September 2009 Vol. 64 No. 9
Features
Corrosive Environment Forces Innovative Solutions In Denver
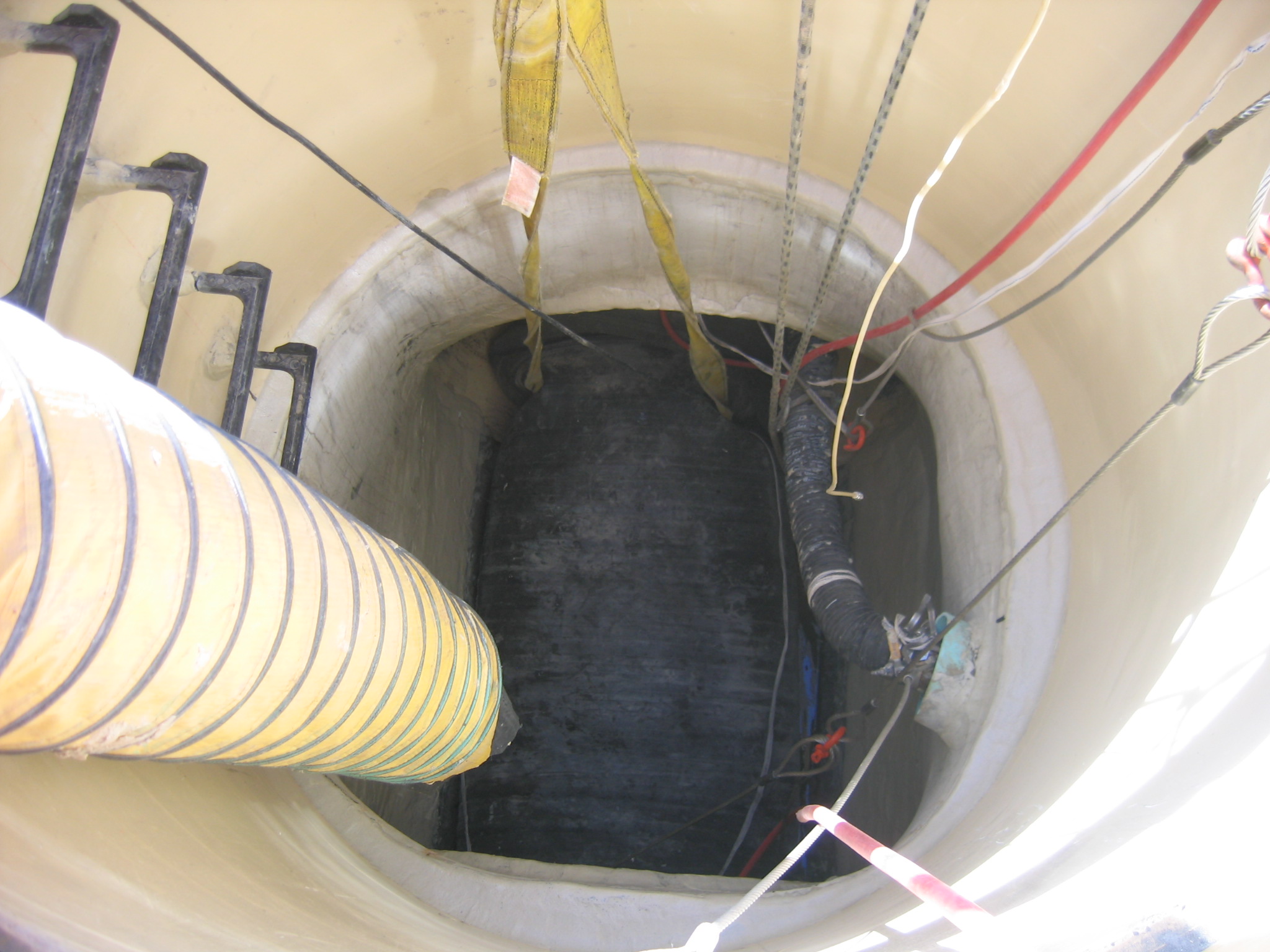
The Metro Wastewater Reclamation District (MWRD) of Denver, CO, successfully completed a significant manhole rehabilitation project on its South Thornton Interceptor this past summer.
