April 2009 Vol. 64 No. 4
Features
Locates At The Design Stage Prove Valuable
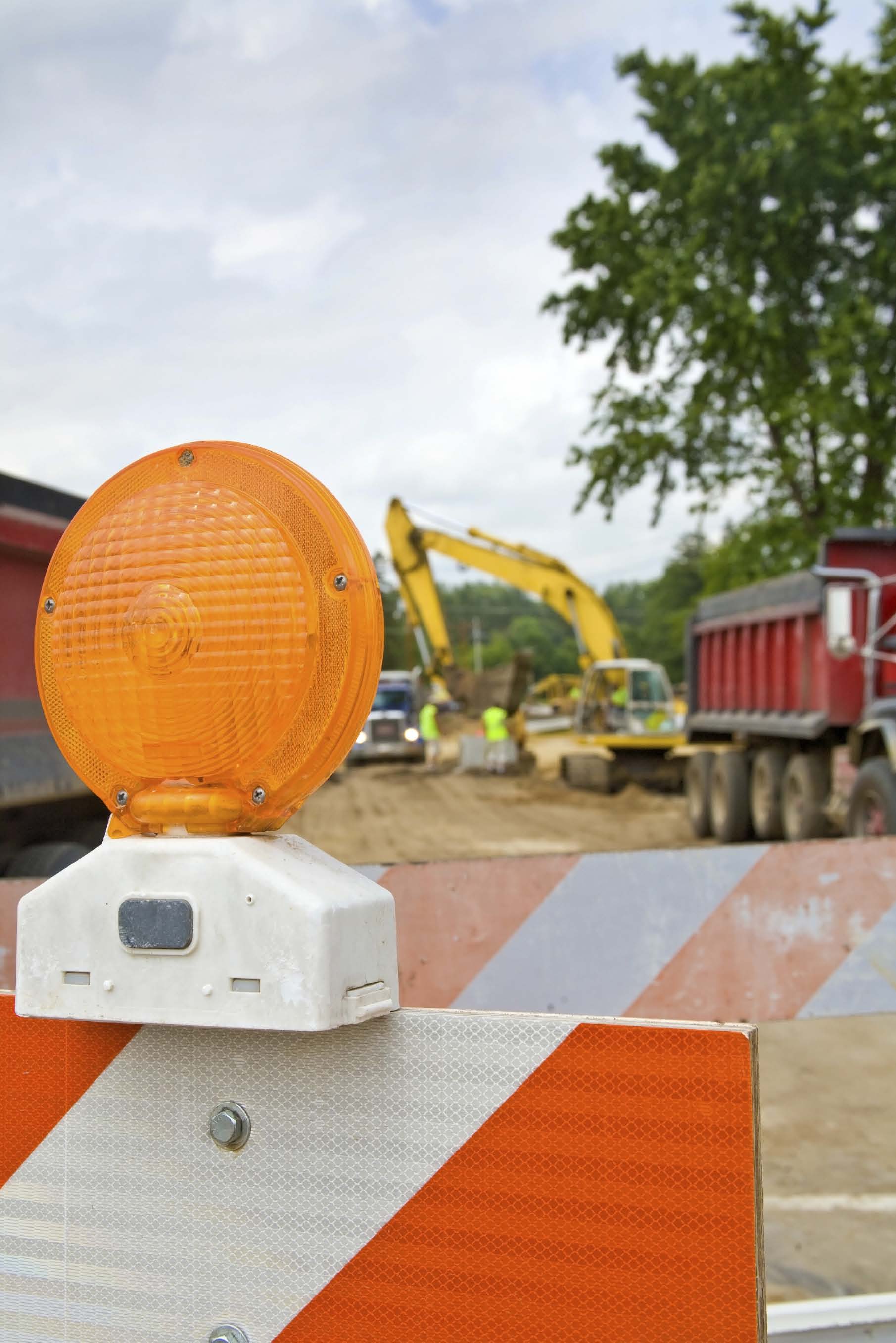
Underground utility construction projects most often are classified as either new construction, usually to extend or upgrade services, or replacement/rehabilitation of old or failing buried infrastructure.
