August 2009 Vol. 64 No. 8
Features
HDD Helps Producer Tap Gas Reserves Under DFW Airport
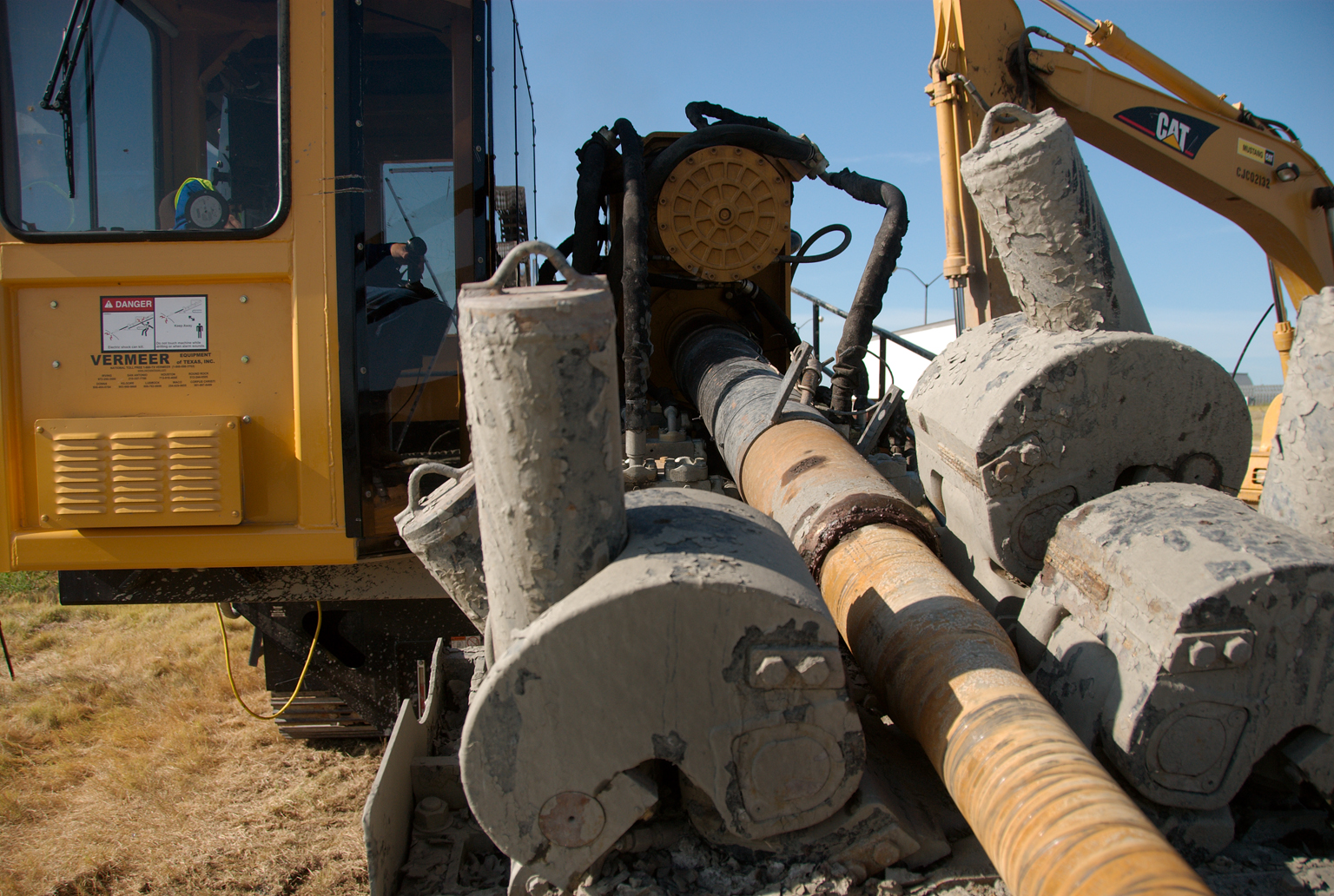
The Barnett Shale is among the nation’s fastest growing natural gas fields. The formation encompasses more than 5,000 square miles and stretches from Dallas to Fort Worth, TX.
With estimated natural gas resources in excess of 30 Tcf, the potential contribution of this formation as an energy source is immense.
Coined an “unconventional” deposit by geologists, the shale that comprises this vast natural gas reservoir is very hard, making it difficult to produce economically in commercial quantities. As if the geometric composition weren’t challenging enough, development has also been hampered by the fact that major portions of the field lay beneath the most densely populated areas of North Texas most notably, the Dallas Fort Worth metroplex. But recent technological improvements in hydraulic fracturing and horizontal directional drilling (HDD) techniques have since changed all that.
Among the largest lease offerings located within the Barnett Shale was an 18,000 acre tract encompassing Dallas Fort Worth International Airport. The airport authority awarded the lease and drilling rights to Chesapeake Energy, one of the nation’s largest producers of natural gas. Chesapeake selected Dallas based Driver Pipeline to tackle the complicated task of installing an intricate pipeline system to transport the natural gas produced from beneath the third busiest airport in the world. Driver Pipeline was well positioned to complete the pipeline work, having more than 800 employees and a fleet of equipment that numbers over 300.
