July 2009 Vol. 64 No. 7
Features
Encapsulation Method Keeps Valve Functioning, Seals Leaks
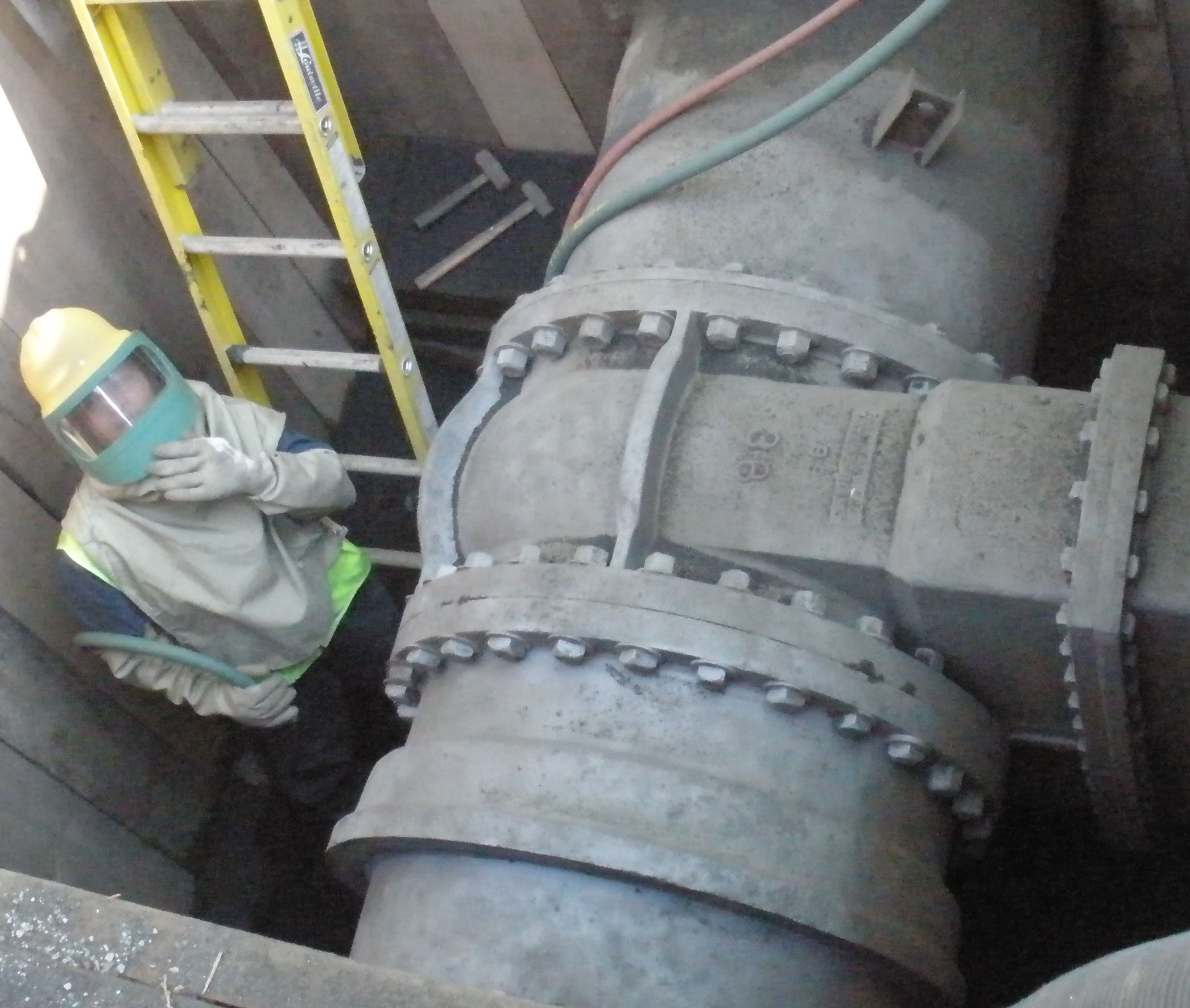
Trouble in underground infrastructure often occurs in difficult-to-access areas where making necessary repairs has the potential for disrupting normal activities.
