April 2009 Vol. 64 No. 4
Features
Understanding Environmental Implications Of CIPP Rehab Technology
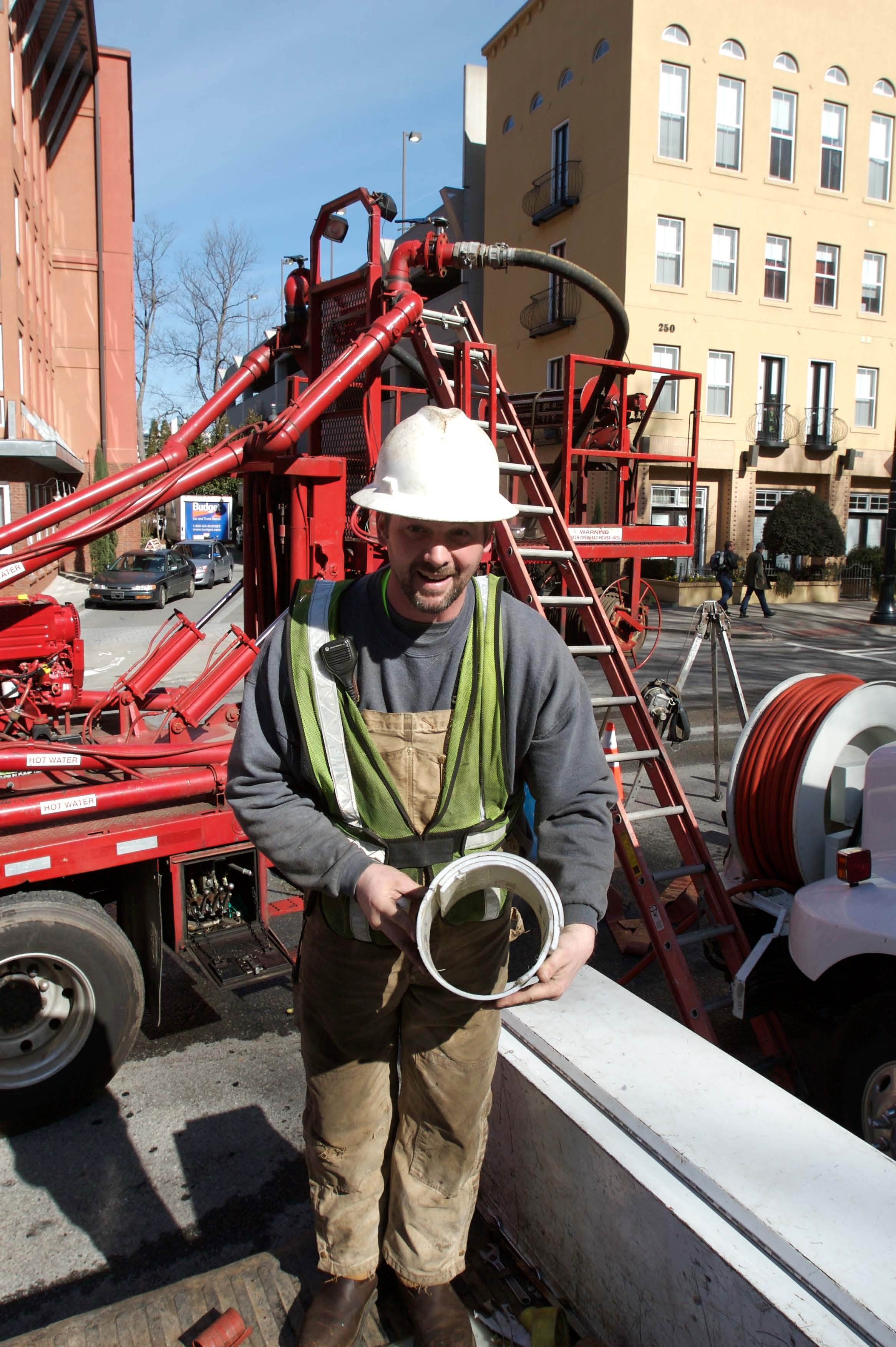
In May 2008, the Virginia Department of Transportation issued the results of a study (VTRC 08 R16) of which the purpose and scope was “to evaluate the potential for impacts on water quality from use of the steam cured CIPP process.” Given the potential value of having an independent investigative look at the potential environmental impacts of using styrenated resin systems in storm water system rehabilitation, the industry looked forward to the gains from such a study; and the potential for having the information available to the consulting engineering community as they continued to increase their usage of CIPP in storm sewer and culvert applications. This article will explore the path of the research, findings of the researchers and their technical conclusions.
