November 2009 Vol. 64 No. 11
Features
Specifying Backhoes For Maximum Versatility
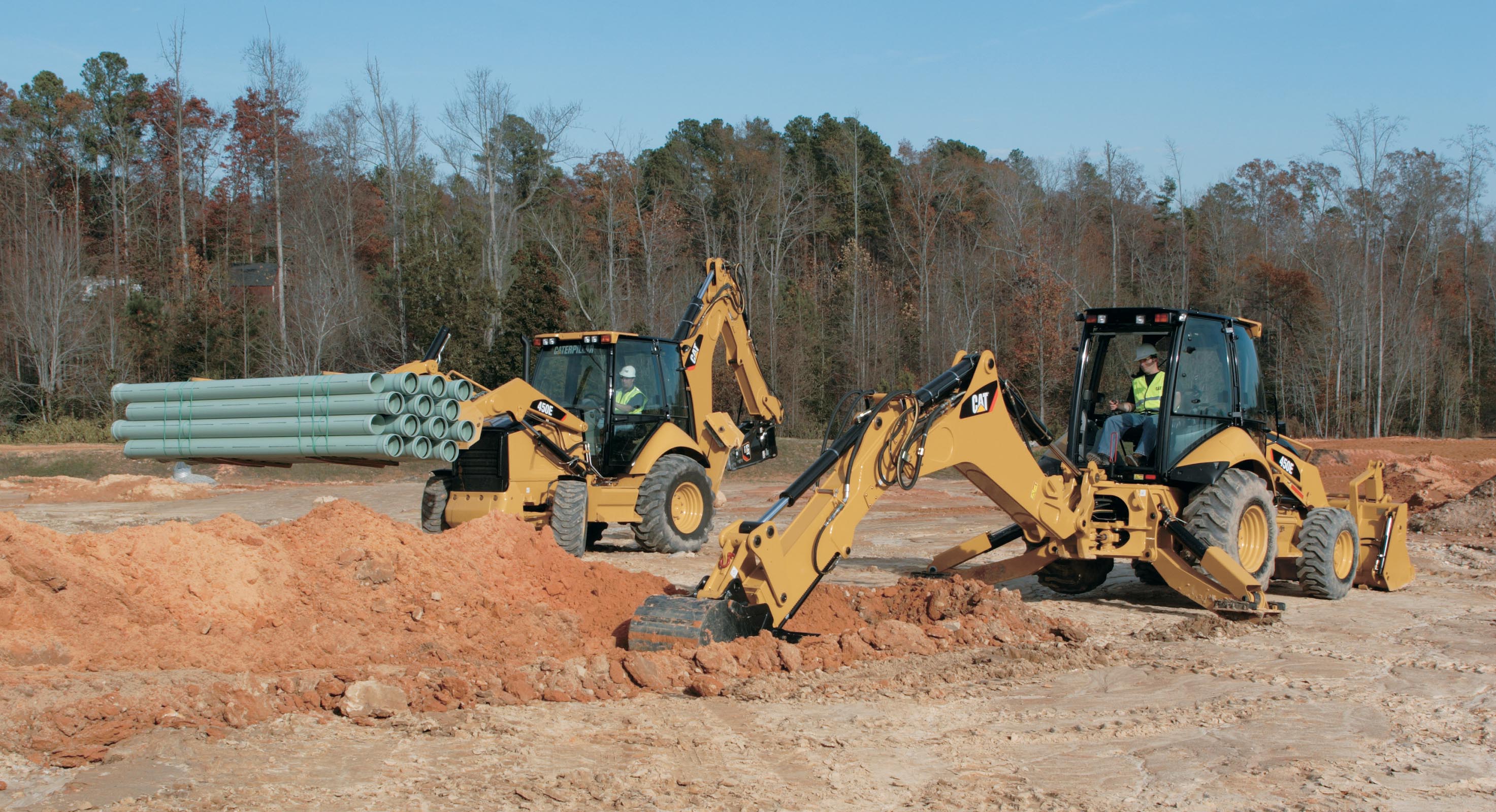
The backhoe loader is really two machines in one, and the specifying process is twice as important.
Backhoe loaders are among the most versatile construction machines around, so contractors must consider many factors, whether they are purchasing or renting a machine. Choosing the right model is much like selecting a separate compact front end loader and mini excavator.
The first decision is whether or not the backhoe suits the job to begin with. Scott Cowan, president of Knox Tenn Rental in Knoxville, TN, points out that the most likely substitute for excavation is the mini excavator, which has seen increased adoption in recent years. Cowan, whose company rents Allmand Bros. and John Deere backhoes, points out that stability is an advantage to the backhoe. He adds that the backhoe provides tremendous mobility and often can be driven from one site to another nearby without the need for a trailer. The backhoe also can haul material in the front bucket, he adds.
