September 2008 Vol. 63 No. 9
Business
Seismic-Prone Project Area Requires HDPE
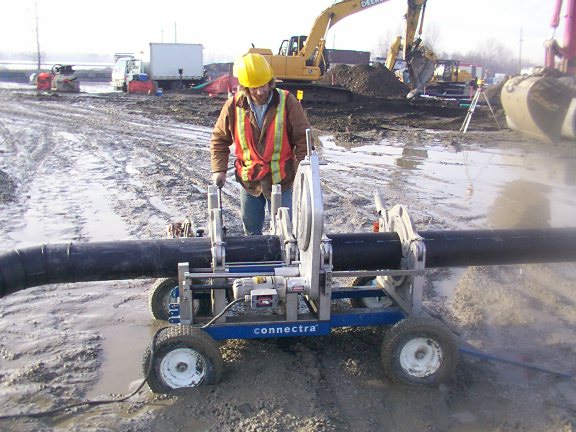
A new retail power center in Burnaby, British Columbia, Canada, is quite literally ‘floating’ on a bed of wood, gravel and concrete. In an area where construction must always consider the impact of seismic activity, the potentially fluid nature of this site’s foundation meant that for underground contractor TAG Construction Ltd. of Langley, British Columbia, the choice when it came to the construction of the underground water and sewer lines was crystal clear.
“In this case it was readily apparent that only HDPE pipe would be able to sustain the flexible nature of the site,” said professional engineer Michael Grant of TAG.
The site of the 302,000 square foot Big Bend Crossing shopping center had been a waste dump for building demolition material for many years. Then it was pre-loaded for construction using building excavation material from sites throughout the lower mainland.
“This made for very fluid soil conditions,” explained Grant. “The design using HDPE mains and services for water and sanitary was based on the ‘flexible’ nature of the site, given the presence of the wood wastes below and their ground water content, and the need to ensure the integrity of the pipe in the moving ground.”
HDPE pipe can be bent to a radius 25 times the nominal pipe diameter for mid range pressure pipe, 20 times for heavy wall pipe and 30 times for low pressure pipe. In addition to eliminating many fittings required for directional changes in a piping system, the “flex” factor makes HDPE pipe ideal in areas of high seismic activity.
An advantage of PE pipe is that gaskets or external joints are not required, explained Brad Warning of Prolite Systems in Maple Ridge, British Columbia, the specialists who provided the pipe, fittings and fusion expertise for the Big Bend Crossing project. PE pipe is joined using a heat fuse process with machines such as the Connectra Fusion 14 inch hand pump machine utilized on this project. The fusion process creates an area at the joint that is even stronger than any other point along the length of pipe, and is therefore equally resilient when bent.
Earthquake considerations
In America, municipalities and states in quake prone regions such as southern California have been installing PE pipe at increasing rates. A report on damage rates to gas distribution lines following the Northridge, CA, earthquake in 1994, stated that while PE makes up 41 percent of the gas piping system in the area, only 27 of the 709 leaks (or 3.8 percent) occurred in PE pipes.
For the Big Bend project, new water mains for the project area were specified to be HDPE DR11 DI OD and were 460 meters in length. Laterals to the site structures accounted for an additional 800 meters of pipe ranging from 150 to 250 mm diameters. Sanitary sewer lines were all low pressure force mains and constructed using 400 meters of HDPE DR26 along the main road and site right-of-ways. Included were four flush out chambers on the main and three additional flush out chambers on the laterals to the site structures adjacent to the right-of-way. Sanitary servicing to the remainder of the site, not adjacent to the right of ways, required an additional 165 meters of HDPE DR26, and PE series 75, including the laterals to the individual units.
The building construction program was on going throughout the $730,000 utility installation, creating an even more challenging work environment for the installation crew. In order to ensure access to the site for other contractors, only certain lengths of pipe string could be pre joined. This meant that some of the HDPE fusion welds had to be done in the trench, requiring a fusion machine that could perform complicated ditch welds and fusion of fittings.
In addition, the flush out chambers on the sanitary lines required a riser that could be accessed by a flush truck for maintenance purposes, creating a space problem. Some of the HDPE fittings had to be customized and re welded in order to fit inside the specified 1,500 mm diameter barrel of the chambers. A Connectra Fusion 14 inch hand pump machine was used both in and out of the trench to perform all of the 230 required fusion welds for the project. “There is no question this was a complicated job when it came to joint fusion,” said Warning. “The fusion machine was perfect for the job because of its adaptability and ease of use in tight spaces.”
In total, 2,800 meters of pipe ranging from 2 inch to 10 inch DIPS were fused. All the water and sanitary mains were installed by standard trenching with a depth of cover of approximately 1.5 meters and imported bedding and granular backfill were used.
FOR MORE INFORMATION:
Utility contractor: TAG Construction, (604) 534 2685, www.tagconstruction.com
Fusion equipment: Connectra Fusion, (877) 776 7100, www.connectrafusion.com
HDPE pipe supplier: Prolite Systems Inc., (604) 460 8250, www.prolitepiping.com
Comments