However, many projects are to relocate utilities because of street, highway improvements or other types of general construction that makes it necessary to move buried utilities to a new location. Although planning for such projects begins months – even years – before ground is broken, locations of existing buried utilities may not be identified until shortly before construction is scheduled to begin.
Not knowing where facilities are buried during planning can result in costly delays and safety issues once construction is under way.
Mapping utilities before a project begins is one element in the discipline of subsurface utility engineering (SUE), promoted by the U.S. Department of Transportation Federal Highway Administration and, until recently, used primarily on large highway projects.
SUE is an engineering process that goes far beyond locating and marking buried utilities, and although SUE is being applied to projects other than highway construction, many project owners do not retain SUE specialists. For whatever reasons, many project owners and engineer consultants continue to exclude precise utility location from the planning stage.
Early knowledge beneficial
Brian Dorwart, P.E., P.G., vice president of Haley & Aldrich Inc., is an engineer with experience in planning a wide variety of underground utility projects, and he recognizes the value and importance of confirming locations of buried utilities early in a project’s planning.
“Knowing where utilities are allows engineers to take them into account from the outset and manage the risk during construction,” Dorwart said. “Encountering buried facilities unexpectedly during drilling or excavation can create safety hazards and cost money to pay contractors to stand by while planning adjustments are made. All this results in scheduling delays that are significantly higher than the cost of reliable locating early in the design phase.
“I prefer,” Dorwart continued, “to make locates during the permitting phase and while working on the base plan. We do our research, do vacuum excavation verification of utility locations and plan with realistic data.”
Dorwart said that he wants to know the locations of utilities within 25 to 50 feet of the projected bore or excavation path.
“We cover that much area because we need to develop the most cost effective route through congested areas that have significant surface access restrictions,” he explained.
Verification is important because utilities often are not present in available records or they are not in the locations indicated on records.
“Urban utilities in particular often are not at locations indicated on available records,” Dorwart said. “Additionally, older cities often include abandoned and removed utilities on locate plans that occupy otherwise free space, and there often is no reliable procedure for their removal because of liability issues. Engineering around these ‘phantom’ utilities and redesigning during construction because of mislocated utilities can result in significant cost to new projects for unnecessary, new right of way acquisition, or planning locations that could have been avoided.”
In addition, municipal utilities such as sewers often have no build restrictions above the utility to permit access for repairs.
“I know of one project where a sewer owner required that a significant segment of a newly installed utility be removed and reinstalled because it had been built over an existing sewer,” Dorwart said.
Time sensitivity
Some project planners may not make utility locations early because of the time it requires.
Many state one call agencies process requests for member organizations to locate and mark their buried facilities before construction begins. Depending on where the project is, facility owners and operators may not respond to requests for locates far in advance of construction.
“If the goal is efficiency in damage prevention, one call design tickets for locating and marking during the project planning make sense,” said Walt Kelly, excavation damage prevention consultant.
“If the immediate goal is taking calls prior to excavation, then design tickets are not appropriate, and a separate, parallel system should be established. In the past, New Jersey and Virginia actually fined designers and excavators who tried to use one call for assisting in design. But that is no longer the case.”
In Kelly’s home state of Minnesota, Gopher State One Call (GSOC) has non excavation tickets and, in fact, requires that GSOC be contacted in many circumstances involving contract and bid proposals.
However, even though many one call centers do process engineering and design requests from facility owners and operators, many utilities are not owned by one call members.
J.D. Maniscalco can view the issue of whether to locate or not locate during planning from three perspectives: he is executive director of the Utility Notification Center of Colorado, a board member of the Common Ground Alliance (CGA) representing one call centers, and past chairman of One Call Systems International (OCSI) and currently is chairman of the OCSI data collection committee.
The Common Ground Alliance (CGA) is the private, nonprofit organization that has taken the lead in developing and implementing industry Best Practices to help protect underground utilities for those who live and work by them, said Maniscalco.