That certainly was the case when the Public Service Electric and Gas Co. (PSE&G) discovered a leak in a 36 inch flange valve in its gas distribution system in Kearny, NJ. The valve was buried under about four feet of cover beneath a residential street.
PSE&G initiated a proactive approach to permanently fix the problem, said Vincent Guariglia, supervising engineer for the company’s Harrison Gas District.
Evaluation of the problem revealed three options, said Guariglia.
“We could have replaced the valve which would have required road closures for an extensive excavation and could have caused various municipal problems,” he said. “This solution also would have been very costly.
“The second option would be to cut the valve completely. However, this would have removed a critical point of control from the system, resulting in reduced system reliability in a critical situation.”
Course of action
The third option – and the one PSE&G decided to take – was to encapsulate the valve while maintaining system control and valve functionality. With this process, a two part polyurethane mixture surrounds and permanently seals leaking joints, compression couplings and distribution fittings.
“There were many benefits to this approach for this situation,” said Guariglia. “Sizes of excavations were minimized which reduced the expense of the project. It also left the
town content because it minimized road repairs and reduced the number of complaints from the public. However, in order to use the encapsulation method, valve functionality had to be maintained during construction.”
Guariglia explained that PSE&G has successfully used the encapsulation technique in the past, but the 36-inch valve is the largest ever done.
The project contractor the project was Miller Pipeline Corp. which used its Encapseal Safe-T-Seal system on the project. Guariglia said Miller Pipeline previously completed several encapsulation projects for PSE&G.
In order to encapsulate the valve, a mold had to be designed and fabricated. The first step in that process was to uncover the leaking valve. Steve Kasmin, Miller district manager, went on site, pinpointed the location of leaks, and obtained fitting measurements and other information to design the mold which would contain the flange valve but also one innertite joint.
After measurements were completed, the excavation was covered with plates.
“Creation of the mold to the project’s specifications is the most critical step in the process because there is little margin for error,” said Kasmin. “For a proper seal, the form for the mold had to be constructed to exact measurements specified in the design.”
The mold was constructed in four pieces and when assembled measured 4½ feet wide by 10-feet high. Produced entirely in house, Miller’s design, fabrication, paint and shipping departments devoted 200 hours to the project.
From the time the valve was exposed and measurements taken to its installation took about two months, said Guariglia. While the mold was being fabricated, permitting, out sourcing and other preparations were completed.
Prep
To prepare for installation of the mold, Miller crew members spent a day cleaning the valve. The mold was assembled, and nine crewmen mixed and poured the polyurethane sealant into the mold through four pressure pots. Work started early in the morning and was completed about midnight, using 314 gallons of sealant to fill the mold.
“Because Safe-T-Seal begins to gel in 15 minutes after mixing, coordination of the mixing and pouring process is critical,” said Kasmin.
The mold was disassembled and removed two days later, and tests confirmed there were no leaks.
Guariglia said the valve repair was successful.
“The leaks were stopped, the valve continued to function throughout the procedure, and there was little disturbance to the neighborhood,” he reported. “The town commended us for a job well done. Miller Pipeline has served us well on other projects and is familiar with PSE&G procedures. Miller personnel have the experience and ability to do the job right the first time, and came through with an effective solution for us.”
PSE&G is part of the Public Service Enterprise Group. It is one of the largest combined electric and gas companies in the United States and is also New Jersey’s oldest and largest publicly owned utility. Its service area comprises nearly 75 percent of New Jersey’s population across a 2,600 square mile service area that includes 2.1 million electric customers and 1.7 million gas customers in more than 300 urban, suburban, and rural communities, including the state’s six largest cities.
Founded in 1953, Miller Pipeline Corporation is one of the nation’s premier natural gas distribution, transmission pipeline and utility contractors, providing a comprehensive range of pipeline contracting and rehabilitation services for natural gas, liquids, water and wastewater pipelines. Specialty products and services for the industrial and telecommunication industries also are offered.
Miller is headquartered in Indianapolis, IN with offices nationwide and maintains hundreds of crews composed of skilled, professional, highly trained employees.
FOR MORE INFORMATION:
Miller Pipeline Corp., (800) 428-3742, www.millerpipeline.com
Comments