Marcello Bargellini, product specialist for Volvo Construction Equipment, adds that backhoes can travel upwards of 20 mph. For jobs that do not involve operation in tight spaces or extremely hilly terrain, the backhoe is the right choice and can dig, backfill, grade, crane, load and unload, and perform other functions. Tom Reith, product manager for Terex Construction Americas, adds site preparation, trenching, installing, concrete breakup, posthole digging and site cleanup.
The next step is choosing the right model. The primary rating criterion in North America is digging depth, notes Bargellini. This is the maximum distance achievable from the ground line to below grade at the tips of the bucket teeth and typically is expressed as “digging depth 2 foot flat bottom” and “8 foot flat bottom.” These expressions refer to a flat bottom trench that is excavated two-feet deep and eight-feet long. Standard rated digging depths are 14, 15, 16 and 17 feet. Bargellini reports that the most popular dig depth segment is 14 feet, the rating of about 80 percent of all backhoes sold in North America. In the past few years, he adds, the 15 foot dig depth backhoe has been gaining in popularity. Making up most of the remainder of the market, he adds, are “compact backhoes” with dig depths of 8 to 13 feet.
Starting points
The contractor should first select a backhoe by dig depth class and price range and by various features, options, specifications and attachments that are appropriate for most projects, Bargellini says. Other important items are productivity, fuel efficiency, safety, serviceability, operator comfort and dealer service support, he adds. Paul Grohsmeyer, backhoe loader marketing manager for Caterpillar Inc., notes that adding an extendable stick to the rear boom can expand the digging depth by up to four feet. Another variable affecting the digging depth is the bucket size, Grohsmeyer adds.
One of the most important specifications is backhoe bucket breakout, or digging, force, according to Bargellini. This is the maximum calculated force in pounds applied at the tip of the bucket teeth. Calculations are based on the highest system relief valve setting. Both the bucket digging force and dipper digging force are factors in determining work output. The other factor that determines output, Bargellini says, is speed, which is determined by available hydraulic flow. Lowell Stout, senior product manager, and Reith of Terex Construction America prioritize horsepower, bucket breakout force and stick force because all of these contribute to the machine’s ability to move and lift material, says Stout. Knowledge of typical soil types is valuable in determining the necessary bucket or stick breakout force. Although horsepower affects how quickly the machine can work, the right power to weight ratio is a more accurate predictor of productivity.
In recent years, manufacturers have been developing more powerful and intelligent hydraulics. Bargellini notes that almost all manufacturers now offer optional or standard pilot controls as opposed to mechanical “wobble sticks.” Besides being light to the touch and less tiring for the operator, pilot control joysticks can be converted from backhoe to excavator control with a switch of a lever, usually located inside the cab.
Digging depth and capacity are two items to specify early in the decision process. An issue related to digging depth, and often considered a factor in productivity, is the reach of the rear boom because the greater the machine’s reach, the less often it needs to be repositioned during trenching operations. Bargellini notes that reach from the swing pivot is measured as the distance, at the ground line, from the backhoe swing pin line to the end of the bucket teeth with the backhoe fully extended.
Contractors can get greater digging depth with the extendable stick and this feature also provides greater horizontal reach, Grohsmeyer notes. This greater reach allows digging a longer trench in fewer machine redeployments and after the final pass, the operator can backfill by reaching across the spoil pile. Cowan adds that some advancements have addressed machine stability, such as wider footprints, lower profiles and lower centers of gravity.
Determining the appropriate machine configuration for typical jobs is also important, Stout says. The contractor should consider specifying an extendable stick and perhaps a multi purpose bucket for the front of the machine, depending on need. Determining what the machine’s carrying capacity is, as well as the size of buckets and their possible compatibility with specialty buckets such as clam style 4 in 1s, side dumpers and logging buckets equipped with grapples on the front aid in matching the backhoe to the typical project.
The machine’s physical and operating dimensions are an important consideration, according to Bargellini. The dimensions are important relative to typical working area footprints and nearby obstructions. These dimensions include overall length, overall width, ground clearance, operating height, bucket rotation, dump height, wheelbase, overall and bucket width, operating weight, cycle times (raise, lower, dump) and front and rear axle load rating (static and dynamic).