All engineering projects must contain an environmental assessment of the disruption that potentially might occur as a result of the contemplated work; trenchless pipeline rehabilitation using CIPP is no exception. CIPP projects, because of their short duration and limited area of impact, typically fall under the Environmental Protection Agency’s construction general permit (CGP), if at all. Projects fitting under the CGA requirements are those having an impact area of between one and five acres. This permitting program was established by the EPA in an effort to forego the massive amount of paperwork that would be required to address each individual small construction project such as CIPP work. In my experience, the impact areas of essentially all CIPP projects are less than one acre in size. Further, most DEQ engineers would probably feel that given there is little or no excavation and/or soil movement, this rehabilitation work falls outside of the CGP.
Given such an extremely small project footprint, CIPP project sites should be governed under the broader self oversight requirements for a potentially hazardous material. Self oversight, however, can be a challenge as the EPA has no stated or pre determined limits for discharges of water containing styrene from construction sites. Therefore, the CIPP installer must consider the assimilative capacity of the downstream receiving ditch or waterway to accept the estimated VOC and/or thermal loading that will result from the process methodology as it pertains to the known downstream aquatic organisms.
Compounding this analysis, the rapid volatilization of styrene in the environment has to be taken into account. Acute toxicity studies, by their nature, hold the concentrations of the “toxins” under scrutiny at a constant level for the reported study period. This is inconsistent with styrene’s high volatilization rate in the real world. Further supporting this self-diminishing impact is the fact that styrene has been confirmed not to be bioaccumulative.
V-Dot report
In VTRC 08 R16, the researchers state that a literature review revealed that spills of uncured resin from CIPP installations can cause large fish kills. This author could only find one written example of such a purported occurrence: a Lockheed Martin Energy Systems internal report dated Aug. 17, 1995, that recounted the installation of 280 feet of 36 inch diameter CIPP into a storm water pipe. The CIPP was cured using hot water and during processing it was estimated that “approximately three to four gallons of uncured resin extruded into the manhole at the lower end of the liner.”
Because the storm water system under rehabilitation discharged into the East Fork Poplar Creek, the project engineer had directed the installer to hold the process water in the cured liner until it reached a temperature of 72 degrees F before discharging it into the downstream piping and subsequent holding lake. Normally, the installer’s processing steps called for cutting a two inch diameter hole to allow the 90 100 degree F water to drain slowly from the cured lined which had been demonstrated to cure “the extruded uncured resin causing it to precipitate out as an insoluble solid.”
The post installation discovery of a fish kill in the East Fork Poplar Creek having a measured dead count of 5,500 fish was quickly attributed to a styrene release when a quantity of uncured resin was found in the downstream manhole of the lining work. The concentration level of the water in the manhole was around 100 parts per million (ppm). Curiously, the styrene concentration in the holding lake downstream at this same point in time was found to be 0.066 ppm (the outfall point to the creek was not sampled). No information was given in the posted report to ascertain the validity of the assumption that styrene was indeed the culprit. Certainly a discharge containing 0.066 ppm or less would not have triggered such an occurrence.
On a positive note, the Lockheed Martin report’s author stated that, “After dead fish were observed, actions were implemented to remove the uncured resins from the creek and the storm drainage system. The creek, lake and aquatic life returned to normal conditions after the cleanup efforts were completed.” VTRC 08 R16’s authors went on to state that in their opinion, “Except in the immediate vicinity of a spill, exposures to styrene are not deemed to cause deleterious effects on natural communities of organisms. Styrene volatilizes rapidly and has not been shown to bioaccumulate in organisms to any measurable extent.” Further, they related other bodies of work that had shown that styrene “introduced in river water in concentrations up to 37 ppm was reduced [naturally] by 99 percent after 20 days.” Also, that “Fu and Alexander found that 50 percent of two to 10 ppm was lost by volatilization in one to 3 hours in lake water samples.”
Common sense tells one that while styrene can indeed kill fish and other aquatic organisms, the risks are essentially nil when proper housekeeping practices are in use to contain, pick up and dispose of any uncured resin that occurs during the installation of the CIPP. While this one incident was cited in the report, it’s hard to find any other writings of styrene related fish kills caused by CIPP installations. There are numerous examples of this happening at resin manufacturing and processing facilities; but none that I could find for CIPP installations.
