April 2024 Vol. 79 No. 4
Features
Jacob Trapani, NASSCO Standard Bearer
EDITOR’S NOTE: NASSCO continues to set standards for the assessment and rehabilitation of underground infrastructure. A vast array of individuals has contributed to the success of the association, both in the past and present, that has driven NASSCO’s industry mission. This series of articles recognizes those who have not only been critical to the success of NASSCO, but the industry as well.
This month, we profile Jacob Trapani who has proven to be not only a tremendous leader in private industry, helping to elevate BLD Services, but leading NASSCO through tough and changing situations during COVID.
-----------------------------------------
I grew up in Metairie, La., a suburb just outside the great city of New Orleans. We were your typical middle-class family: our mom stayed home to raise her three boys, and I grew up in the shadow of my older brother while, at the same time, vying for her attention that was constantly showered on my younger brother – middle child syndrome is a real thing!
Dad was an engineer for the school board and made a good living, and also enjoyed his hobby of wood working, where he fabricated the iconic horsedrawn and horseless carriages that are frequently seen throughout the streets of New Orleans. His hobby occasionally took us on trips to the Amish Country in Pennsylvania to find wheels for the carriages that he could not build himself, and that introduced me to quite a different kind of lifestyle, one I had never experienced in Louisiana.
Helping my dad with his hobby when I was a young boy taught me life lessons that I have carried into my career today. I was so impressed with how the Amish made so much with so little. They had none of the modern conveniences that we take for granted in our everyday lives, and yet they saw so much value in small, insignificant things.
CIPP
In 1986, I was attending the University of New Orleans when I was first introduced to the massive industry of underground infrastructure. My friend’s brother worked for Insituform, and they needed help for the summer, so I decided to join the company. I learned the cured-in-place pipe (CIPP) process quickly and really took a liking to it. So, after receiving my degree in Business Administration, I started working with Insituform full-time.
It was an exciting time for the company; it was acquiring as many licensed contractors as possible. I first worked with Naylor Envirosystems, an Insituform subsidiary founded by Tim Naylor’s father and grandfather. To this day, Tim continues to work as a salesperson for Insituform out of the Austin, Texas, office.
As CIPP technology was gaining traction, we were able to pick up bigger and bigger construction projects. In the late 1980s, one of the largest at the time was San Antonio with a $15 million rehabilitation project, so I moved from my home in New Orleans to gain experience by working in the field under Naylor/Insituform Gulf South.
In 1992 I moved to Houston where there was an enormous amount of rehabilitation work, as the result of a major consent decree. This is where I first met Bob Affholder and his team. They managed North Texas, while we oversaw the Southern part of the state. Bob purchased the first mid-America license of the Insituform process back in 1982 and took the company public as Insituform Mid-America in 1987.
The company just snowballed from there, becoming the largest Insituform licensee in North America until it merged with Insituform Technologies (now Aegion). I was caught up in this whirlwind of mergers and acquisitions until I moved back to Louisiana in 1997, where I remained with Insituform until November 2008.
Insituform sold its lateral lining division to BLD Services LLC on Oct. 31, 2008. The date sticks in my head because we were pushing Brad Dutruch to sign the deal, but he was out trick-or-treating with his kids, so we had to wait for final signatures to move forward.
New direction
Shortly after that, I was caught up in a corporate reorganization within Insituform, so I asked Brad at BLD if he would consider hiring me to help run the lateral group he just purchased. As fate would have it, he said “yep!” Subsequently, I started my career working for BLD on Dec. 1 partnering with Dan Wagner, the president of BLD. With a lot of sweat equity, coordination and perseverance, we had crews installing laterals in the field by Jan. 1.
Today, with 35 crews, 16 office locations and approximately 1,800 laterals installed per month in 26 states, BLD is now the largest lateral contractor in the United States and has exponentially increased in value over the last 15 years.
This brings me back to the life lessons I learned from my early days with my father and what he taught me about recognizing the merit in situations. Insituform did not see the value in their lateral division, nor their people, but Dan and I were able to make something significant out of what was discarded, including hiring many of the employees they let go during the restructuring.
Brad was the person who got me involved with NASSCO, when he asked me to attend the annual conference in Palm Springs in 2009. Brad was very much involved with NASSCO as a board member, and he later served as president from 2010-2011. One of the first things I did way back then was join NASSCO’s Lateral Committee. There were just four of us at that first meeting: Dean Monk, Mark Metcalfe, Larry Kiest and me, and we worked together as competitors and colleagues to develop the first lateral overview document. NASSCO’s Lateral Committee now has 25 active members across the United States and Canada, indicating the growth and support that has developed over the years.
Once Brad’s term as NASSCO President ended, I had the opportunity to be elected to NASSCO’S Board of Directors, and eventually moved up to president in 2019. Presidential terms are typically for one year, but I was invited to serve as president for a second year because of the pandemic. The association had to react very quickly with virtual training, working from home and other accommodation, so we determined that to keep consistency, it was best that our Executive Committee stay in place for another year.
NASSCO mission, accomplishments
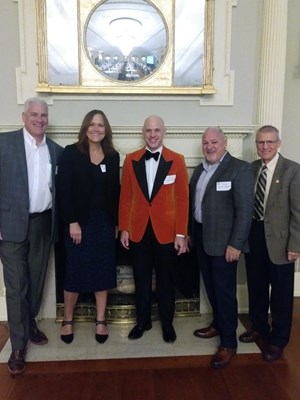
The highlight of the year for NASSCO members is the Annual Conference. Always held at a beautiful location, the event draws members together to network and learn from each other. In 2020 and 2021, our meetings were held via ZOOM. It was disappointing, but we provided our members with updates, elected board members and did our best to maintain a sense of normalcy.
I anticipated a drop in membership, but we actually saw an increase during that time, proving to me that our members are in it for the right reasons, like setting industry standards and advocating for our industry, and not just to network at the annual conference. Ironically, the pandemic brought us closer together.
Another benefit of the pandemic was when EPA Administrator Andrew Wheeler sent a letter to governors in all 50 states, territories and Washington DC, urging them to ensure that drinking water and wastewater employees, as well as the manufacturers and suppliers who provide vital services, be considered essential workers. This was critical to keeping our crews employed and our underground systems well maintained.
NASSCO is the first trade association that I have been a part of where the majority of people check their company hat at the door. BLD, together with many other companies, comes together under the NASSCO banner to learn and grow from each other. We also address issues such as claims regarding styrene emissions in the CIPP process and look to NASSCO’s Director of Health, Safety and Environmental, Dennis Pivin, CSP, as well as its highly respected Technical Advisory Council, which was formed during my term as president, for guidance and support.
NASSCO truly has evolved into the industry source for education, technical resources and advocacy. With its Pipeline Assessment Certification (PACP) and other training opportunities, the standards are getting stronger every year.
In closing, NASSCO membership goes way beyond the training discounts, safety audits, participation in committees and networking. Being a NASSCO member has helped me tremendously both personally and professionally. Experiencing collaboration with competitors sitting across the table, working toward one common goal, is a unique and rewarding experience. It has taught me valuable lessons that I have taken out of NASSCO to help me deal with conflicts and find resolution on a day-to-day basis.
Comments