Recently, fuel costs have become a major concern for contractors. Bargellini cautions that fuel efficiency varies greatly in backhoes because it depends on how the machine is operated and how it is equipped. For example, it might be used mostly in excavation work, loading work or driven for long distances. Closed center, load sensing systems with variable displacement piston pumps in their backhoes now are being used versus open center systems with fixed displacement gear pumps. The former configuration is usually more fuel efficient, Bargellini points out, because it supplies oil only “on demand,” meaning when the load sensing system on the pump detects that oil flow is not required, the system reduces pump flow and horsepower to conserve fuel.
Jeff Aubrey, product manager for Komatsu America, says that the contractor should try to determine if limitations to size and weight of the machine exist relative to truck and trailer capacities. Also, the contractor should think ahead to determine what the backhoe’s future requirements might be, particularly in regard to attachments because auxiliary hydraulics capable of providing adequate pressure and flow to run those attachments might be necessary.
Differentiating features
Manufacturers are responding to increasingly sophisticated marketplace demands and differentiating their equipment.
For several years, in response to marketplace concerns about worker retention and an OSHA focus on ergonomics, manufacturers have devoted more time and effort to the operator cab. The use of servo hydraulics, Cowan notes, has gone a long way toward making control of the front and rear components smoother and less tiring for the operator.
Bargellini notes that fingertip control possible via the use of pilot controls is just one recent fatigue reducing advancement. Seats are available in heavy duty or air suspension versions and often have an available heat switch. Aubrey adds that the seat and controls are commonly adjustable now, allowing each operator to work in a customized position. Other features that contribute to operator comfort, Bargellini adds, include tilt steering, separate heating and air conditioning systems, a one piece excavator style rear window and flat cab glass that opens partially or fully.
Another example of an operator comfort driven development is Caterpillar’s addition of fully automatic shifting mode on power shift transmissions, says Grohsmeyer. Because the operator does not have to shift from first to second gear in this mode, more attention can be paid to machine functions outside of shifting. This feature also allows the operator to put the machine into an automatic ride control mode to drive the machine over medium distances.
Advancements in machine and operator safety have similarly grown in recent years. Aubrey notes that manufacturers have been focusing on noise levels, operational and safety labeling, and backup alarms. For road use, work lights, highway lights, turn signal lights, emergency flashers and rotating beacons are also available. The market has also enhanced the operator’s ability to view obstacles out the front, side and rear of the machine, Aubrey adds.
Grohsmeyer notes that seemingly minor design features such as proper openings, steps and handles for operator ingress and egress have become more common. Other items include wear resistant punched steel skid plates and an overall increase in cab space. A major safety advancement in recent years as machine speeds of 25 mph are now common, Grohsmeyer notes, is more powerful braking systems such as commonly available power boost brakes.
These machines’ high versatility and dual functionality have led manufacturers to focus a great deal upon maneuverability in tight spaces. Bargellini says that the best indicator of maneuverability is expressed as turning radius or “curb turning circle,” the maximum diameter of the tire path at the track, or center, of the tire. Manufacturers have published turning circles with and without brakes applied, he notes.
Four wheel drive is a key tool in machine maneuverability because it provides access to work areas that a two wheel drive machine would have difficulty negotiating. It also improves loader performance by providing additional loading effort going into the pile. Another key maneuverability enhancing feature is all wheel steer, which gives larger loaders comparable performance to small front end loaders in this area. Many manufacturers have addressed machine length, notes Grohsmeyer. For example, he says, many have reduced machine length by pulling the rear boom tighter to the machine body to provide better stability when the front bucket is used.
Increasingly, contractors have viewed their machines as financial assets as much as workhorses. Keeping them moving dirt is a key to company profitability, so uptime is at a premium and manufacturers have responded to this demand by minimizing the need for maintenance of some components and making other required maintenance more efficient.
In the past five years or so, manufacturers have incorporated bearings that distribute grease around high pressure points, Grohsmeyer says. He points out that electronically controlled Tier III engines have made diagnostics more intelligent by providing the ability to pick more diagnostic information out of a machine and even allow trouble alerts to be sent to management wirelessly. Bargellini argues that if maintenance is not made easy, it will not get done. He points to developments that have addressed this concept, such as one piece, rear tilting hoods that can be opened with a latch rather than by unscrewing bolts and side panels; pivot joints that are designed to accept grease weekly rather than daily; and grease fittings (zerks) placed on one side of the machine for easier access. Cowan notes that lubrication intervals on bushings have increased.
FOR MORE INFORMATION:
John Deere, (309) 748-0114, www.johndeere.com
Case, (262) 636-6772, www.casece.com
Caterpillar, (309) 675-1000, www.cat.com
Volvo, (825) 650-2043, www.volvo.com
Comments