September 2008 Vol. 63 No. 9
General
Pilot Tube Microtunneling Proves Effective Under Busy Houston Street
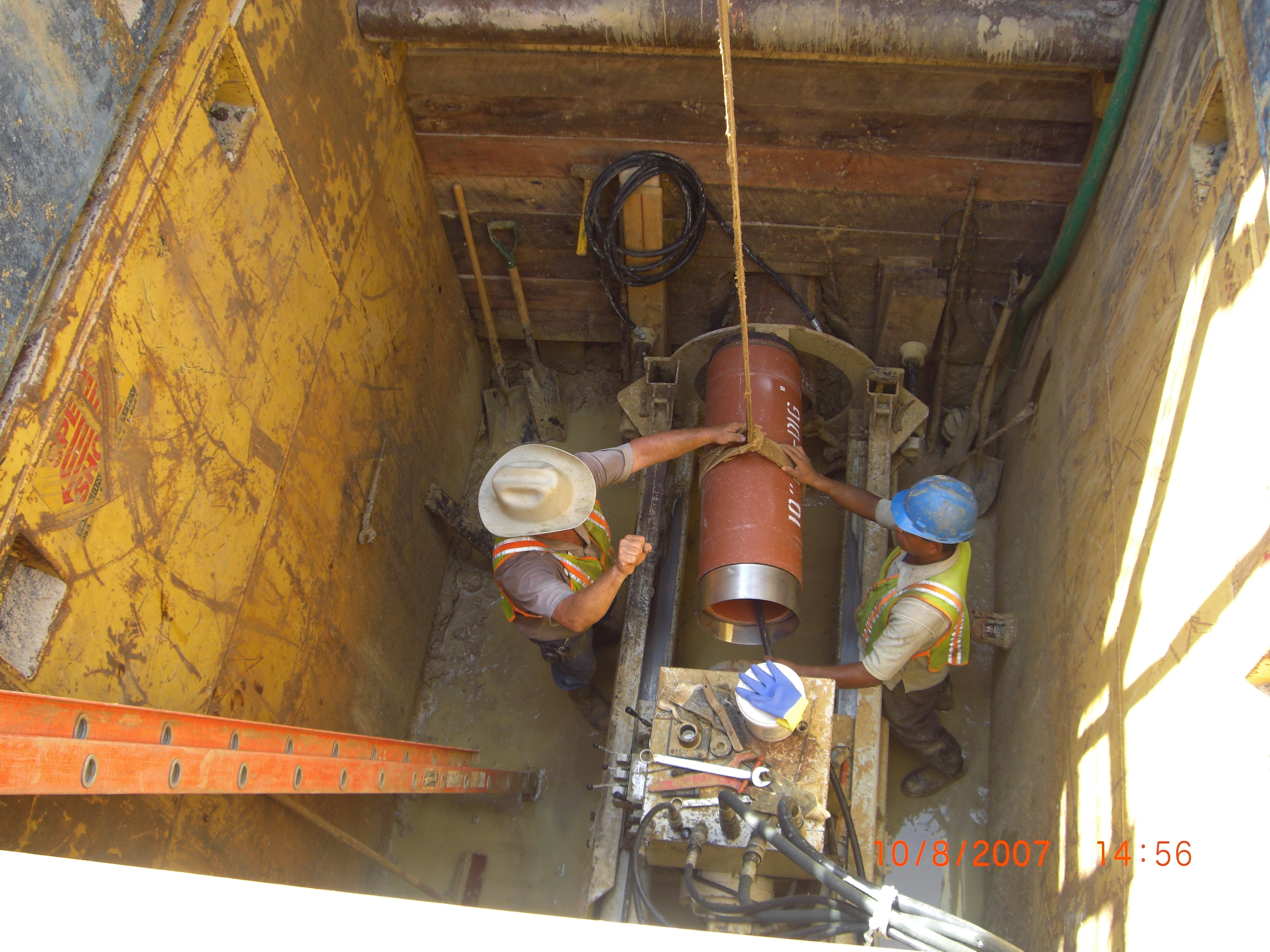
Many underground utility projects are necessary when construction for a variety of improvements requires relocation of existing buried infrastructure. In such situations, work often is complicated by surface improvements and heavy traffic in and around the job site.