The interceptor operates in one of the district’s most challenging environments with levels of hydrogen sulfide gas in areas as high as 1,000 parts per million (ppm), significant flows and extensive concrete corrosion throughout the five-mile-long wastewater pipeline.
The project included rehabilitation of 49 manholes and was completed using an epoxy system to coat rebuilt base, benches and invert areas and the installation of fully structural composite manhole inserts.
Designed in house by the MWRD engineering department, the project was the culmination of research and efforts to find the most corrosion resistant, structural rehabilitation products and the best qualified contractor to install these products in the severe environment of the South Thornton Interceptor. Contractor on the project was Fisher Company Inc.
“We are very pleased with the outcome of this latest manhole rehabilitation effort,” said Jeff Maier, P.E. , MWRD project manager and lead design engineer for the South Thornton Interceptor Manhole Remediation Project. “The South Thornton Interceptor has been challenging for us given its extremely corrosive environment and high flows. The contractor, Fisher Company, did an excellent job.”
Work on the project began in August 2008 and was completed in July 2009. The project included the use of innovative wastewater flow management techniques throughout the interceptor and in-pipe diameters ranging from 36 to 60 inches, carrying average daily flows of 6 to 14 million gallons per day (mgd), with peak flows exceeding 20 mgd.
Anything but ordinary
To completely and correctly rehabilitate the 49 manholes involved many challenges, starting in design and finishing with the successful installation of SewerShield epoxy and fully structural SewerShield corrosion resistant, composite manhole inserts.
“This was not your basic manhole rehabilitation project – it was much more extreme – and we did not use basic manhole rehabilitation products or processes,” said Charlie S. Fisher, Fisher Company business development director. “The severely corrosive environment and dangerous hydrogen sulfide levels posed major obstacles in making sure this project was done well and in a safe manner.”
Due to its limited grade and numerous force main connections throughout, the South Thornton Interceptor has significantly higher levels of hydrogen sulfide gas and consequently more severe corrosion than other interceptors in the Denver metro area. Levels of hydrogen sulfide gas in the Interceptor typically range from 50 parts per million (ppm) to 1,000 ppm, depending on the temperature, time of day and day of the week.
Structures ranged from six to 39 feet in depth with diameters from five to 8 feet. All were considered to be in poor condition prior to this project and a high priority need for rehabilitation.
The structures previously had been coated or lined with as many as three other rehabilitation/protective coating products that had all failed in the severe conditions. Maier said the failures of these previous rehabilitation efforts prompted MWRD to develop and implement a comprehensive, in house rehabilitation product evaluation/approval program to seek out quality products that could withstand severe wastewater conditions and identify applicator contractors that provide top quality workmanship. Maier said SewerShield and Fisher Company were found through this program. To date, he added, six rehabilitation product manufacturers and their respective applicators have been approved for use on MWRD projects.
The first challenge to getting the project under way was the bypass system to accommodate flow during construction.
“Bid documents for this project required complete bypass pumping,” Fisher said. “However, Fisher Company was able to provide the client a substantial cost savings through use of alternate wastewater flow management methods, developing a wastewater flow management plan utilizing flow though plugs and piping to manage flows including those from numerous incoming force mains. Fisher Company project managers worked closely with Plug It Products on the development and design of plugs and fittings to meet the exact needs for this project and interceptor system.”
Advantages
The advantages of Fisher Company’s approach were realized almost immediately from both financially and operational standpoints.
“Because Fisher Company was thinking outside the box regarding flow management methods,” said MWRD’s Maier, “we were able to use a higher quality rehabilitation product that might have otherwise been too expensive, effectively utilizing the cost savings that would have instead been spent on unproductive bypass pumping. At Metro Wastewater, we encourage innovative thinking and creative problem solving to make the most of every rate payer dollar.”