Monitoring
There were seven CIPP installation sites monitored for VTRC 08– R16 representing the installation practices of three CIPP installers. None of the installations chosen represented curing the CIPP by hot water or UV light; only sites utilizing the steam curing method were evaluated. Further, no review was made of the various installers curing expertise or confirmation of the resultant CIPP’s percent of cure.
Being culvert installations, the sites were classified as having low intermittent flow, low to medium continual flow, low to heavy continual flow, and medium to heavy continual flow. The timing of the samples taken to measure the styrene content in the downstream waterway was varied; and in some cases no measurements were made until 15 days after the installation (at one site they didn’t make a visit until 37 days after the installation).
At site number four, the storm water pipe only carried flow during rainfall events so the researchers chose to pour one gallon of distilled water into the inlet of the pipe and capture it on the outlet end; that’s one gallon of water running through 121 linear feet of 24 inch diameter pipe. While the researchers stated that upstream samples were taken at sites 2, 5 and 7 at the commencement of testing, upstream samples were not taken at sites 1, 3, 4 and 6 at the commencement of their monitoring.
Additionally, no upstream samples were taken throughout the course of the study which could have provided the user of the report with confidence that the styrene concentrations post installation were the result of the newly installed CIPP. This fact was particularly disturbing to the NASSCO styrene task group as the flows carried by these storm water installations carry flow from the roadway. Automobile emissions are a known source of styrene in the environment. A condensed presentation of the styrene concentrations found by the researchers is shown in the accompanying table.
What is the assimilative capacity of the seven project sites investigated? No analyses were made by the researchers.
Were there any observed fish kills or other environmental impact to these project sites? None were reported by the researchers.
As these are storm water pipes, the contaminate loading rates should have been assessed based upon the assimilative capacity of the receiving waterway and the aquatic species therein. Instead, the concentrations measured by singly taken grab samples were compared against the maximum contaminant level for styrene in treated drinking water: 0.1 ppm. Additionally, we were provided with reference levels of styrene concentration for the water flea (48 hour E50) and rainbow trout (96 hour LC50). From the lack of documented environmental impacts at these sites, one can logically conclude that the assimilative capacities of the receiving waterways were, in fact, not exceeded by the direct discharge of the measured styrene concentrations from these CIPP processing operations, or by the subsequent styrene concentrations measured in the storm water flushing of the newly installed CIPP.
Preliminary findings
VTRC 08 R16’s preliminary findings issued in mid-2007 were that the VA DOT should suspend the use of styrene based CIPP and undertake additional study to understand CIPP; that the DOT should evaluate their contract documents to ensure that CIPP contractors are specifically required to prevent the escape or leaching of process residuals (capturing and properly disposing of cure water, cure steam condensate, and escaped resin); and if styrene based CIPP is re instated that the DOT should ensure that it has proper oversight on hand during the CIPP’s installation. As a result of these findings and the researchers’ recommendations, the following notable changes were issued by the VA DOT in April of 2008:
- A project inspector, properly trained in CIPP, must be present for the duration of each installation;
- The contractor must obtain and comply with all discharge related permits, including air, water, and wastewater treatment;
- Styrene-resin based CIPP systems must have an impermeable inner and outer plastic film or plastic pre liner to promote complete polymerization, prevent resin migration and loss, and prevent styrene contamination of the interior of the finished product;
- For styrene resin based systems, the contractor shall place an impermeable sheet immediately upstream and downstream of the host pipe to capture any raw resin spillage during installation and shall remove and properly dispose of any waste materials;
- The contractor must submit preconstruction installation and cure specifications. Included shall be the requirement for monitoring temperature via a minimum of three thermocouples on the outer surface of the liner (upstream end, downstream end and at the approximate midpoint of the lining). The thermocouples shall be connected to a data logger capable of producing a print out which shall be given to the project inspector;
- Additional lining materials and measures to ensure the containment of resin and styrene;
- Procedures for monitoring the curing of the CIPP lining material;
- Thorough rinsing of the finished CIPP;
- The contractor shall capture and properly dispose of cure water, cure condensate and rinse water by transporting it to an off site disposal location; and
- Water and soil testing to be done prior to and after installation. Samples shall be taken within three feet of both ends of the pipeline being rehabilitated. The post installation sampling must be accomplished within one week of the installation.
The impact of those changes to the VA DOT’s specifications have essentially been mixed. Some installers already had a policy in place to transport and dispose of the process water from hot water curing at a nearby wastewater treatment facility. This was due to the lack of definitive information on the process water’s potential environmental impact and the general public’s fear of chemicals that smell. Steam condensate is not typically transported away. Appropriate permits were obtained in the past by most installers.
