April 2009 Vol. 64 No. 4
New Products
First Look: See-Through PVC Panel Rehab System Introduced By National Liner
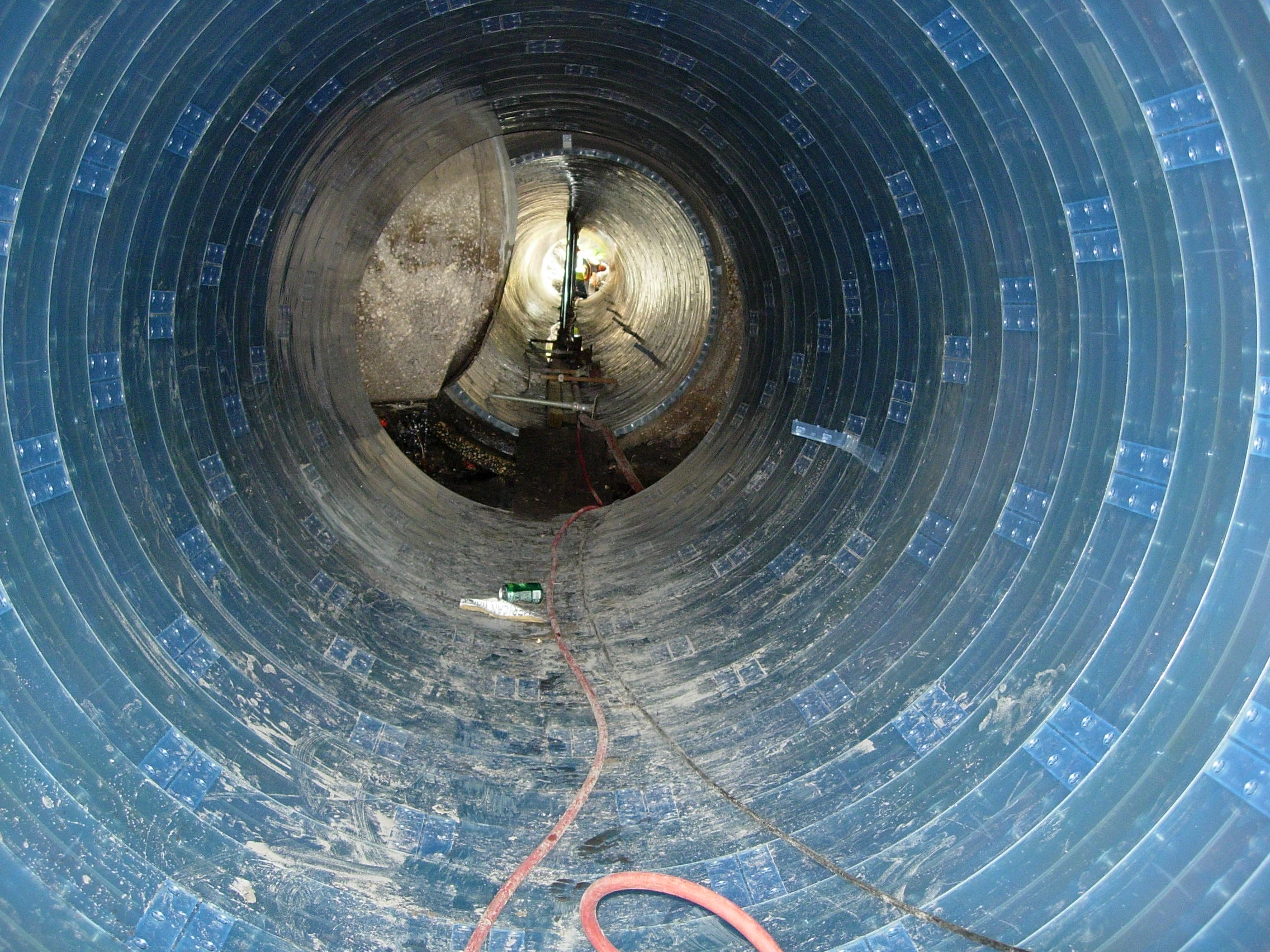
National Liner LLC has introduced a trenchless rehabilitation lining process that uses see-through PVC panels to rehabilitate circular pipes, box culverts and structures of other shapes.
The 3S Segment Panel System uses translucent, PVC panels bolted together inside the pipe to form an inner pipe, said Ray Pavlic, National Liner director of marketing and sales.
“This is a new process for rehabilitation of large diameter pipes and box culverts,” Pavlic pointed out. “PVC segment panels can be used in pipes ranging from 48 to 120 inches in diameter and are designed for optimal application to the conditions of the host pipe or structure. They are light in weight and can be hand carried into the pipe – no large machinery or complicated equipment is required for construction.”
See through segment panels make it easy to visually confirm grouting of the annular cavity is complete and without voids. Assembled rings can accommodate a joint offset of up to two percent and joint gaps up to six inches. Angular changes in alignment of up to 3 degrees can be made in the field.
“Minimal flow of wastewater is no hindrance to installation of the panels which can be installed in flow depths of up to 10 inches,” Pavlic continued. “If necessary, temporary cessation of the installation process is possible.”
Classification, approvals
Pavlic said the panels meet approval of the UK’s WRc Group (a research-based group providing consultancy in the water, waste and environment sectors) as Type 1 sewer rehabilitation technique. In the United States, the panel system is classified as a grout in place liner (GIPL).
“The PVC material used in the panels has been shown to be equal or superior in abrasion resistance to the performance of typical PVC wastewater piping,” Pavlic said, “and has passed the ‘pickle jar’ chemical resistance testing required by the Los Angeles Greenbook.”
Design calculations take into account the residual strength of the existing pipe and panels which enable rehabilitated pipe to be stronger than the original pipe when new, Pavlic explained. Once joined panels are in place inside the pipe or structure, grout is injected between the host and the panel segments.
“An economic analysis of the cost of installing this system compared to CIPP for relatively short runs of pipe shows the segmental panel system to be the clear winner,” Pavlic stressed. “In addition, where access is limited and the cost of sinking shafts becomes excessive, longer runs also can be most cost effective.”
Pavlic said a recent inspection of a 72 inch run of the system installed in Orlando, FL, in 2005 “looks as good as the day it was installed.”
“We believe,” said Pavlic, “introduction of the 3S Segment Panel process combined with National Liner’s CIPP technology for mains and lateral lining, offers municipalities a complete line of products and processes to rehabilitate and extend the life of their sewer systems.”
The 3S segment paneling system is manufactured in Japan by Shonan Plastic Mfg. Co. Ltd. and is available in the United States from National Liner through its licensed installers.
FOR MORE INFORMATION:
National Liner: (281) 874-0111, www.nationalliner.com
Comments