26757
Many areas of the country suffer drought conditions, ranging from mild to extremely serious, and responses to the prospect of running low or out of water by local governments and water providers vary widely.
In Colorado, the cities of Denver, Aurora and 10 South Metro water providers have formed a partnership that provides communities the opportunity to purchase, transport and treat available renewable water.
Water Infrastructure and Supply Efficiency (WISE) is one of the first organizations of its kind in the country, according to the website of the municipality of Castle Rock, one of the WISE participants. Regional water providers are working together to share in renewable water, well water, physical pipes, treatment and storage assets, while still maintaining independent jurisdictions.
For Castle Rock to utilize the water, the town has built a new 5-mile, 36-inch diameter water line connecting Castle Rock’s water infrastructure system with that of the town of Parker, another WISE member.
The project engineer was Burns and McDonnell Engineering Co., with Garney Construction serving as primary contractor. Underground Solutions provided pipe and completed fusions, and Global Underground Corp. completed trenchless portions of the pipeline by horizontal directional drilling (HDD).
Understanding challenges
Early in the project, it was recognized there were two specific challenges.
First, the new pipe would be exposed to excessive corrosion potential from Colorado’s highly corrosive soils and the potential of stray current from Xcel Energy’s overhead high-voltage cable along the right-of-way shared by the pipeline route. If metallic pipe was used for the water line, it would require a costly cathodic protection system.
Second, was the need for three, complex trenchless crossings under several drainage basins and residential streets.
The difficult design considerations were solved by using a fusible hybrid PVC pipe system for trenchless segments and all restrained-joint pipe sections.
Part of the planning included a preselection process to identify qualified HDD contractors. Ultimately, Global Underground Corp. was selected to make the three trenchless installations.
“The three bored sections of pipe were located in various locations on the project,” said Robert Meadows, president of Global Underground. “The bore lengths were 762, 950 and 1,712 feet. All three bores were under drainage basins and one bore also crossed several residential streets, as well. The project was built in easement in-between two subdivisions. There was lots of scrub oak, tall grass, fine sand and surface rock in the area. Subsurface conditions ranged from sandstone, cobble, gravel, shale, boulders and granite formations greater than 20,000 psi.”
There was a wide range of depths, with the deepest being 63 feet. All pipe was 36-inch fusible PVC.
Overall, access to the equipment setup and pipe layout locations was better than most projects, Meadows said.
“Work hours,” he continued, “were limited to 7 a.m. to 5:30 p.m. due to the close proximity to neighboring houses. Crane mats were placed under all equipment to help keep mud from being tracked onto the roads.”
Bores
The three directional bores were made using an American Augers DD440 with 80,000 pounds of rotary torque and 440,000 pounds of push/pull. Support equipment included a Vermeer R9x12T fluid cleaning system and Tulsa Rig Iron TT660 mud pump.
Solids and excess drilling fluids were excavated utilizing a trackhoe, and hauled away in dump trucks. Thick excess drilling fluids were removed with a Vactor vacuum excavator. Thin excess drilling fluids were vacuum excavated with an 80BBL vacuum truck.
One of the benefits of using the hybrid fusible PVC, said Meadows, was being able to install pipe in a smaller reamed hole than would have been required with HDPE pipe.
“A 9 7/8-inch pilot hole was completed for each of the bores and then 26-, 38- and 54-inch ream passes were completed,” he said. “A 48-inch swab was completed and then the pipe was pulled with a 48-inch tapered barrel reamer.
“The 20,000-plus psi granite was encountered on the first 762-foot bore, and the hole openers were changed from mill tooth to TCI in order to cut the rock.”
Meadows said the three installations went smoothly considering the freezing weather conditions that required overnight circulation and other winter-weather precautions.
Return mud lines were run from the exit ends of the bores back to the mud cleaning system to help lessen the impact in the neighborhoods, by pumping returns rather than driving vacuum trucks back and forth all day. Four- and six-inch HDPE lines were bored in when needed.
The two shorter bores were fused into one string, and a mid-fuse was necessary in the long one. All pipe was placed on rollers and in pipe cradles during pull-back operations.
Fusion
“The fusing process for PVC is the same as with HDPE, but is specific to the PVC material,” Meadows explained. “Garney Construction handled the pipe during the fusion and pull-back operations, completed all HDD tie-ins, and handled the open cut portion of the project.”
Meadows said the 1,712-foot bore took about eight hours to pull because a mid-fuse was required. The other two bores each were pulled in four to five hours. Rig breakdown and demobilization required one week.
The project was constructed and completed in summer 2017. All pipeline segments, including the three, long HDD installations, were pressure tested to 150 psi for two hours, and the line was placed into service.
Reflecting on the project, Meadows said several factors contributed to the successful installation of the trenchless segments.
“Global Underground,” he said, “teamed with two engineering firms to complete the design profiles and HDD calculations to insure all aspects of these crossings were discovered and evaluated.
“Communication and teamwork between the owner, general contractor, engineer and Global Underground were the key reasons that this project was successful. All parties involved had the same goal in mind. Whenever potential issues were discovered, the team worked together to come up with solutions.”
Based in Colorado Springs, Colo., Global Underground provides underground utility construction to a broad range of clients utilizing open-cut construction, HDD, pipe bursting and hydro excavation methods.
FOR MORE INFO:
Burns and McDonnell Engineering, (713) 622-0227, burnsmcd.com
Garney Construction, (303) 791-3600, garney.com
Underground Solutions, (858) 679- 9551, aegion.com
Global Underground Corp., (719) 471-7414, globalug.com
American Augers, (800) 324-4930, americanaugers.com
Vermeer Corp.,(888) 8370-6337, Vermeer.com
Tulsa Rig Iron, (918) 321-3330, tulsarigiron.com
Vactor, (815) 672-3171, vactor.com
From Archive
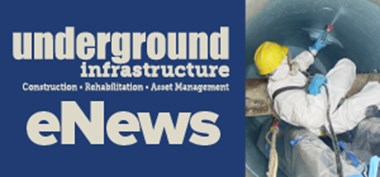
- Texas A&M weighs underground transit plan with Elon Musk's Boring Co. to reduce campus traffic
- Lynchburg, Va., breaks ground on largest-ever Blackwater CSO tunnel project
- Federal court halts permits for 32-mile Tennessee gas pipeline project
- Cadiz to reuse steel from terminated Keystone XL pipeline for California groundwater project
- CGA’s 2023 DIRT report shows fewer utility damages, urges action on locating delays
- Wisconsin proposes new PFAS drinking water standards to align with federal rules
- Dog River pipeline replacement in Oregon improves water supply with new HDPE pipe
- Leaking wastewater systems named top source of San Diego River contamination, study finds
- New Portable Welding System From Miller
- Excavator Causes Puerto Rico Power Outage
Comments