Looking ahead
The question going forward is, have installers been missing any required permitting? In the short term, the requirements have resulted in some of the installers not bidding the DOT’s projects while they sort out these new requirements. Others continuing to bid the work claim pricing has approximately doubled since implementation on the new rules. The environmental costs to transport the water used in the CIPP processing (increased engine emissions, diesel usage, etc.) have not been quantified. It is logical to conclude, however, that there has been a negative environmental and economic cost to the new requirements. Is this added cost technically justified?
In the newly issued NASSCO Guideline for the Use and Handling of Styrenated Resins in Cured In Place Pipe, it was concluded that “All that CIPP resin systems require is that good housekeeping be practiced by the installation team on the project site.” Further, provisions must be made by the contractor in advance for containing any accidental spillage of the resin on the work area. By law, spills less than the hazardous materials “regulated quantity” of 1,000 pounds of styrene (2,500 pounds of resin) are to be handled in a responsible manner by the contractor. Absorption with an inert material and placing in an appropriate waste disposal container is the industry standard for handling small spills like this on the ground. Oil dry, kitty litter and sand work well for this action. If the spill occurs on a hard surface, the area should be scrubbed with soap and water after the bulk of the spill has been cleaned up by the absorbent material. If the spill gets into a waterway, the spill should be contained using a temporary dike. The resin can then be picked up by vacuuming the resin into a vacuum truck and subsequently placed in an appropriate waste disposal container.
It is imperative that the processing of the liner, whichever method of curing is used, is properly completed. Properly cured liners release little or no styrene to the environment. Thermocouples placed strategically in the liner host pipe interface are a must. A written curing schedule developed for a CIPP system acknowledging the conditions that can be present in the curing environment and the resin system proposed will lead to a proper cure and a long CIPP life; and, in this author’s opinion, no measurable environmental impact.
In the NASSCO guideline, proper curing and handling of CIPP systems is recommended to be implemented using the following steps:
Water Curing
Sanitary Sewers
- Cure resin system per written curing schedule; and
- Release process water to the sewer after per industry standards during/after cool down.
Storm Sewers and Culverts
- Cure resin systems per written curing schedule; and
- Based upon receiving waterway’s assimilate capabilities:
- Discharge water when at ambient air temperature;
- Discharge water when styrene concentration is confirmed to be at or below 25 ppm; or
- Transport process water to nearest wastewater treatment facility.
Steam Curing
Sanitary Sewers
- Cure resin system per written curing schedule; and
- Release condensate water directly to receiving sewer while processing.
Storm Sewers and Culverts
- Cure resin system per written curing schedule;
- Based upon receiving waterway’s assimilative capabilities:
- Detain condensate in a lined holding pond until it cools to ambient;
- Discharge water when styrene concentration is confirmed to be less than 25 ppm; or
- Retrieve condensate by pumping it into the steam generation truck’s reservoir; or
- Transport condensate to nearest wastewater treatment facility.
Using the above recommendations, any residual styrene concentrations from a properly cured resin system that are taken into the runoff water from storm events will typically be short lived, in the range of less than 1.0 ppm and pose no significant environmental threat.
It is recommended that the VA DOT perform additional sampling, studies and evaluations of CIPP installations and their effect on the environment, using good sound engineering and testing principles. The VA DOT has a wonderful opportunity to provide the industry with a review of its installation practices and refine them as needed to preserve cost effective and environmentally effective usage. The Virginia Water Quality Standards state that “state waters . . . shall be free from substances . . . [that] interfere directly or indirectly with designated uses of such water or which are inimical or harmful to human, animal, plant or aquatic life.” Further, the standards state that “Effluents which tend to raise the temperature of the receiving water will also be controlled.” The additional studies should use these defined guidelines in the context of proper installations following good housekeeping practices to assess the true environmental implications of CIPP rehabilitation technology in culvert and storm sewer rehabilitation. In so doing, the industry is confident that they will conclude that the NASSCO recommendations given previously are in line with Virginia’s clean water requirements.
ABOUT THE AUTHOR: Ed Kampbell is president of Rehabilitation Resource Solutions, an engineering consulting firm specializing in trenchless rehabilitation of sewer and water systems. Kampbell is a nationally recognized authority on CIPP, and holds patents related to the technology. (614) 529 8204; ekampbell@sbcglobal.net.
Comments