Best practice
He cites the CGA Best Practice statement covering identification of existing facilities in the planning and design phase which recommends:
“During the planning phase of the project, existing facilities are shown on preliminary design plans. The planning documents include possible routes for the project together with known underground facility information. The various facilities are then given the opportunity to provide appropriate feedback.
“During the design phase of the project, underground facility information from the planning phase is shown on the plans. If information was gathered from field located facilities, from underground facility surveys or from subsurface utility engineering, this is noted on the plans. The designer and the contractor both know the quality of the information included on the plans. If an elevation was determined during the information gathering, it is shown on the plan. The facilities shown include active, abandoned, out of service, and proposed facilities. The design plans include a summary drawing showing the proposed facility route or excavation including streets and a locally accepted coordinate system. The plans are then distributed to the various facility owners/ operators to provide the opportunity to furnish additional information, clarify information, or identify conflicts.”
Following this practice, said Maniscalco, provides complete underground facility information and including this data on design drawings reduces the hazards, simplifies coordination and minimizes the cost to produce the final project.
“Many state one call laws do outline procedures for making locates during the design process, but don’t necessarily require them to be made in the same time frame,” Maniscalco said. “But we hear that many times, these requests go unnoticed and unattended for that reason. However, there are some one call centers that do handle design locates routinely and the majority of facility owners do a fine job to accommodate the request by either providing maps or physical marks with paint or flags.”
Workload
During the past decade, the drive to build and the resulting number of locate tickets has made it difficult to fill requests for locates to use in planning.
“Some facility owners and operators have struggled to keep up with processing basic location requests so they can be completed before excavation is scheduled to begin,” he said. “Possibly with the slowdown in construction, some of this pressure may be relieved.”
Complicating the problem, Maniscalco added, are instances when a large project goes to bid and several competitive firms overload the system firms with requests for the same information. The company receives the contract and locates are requested again for the same area when work is started.
One way some project planners have expedited one call generated locates for planning is to indicate that earth will be moved which changes the notification to an excavation notice, he added.
In conclusion, Maniscalco said there currently is no national effort directed at promoting utility location during planning.
“We see pockets of private companies, SUE companies hired by utility owners to gather information, but no industry organized group advocating the benefits of making utility location a part of the process,” said Maniscalco. “In Colorado, we had a pilot project five years ago to encourage five major counties to begin a project that would build data into the system so it would be available, but it became so large and unwieldy, it was dropped.”
“The logical development is to incorporate SUE information into a system,” he said. “It will have to begin small in a city, then to a county, and expand a step at a time. The more detailed information made available will help the industry improve overall management of right of way.”
FOR MORE INFORMATION:
Common Ground Alliance, (703) 836 1709, www.commongroundalliance.com.
Haley & Aldrich Inc.: Brian Dorwart, P.E., (603) 625 5353, bcd@haleyaldrich.com
Walt Kelly LOOK UP INFO
Utility Notification Center of Colorado: J.D. Maniscalco, (303) 232-1991, www.uncc2.org/web/
Further information: SUE and Highway Construction
Subsurface utility engineering (SUE) is much more than locating and marking underground utilities – it is an engineering process that has evolved over the past few decades. SUE was born in the early 1980s when it was recognized that traditional methods of dealing with subsurface utilities were not working.
The SUE process combines civil engineering, surveying and geophysics. It utilizes several technologies, including vacuum excavation and surface geophysics.
When the Federal Highway Administration (FHWA) began promoting SUE in the early 1990s, only a few state departments of transportation (DOTs) were known to be using it. Today, nearly every state DOT has used it to some extent on highway projects and SUE has expanded into Puerto Rico and Canada. Many state agencies now use the SUE process routinely on every project. In addition, SUE is being used by local highway agencies, utility companies and design consultants and has expanded beyond the highway industry to military, airport, transit, port and other transportation industries.
SUE services are provided by specialty companies.
The American Society of Civil Engineers (ASCE) has established a national standard stating responsibilities of engineers, project owners and contractors for the collection and depiction of existing subsurface utility data on design and construction documents. The FHWA and several SUE providers helped fund this activity. Compiled from information on the FHWA web site, www.fhwa.dot.gov.
Comments