Because of the severe condition of the manholes, Fisher Company proposed using fully structural SewerShield composite manhole inserts on all standard manholes which would virtually eliminate existing manhole barrel sections and cones.
After rebuilding base, benches and invert areas, SewerShield 100 epoxy was applied (see below for a step-by-step description of the rehabilitation process).
SewerShield 100 is a 100 percent solids solvent free epoxy system designed with 98 percent acid resistance and providing superior performance in adverse wastewater environments. In addition to manholes, it is used for applications that include wet wells, grit chambers, headwork channels, clarifiers, acid containment, thickeners, sewage piping, floors and other areas exposed to hydrogen sulfide.
SewerShield composite manhole inserts are manufactured using the same SewerShield 100 and SewerShield 150 epoxy resins reinforced with fiberglass to provide a stand alone manhole system that is H 20 load certified.
“Overall,” said Maier, “we are very happy with the expert workmanship, innovative thinking and attention to detail that Fisher Company provided Metro Wastewater on this challenging project. The SewerShield epoxy and composite manhole inserts are rehabilitation products of the highest quality, designed to withstand severe wastewater conditions and corrosive environments. I am confident that we have finally installed a permanent, structural rehabilitation solution to the South Thornton Interceptor corrosion problems.”
Fisher Company Inc., Granby CO, is an infrastructure construction services company certified to install a variety of structural lining products designed for highly corrosive environments in both new and existing structures. Fisher Company promotes its rehabilitation processes as having the potential for a cost savings to project owners with minimal impact to existing facilities. Fisher Company is a certified applicator for Environmental Coatings and SewerShield composite products.
The Metro Wastewater Reclamation District is the wastewater treatment authority for most of metropolitan Denver. It was formed by the Colorado state legislature in 1961 to provide wastewater transmission and treatment services to its member municipalities and special connectors in compliance with federal, state and local laws. These municipalities and connectors, in turn, provide retail wastewater services to approximately 1.6 million people in a 615 square mile service area. MWRD collects and treats about 140 million gallons of wastewater per day. There are approximately 4,500 manholes and 232 miles of pipe in Metro’s trunk line sewer system.
SewerShield products are manufactured by Environmental Coatings, LLC, Mesa, AZ. Environmental Coatings is a wholly owned subsidiary of JPCI Services and provides products and services for municipal water and wastewater system rehabilitation. JPCI has also provided consultation, specification, and troubleshooting services for many cities, companies and engineering firms.
Steps In The Structure Rehab Process
Rehabilitating structures in the South Thornton Interceptor Manhole Remediation project included these basic steps, said Charlie Fisher of Fisher Company.
After establishing necessary traffic control:
- A saw cut in surface pavement was made to expose the perimeter of the existing manhole barrel;
- Excavating around the existing cone section allowed removal of the cone;
- The plug assembly was installed to manage wastewater flows;
- Existing coatings and liners were removed from base sections and the invert area;
- Complete surface preparation of base, benches and invert area by abrasive blasting and pressure washing;
- Base, benches and invert area were rebuilt with C 120 calcium aluminate mortar and applicable reinforcing bars;
- SewerShield 100 epoxy was applied to rebuilt portions of the structure;
- Plug assemblies were removed to restore flows to rehabilitated invert;
- The SewerShield composite manhole insert (barrel and cone section) was installed; inserts were specifically manufactured for each structure;
- Annular spacing between the existing structure and new composite insert were filled with hydrophobic polyurethane grout;
- Backfill around new composite cone sections was completed and paved surfaces restored;
- And last, coated surfaces were spark tested and visually inspected in the presence of a project owner representative to detect any pinholes, which were patched as necessary.
FOR MORE INFORMATION:
Fisher Company Inc., (970) 887-9006, www.fishercompanyinc.com
SewerShield by Environmental Coatings, (480) 984-7608, www.sewershield.com
Plug-It Products, (800) 575-8448, www.plugitproducts.com
Comments