Comments