The project involves installing a 24 inch pipeline around the parameter of the airport and a gathering line consisting of 8 24 inch lateral lines to channel the extracted natural gas from an estimated 100 wells. The gathering line transports the gas to a compressor station located on the north side of the airport which functions to pressurize the gas before moving on to another pipeline for distribution and delivery to market. There will also be a 10 inch line to take saltwater back to injection wells and both 10 and 12 inch lines to carry fresh water to the wells.
The entire saltwater gathering line is composed of 50 foot polyethylene links that were fused together using a poly fusion machine and installed using advanced HDD techniques. The various bores range from 15 65 feet in depth, depending on what Driver’s crews encounter underground. When complete, the gathering line plus additional feeder lines will total over 100 miles in length.
“As you can imagine, there are numerous logistical challenges involved with installing such an intricate pipeline system under one of the world’s busiest airports,” said Scott Driver, vice president of operations for Driver Pipeline. “The only way this project could be completed is by using HDD since what lies on the surface is a network of runways, terminals and cargo facilities. And that just describes the surface. What lies underneath presents another set of challenges.”
From the ground up (subhed)
Geological surveys completed prior to beginning the installation showed that the ground conditions and composition of the subsurface soils varied a great deal. According to Driver, the project started out in black gumbo like dirt and moved to red clay with sandstone layers. Opposite the starting point, Driver’s crews encountered sandstone with rock ledges along with just basic sand.
“The soil conditions were very difficult,” he said. “Anytime you have a sandstone layer that’s down below the ground that you can’t see, it plays havoc with drilling equipment. It takes good equipment and a skilled operator who understands the ‘feel’ of the rig, and how it is responding to what is being encountered.”
Driver credits good employees for the company’s ability to take on large and complicated projects successfully and the use of high quality equipment to complete the work efficiently. The company is using a fleet of nine Vermeer HDD rigs, including the D100x120 Series II and D330x500 models, to complete the project.
“We use our in house survey crews to plot each bore,” Driver said. Once all utilities and related lines are located, a Vermeer vacuum excavation machine is used to uncover all the lines and do a drill profile. Then we plot each utility on the drill profile before the rig ever comes in. We have five or six vacuum excavation machines that play a very big role in the drilling project on the front end. It is an essential part of the process to ensure that we don’t damage any of the existing lines.”
The pre drill process involves running tungsten carbon inserts to start a pilot hole. The size of the hole is determined by the size of pipe to occupy the bore. For example, a 24 inch pipe requires a 24 inch pass followed by a 36 inch pass and then a mud or “swab” pass to prep the hole. These passes determine the difficulty of the penetration rate that will be encountered with the cutters. A rule of thumb for over cutting is 1.5 times the diameter of the pipe.
“Water is pumped into the shale that is mixed in with some recyclers,” Drivers said. “We also have a mud mixing unit set up next to the drill rig. The mud mixture is pumped down the hole with a triplex pump, anywhere from 85 300 gpm, depending on the rig size. This is also reclaimed so it can be used again.”
Production rates vary depending on the conditions, but Driver’s crew of between 125 150 onsite, average approximately 500 feet a day to ream and pull pipe through.
Installation challenges (subhed)
With hundreds of takeoffs and landings occurring daily and the potential for thousands of people looking on, Driver agreed that this is the most visible and important project ever undertaken by the company. The company’s knowledge and experience, plus the fact that Driver is locally based, provided an advantage over other contractors.
“This is our backyard,” Driver said. “We know the terrain, the composition and the geography better than anyone. We’ve done a lot of work in urban areas that are congested, have high visibility and are complicated. But this one certainly is the trophy. We are constantly in the forefront of people coming and going, in and out of the airport, so that alone generates a lot of attention. We did a project similar to this a few years ago that involved installing a gas pipeline near the Baltimore/Washington Airport, but nothing of this magnitude.”
Working with a number of different entities for bidding, permits and compliance with FAA regulations and restrictions is also a daunting component of this project. And if that weren’t enough, when work commenced, Driver had to deal with the wrath of Mother Nature.
“We had rain for more than 50 of the first 90 days when we started the work,” Driver recalled. “We needed to get the first five miles of 24 inch pipeline in the ground in order to begin production on the initial wells and not have what we call a WOPL (i.e. waiting on the pipeline). We were able to stay on schedule and constructed the first five miles using HDD under two major highways, railroads, water lines and environmental restrictions. It was quite an accomplishment.”
Driver has completed nearly 80 percent of the installation so far and should be close to completion within the next few months. When the infrastructure is complete, this vast underground maze of pipelines will deliver a large amount of natural gas from beneath one of the world’s busiest airports, and ultimately, to locations throughout the United States, providing energy for thousands of customers.
FOR MORE INFORMATION:
Driver Pipeline, (214) 638-7131, www.driverpipeline.com
Vermeer Corp., (888) 837-6337, www.vermeer.com
Comments