HDD Tooling Maximizes Productivity on Fiber Jobs
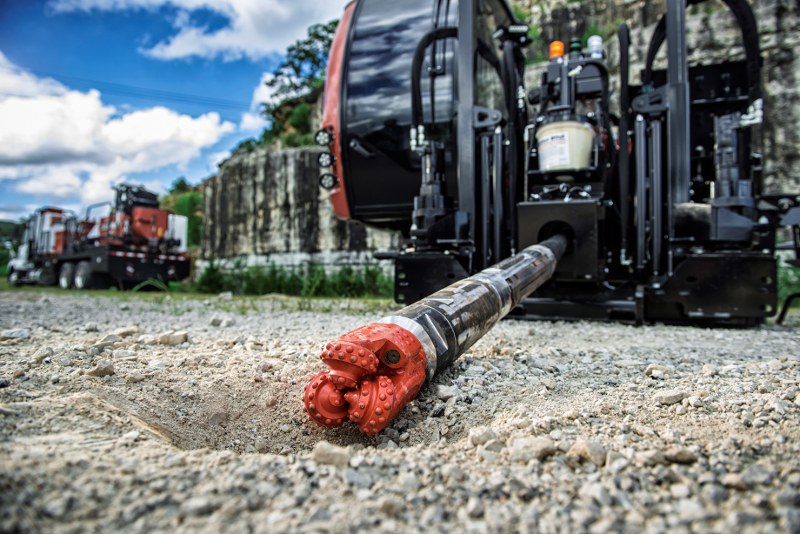
HDD Tooling Maximizes Productivity on Fiber Jobs
By Jeff Davis, Ditch Witch product manager of HDD tooling and drill pipe
The fiber industry is rapidly expanding, increasing demand for horizontal directional drilling (HDD) installation. It is a demand that will continue steadily, as the need for quicker data delivery shows no signs of slowing down.
Most contractors working in the underground-fiber installation industry, know that selecting the appropriate drill for each project is key to optimal productivity and ROI. Some may not realize, however, the equal importance of choosing the right HDD tooling for each job.
HDD plays an important role in the fast-growing fiber installation industry. Even on long-haul jobs – where vibratory plows and trenchers are best suited for product installation – HDD units are often required to step into tough operator conditions, such as overpass embankments, side hills, water crossings, wooded areas and rough terrain.
HDD tooling is vital to helping operators maximize their productivity on projects where drills take a leading role.
Backreamers can make these projects easier when installing large diameter products. Drill bits, on the other hand, can be used exclusively to create the smaller bore paths required for many feeder lines which extend off the main, central fiber backbone. On these projects, many operators forego a backreaming process, and after the pilot hole is shot and the exit pit is reached, a pull tool can be applied to the drill bit to quickly pull the product back. .
To help guide HDD tooling selection for fiber jobs, operators should consider these questions:
What are the ground conditions?
While many fiber job sites have a smaller footprint, requiring compact drill rigs, ground conditions can vary widely. Operators need to know what they’ll encounter underground to select the best tooling to confidently, effectively and efficiently complete the project, as well as increase the life of their equipment. After all, time is money.
Soft soil, sand, dirt and cobble rock each impact drill bits and backreamers differently. For instance, cobble rock requires tooling that will help operators more accurately steer and maneuver down hole. Clay, meanwhile, requires tooling that helps with fluid management and accuracy. Correctly matching HDD tooling to ground conditions before a job begins will help reduce premature wear on equipment.
Remember: Every job and bore is different, so tooling decisions should be made separately for each project after conditions are analyzed.
What tooling is best for varying ground conditions?
Soft Ground
In soft soils, it is recommended that operators use a bit that effectively penetrates the soil, assists with steering adjustments and helps properly mix soil with fluids. For example, the Ditch Witch Barracuda, the Dura bit, and the Tornado bit are the most cost-effective in these conditions and don’t wear prematurely, especially in more abrasive soils such as sand or soft clay. Additionally, the paddle design and angle best mix material with fluids for a successful bore.
If a backream is necessary in soft soils, it is recommended that operators choose a backreamer that will quickly attach to the drill string, saving valuable time on the job. Today, some backreamers have easy connectors built-in, such as the Ditch Witch EZ backreamer, which helps operators quickly attach the reamer.. In addition, choosing a backreamer with efficient fluid-mixing is important in soft-to-medium soil conditions, like sand and clay, that require more effective fluid management. For example, the new Ditch Witch SandHog HD and Beavertail HD backreamers effectively enlarge the hole while mixing the drilling fluids with spoils using less horsepower for easier product installation.
Hard Soil Conditions
Hard soil conditions present their own set of distinctive challenges on fiber projects. Drill bits often wear down prematurely can increase overall time and money spent on the job, cutting your profits. Choosing a drill bit that most effectively navigates through hard soil conditions will assist operators with steering and provide a clearer cutting path. To boost performance in these conditions, drill bits with a hard surface, such as carbide, help protect the tool from abrasive environments and extend their usable life. Additionally, replaceable, angled carbide teeth improve longevity and increase cut productivity. The Ditch Witch Tuff bit, Steep Taper Tuff bit, and the TriHawk bit are designed specifically for hard soils, and if drilling in solid rock, the Rockmaster rotary bits are designed specifically for our All Terrain drills, to improve productivity and assist with more accurate steering.
When installing fiber in rocky conditions, operators may or may not require a backreamer and enlarged hole. For fast installation in these environments, the Ditch Witch Swab backreamers flush the hole with proper drilling fluids without enlarging it. If a project calls for an enlarged bore hole, however, the Rockmaster backreamer help operators productively install fiber conduit by enlarging the hole in solid rock.
Understanding ground conditions and selecting the correct tooling is the first step for any fiber job. This will both improve job-site productivity and extend the life of the equipment. Do your research and make sure tooling is a part of the planning process. For assistance with tooling selections, visit the Ditch Witch tooling site or contact your local Ditch Witch dealer.
From Archive
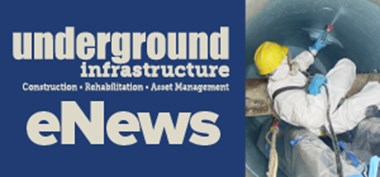
- Texas A&M weighs underground transit plan with Elon Musk's Boring Co. to reduce campus traffic
- Lynchburg, Va., breaks ground on largest-ever Blackwater CSO tunnel project
- Federal court halts permits for 32-mile Tennessee gas pipeline project
- Cadiz to reuse steel from terminated Keystone XL pipeline for California groundwater project
- CGA’s 2023 DIRT report shows fewer utility damages, urges action on locating delays
- Wisconsin proposes new PFAS drinking water standards to align with federal rules
- Dog River pipeline replacement in Oregon improves water supply with new HDPE pipe
- Leaking wastewater systems named top source of San Diego River contamination, study finds
- New Portable Welding System From Miller
- Excavator Causes Puerto Rico Power Outage
Comments