A good example is a recent project in Houston that required improvements to a portion of the city’s sanitary sewer. The Westheimer to West Alabama Sewer Relocation Project was located on one of Houston’s busiest thoroughfares and excavation would have caused major disruptions of traffic, making trenchless construction the best option for most segments of the project. Wet boring, pilot tube microtunneling and a limited amount of open cut construction were used to complete the project.
Magnum Tunneling, LLC, used the pilot tube microtunneling method to install 2,440 linear feet of Mission Clay No Dig pipe in diameters of 8, 10 and 12 inches. Magnum was a subcontractor for ACM Contractors, Houston.
“Pilot tube microtunneling enabled pipe to be installed while maintaining continual traffic flow during construction,” said Patrick L. Mann, Magnum’s chief operating officer.
All about pilot tube
The pilot tube procedure provides many of the advantages of conventional microtunneling for installation of smaller diameter pipes at shorter distances and at significantly lower costs than microtunneling installations of larger size pipes.
Unlike conventional microtunneling, a pilot tube installation establishes line and grade with a small diameter pilot tube before pipe is jacked into place.
The hollow pilot tube provides the optical path for the theodolite to display head position and orientation for steering the path of the tube. Sections of tube are added as the drive continues, connected by hex connectors with threaded couplings. Spoil from the pilot tube installation is displaced for removal. As the drive progresses, pilot tube pipe joints are removed in the receiving pit. Pilot holes are enlarged by backreaming to accommodate the outside diameter of the pipe being installed, and spoil is removed by an auger system.
Pilot tube installations employ smaller, less expensive equipment, require smaller jacking pits, and topside footprints require less space than conventional microtunneling projects. Pilot tube projects generally are for pipe from 4 to 12 inches in diameter and for drives to distances of 250 feet.
For the Westheimer project, Mann said an Akkerman 240A single stage jacking frame was used. Eleven drives were made, ranging in length from 57 to 301 feet. Most of the drives fell between 240 and 260 feet. Work shafts were at manhole locations. The guided boring machine (GBM) was placed in 8 by 12 foot trench boxes dug at manhole points. Subsurface soil conditions consisted of stiff, firm clay. The work area was in the center median to allow outside traffic lanes to remain open.
Lengths of clay pipe installed by pilot tube microtunneling were:
• 8 inch pipe, 260 feet;
• 10 inch pipe, 760 feet; and
• 12 inch pipe, 1,420 feet
Pipe joints were one meter in length which fit easily into the trench boxes.
The Akkerman 240A single stroke jacking frame can be accommodated in shafts 8 to 12 feet wide, and is capable of producing 100 tons of jacking force, 50 tons of pullback and 10,000 foot pounds of rotary torque. Its theodolite guidance system is designed for an accuracy of one quarter inch at 300 feet. Dual wall pilot tube design provides lubrication of pilot shaft as it passes through the ground, reducing the amounts of thrust and rotational force during installation. The unit’s power package was positioned on the surface.
Clay pipe
Vitrified clay pipe is used for more pilot tube installations than any other type of pipe, said Jeff Boschert, P.E., field engineer for the National Clay Pipe Institute.
“Clay pipe has high compressive strength for jacking, is chemically resistant to sewer gases and short, one meter lengths are perfectly suited to pilot tube technology,” he added.
The Mission Clay No Dig jacking pipe used on the Westheimer project employs resilient gasket material and stainless steel collars at each low profile joint resulting in a leak free system. A chipboard compression ring distributes jacking forces from one section of pipe to the next.
For the tunneling industry, No Dig pipe is available in sizes ranging from 8 to 36 inches in diameter. Since the product was introduced in 1992, more than 300,000 linear feet of pipe have been installed on tunneling projects in the Unites States, said Billy Nelson, area manager for the No Dig Division of MCP Industries.
Magnum Tunneling completed its pilot tube segments over a two month period. Project owner is the city of Houston Department of Public Works and Engineering. Brown & Gay Engineers, Houston, was the consulting engineering firm on the project.
Based in Houston, Magnum Tunneling specializes in heavy underground construction of tunnels, drainage systems, pipelines, shafts, sewer, water and gas lines, electrical telecommunications systems and residential developments.
FOR MORE INFORMATION:
Magnum Tunneling & Boring, (832) 300-3333, www.magnumboring.com
Mission Clay No-Dig Pipe, (210) 863-3350, www.no-dig-pipe.com
Akkerman Inc., (800) 533-0386, www.akkerman.com
Comments